Recycling of siliceous by-products to reduce their impacts on the environment
DOI:
https://doi.org/10.15587/2706-5448.2023.277784Keywords:
Tamazert raw kaolin, siliceous by-products, mineral processing, silica, glassAbstract
Currently, there is a tendency to use less silica rich ores given the depletion of high-quality resources. The raw kaolin treatment of Tamazert (Eastern Algeria) produces, by hydrocyclone process, approximately 80 % of siliceous by-products. These siliceous wastes, which are stored in the open air, constitute a significant environmental problem. This research work aims to improve the quality of siliceous by-products, more particularly, to a process for the elimination of iron oxides and aluminum to make this raw material usable industrially as well as solving environmental issues. The collected by-products, were characterized by different techniques, such as X-ray fluorescence (XRF) and X-ray diffraction (XRD). XRF confirmed that the by-products east siliceous, with content going up to 82 % of SiO2. The by-product resulted from the raw kaolin treatment, mainly contains varying amounts of impurities such as iron oxide, titanium oxide and alumina. In all cases, the presence of these impurities affects the color and the physical properties of the mineral, and so lowers the economic value and limits the industrial application. In this framework, the classified fraction (–500)–(+100) µm was directed to attrition scrubbing followed by magnetic separation technique and chemical treatment by sulphuric acid with different concentrations. The results of the beneficiation tests of by-product indicate that using the attrition scrubbing alone not provides a suitable product for glass manufacture. The magnetic separation was tested with attrition on the useful fraction ((–500)–(+100) μm). The non-magnetic attritional fraction concentrates less than 0.45 % of Al2O3 and 0.05 % of Fe2O3. This low content coupled with a remarkable percentage in silica of 97.98 %.The tests by attrition and leaching with 40 % of sulphuric acid show, on the one hand, significant results with a high percentage of silica (>98.5 %) against 0.04 % Fe2O3 and 0.66 % Al2O3 ,and on the other hand, that the enriched product meets the standards required by glass making.
References
- Boulos, T. R., Yehia, A., Morsi, M. B., Ibrahim, S. S. (2017). High quality fused silica from Egyptian silica sand concentrate. International Journal of Science and Engineering Investigations, 6 (62), 160–166.
- Konev, N. N., Salo, I. P., Lezhnev, Yu. P., El’skii, V. P. (2001). Magnetic concentration of quartz sand for glass industry. Glass and ceramics, 58 (1-2), 57–59. doi: https://doi.org/10.1023/a:1010997414948
- Thio, P. R., Koffi, K. B., Konan, K. D., Yao, K. A. (2021). Production of High-Purity Silica Sand from Ivorian Sedimentary Basin by Attrition without Acid Leaching Process for Windows Glass Making. Journal of Minerals and Materials Characterization and Engineering, 9 (4), 345–361. doi: https://doi.org/10.4236/jmmce.2021.94024
- Zhong, T., Yu, W., Shen, C., Wu, X. (2021). Research on Preparation and Characterisation of High-purity Silica Sands by Purification of Quartz Vein Ore from Dabie Mountain. Silicon, 14 (9), 4723–4729. doi: https://doi.org/10.1007/s12633-021-01217-x
- Yin, W., Wang, D., Drelich, J. W., Yang, B., Li, D., Zhu, Z., Yao, J. (2019). Reverse flotation separation of hematite from quartz assisted with magnetic seeding aggregation. Minerals Engineering, 139, 105873. doi: https://doi.org/10.1016/j.mineng.2019.105873
- Tuncuk, A., Akcil, A. (2016). Iron removal in production of purified quartz by hydrometallurgical process. International Journal of Mineral Processing, 153, 44–50. doi: https://doi.org/10.1016/j.minpro.2016.05.021
- Osman, R. A. (2021). Preliminary study on upgrading silica sand from the Elwadi Elgedid, Western Desert, Egypt for compatibility with various industrial applications. Journal of Particle Science and Technology, 7 (2), 107–117. doi: https://doi.org/10.22104/jpst.2022.5513.1202
- Ibrahim, S. S., Selim, A. Q., Hagrass, A. A. (2013). Gravity Separation of Silica Sands for Value Addition. Particulate Science and Technology, 31 (6), 590–595. https://doi.org/10.1080/02726351.2013.800930
- Bouabdallah, S., Bounouala, M., Idres, A., Chaib, A. (2015). Iron removal process for high-purity silica production by leaching and magnetic separation technique. Natsional'nyi Hirnychyi Universytet. Naukovyi Visnyk, 5, 47.
- Anas Boussaa, S., Kheloufi, A., Boutarek Zaourar, N., Bouachma, S. (2017). Iron and Aluminium Removal from Algerian Silica Sand by Acid Leaching. Acta Physica Polonica A, 132 (3–II), 1082–1086. doi: https://doi.org/10.12693/aphyspola.132.1082
- Ala'a, M. K., Bader, N. D., Khachiek, T. V., Fleah, I. K., Issa, I. G. (2011). Biobenefication of Silica Sand for Crystal Glass Industry from Ardhuma Location, Iraqi Western Desert. Iraqi Bulletin of Geology and Mining, 7 (1), 77–86.
- Du, F., Li, J., Li, X., Zhang, Z. (2011). Improvement of iron removal from silica sand using ultrasound-assisted oxalic acid. Ultrasonics Sonochemistry, 18 (1), 389–393. doi: https://doi.org/10.1016/j.ultsonch.2010.07.006
- Al-Maghrabi, M. N. N. (2004). Improvement of low-grade silica sand deposits in Jeddah area. Engineering Sciences, 15 (2).
- Rapport interne de la mission chinoise sur Djebel Tamazert carte géologique (1986). SONAREM.
- Liu, Y., Peng, H., Hu, M. (2013). Removing iron by magnetic separation from a potash feldspar ore. Journal of Wuhan University of Technology-Mater. Sci. Ed., 28 (2), 362–366. doi: https://doi.org/10.1007/s11595-013-0696-3
- Hickin, A. S., Huntley, D. H. (2011). Attrition experiments for the beneficiation of unconsolidated sand sources of potential hydraulic fracture sand, Northeastern British Columbia. Available at: https://www.researchgate.net/publication/273765229_Attrition_experiments_for_the_beneficiation_unconsolidated_sand_sources_of_potential_hydraulic_fracture_sand_northeast_British_Columbia
- Abdel-Rahman, I. F., Elshennawy, A. A. (2012). Improvement of Low-Grade Silica Sand Deposits in Um Bogma Area-West Central Sinai, Egypt. Nuclear Sciences Scientific Journal, 1 (1), 167–170. doi: https://doi.org/10.21608/nssj.2012.31027
- Chen, L., Yang, R., Zeng, J., Shao, Y., Xiao, Q., Guo, S. (2016). A wet belt permanent high gradient magnetic separator for purification of non-metallic ores. International Journal of Mineral Processing, 153, 66–70. doi: https://doi.org/10.1016/j.minpro.2016.06.004
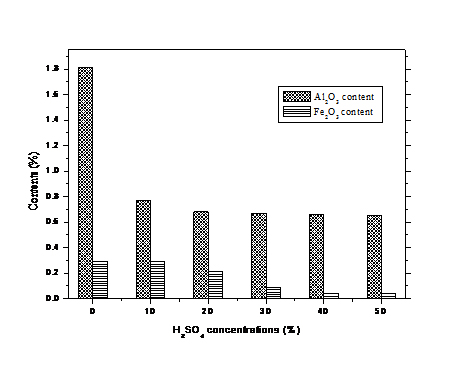
Downloads
Published
How to Cite
Issue
Section
License
Copyright (c) 2023 Soufiane Bouabdallah, Abdeslam Chaib, Mohamed Bounouala, Nadiia Dovbash, Aissa Benselhoub, Stefano Bellucci

This work is licensed under a Creative Commons Attribution 4.0 International License.
The consolidation and conditions for the transfer of copyright (identification of authorship) is carried out in the License Agreement. In particular, the authors reserve the right to the authorship of their manuscript and transfer the first publication of this work to the journal under the terms of the Creative Commons CC BY license. At the same time, they have the right to conclude on their own additional agreements concerning the non-exclusive distribution of the work in the form in which it was published by this journal, but provided that the link to the first publication of the article in this journal is preserved.