Effect of vibration dampers on the dynamic state of a drill string
DOI:
https://doi.org/10.15587/2706-5448.2023.290145Keywords:
drill string, dynamic state, anti-vibration shock absorbers, pitting, pitting engine, dynamic modelAbstract
The object of research is the drill string bottom structure using the correcting devices of drilling modes to control the dynamics of the drill string. The work is aimed at the study of longitudinal, torsional and transverse oscillations when adjusting the axial load on the bit by using a drilling shock absorber with a two-link characteristic.
A dynamic model of the drill string during the drilling process is presented, which is a concentrated-continuous nonlinear system that interacts with the ball bit and the downhole engine as a source of energy. It is shown that elastic oscillations of all types affect the interaction of the bit with the outcrop rock. In order to evaluate drilling performance, it is necessary to take into account not only longitudinal, torsional and transverse oscillations, but also parametric oscillations, which are associated with the deformation of the weighted drill pipe under axial loads and during its rotation in the process of deepening the hole. It was found that transverse vibrations of weighted drill pipes, as a flexible element, during the drilling process are, as a rule, parametric in nature. They lead to the appearance of additional stresses in the elements of the column and, as a result, to the acceleration of their destruction and accelerated wear of the bit arms and rolling bearings. It is proved that in the future, for the development of dynamic models, it is necessary to take into account their hydrodynamics and the type, design and parameters of the applied punching elements.
The obtained research results can be applied in practice in the process of designing the structure of the drill string bottom structure (DSBS) using correcting devices of drilling modes to control the dynamics of the drill string, by using a drilling shock absorber with a two-link characteristic in order to correct the axial load on the bit.
References
- Surnin, L. S. (1986). Prvishenie effektivnosti primeneniia amortizatorov na baze issledovaniia volnovikh protcessov v burilnoi kolonne. Ivano-Frankivsk, 187.
- Ullah, F. K., Duarte, F., Bohn, C. (2016). A Novel Backstepping Approach for the Attenuation of Torsional Oscillations in Drill Strings. Solid State Phenomena, 248, 85–92. doi: https://doi.org/10.4028/www.scientific.net/ssp.248.85
- Riane, R., Doghmane, M. Z., Kidouche, M., Tee, K. F., Djezzar, S. (2022). Stick-Slip Vibration Suppression in Drill String Using Observer-Based LQG Controller. Sensors, 22 (16), 5979. doi: https://doi.org/10.3390/s22165979
- Iunin, E. K. (1983). Upravlenie nizkochastotnimi kolebaniiami burilnoi kolonni s tceliu povisheniia effektivnosti protcessa bureniia. Moscow, 367.
- Vaziri, V., Kapitaniak, M., Wiercigroch, M. (2018). Suppression of drill-string stick–slip vibration by sliding mode control: Numerical and experimental studies. European Journal of Applied Mathematics, 29 (5), 805–825. doi: https://doi.org/10.1017/s0956792518000232
- Ogorodnikov, P. I. (1990). Upravlenie uglubleniia zaboia skvazhini na baze izucheniia dinamicheskikh protcessov v burilnoi kolonne. Moscow, 423.
- Tcifanskii, S. L., Beresnevich, V. I., Oks, A. B. (1991). Nelineinye i parametricheskie kolebaniia vibratcionnykh mashin tekhnologicheskogo naznacheniia. Riga: Zinatne, 229.
- Canudas-de-Wit, C., Rubio, F. R., Corchero, M. A. (2008). D-OSKIL: A New Mechanism for Controlling Stick-Slip Oscillations in Oil Well Drillstrings. IEEE Transactions on Control Systems Technology, 16 (6), 1177–1191. doi: https://doi.org/10.1109/tcst.2008.917873
- Belovodskii, V. N., Tcifanskii, S. L., Ozhiganov, V. M. (1983). Vynuzhdennye kolebaniia sistemy s nesimmetrichnoi zhestkoi kharakteristikoi uprugoi vostanavlivaiushchei sily. Riga: Zinatne, 41, 105–110.
- Khegai, V. K., Iunin, E. K. (2003). K voprosu ustoichivosti vrashcheniia burilnoi kolonny, sostoiashchei iz raznorodnykh uchastkov. XXIII Rossiiskaia shkola po problemam nauki i tekhnologii. Ekatirinoburg: Uralskoe otdelenie RAN, 98–103.
- Saroian, A. E. (1979). Burilnye kolonny v glubokom burenii. Moscow: Nedra, 229.
- Iunin, E. K., Khegai, V. K. (2004). Dinamika glubokogo bureniia. Moscow: Nedra, 285.
- Panovko, Ia. G. (1960). Vnutrennee trenie pri kolebaniiakh uprugikh sistem. Moscow: Fizmatgiz, 193.
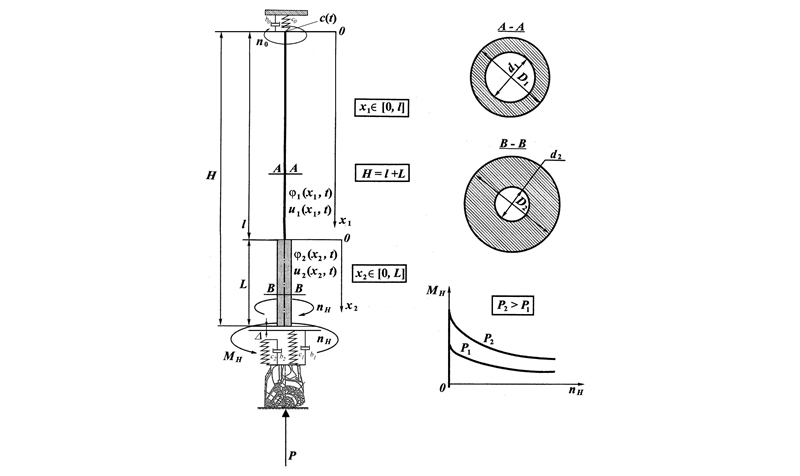
Downloads
Published
How to Cite
Issue
Section
License
Copyright (c) 2023 Viktor Svitlytskyi, Sergii Iagodovskyi, Nataliia Bilenko

This work is licensed under a Creative Commons Attribution 4.0 International License.
The consolidation and conditions for the transfer of copyright (identification of authorship) is carried out in the License Agreement. In particular, the authors reserve the right to the authorship of their manuscript and transfer the first publication of this work to the journal under the terms of the Creative Commons CC BY license. At the same time, they have the right to conclude on their own additional agreements concerning the non-exclusive distribution of the work in the form in which it was published by this journal, but provided that the link to the first publication of the article in this journal is preserved.