Research of the influence of the use of a feedback telecommunication system on the wire arc additive manufacturing process
DOI:
https://doi.org/10.15587/2706-5448.2023.290204Keywords:
WAAM, electric arc welding, CAE systems, robotics, 3D modelling, Abaqus, wireless telecommunication feedback systemAbstract
The object of the research is the possibilities of using a wireless communication system for feedback to improve the additive manufacturing process of a part using the arc welding technology with temperature control for heat propagation.
The problem to be addressed includes determining the geometric properties, print topology, and temperature control regimes for the mentioned part. It also involves the installation of telecommunications sensors and cameras for temperature monitoring, conducting simulation calculations using ABAQUS software, and physical experiments.
The results of the work include simulating the additive manufacturing process at necessary hierarchical system levels, considering specific requirements and obtaining the required geometric dimensions. Residual stresses have been analyzed, software-related heat propagation issues have been discussed, the influence of cooling on production quality has been verified, and optimal print parameters have been created. Additionally, the potential use of a feedback telecommunication system with telecommunication devices such as cameras and laser sensors for temperature control has been explored. The obtained data has been used for the possibility of generating an automated program for robot control during the additive manufacturing process. Based on the data obtained, residual stress values and defects in the produced samples were determined. A real experiment was conducted, and the results of the real experiment were compared and analyzed.
The assessment of the impact of the feedback telecommunication system on the additive manufacturing process using arc welding with heat propagation control through cooling periods in practice allows for improved printing quality, technology of the produced part, cost reduction, and speeding up the production process.
References
- Pant, H., Arora, A., Gopakumar, G. S., Chadha, U., Saeidi, A., Patterson, A. E. (2023). Applications of wire arc additive manufacturing (WAAM) for aerospace component manufacturing. The International Journal of Advanced Manufacturing Technology, 127 (11-12), 4995–5011. doi: https://doi.org/10.1007/s00170-023-11623-7
- Geng, R., Du, J., Wei, Z., Xu, S., Ma, N. (2021). Modelling and experimental observation of the deposition geometry and microstructure evolution of aluminum alloy fabricated by wire-arc additive manufacturing. Journal of Manufacturing Processes, 64, 369–378. doi: https://doi.org/10.1016/j.jmapro.2021.01.037
- Wieczorowski, M., Pereira, A., Carou, D., Gapinski, B., Ramírez, I. (2023). Characterization of 5356 Aluminum Walls Produced by Wire Arc Additive Manufacturing. Materials, 16 (7), 2570. doi: https://doi.org/10.3390/ma16072570
- Anikin, P. S., Shilo, G. M., Kulykovskyi, R. A., Molochkov, D. E. (2020). Automation control system of 3d printing robotic platform with implemented wire + arc welding technology. Electrical Engineering and Power Engineering, 4, 35–48. doi: https://doi.org/10.15588/1607-6761-2020-4-4
- Kim, J.-D., Cheon, J. Y., Ji, C. (2021). Review on the Wire Arc Additive Manufacturing Process and Trends in Non-ferrous Alloys. Journal of Welding and Joining, 39 (6), 603–612. doi: https://doi.org/10.5781/jwj.2021.39.6.5
- Kozamernik, N., Bračun, D., Klobčar, D. (2020). WAAM system with interpass temperature control and forced cooling for near-net-shape printing of small metal components. The International Journal of Advanced Manufacturing Technology, 110 (7-8), 1955–1968. doi: https://doi.org/10.1007/s00170-020-05958-8
- Teixeira, F. R., Scotti, F. M., Jorge, V. L., Scotti, A. (2023). Combined effect of the interlayer temperature with travel speed on features of thin wall WAAM under two cooling approaches. The International Journal of Advanced Manufacturing Technology, 126 (1-2), 273–289. doi: https://doi.org/10.1007/s00170-023-11105-w
- Dash, A., Squires, L., Avila, J. D., Bose, S., Bandyopadhyay, A. (2023). Influence of active cooling on microstructure and mechanical properties of wire arc additively manufactured mild steel. Frontiers in Mechanical Engineering, 9. doi: https://doi.org/10.3389/fmech.2023.1130407
- Jorge, V. L., Teixeira, F. R., Scotti, A. (2022). Pyrometrical Interlayer Temperature Measurement in WAAM of Thin Wall: Strategies, Limitations and Functionality. Metals, 12 (5), 765. doi: https://doi.org/10.3390/met12050765
- Anikin, P., Shilo, G. (2023). Enhancement of Wire Arc Additive Manu-facturing Production of Aluminum Part. Technical Sciences and Technologie, 3.
- Chen, C., He, H., Zhou, J., Lian, G., Huang, X., Feng, M. (2022). A profile transformation based recursive multi-bead overlapping model for robotic wire and arc additive manufacturing (WAAM). Journal of Manufacturing Processes, 84, 886–901. doi: https://doi.org/10.1016/j.jmapro.2022.10.042
- Zhang, J., Xing, Y., Cao, J., Zhang, X., Yang, F. (2022). The gap-filling overlapping model for wire and arc additive manufacturing of multi-bead components. The International Journal of Advanced Manufacturing Technology, 123 (3-4), 737–748. doi: https://doi.org/10.1007/s00170-022-10132-3
- Lee, S. H. (2020). CMT-Based Wire Arc Additive Manufacturing Using 316L Stainless Steel: Effect of Heat Accumulation on the Multi-Layer Deposits. Metals, 10 (2), 278. doi: https://doi.org/10.3390/met10020278
- Park, J., Lee, S. H. (2021). CMT-Based Wire Arc Additive Manufacturing Using 316L Stainless Steel (2): Solidification Map of the Multilayer Deposit. Metals, 11 (11), 1725. doi: https://doi.org/10.3390/met11111725
- Bendia, R., Lizarralde, F., Coutinho, F. (2021). Multivariable closed-loop control for layer geometry in Wire-Arc Additive Manufacturing. XV Simpósio Brasileiro de Automação Inteligente, 1 (1). doi: https://doi.org/10.20906/sbai.v1i1.2732
- Parmar, K., Oster, L., Mann, S., Sharma, R., Reisgen, U., Schmitz, M. et al. (2021). Development of a Multidirectional Wire Arc Additive Manufacturing (WAAM) Process with Pure Object Manipulation: Process Introduction and First Prototypes. Journal of Manufacturing and Materials Processing, 5 (4), 134. doi: https://doi.org/10.3390/jmmp5040134
- Sandeep, K. J., Teja, P. J., Choudhary, A. K., Jain, R. (2022). Development of correlation between temperature, liquid life span, molten pool, and porosity during Wire Arc Additive Manufacturing: A finite element approach. CIRP Journal of Manufacturing Science and Technology, 38, 274–287. doi: https://doi.org/10.1016/j.cirpj.2022.05.002
- Tangestani, R., Farrahi, G. H., Shishegar, M., Aghchehkandi, B. P., Ganguly, S., Mehmanparast, A. (2020). Effects of Vertical and Pinch Rolling on Residual Stress Distributions in Wire and Arc Additively Manufactured Components. Journal of Materials Engineering and Performance, 29 (4), 2073–2084. doi: https://doi.org/10.1007/s11665-020-04767-0
- Anikin, P., Shilo, G., Bastos, F. (2023). Wire arc additive manufacturing three level hierarchical model. Computer Science and Applied Mathematics, 2.
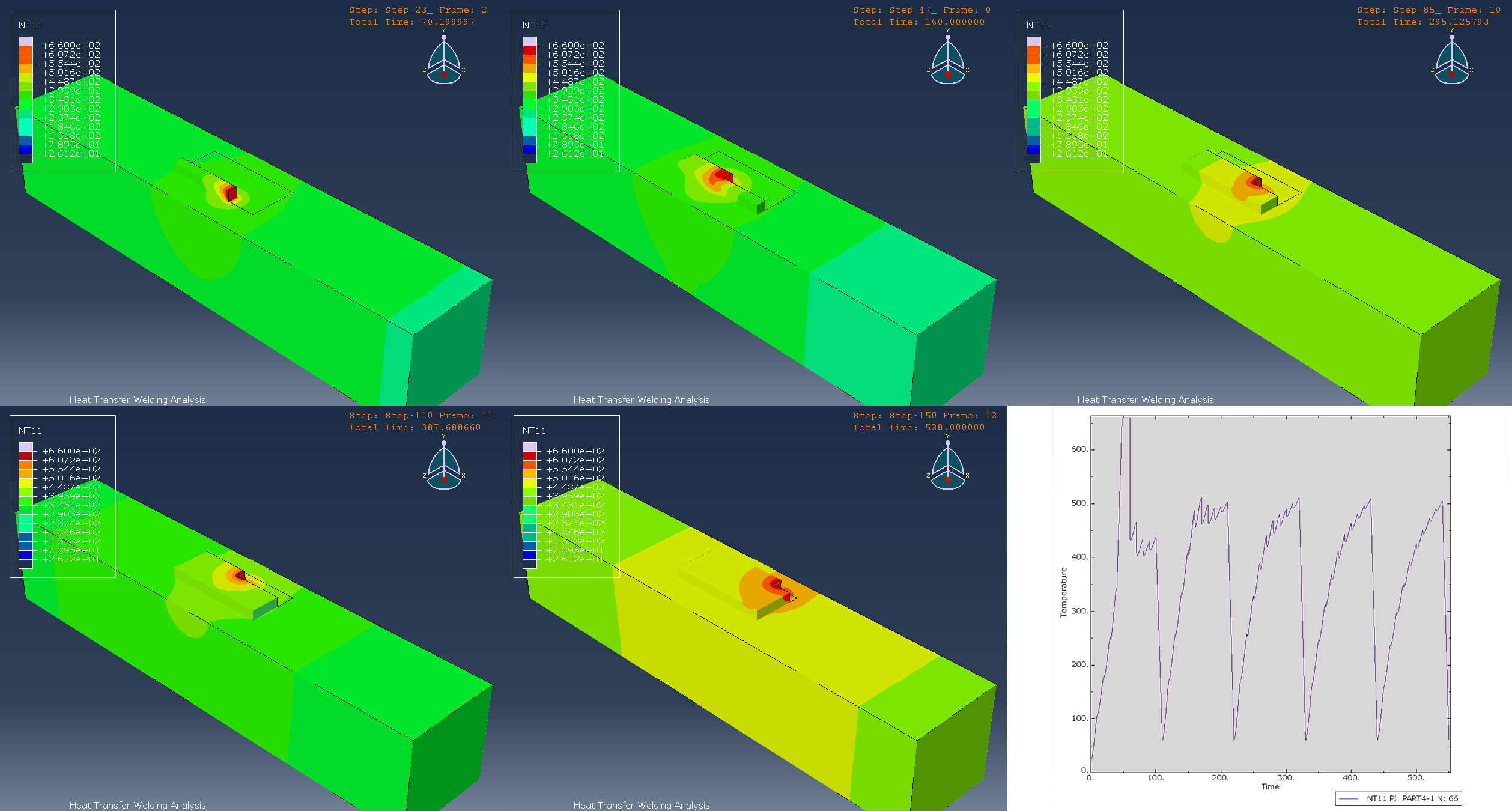
Published
How to Cite
Issue
Section
License
Copyright (c) 2023 Pavlo Anikin

This work is licensed under a Creative Commons Attribution 4.0 International License.
The consolidation and conditions for the transfer of copyright (identification of authorship) is carried out in the License Agreement. In particular, the authors reserve the right to the authorship of their manuscript and transfer the first publication of this work to the journal under the terms of the Creative Commons CC BY license. At the same time, they have the right to conclude on their own additional agreements concerning the non-exclusive distribution of the work in the form in which it was published by this journal, but provided that the link to the first publication of the article in this journal is preserved.