Mathematical models creation for calculating dimensional accuracy at the construction stages of an analytical standard using the chain method
DOI:
https://doi.org/10.15587/2706-5448.2024.297732Keywords:
loft-template method, reverse engineering, aerodynamic profile, analytical portrait, dimensional chainAbstract
The object of research is the process of forming a mathematical model (MM) for calculating accuracy at the stages of construction an analytical standard (AS) using the chain method, the application of which is shown on the example of an aviation object (AO). The analysis of the investigated AO, namely the helicopter stabilizer, was carried out using modern 3D scanners and the creation of its analytical portrait (AP). The problem is to create the most similar AP and compare it with AS, taking into account the results of the calculations. The following results were obtained: the AS was built and the AP of the stabilizer geometry was created, a comparative analysis of the AP and AS was carried out, and the results of the accuracy of the object geometry calculations were obtained. Aerodynamic calculations of stabilizer characteristics were also carried out, analysis of standardized aerodynamic profiles was carried out taking into account the accepted limitations for forming the stabilizer AS. The scientific and practical novelty of the obtained results is as follows: the created MM for calculating the accuracy of the dimensions of the unit contour using the chain method made it possible to estimate the tying errors that occur when using the loft-template method. This made it possible to choose equipment and software for construction the AS stabilizer. The selection of improved values of the object's aerodynamic characteristics made it possible to build an AS based on the standardized NACA 0012 profile. This can be used as an information basis for the organization of small-scale production of the object under study. That is, in general, the process of reverse engineering made it possible to conduct a detailed analysis of sections, aerodynamic characteristics and improve them for the future improved profile. This design approach provides wider opportunities, eliminates intermediate links and maintains high accuracy of object parameters during its manufacture, which is one of the main requirements in aircraft construction.
References
- Miah, H., Chand, D. S., Malhi, G. S. (2023). Research on key charrecteristics of aircraft product assembly process to improve assembly accuracy. Recent Advances in Material, Manufacturing, and Machine Learning, 352–358. doi: https://doi.org/10.1201/9781003358596-37
- Najmon, J. C., Raeisi, S., Tovar, A. (2019). Review of additive manufacturing technologies and applications in the aerospace industry. Additive Manufacturing for the Aerospace Industry, 7–31. doi: https://doi.org/10.1016/b978-0-12-814062-8.00002-9
- Shiping Zhu, Yang Gao. (2010). Noncontact 3-D Coordinate Measurement of Cross-Cutting Feature Points on the Surface of a Large-Scale Workpiece Based on the Machine Vision Method. IEEE Transactions on Instrumentation and Measurement, 59 (7), 1874–1887. doi: https://doi.org/10.1109/tim.2009.2030875
- Kryvtsov, V. S., Vorobiov, Yu. A., Bukin, Yu. M. et al. (2009). Tekhnolohiia vyrobnytstva litalnykh aparativ (skladalno-montazhni roboty). Kharkiv: Nats. aerokosm. un-t «Khark. aviats. in-t», 80.
- Campbell, F. C. (2006). Manufacturing Technology forAerospace Structural Materials. Elsevier Ltd., 600. doi: https://doi.org/10.1016/b978-1-85617-495-4.x5000-8
- Maiorova, K., Sikulskyi, V., Vorobiov, I., Kapinus, O., Knyr, A. (2023). Study of a Geometry Accuracy of the Bracket-Type Parts Using Reverse Engineering and Additive Manufacturing Technologies. Lecture Notes in Networks and Systems, 146–158. doi: https://doi.org/10.1007/978-3-031-36201-9_13
- Maiorova, K., Vorobiov, I., Andrieiev, O., Lupkin, B., Sikulskiy, V. (2022). Forming the geometric accuracy and roughness of holes when drilling aircraft structures made from polymeric composite materials. Eastern-European Journal of Enterprise Technologies, 2 (1 (116)), 71–80. doi: https://doi.org/10.15587/1729-4061.2022.254555
- Vorkapić, M. (2023). Implementation of RE in the 6R Strategy in Considering the Sustainable Development of Parts for the Aviation Industry Using Additive Technologies. Sustainable Aviation, 369–375. doi: https://doi.org/10.1007/978-3-031-42041-2_47
- DSTU 8540:2015. Prokat lystovyi hariachekatanyi. Sortament (2016). Chynnyi vid 01.07.2016. Kyiv: Natsionalnyi standart Ukrainy, 39.
- Adamenko, Yu. I., Herasymchuk, O. M., Maidaniuk, S. V., Minitska, N. V., Pasichnyk, V. A., Plivak, O. A. (2016). Dopusky, posadky ta tekhnichni vymiriuvannia. Praktykum. Chastyna 1. Ivano-Frankivsk: Symfoniia forte, 164.
- Adamenko, Yu. I., Herasymchuk, O. M., Maidaniuk, S. V., Minitska, N. V., Pasichnyk, V. A., Plivak, O. A. (2016). Dopusky, posadky ta tekhnichni vymiriuvannia. Praktykum. Chastyna 2. Ivano-Frankivsk: Symfoniia forte, 188.
- Nikolenko, Ye. Yu., Tkachov, Yu. V. (2006). Osnovy tekhnolohii vyrobnytstva raketno-kosmichnykh litalnykh aparativ. Dnipropetrovsk: RVV DNU, 116.
- Subsonic Airfoil Development System: XFOIL. Available at: https://web.mit.edu/drela/Public/web/xfoil/
- Gopalakrishnan Meena, M., Taira, K., Asai, K. (2017). Low Reynolds number wake modification using a Gurney flap. 55th AIAA Aerospace Sciences Meeting. doi: https://doi.org/10.2514/6.2017-0543
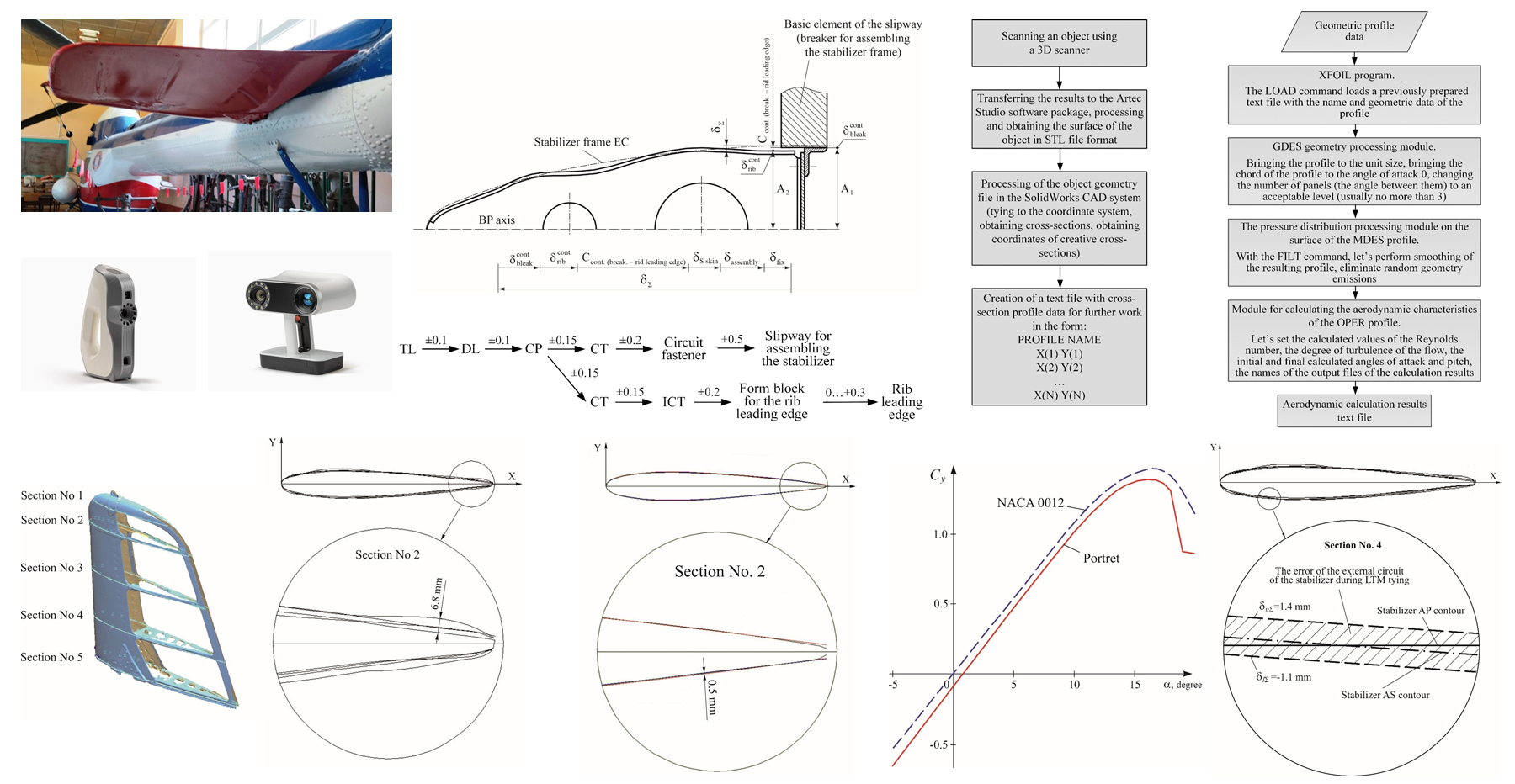
Downloads
Published
How to Cite
Issue
Section
License
Copyright (c) 2024 Iuriy Vorobiov, Kateryna Maiorova, Iryna Voronko, Oleksandr Skyba, Oleh Komisarov

This work is licensed under a Creative Commons Attribution 4.0 International License.
The consolidation and conditions for the transfer of copyright (identification of authorship) is carried out in the License Agreement. In particular, the authors reserve the right to the authorship of their manuscript and transfer the first publication of this work to the journal under the terms of the Creative Commons CC BY license. At the same time, they have the right to conclude on their own additional agreements concerning the non-exclusive distribution of the work in the form in which it was published by this journal, but provided that the link to the first publication of the article in this journal is preserved.