Study of the features of permanent and usual reverse-engineering methods of details of complex shapes
DOI:
https://doi.org/10.15587/2706-5448.2024.297768Keywords:
stable reverse engineering, reverse engineering, 3D scanning, analytical standard, parts of complex shapeAbstract
The subject of the study is sustainable reverse engineering and conventional reverse engineering of aviation equipment (AE) samples. The object of the study is the geometric accuracy of the extracted portrait of a part of a complex shape in comparison with the constructed analytical standard (AS). The work is aimed at researching the methods of sustainable reverse engineering and conventional reverse engineering on the example of the digitization of the box of the AE steering machine, chosen as a part of a complex shape. For this, a portrait of the "*.stl" and AS format file was created and compared by performing a control operation with the determination of the time spent. A structural and technological analysis of the box of the AE steering machine was carried out, which showed that the box has through holes of various diameters (from 10 to 41.6 mm) and shapes (square, trapezoidal, round); thin walls between holes (up to 1.6 mm); right angles and their rounding radii (up to 1–4 mm); the thickness of the body walls is 2.4 mm, etc. 3D scanner – ARTEC SPACE SPIDER (Luxembourg) was selected and scanning was performed. According to the analysis of research methods of reverse engineering, it was established that the use of permanent and conventional reverse engineering allows, in the first case, to quickly manufacture a part by 3D printing or milling on CNC machines, and in the second case, to create its AS with the provision of the specified geometric accuracy. The difference in time between permanent and normal reverse engineering was 8 hours in favor of the former. Control of the ideal portrait according to the AS of the AE steering machine body showed the maximum deviations from –0.30 mm to +0.23 mm and the minimum deviations from –0.04 mm to +0.08 mm. The smallest indicators were observed on vertical and horizontal planes, and the largest - in cities with plane slopes, corners and small radii. This made it possible to establish that the existing capabilities of the Geomagic Design X software for correcting the received portrait of the "*.stl" format file currently do not guarantee the provision of geometric accuracy requirements (up to ±0.5 mm) for the manufacture of an experimental part of a complex shape – the AE steering machine body with 3D printing. The resulting ideal portrait can be used to manufacture a part by milling on CNC machines, taking into account deviations at the stage of process model formation, which can become the topic of further research.
Supporting Agency
- Presentation of research in the form of publication through financial support in the form of a grant «Technological systems of production and restorative repair of objects and components of military equipment, provided by foreign partners or captured, to solve the problems of import substitution and strengthening the defense capability of Ukraine» from the publisher National Aerospace University «Kharkiv Aviation Institute» (Kharkiv, Ukraine).
References
- Stojkic, Z., Culjak, E., Saravanja, L. (2020). 3D Measurement – Comparison of CMM and 3D Scanner. Proceedings of the 31st International DAAAM Symposium 2020. Vienna: DAAAM International, 780–787. doi: https://doi.org/10.2507/31st.daaam.proceedings.108
- Bychkov, I., Seleznova, A., Maiorova, K., Vorobiov, I., Sikulskiy, V. (2022). Requirements development for the information support manufacturing of aerospace products to ensure their quality. Aerospace Technic and Technology, 4, 22–35. doi: https://doi.org/10.32620/aktt.2022.4.03
- Maiorova, K., Vorobiov, I., Boiko, M., Suponina, V., Komisarov, O. (2021). Implementation of reengineering technology to ensure the predefined geometric accuracy of a light aircraft keel. Eastern-European Journal of Enterprise Technologies, 6 (1 (114)), 6–12. doi: https://doi.org/10.15587/1729-4061.2021.246414
- Sikulskiy, V., Maiorova, K., Vorobiov, I., Boiko, M., Komisarov, O. (2022). Implementation of reengineering technology to reduce the terms of the technical preparation of manufacturing of aviation technology assemblies. Eastern-European Journal of Enterprise Technologies, 3 (1 (117)), 25–32. doi: https://doi.org/10.15587/1729-4061.2022.258550
- Bychkov, I. V., Plankoskiy, S. I., Romanov, A. A. (2014). The life cycle of the product and its information support. Avtomatizatciia i upravlenie tekhnologicheskimi protcessami i proizvodstvami, 18 (1 (62)), 149–155.
- Yurdakul, M., İç, Y. T., Celek, O. E. (2021). Design of the Assembly Systems for Airplane Structures. Design Engineering and Science, 521–541. doi: https://doi.org/10.1007/978-3-030-49232-8_18
- Durupt, A., Bricogne, M., Remy, S., Troussier, N., Rowson, H., Belkadi, F. (2018). An extended framework for knowledge modelling and reuse in reverse engineering projects. Proceedings of the Institution of Mechanical Engineers, Part B: Journal of Engineering Manufacture, 233 (5), 1377–1389. doi: https://doi.org/10.1177/0954405418789973
- Montlahuc, J., Ali Shah, G., Polette, A., Pernot, J.-P. (2019). As-scanned Point Clouds Generation for Virtual Reverse Engineer-ing of CAD Assembly Models. Computer-Aided Design and Applications, 16 (6), 1171–1182. doi: https://doi.org/10.14733/cadaps.2019.1171-1182
- Stark, R. (2022). Major Technology 6: Digital Mock-Up – DMU. Virtual Product Creation in Industry. Berlin, Heidelberg: Springer, 273–304. doi: https://doi.org/10.1007/978-3-662-64301-3_12
- Ivanov, V., Dimitrov, L., Ivanova, S., Volkova, M.; Karabegović, I. (Eds.) (2021). Reverse Engineering in the Remanufacturing: Metrology, Project Management, Redesign. New Technologies, Development and Application IV. NT 2021. Lecture Notes in Networks and Systems. Vol 233. Cham: Springer, 169–176. doi: https://doi.org/10.1007/978-3-030-75275-0_20
- Toche, B., Pellerin, R., Fortin, C., Huet, G. (2012). Set-Based Prototyping with Digital Mock-Up Technologies. IFIP Advances in Information and Communication Technology, 299–309. doi: https://doi.org/10.1007/978-3-642-35758-9_26
- Silva, J. V., Costa, S. L., Puga, H., Peixinho, N., Mendonça, J. P. (2013). Sustainable Reverse Engineering Methodology Assisting 3D Modeling of Footwear Safety Metallic Components. Vol. 2A: Advanced Manufacturing. San Diego. doi: https://doi.org/10.1115/imece2013-65190
- Saiga, K., Ullah, A. S., Kubo, A., Tashi. (2021). A Sustainable Reverse Engineering Process. Procedia CIRP, 98, 517–522. doi: https://doi.org/10.1016/j.procir.2021.01.144
- Technical specifications Artec Space Spider. Available at: https://www.artec3d.com/portable-3d-scanners/artec-spider#specifications
- Maiorova, K., Sikulskyi, V., Vorobiov, Iu., Kapinus, O., Knyr, A.; Nechyporuk, M., Pavlikov, V., Kritskiy, D. (Eds.) (2022). Study of a geometry accuracy of the bracket-type parts using reverse engineering and additive manufacturing technologies. Integrated Computer Technologies in Mechanical Engineering – 2022. ICTM 2022. Vol. 657. Kharkiv: National Aerospace University «Kharkiv Aviation Institute», 146–158. doi: https://doi.org/10.1007/978-3-031-36201-9_13
- Sikulskyi, V., Maiorova, K., Shypul, O., Nickichanov, V., Kapinus, O.; Nechyporuk, M., Pavlikov, V., Kritskiy, D. (Eds.) (2023). Algorithm for Selecting the Optimal Technology for Rapid Manufacturing and/or Repair of Parts. Integrated Computer Technologies in Mechanical Engineering – 2023. ICTM 2023. Kharkiv: National Aerospace University «Kharkiv Aviation Institute». (in print)
- Anwar, M. Y., Ikramullah, S., Mazhar, F. (2014). Reverse engineering in modeling of aircraft propeller blade – first step to product optimization. IIUM Engineering Journal, 15 (2). doi: https://doi.org/10.31436/iiumej.v15i2.497
- Guan, G., Wen-Wen, G. (2019). Reconstraction of propeller and complex ship hull surface based on reverse engineering. Journal of Marine Science and Technology, 27 (6), 498–504. doi: https://doi.org/10.6119/JMST.201912_27(6).0002
- Gómez, A., Olmos, V., Racero, J., Ríos, J., Arista, R., Mas, F. (2017). Development based on reverse engineering to manufacture aircraft custom-made parts. International Journal of Mechatronics and Manufacturing Systems, 10 (1), 40–58. doi: https://doi.org/10.1504/ijmms.2017.084406
- Dubovska, R., Jambor, J., Majerik, J. (2014). Implementation of CAD/CAM System CATIA V5 in Simulation of CNC Machining Process. Procedia Engineering, 69, 638–645. doi: https://doi.org/10.1016/j.proeng.2014.03.037
- Hoque, A. S. M., Halder, P. K., Parvez, M. S., Szecsi, T. (2013). Integrated manufacturing features and Design-for-manufacture guidelines for reducing product cost under CAD/CAM environment. Computers & Industrial Engineering, 66 (4), 988–1003. doi: https://doi.org/10.1016/j.cie.2013.08.016
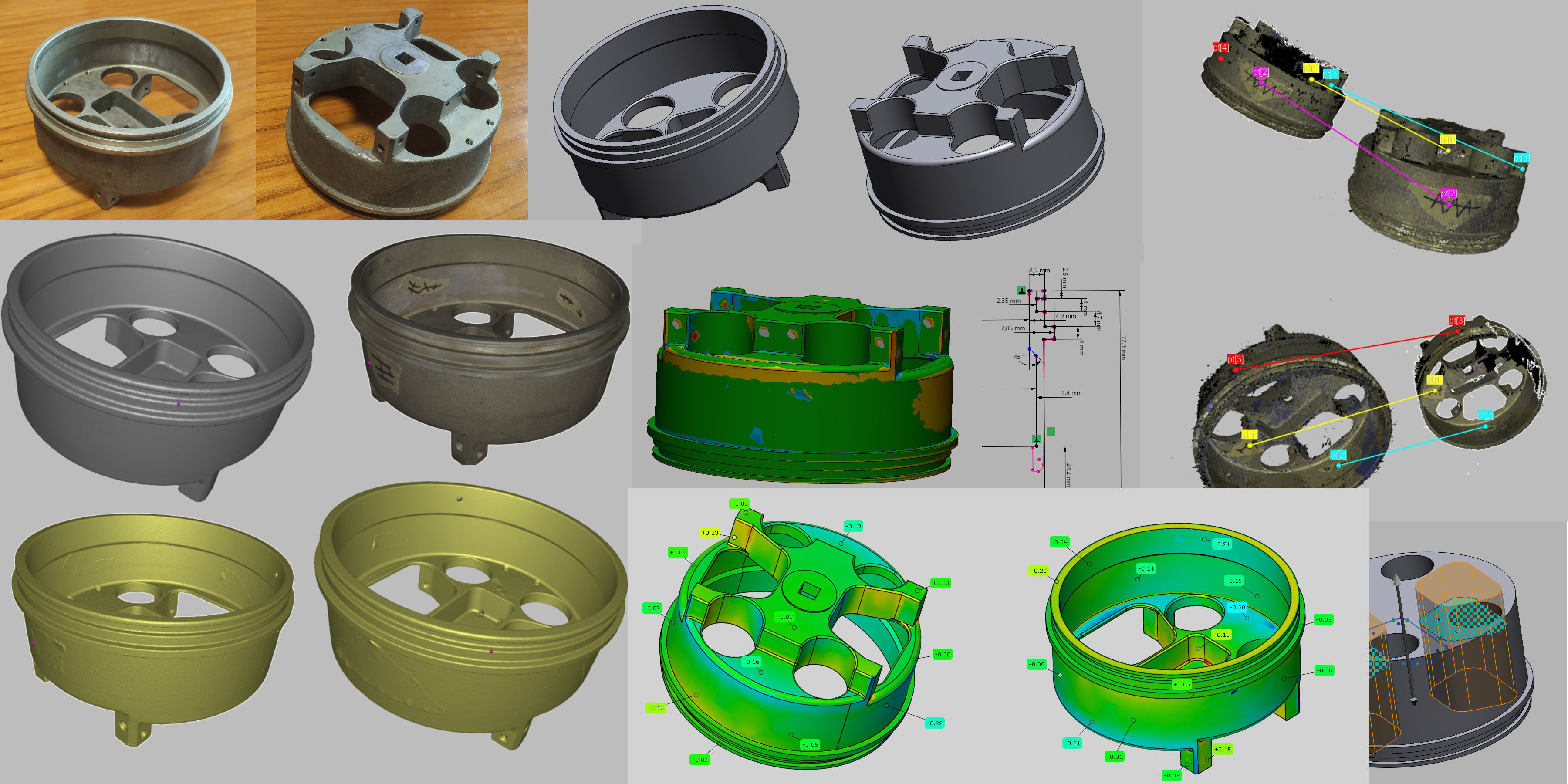
Downloads
Published
How to Cite
Issue
Section
License
Copyright (c) 2024 Kateryna Maiorova, Oleksandra Kapinus, Oleksandr Skyba

This work is licensed under a Creative Commons Attribution 4.0 International License.
The consolidation and conditions for the transfer of copyright (identification of authorship) is carried out in the License Agreement. In particular, the authors reserve the right to the authorship of their manuscript and transfer the first publication of this work to the journal under the terms of the Creative Commons CC BY license. At the same time, they have the right to conclude on their own additional agreements concerning the non-exclusive distribution of the work in the form in which it was published by this journal, but provided that the link to the first publication of the article in this journal is preserved.