Exploring the possibility of undesirable manufacturing heritage reduction in parts made of composites and their joints
DOI:
https://doi.org/10.15587/2706-5448.2024.299227Keywords:
residual stress, reinforcing material, synergetic method, composites, impulse loading, metal tipsAbstract
The object of the research is the possibility of improving the quality of parts made of composites (CM) by means of pre-polymerization treatment of the wet package with intensive pulse loading. The existing technologies for forming parts from CM involve the compaction of the collected impregnated package of reinforcement layers and their subsequent polymerization under the influence of pressure and temperature. As a result of this technology, residual thermal and shrinkage stresses occur in the composite package, which lead to undesirable spatial deformations of profile parts, a violation of monolithicity in the areas of the connection of the composite and metal ends.
Using the example of an angular composite profile with a profile with doubler on one of the caps, the residual stress calculation is given and the method of choosing rational angles for stacking the reinforcing material is demonstrated in order to reduce the amount of residual thermal stresses that arise in the composite during its polymerization. The dependence of the twisting parameter of a long-dimensional composite profile of constant cross-section along its axis on the modulus of elasticity and the coefficient of linear temperature expansion is plotted. The work explains the mechanism of the emergence of such harmful technological heredity. The value of the residual deformations was estimated.
Based on the analysis of the impregnation process of dry reinforcing material with a binder, the task of increasing the maximum contact area of the binder with fibers is formulated and a possible method of its increase is analyzed. Thus, using the model of capillaries between the fibers of the composite, it is concluded that it is necessary to apply additional pressure to the binder for its deeper advancement between the fibers.
Using a synergistic method of combining knowledge from various branches of industry and based on experimental data, a process of pre-polymerization loading of the impregnated package with intense impulse loading (shock waves) is proposed. This process greatly improves the quality of parts of the units produced.
References
- Guz, A. N., Tomashevskii, V. T., Shulga, N. A., Iakovlev, V. S. (1982). Tekhnologicheskie napriazheniia i deformatcii v kompozitcionnykh materialakh. Kyiv: Vishcha shkola, 270.
- Cappello, R., Pitarresi, G., Catalanotti, G. (2023). Thermoelastic Stress Analysis for composite laminates: A numerical investigation. Composites Science and Technology, 241, 110103. doi: https://doi.org/10.1016/j.compscitech.2023.110103
- Kučera, P., Kondratiev, A., Píštěk, V., Taranenko, I., Nabokina, T., Kaplan, Z. (2023). Thin-walled open-profile composite beams under thermo-mechanical loading. Composite Structures, 312, 116844. doi: https://doi.org/10.1016/j.compstruct.2023.116844
- Taranenko, I. M. (2003). Raschet deformirovannogo sostoianiia z-obraznogo kompozitnogo profilia. Voprosy proektirovaniia i proizvodstva konstruktcii letatelnykh apparatov, 33 (2), 67–73.
- Belmas, I., Bilous, O., Tantsura, H. (2022). Determination of the stress-deformed state of a multilayer composite. Strength of Materials and Theory of Structures, 109, 426–440. doi: https://doi.org/10.32347/2410-2547.2022.109.426-440
- Teixidó, H., Staal, J., Caglar, B., Michaud, V. (2022). Capillary Effects in Fiber Reinforced Polymer Composite Processing: A Review. Frontiers in Materials, 9. doi: https://doi.org/10.3389/fmats.2022.809226
- Krivtcov, V. S., Gilmanov, E. S. (1998). Formovanie kompozitnykh konstruktcii impulsnym metodom. Sovershenstvovanie protcessov i oborudovaniia obrabotki davleniem v metallurgii i mashinostroenii. Kramatorsk, 268–272.
- de Almeida, E., Hofland, B. (2020). Validation of pressure-impulse theory for standing wave impact loading on vertical hydraulic structures with short overhangs. Coastal Engineering, 159, 103702. doi: https://doi.org/10.1016/j.coastaleng.2020.103702
- Gulyi, G. A. (1990). Nauchnye osnovy razriadnoimpulsnykh tekhnologii. Kyiv: Naukova dumka, 208.
- Taranenko, M. E. (2011). Elektrogidravlicheskaia shtampovka: teoriia, oborudovanie, tekhprotcessy. Kharkiv: Natc. aerokosm. un-t im. N. E. Zhukovskogo «Khark. aviatc. in-t», 272.
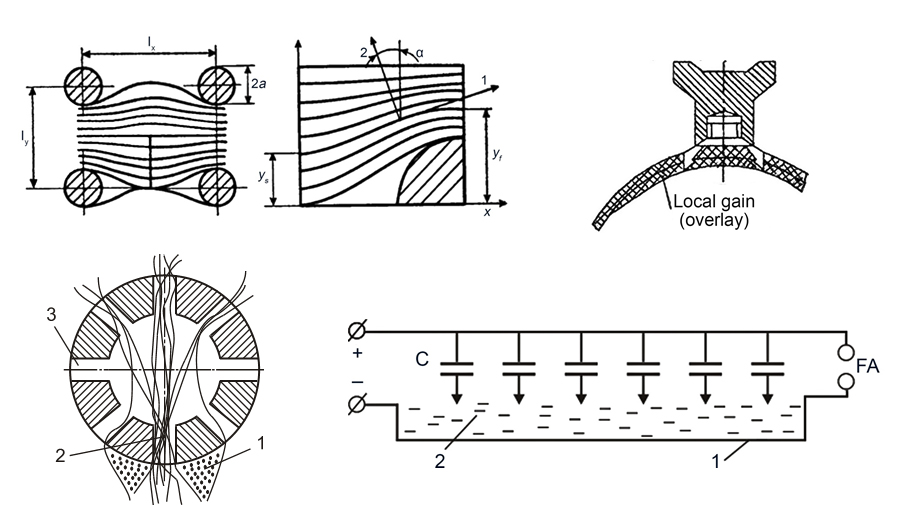
Downloads
Published
How to Cite
Issue
Section
License
Copyright (c) 2024 Igor Taranenko, Tetiana Kupriianova

This work is licensed under a Creative Commons Attribution 4.0 International License.
The consolidation and conditions for the transfer of copyright (identification of authorship) is carried out in the License Agreement. In particular, the authors reserve the right to the authorship of their manuscript and transfer the first publication of this work to the journal under the terms of the Creative Commons CC BY license. At the same time, they have the right to conclude on their own additional agreements concerning the non-exclusive distribution of the work in the form in which it was published by this journal, but provided that the link to the first publication of the article in this journal is preserved.