Consideration of ways to improve the efficiency of deep well drilling
DOI:
https://doi.org/10.15587/2706-5448.2024.314138Keywords:
well, drilling, dynamic state, screw amplifier, mechanical speed, deepening per runAbstract
The object of the research is the composition of the bottom of the drill string when installing screw amplifiers. One of the biggest problems is the place of installation of the screw amplifier in the arrangement of the bottom of the drill string and its influence on the dynamic properties of the rock-crushing tool.
The results of the study of the influence of the use of a screw amplifier on the efficiency of drilling deep wells were obtained. According to the results of research, it was determined in particular that the imposition of vibrations often causes a change in the nature of the interaction of the bit with the hole rock, therefore, the installation of the amplifier at different points of the layout will have different effects on the drilling performance. It is shown that the kinetic energy accumulated by the weighted drill pipes, when the amplifier is installed above the bit, is transmitted through the screw mechanism to the rock-destroying tool (bit) and is an operation that leads to an increase in drilling performance.
Thanks to the conducted research, it has been proven that the property of the drill string elements and the disturbances of the oscillatory processes of various nature acting on them are related to the dynamic loading of its elements due to the installation of the amplifier in different places of the layout of the bottom of the string. This is due to the fact that the proposed screw amplifier is used with a friction fuse, which causes the rotary movement of the screw under the action of the torque and the translational movement of the nut together with the overbit mass attached to the bit.
In most practical cases, especially during deep drilling, bits fail due to the destruction of the rolling bearings of the roller bit, which leads to jamming of the roller bit and leaving them in the holes. For practical use, the proposed design uses a friction fuse, which connects the bit to the drill pipe column through an elastic element. Analytical studies and performed calculations show that this screw amplifier will effectively ensure the destruction of any rocks, especially during overloads without slippage of reaches and be used for the construction of wells in native mining and geological conditions.
References
- Ogorodnikov, P. I. (1991). Upravlenie uglubleniem zaboia skvazhiny na baze izucheniia dinamicheskikh protcesov v burilnoi kolone. Doctoral dissertation. MINKhiGP im akad. Gubkina I. P.
- Pavlychenko, A. V., Koroviaka, Ye. A., Ihnatov, A. O., Davydenko, O. M. (2021). Hidrohazodynamichni protsesy pry sporudzhenni ta ekspluatatsii sverdlovyn. Dnipro: NTU «DP», 201.
- Spanos, P. D., Chevallier, A. M., Politis, N. P., Payne, M. L. (2003). Oil and Gas Well Drilling: A Vibrations Perspective. The Shock and Vibration Digest, 35 (2), 85–103. https://doi.org/10.1177/0583102403035002564
- Depouhon, A., Detournay, E. (2014). Instability regimes and self-excited vibrations in deep drilling systems. Journal of Sound and Vibration, 333 (7), 2019–2039. https://doi.org/10.1016/j.jsv.2013.10.005
- Eren, T., Kok, M. V. (2018). A new drilling performance benchmarking: ROP indexing methodology. Journal of Petroleum Science and Engineering, 163, 387–398. https://doi.org/10.1016/j.petrol.2018.01.002
- Heisig, G., Sancho, J., Macpherson, J. D. (1998). Downhole Diagnosis of Drilling Dynamics Data Provides New Level Drilling Process Control to Driller. SPE Annual Technical Conference and Exhibition. https://doi.org/10.2118/49206-ms
- Ohorodnykov, P. Y., Stoliarov, V. A. (1973). A.S. SRSR No. 386122. Naddolotnyi amortyzator. MPK E 21V17/06; published: 14.06.1973. Biul. No. 26.
- Pavlyshyn, L. V., Ohorodnikov, P. I., Yanush, S. I., Svitlytskyi, V. M., Shcherbatiuk, Yu. Z., Fuhlevych, O. M. et al. (2012). Pat. No. 72885U UA. Prystrii pidvyshchenia osovoho navantazhenia. MPK: E21V 17/06, E21V 17/07. No. u201203816; declareted: 29.03.2012, published: 27.08.2012, Bul. No. 16.
- Bocharov, Iu. A. (1976). Vintovye pressy. Mashinostroenie, 245.
- Saroian, A. E. (1979). Burilnye kolonny v glubokom burenii. Nedra, 231.
- Navarro-López, E. M., Cortés, D. (2007). Avoiding harmful oscillations in a drillstring through dynamical analysis. Journal of Sound and Vibration, 307 (1-2), 152–171. https://doi.org/10.1016/j.jsv.2007.06.037
- Kapitaniak, M., Vaziri Hamaneh, V., Páez Chávez, J., Nandakumar, K., Wiercigroch, M. (2015). Unveiling complexity of drill-string vibrations: Experiments and modelling. International Journal of Mechanical Sciences, 101-102, 324–337. https://doi.org/10.1016/j.ijmecsci.2015.07.008
- Ohorodnikov, P. I., Svitlytskyi, V. M. (2018). Pat. No. 123105U UA. Prystrii rehuliuvannia dynamichnoho stanu burylnoi kolony. MPK E21V 17/06. No. u201708539; declareted: 21.08.2017; published: 12.02.2018, Bul. No. 3.
- Eigeles, R. M. (1971). Razrushenie gornykh porod pri burenii. Nedra, 231.
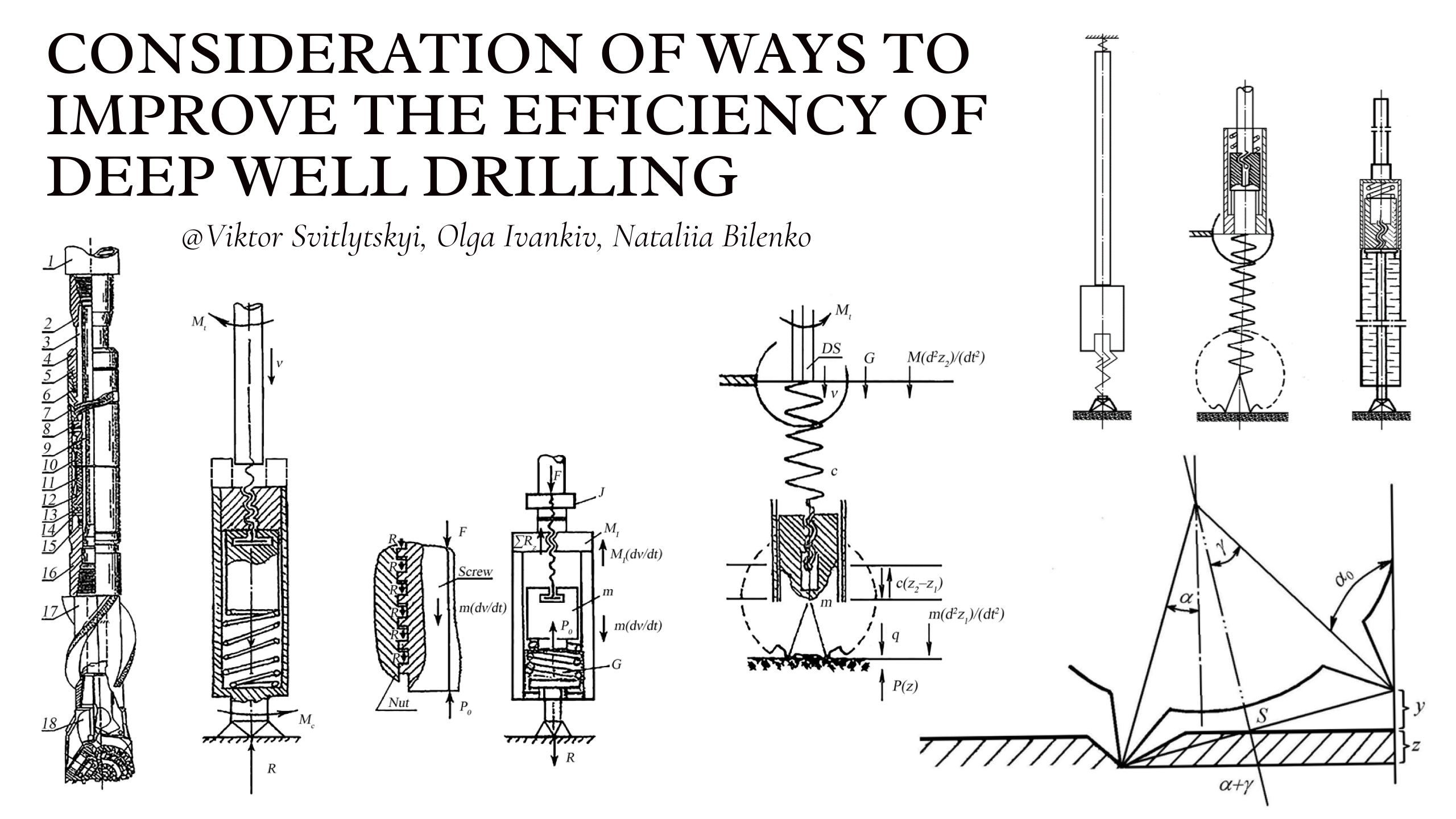
Downloads
Published
How to Cite
Issue
Section
License
Copyright (c) 2024 Viktor Svitlytskyi, Olga Ivankiv, Nataliia Bilenko

This work is licensed under a Creative Commons Attribution 4.0 International License.
The consolidation and conditions for the transfer of copyright (identification of authorship) is carried out in the License Agreement. In particular, the authors reserve the right to the authorship of their manuscript and transfer the first publication of this work to the journal under the terms of the Creative Commons CC BY license. At the same time, they have the right to conclude on their own additional agreements concerning the non-exclusive distribution of the work in the form in which it was published by this journal, but provided that the link to the first publication of the article in this journal is preserved.