Modeling the loading process of pneumatic separation channels
DOI:
https://doi.org/10.15587/2706-5448.2024.320265Keywords:
dynamics of bulk material, grain mixture, distribution uniformity, analytical expressions, rational parameters, separation equipmentAbstract
The object of research is the problem of uniform distribution of bulk materials across the width of the working elements of the separation equipment. Such a problem limits the productivity and quality of the process of separation of bulk materials by aerodynamic and dimensional characteristics. To ensure uniformity of the layer of bulk material across the width, an integrated design of the loading device is proposed, which consists of a gable surface with a variable angle of inclination from the center of the feed to the extreme limits of the device. The working part of the device is made in the form of surfaces of variable width, and the width of each slope of the surface increases proportionally to the distance to the walls of the housing. This allows for controlled distribution of the material across the width. The studies were conducted using analytical and experimental methods. To determine the parameters of the movement of the bulk grain medium along the integrated inclined surface, analytical expressions were obtained that take into account the parameters of the proposed loading device and the properties of the bulk grain material. The patterns of change in the rate of descent of particles of bulk grain material from the inclined surface, as well as the dependence of the velocity of their fall to the hopper bottom, were obtained. Experimental studies were based on high-velocity video recording of the process with identification of dynamic parameters of bulk material and comparison with modeling data. The adequacy of the model was confirmed by experiments with a difference of up to 3.6 %. The influence of the following significant factors on the final velocity of particles of bulk grain material (BGM) was established: the length of the sloping surface at the level of 47.5–116.5 %, then the distance from the surface to the hopper bottom at the level of 76.7–85.6 % and the angle of inclination of the sloping surface at the level of 24.4–41.1 %. The ranges of variation of the BGM particle velocities were established: the initial velocity of particles on the sloping surface 0.82–1.27 m/s, the velocity of particles descending from the sloping surface 0.85–1.43 m/s, the velocity of falling particles 0.68–1.47 m/s. The research results were rational parameters of the integrated loading device, which provides excellent particle movement velocities and leads to uniform distribution of bulk grain material across the width of the separation equipment with an inlet to outlet ratio of (1:5). The results obtained prove the existence and method of scientific and technical solution to the problem, create conditions for further research and design of separation equipment with high technological indicators.
References
- Jesny, S., Prasobh, G. R. (2022). A Review on Size Separation. International Journal of Pharmaceutical Research and Applications, 7 (2), 286–296. Available at: https://ijprajournal.com/issue_dcp/A%20Review%20on%20Size%20Separation.pdf
- Adamchuk, V., Bulgakov, V., Ivanovs, S., Holovach, I., Ihnatiev, Y. (2021). Theoretical study of pneumatic separation of grain mixtures in vortex flow. 20th International Scientific Conference Engineering for Rural Development Proceedings. https://doi.org/10.22616/erdev.2021.20.tf139
- Hou, J., Liu, X., Zhu, H., Ma, Z., Tang, Z., Yu, Y., Jin, J., Wang, W. (2023). Design and Motion Process of Air-Sieve Castor Cleaning Device Based on Discrete Element Method. Agriculture, 13 (6), 1130. https://doi.org/10.3390/agriculture13061130
- Liu, H., Jia, J., Liu, N., Hu, X., Zhou, X. (2018). Effect of material feed rate on sieving performance of vibrating screen for batch mixing equipment. Powder Technology, 338, 898–904. https://doi.org/10.1016/j.powtec.2018.07.046
- Mohanty, M. K., Palit, A., Dube, B. (2002). A comparative evaluation of new fine particle size separation technologies. Minerals Engineering, 15 (10), 727–736. https://doi.org/10.1016/s0892-6875(02)00169-3
- Tishchenko, L. (2004). Intensification of grain separation. Kharkiv: Osnova, 224.
- Kharchenko, S., Kovalyshyn, S., Zavgorodniy, A., Kharchenko, F., Mikhaylov, Y. (2019). Effective sifting of flat seeds through sieve. INMATEH-Agricultural Engineering, 58 (2), 17–26. Available at: http://elar.tsatu.edu.ua/bitstream/123456789/15835/1/EFFECTIVE%20SIFTING%20OF%20FLAT%20SEEDS%20THROUGH%20SIEVE.pdf
- Nesterenko, A. V., Leshchenko, S. M., Vasylkovskyi, O. M., Petrenko, D. I. (2017). Analytical assessment of the pneumatic separation quality in the process of grain multilayer feeding. INMATEH-Agricultural Engineering, 53 (3), 65–70. Available at: http://www.inmateh.eu/INMATEH_3_2017/53-09%20Nesterenko.pdf
- Bredykhin, V., Shchur, T., Kis-Korkishchenko, L., Denisenko, S., Ivashchenko, S., Marczuk, A., Dzhidzhora, O., Kubon, M. (2024). Determination of Ways of Improving the Process of Separation of Seed Materials on the Working Surface of the Pneumatic Sorting Table. Agricultural Engineering, 28 (1), 51–70. https://doi.org/10.2478/agriceng-2024-0005
- Pfaff, F., Pieper, C., Maier, G., Noack, B., Kruggel-Emden, H., Gruna, R., Hanebeck, U. D., Wirtz, S., Scherer, V., Längle, T., Beyerer, J. (2016). Improving optical sorting of bulk materials using sophisticated motion models. Tm – Technisches Messen, 83 (2), 77–84. https://doi.org/10.1515/teme-2015-0108
- Lukyanenko, V. (2015). Choice of continuum dynamics model to describe vibration separation processes of seed mixtures. MOTROL. Commission of Motorization and Energetics in Agriculture, 17 (7), 3–10.
- Aliiev, E., Gavrilchenko, A., Tesliuk, H., Tolstenko, A., Koshul’ko, V. (2019). Improvement of the sunflower seed separation process efficiency on the vibrating surface. Acta Periodica Technologica, 50, 12–22. https://doi.org/10.2298/apt1950012a
- Kovalyshyn, S., Ptashnyk, V., Shvets, O., Ivashchyshyn, F., Nester, B., Kasner, R., Urbańska, P. (2021). The separation assessment of small-seeded mixtures of agricultural crops. Journal of Physics: Conference Series, 1781 (1), 012020. https://doi.org/10.1088/1742-6596/1781/1/012020
- Nanka, A., Kharchenko, S., Sementsov, V. I., Sementsov, V. V., Abduev, M. (2019). Intensification of the process of dosing bulk concentrated feeds by sieve hopper. Eastern-European Journal of Enterprise Technologies, 2 (1 (98)), 14–20. https://doi.org/10.15587/1729-4061.2019.161410
- Bredykhin, V., Tikunov, S., Slipchenko, M., Alfyorov, O., Bogomolov, A., Shchur, T., Kocira, S., Kiczorowski, P., Paslavskyy, R. (2023). Improving Efficiency of Corn Seed Separation and Calibration Process. Agricultural Engineering, 27 (1), 241–253. https://doi.org/10.2478/agriceng-2023-0018
- Kharchenko, S., Borshch, Y., Kovalyshyn, S., Piven, M., Abduev, M., Miernik, A., Popardowski, E., Kiełbasa, P. (2021). Modeling of Aerodynamic Separation of Preliminarily Stratified Grain Mixture in Vertical Pneumatic Separation Duct. Applied Sciences, 11 (10), 4383. https://doi.org/10.3390/app11104383
- Akhmadiev, F. G., Gizzyatov, R. F., Kiyamov, Kh. G. (2013). Mathematical modeling of thin-layer separation of granular materials on sieve classifiers. Theoretical Foundations of Chemical Engineering, 47 (3), 254–261. https://doi.org/10.1134/s0040579513030019
- Piven, M. (2019). Research on the effect of the initial speed of the mixture on the process of loading. Vibrations in Engineering and Technology, 4 (95), 47–55. https://doi.org/10.37128/2306-8744-2019-4-6
- Koruniak, P. S., Vankevych, P. I. (2005). Dozator. Patent na KM No. 10316, MPK G01F 11/10. No. u200503404; zavl. 11.04.2005; opubl. 15.11.2005, biul. No. 11.
- Olshanskii, V. P., et al. (2017). Teoriia separuvannia zerna. Kharkiv: KhNTUSH, 802.
- Kharchenko, S. O., Bilovod, O. I., Abduyev, M. M., Lytvynenko, V. V., Volvach, T. S. (2024). Study of air flow uniformity in the working zones of pneumatic separation channels. Bulletin of Sumy National Agrarian University. The Series: Mechanization and Automation of Production Processes, 2 (56), 90–100. https://doi.org/10.32782/msnau.2024.2.13
- Zaika, P. M. (2006). Teoriya silskohospodarskykh mashyn. Ochystka i sortuvannia zerna. Kharkiv: Oko, 408.
- Kharchenko, S., Kovalyshyn, S., Bakum, M., Krekot, M., Maiboroda, M. (2023). Sposib pidvyshchennia rivnomirnosti podachi vykhidnoho zernovoho materialu zavantazhuvalnym prystroiem zernoochysnoi mashyny. Patent na KM No. 152714, MPK G01F 11/10. No. u202201515; zavl. 11.05.2022; opubl. 05.04.2023, biul. No. 14.
- Kharchenko, S. O. et al. (2023). Zavantazhuvalnyi prystrii zernoochysnoi mashyny. Patent na KM No. 152715, MPK V02V7/00. No. u202201610; zavl. 18.05.2022; opubl. 05.04.2023, biul. No. 14.
- Bakum, N. V., Olshanskyi, V. P., Krekot, N. N. (2015). Yssledovanyia parametrov dvyzhenyia chastyts v ploskom naklonnom kanale pnevmatycheskoho separatora. Inzheneriia pryrodokorystuvannia, 1, 50–55.
- Tishchenko, L. N., Ol’shanskii, V. P., Ol’shanskii, S. V. (2011). On velocity profiles of an inhomogeneous vibrofluidized grain bed on a shaker. Journal of Engineering Physics and Thermophysics, 84 (3), 509–514. https://doi.org/10.1007/s10891-011-0498-4
- Piven, M. (2015). Grain flow dynamics on vibrating flat sieve of finite width. TEKA. Commission of motorization and energetics in agriculture, 15 (3), 113–119.
- Kharchenko, S. O. (2017). Intensification of grain sifting on flat sieves of vibration grain separators. Kharkiv: Disa+, 220.
- Coetzee, C. J., Scheffler, O. C. (2022). Review: The Calibration of DEM Parameters for the Bulk Modelling of Cohesive Materials. Processes, 11 (1), 5. https://doi.org/10.3390/pr11010005
- Huang, H., Zhang, Y., Wang, D., Fu, Z., Tian, H., Shang, J., Helal, M., Lv, Z. (2024). Study the Flow Capacity of Cylindrical Pellets in Hopper with Unloading Paddle Using DEM. Agriculture, 14 (4), 523. https://doi.org/10.3390/agriculture14040523
- Sarno, L., Carravetta, A., Tai, Y.-C., Martino, R., Papa, M. N., Kuo, C.-Y. (2018). Measuring the velocity fields of granular flows – Employment of a multi-pass two-dimensional particle image velocimetry (2D-PIV) approach. Advanced Powder Technology, 29 (12), 3107–3123. https://doi.org/10.1016/j.apt.2018.08.014
- Product-Manual. Phantom Miro M-series Item-Number(s): 1102200/01/02, 1102210/11/12, 1102220/21/22 (2015). Göttingen: LaVision GmbH, Germany, 56.
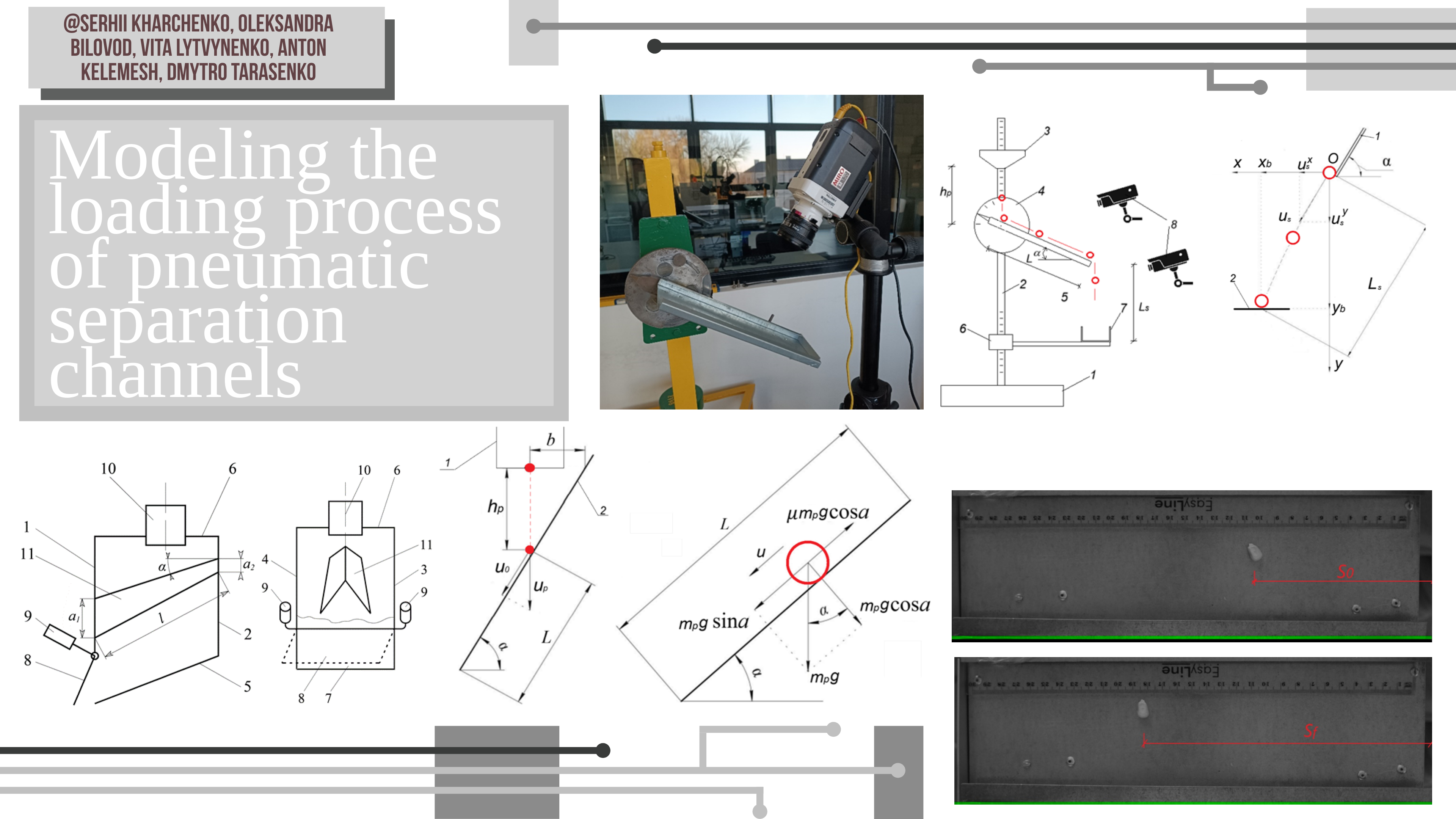
Downloads
Published
How to Cite
Issue
Section
License
Copyright (c) 2024 Serhii Kharchenko, Oleksandra Bilovod, Vita Lytvynenko, Anton Kelemesh, Dmytro Tarasenko

This work is licensed under a Creative Commons Attribution 4.0 International License.
The consolidation and conditions for the transfer of copyright (identification of authorship) is carried out in the License Agreement. In particular, the authors reserve the right to the authorship of their manuscript and transfer the first publication of this work to the journal under the terms of the Creative Commons CC BY license. At the same time, they have the right to conclude on their own additional agreements concerning the non-exclusive distribution of the work in the form in which it was published by this journal, but provided that the link to the first publication of the article in this journal is preserved.