Improving the technology of manufacturing cast brake drums in pink sand molds
DOI:
https://doi.org/10.15587/2706-5448.2024.301715Keywords:
brake drum, chemical composition of cast iron, allowances for mechanical processing, serial melting of cast iron, charge materials, strength limit of cast ironAbstract
The object of research in the paper is the production technology of casting «brake drum» from cast iron of the basic grade SCh20 according to GOST 1412-85 (DSTU EN 1561, EN-GJL-200). The existing problem is that due to the imperfection of the technological processes of manufacturing castings, final internal defects of a shrinking nature are possible. This can lead to a decrease in the strength and operational reliability of the drums, regardless of the chemical composition, which may meet the technical conditions and should provide the specified strength indicators according to the grade of cast iron.
Based on the results of 3D modeling, it has been found that with the existing technology of manufacturing brake drum castings in one-time sand molds, final shrinkage defects are formed in the upper part of the casting. To eliminate this problem, a decision is proposed to increase the allowance for mechanical processing on the upper surface of the casting. The possible excess of the mass of the casting and excess consumption of the alloy that will occur when implementing this solution can be compensated by reducing the allowance on other surfaces based on their optimization by the method of dimensional chains and reducing the thickness of the casting wall. For this, a reduction in the carbon content in the alloy is proposed as a factor in increasing the tensile strength of cast iron. On the basis of 90 serial meltings in industrial conditions, the possibility of increasing the strength limit of cast iron by approximately 11 % by reducing the average carbon content in cast iron from 3.45 % to 3.4 % has been proven.
The proposed solutions are the essence of improving the production technology of cast brake drums, which are produced by casting in one-time sand molds.
The presented study will be useful for machine-building enterprises that have foundries in their structure, where iron is melted for the production of castings.
References
- Savchenko, Yu. E. (2012). Use of computer-integrated systems and technology in the production of pistons. Technology Audit and Production Reserves, 1 (1 (3)), 8–13. doi: https://doi.org/10.15587/2312-8372.2012.4868
- Alekhin, V. I., Belogub, A. V., Marchenko, A. P., Akimov, O. V. (2009). Kompiuterno-integrirovannoe modelirovanie liteinykh protcessov v avtomobilnykh porshniakh na osnove konstruktorsko – tekhnologicheskoi metodiki proektirovaniia detalei DVS. Dvigateli vnutrennego sgoraniia, 2, 101–104.
- Krasnokutskyi, E. A. (2012). The simulation of crystallization in a metal mold cast parts. Technology Audit and Production Reserves, 1 (1 (3)), 3–8. doi: https://doi.org/10.15587/2312-8372.2012.4867
- Alekhin, V. I., Belogub, A. V., Marchenko, A. P., Akimov, O. V. (2010). Modelirovanie mest proiavleniia defektov usadochnogo kharaktera pri proektirovanii litykh detalei DVS. Metall i lite Ukrainy, 12, 27–30.
- Orendarchuk, Y., Marynenko, D., Borysenko, S., Loek, I., Anan’in, V. (2017). Monitoring of castings quality for use in cad systems of foundry production technologies. ScienceRise, 4 (2), 48–52. doi: https://doi.org/10.15587/2313-8416.2017.99442
- Ponomarenko, O. Y., Trenev, N. S. (2013). Computer modeling of crystallization processes as a reserve of improving the quality of pistons of ICE. Technology Audit and Production Reserves, 6 (2 (14)), 36–40. doi: https://doi.org/10.15587/2312-8372.2013.19529
- Akimov, O. V. (2003). Analiz pogreshnostei formoobrazovaniia otlivok koles turbin turbokompressorov dlia nadduva DVS na etape izgotovleniia ikh voskovykh modelei. Eastern-European Journal of Enterprise Technologies, 3 (3), 16–24.
- Penzev, P., Pulyaev, A., Gulaga, M., Vlasiuk, V., Makarenko, D. (2017). Parametric classification of pistons of internal combustion engines parts according to the «hole axis shift relative to the piston axis» criterion. ScienceRise, 5 (2 (34)), 3–41. doi: https://doi.org/10.15587/2313-8416.2017.101975
- Chibichik, O., Sil’chenko, K., Zemliachenko, D., Korchaka, I., Makarenko, D. (2017). Investigation of the response surface describing the mathematical model of the effects of the Al/Mg rate and temperature on the Al-Mg alloy castability. ScienceRise, 5 (2 (34)), 42–45. doi: https://doi.org/10.15587/2313-8416.2017.101923
- Frolova, L. (2023). Search procedure for optimal design and technological solutions to ensure dimensional and geometric accuracy of castings. Technology Audit and Production Reserves, 1 (1 (69)), 18–25. doi: https://doi.org/10.15587/2706-5448.2023.271860
- Borsato, T., Berto, F., Ferro, P., Carollo, C. (2016). Effect of in-mould inoculant composition on microstructure and fatigue behaviour of heavy section ductile iron castings. Procedia Structural Integrity, 2, 3150–3157. doi: https://doi.org/10.1016/j.prostr.2016.06.393
- Bai, Y., Luan, Y., Song, N., Kang, X., Li, D., Li, Y. (2012). Chemical Compositions, Microstructure and Mechanical Properties of Roll Core used Ductile Iron in Centrifugal Casting Composite Rolls. Journal of Materials Science & Technology, 28 (9), 853–858. doi: https://doi.org/10.1016/s1005-0302(12)60142-x
- Frolova, L., Barsuk, A., Nikolaiev, D. (2022). Revealing the significance of the influence of vanadium on the mechanical properties of cast iron for castings for machine-building purpose. Technology Audit and Production Reserves, 4 (1 (66)), 6–10. doi: https://doi.org/10.15587/2706-5448.2022.263428
- Lysenkov, V., Demin, D. (2023). Adaptive method of estimating the dynamic characteristics of the bottom pressing process when making disposable casting molds. Technology Audit and Production Reserves, 5 (1 (73)), 6–11. doi: https://doi.org/10.15587/2706-5448.2023.288152
- Endo, M., Yanase, K. (2014). Effects of small defects, matrix structures and loading conditions on the fatigue strength of ductile cast irons. Theoretical and Applied Fracture Mechanics, 69, 34–43. doi: https://doi.org/10.1016/j.tafmec.2013.12.005
- Demin, D. (2019). Development of «whole» evaluation algorithm of the control quality of «cupola – mixer» melting duplex process. Technology Audit and Production Reserves, 3 (1 (47)), 4–24. doi: https://doi.org/10.15587/2312-8372.2019.174449
- Lysenkov, V., Demin, D. (2022). Reserves of resource saving in the manufacture of brake drums of cargo vehicles. ScienceRise, 3, 14–23. doi: https://doi.org/10.21303/2313-8416.2022.002551
- Kharchenko, S., Barsuk, A., Karimova, N., Nanka, A., Pelypenko, Y., Shevtsov, V. et al. (2021). Mathematical model of the mechanical properties of Ti-alloyed hypoeutectic cast iron for mixer blades. EUREKA: Physics and Engineering, 3, 99–110. doi: https://doi.org/10.21303/2461-4262.2021.001830
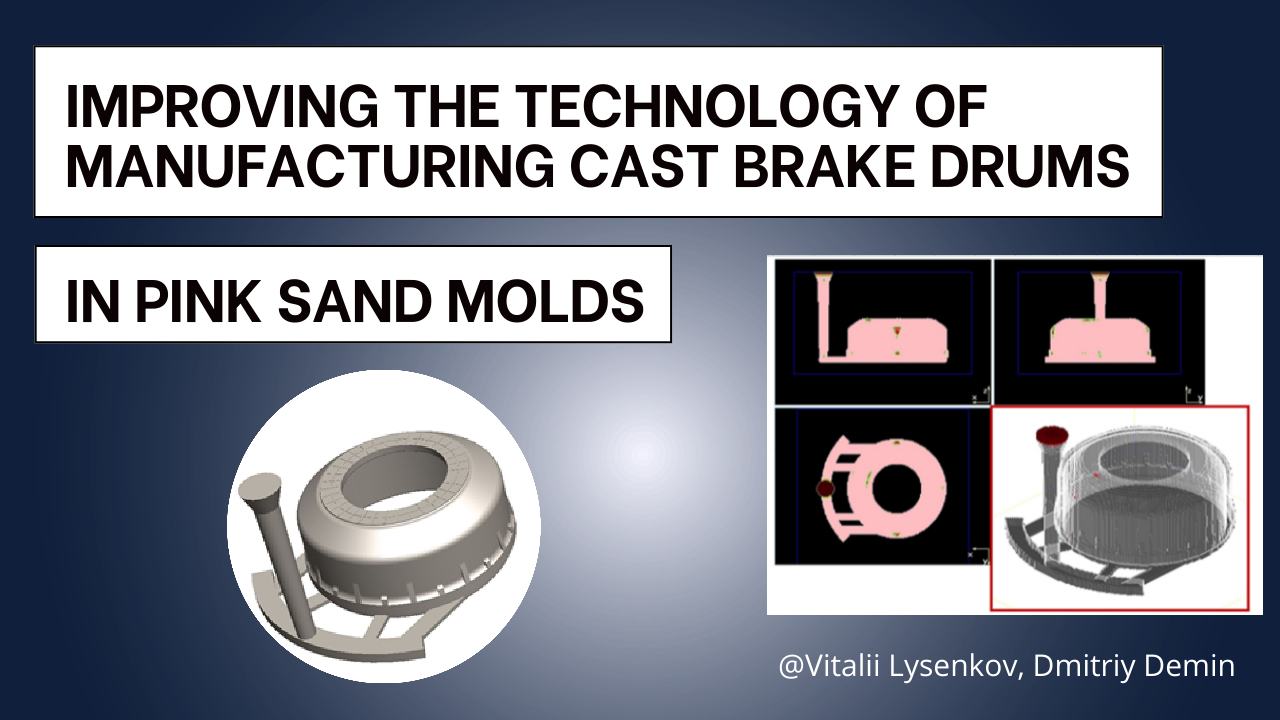
Downloads
Published
How to Cite
Issue
Section
License
Copyright (c) 2024 Vitalii Lysenkov, Dmitriy Demin

This work is licensed under a Creative Commons Attribution 4.0 International License.
The consolidation and conditions for the transfer of copyright (identification of authorship) is carried out in the License Agreement. In particular, the authors reserve the right to the authorship of their manuscript and transfer the first publication of this work to the journal under the terms of the Creative Commons CC BY license. At the same time, they have the right to conclude on their own additional agreements concerning the non-exclusive distribution of the work in the form in which it was published by this journal, but provided that the link to the first publication of the article in this journal is preserved.