Increasing the strength of building ceramics made on the basis of low-melting clays
DOI:
https://doi.org/10.15587/2706-5448.2022.266605Keywords:
ceramic materials, clay raw materials, mechanical strength, silica materials, building ceramics, rotten stone additiveAbstract
The object of the study is the physical and chemical processes of formation of the structure and properties, intensification of sintering of ceramic masses based on local raw materials (Krynichanska low-melting clay raw materials of the Kyiv region, Ukraine) by regulating the chemical and mineralogical composition and technological regimes. When choosing clay raw materials for specific ceramic technologies, it is necessary to be guided by a comprehensive assessment of the physicochemical properties of clay rock. These can be the granulometric and material composition, including the chemical and mineralogical composition of the clay and impurity components, the presence of amorphous material. The state of order in the structure of clay-forming minerals is also important, the knowledge of which makes it possible to determine the ways of regulating the basic technological properties of clay rock in order to bring them to the required level.
Among physical and mechanical parameters, mechanical strength is one of the main criteria for determining the suitability of raw materials for the production of building ceramics. The conducted studies have shown that with an increase in the amount of rotten stone additive introduced from 10 to 20 % of low-melting clay, the mechanical strength of ceramic samples in compression and bending increases. The introduction of rotten stone additive provides an increase in the coefficient of sensitivity to drying low-melting clay raw materials, which has a positive effect on the crack resistance of raw bricks when drying clay rock in order to bring them to the required level.
The use of silica materials in the composition of ceramic masses based on low-melting clays as an additive to improve the physical and mechanical characteristics of the finished product has shown its effectiveness. This can be explained by the fact that the nature of the interaction of silica additives, which was used as rotten stone, differs from the interaction of clay minerals present in ceramic raw materials with water. Since silica exists in rotten stone in the form of amorphous silica gel, it helps to improve the structure of clay, makes it monolithic, increasing mechanical strength. The impurities of low-melting oxides, which are part of the rotten stone, contribute to the formation of low-melting eutectic, reducing the refractoriness of amorphous silica and have a positive effect on the sintering process, forming a glass phase.
Supporting Agency
- The study was conducted without financial support, within the framework of the search topic «Ceramic materials based on mineral raw materials of the Kyiv region» State registration number 0122U000523.
References
- Manoj, D. (2021). Ceramic Technology Diploma&Engineering MCQ. Objective question answers, 107.
- Shestakov, V. L. (2002). Tekhnolohiia keramichnykh stinovykh i lytsiuvalnykh materialiv. Rivne: UDUVHiP, 243.
- Jensen, N. C. (2009). Marketing Silica (quartz, Tripoli, Diatomite, Etc.). Bureau of Mines, Information circular, 7202, 39.
- Şan, O., Gören, R., Özgür, C. (2009). Purification of diatomite powder by acid leaching for use in fabrication of porous ceramics. International Journal of Mineral Processing, 93 (1), 6–10. doi: https://doi.org/10.1016/j.minpro.2009.04.007
- Mymrine, V., Ponte, M. J. J. S., Ponte, H. A., Kaminari, N. M. S., Pawlowsky, U., Solyon, G. J. P. (2013). Oily diatomite and galvanic wastes as raw materials for red ceramics fabrication. Construction and Building Materials, 41, 360–364. doi: https://doi.org/10.1016/j.conbuildmat.2012.11.041
- Wiśniewska, K., Pichór, W., Kłosek-Wawrzyn, E. (2021). Influence of Firing Temperature on Phase Composition and Color Properties of Ceramic Tile Bodies. Materials, 14 (21), 6380. doi: https://doi.org/10.3390/ma14216380
- Mačiulaitis, R., Malaiškienė, J. (2009). Possibilities to control ceramics properties by changing firing cycles. Construction and Building Materials, 23 (1), 226–232. doi: https://doi.org/10.1016/j.conbuildmat.2007.12.012
- Lin, K.-L., Chang, J.-C. (2011). Feasibility of recycling waste diatomite and fly ash cosintered as porous ceramics. Environmental Progress & Sustainable Energy, 32 (1), 25–34. doi: https://doi.org/10.1002/ep.10592
- Hao, L., Gao, W., Yan, S., Niu, M., Liu, G., Hao, H. (2019). Preparation and characterization of porous ceramics with low-grade diatomite and oyster shell. Materials Chemistry and Physics, 235, 121741. doi: https://doi.org/10.1016/j.matchemphys.2019.121741
- Hossain, S. S., Mathur, L., Roy, P. K. (2018). Rice husk/rice husk ash as an alternative source of silica in ceramics: A review. Journal of Asian Ceramic Societies, 6 (4), 299–313. doi: https://doi.org/10.1080/21870764.2018.1539210
- Li, S., Bao, C., Ma, H., Dong, W., Song, S., Wang, Q. et al. (2022). Fabrication and properties of diatomite ceramics with hierarchical pores based on direct stereolithography. Ceramics International, 48 (5), 6266–6276. doi: https://doi.org/10.1016/j.ceramint.2021.11.169
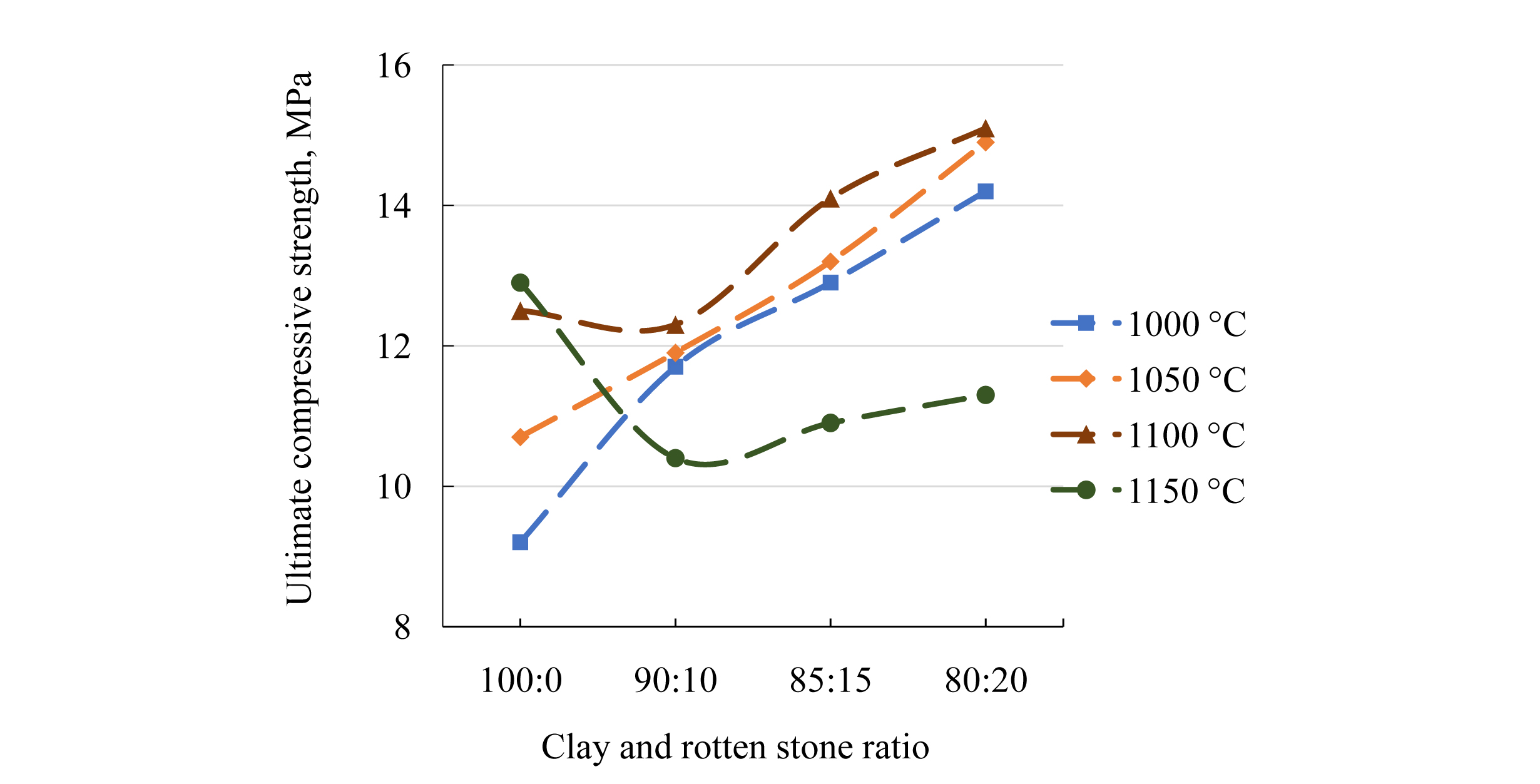
Downloads
Published
How to Cite
Issue
Section
License
Copyright (c) 2022 Іrіna Subbota, Larysa Spasonova, Аnastasia Sholom

This work is licensed under a Creative Commons Attribution 4.0 International License.
The consolidation and conditions for the transfer of copyright (identification of authorship) is carried out in the License Agreement. In particular, the authors reserve the right to the authorship of their manuscript and transfer the first publication of this work to the journal under the terms of the Creative Commons CC BY license. At the same time, they have the right to conclude on their own additional agreements concerning the non-exclusive distribution of the work in the form in which it was published by this journal, but provided that the link to the first publication of the article in this journal is preserved.