Simulation of the work of glass furnaces with the purpose of searching for reserves and increase their efficiency
DOI:
https://doi.org/10.15587/2706-5448.2024.307613Keywords:
glass furnace, regenerators, combustion, electric heating, computer simulation of technological processesAbstract
The object of research is the operation of a glass furnace. The work involved modeling the operation of a glass furnace by changing the technical and economic indicators of its operation in order to optimize the technological processes of manufacturing glass products, increase the energy efficiency of the process, and reduce the ecological burden on the environment. Glass furnaces are complex heat engineering units that require a large amount of energy to operate. Therefore, increasing their effectiveness is the main task of our research. In the work, computer modeling of thermal processes in the furnace was carried out, heat balances were calculated and analyzed, and the performance of the furnace was analyzed after changing and improving the technological regimes of combustion processes, glass boiling and furnace construction. Studies have shown that in order to increase the technical and economic performance of glass furnaces, it is advisable to conduct additional thermal insulation of the furnace enclosures. The thermal insulation of the vault increases the efficiency of the furnace by 2–3 %, and the thermal insulation of the remaining areas of the furnace in total allows to increase the efficiency of the heating unit up to 3 %. Such measures improve the sanitary and technical working conditions of the staff in the machine-bath shop. Studies have shown that additional heating of the air used for burning fuel significantly increases the efficiency of the furnace. Thus, an increase in air temperature by 100 °C increases the efficiency of the furnace by approximately 2.5 %. However, such a measure is possible with a corresponding increase in the volume of regenerator nozzles. A significant increase in the efficiency of the furnace was achieved when additional electric heating was installed. This allows to reduce the total energy costs, and at the same time, the introduction of every 10 % of additional electric heating increases the efficiency of the furnace by up to 3 % and improves the quality of the glass mass. Such additional heating can be recommended in the amount of 20–30 % of the total heat consumption for the operation of the furnace. The analysis of the obtained results showed a fairly good convergence of the results, which indicates the acceptable adequacy of the models. The obtained process simulation results allow choosing the optimal design and operation parameters of the glass furnace. The results of the work can be used in practice for the design of efficient glass furnaces of various purposes and performance.
References
- Plemiannykov, M., Yatsenko, A., Kornilovych, B. (2015). Khimiia i tekhnolohiia skla. Vysokotemperaturni protsesy. Kyiv: Osvita.
- Lecomte, T., Ferreria de La Fuente, J. F., Neuwahl, F., Canova, M., Pinasseau, A., Jankov, I. et al. (2017). Best available techniques (BAT) reference document for large combustion plants. Industrial emissions directive 2010/75/EU (Integrated pollution prevention and control) (No. JRC107769). Joint Research Centre (Seville site).
- Zhdaniuk, N., Pikhulia, N. (2023). Analysis of waste and sources of pollution in glass production. Visnyk of Kherson National Technical University, 1 (84), 9–17. doi: https://doi.org/10.35546/kntu2078-4481.2023.1.1
- Zhdaniuk, N. V., Plemiannikov, M. M. (2022). Enerhotekhnolohiia khimiko-tekhnolohichnykh protsesiv u vyrobnytstvi keramiky ta skla. Palyvo i yoho kharakterystyky. Rozrakhunky horinnia palyva. Kyiv: KPI im. Ihoria Sikorskoho, 62.
- Trier, W. (2013). Glasschmelzöfen: konstruktion und betriebsverhalten. Springer-Verlag. doi: http://doi.org/10.1007/978-3-642-82067-0
- Dolianitis, I., Giannakopoulos, D., Hatzilau, C.-S., Karellas, S., Kakaras, E., Nikolova, E. et al. (2016). Waste heat recovery at the glass industry with the intervention of batch and cullet preheating. Thermal Science, 20 (4), 1245–1258. doi: https://doi.org/10.2298/tsci151127079d
- Conradt, R. (2019). Prospects and physical limits of processes and technologies in glass melting. Journal of Asian Ceramic Societies, 7 (4), 377–396. doi: https://doi.org/10.1080/21870764.2019.1656360
- Mayr, B., Prieler, R., Demuth, M., Potesser, M., Hochenauer, C. (2015). CFD and experimental analysis of a 115 kW natural gas fired lab-scale furnace under oxy-fuel and air–fuel conditions. Fuel, 159, 864–875. doi: https://doi.org/10.1016/j.fuel.2015.07.051
- Wachter, P., Gaber, C., Demuth, M., Hochenauer, C. (2020). Experimental investigation of tri-reforming on a stationary, recuperative TCR-reformer applied to an oxy-fuel combustion of natural gas, using a Ni-catalyst. Energy, 212, 118719. doi: https://doi.org/10.1016/j.energy.2020.118719
- Pashchenko, D. (2022). Natural gas reforming in thermochemical waste-heat recuperation systems: A review. Energy, 251, 123854. doi: https://doi.org/10.1016/j.energy.2022.123854
- Li, L., Lin, H.-J., Han, J., Ruan, J., Xie, J., Zhao, X. (2019). Three-Dimensional Glass Furnace Model of Combustion Space and Glass Tank with Electric Boosting. Materials Transactions, 60 (6), 1034–1043. doi: https://doi.org/10.2320/matertrans.m2019044
- Conradt, R. (2019). Prospects and physical limits of processes and technologies in glass melting. Journal of Asian Ceramic Societies, 7 (4), 377–396. doi: https://doi.org/10.1080/21870764.2019.1656360
- Mase, H., Oda, K. (1980). Mathematical model of glass tank furnace with batch melting process. Journal of Non-Crystalline Solids, 38-39, 807–812. doi: https://doi.org/10.1016/0022-3093(80)90536-0
- Abbassi, A., Khoshmanesh, Kh. (2008). Numerical simulation and experimental analysis of an industrial glass melting furnace. Applied Thermal Engineering, 28 (5-6), 450–459. doi: https://doi.org/10.1016/j.applthermaleng.2007.05.011
- Li, L., Han, J., Lin, H., Ruan, J., Wang, J., Zhao, X. (2019). Simulation of glass furnace with increased production by increasing fuel supply and introducing electric boosting. International Journal of Applied Glass Science, 11 (1), 170–184. Portico. doi: https://doi.org/10.1111/ijag.13907
- Raič, J., Gaber, C., Wachter, P., Demuth, M., Gerhardter, H., Knoll, M. et al. (2021). Validation of a coupled 3D CFD simulation model for an oxy-fuel cross-fired glass melting furnace with electric boosting. Applied Thermal Engineering, 195, 117166. doi: https://doi.org/10.1016/j.applthermaleng.2021.117166
- Daurer, G., Raič, J., Demuth, M., Gaber, C., Hochenauer, C. (2023). Detailed comparison of physical fining methods in an industrial glass melting furnace using coupled CFD simulations. Applied Thermal Engineering, 232, 121022. doi: https://doi.org/10.1016/j.applthermaleng.2023.121022
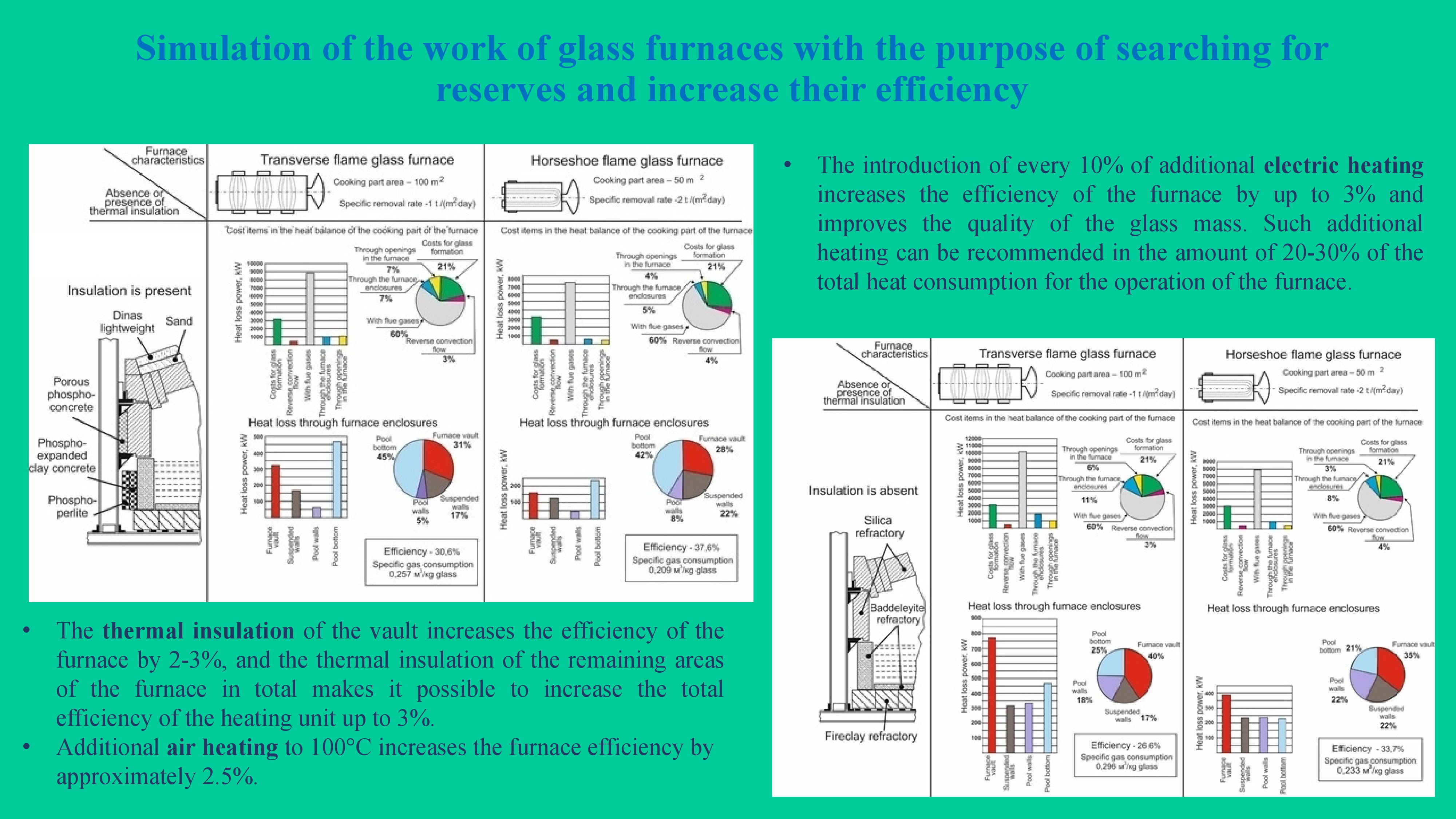
Downloads
Published
How to Cite
Issue
Section
License
Copyright (c) 2024 Nataliіa Zhdanіuk, Oleksii Plemiannikov

This work is licensed under a Creative Commons Attribution 4.0 International License.
The consolidation and conditions for the transfer of copyright (identification of authorship) is carried out in the License Agreement. In particular, the authors reserve the right to the authorship of their manuscript and transfer the first publication of this work to the journal under the terms of the Creative Commons CC BY license. At the same time, they have the right to conclude on their own additional agreements concerning the non-exclusive distribution of the work in the form in which it was published by this journal, but provided that the link to the first publication of the article in this journal is preserved.