Determination of the energy efficiency of granulation equipment based on exergy analysis
DOI:
https://doi.org/10.15587/2706-5448.2024.311777Keywords:
granulation of mineral fertilizers, granulator, urea, filling, rolling, active hydrodynamics, granulation, exergyAbstract
The object of research is the process of granulation of mineral fertilizers by applying rolling and pouring methods, as well as in fluidized and suspended layers with active hydrodynamics of flows. It is noted that the development of the main technological stages of the production of granulated fertilizers should be aimed at improving the hardware design of granulators, establishing the most rational regime and technological parameters of the process in order to increase its efficiency and reduce energy costs. It is noted that the main indicators of the efficiency of granulation plants using heat are economic costs, exergy losses, as well as reduced costs. The method of exergy analysis for the assessment of energy costs for granulation processes in different types of granulators is presented, which allows to justify the choice of rational parameters of the specified processes, taking into account energy costs and equipment efficiency. Equations are presented for determining the amount of exergy of material flows and exergy losses caused by heat exchange at finite temperature differences of technological flows at the entrance to the device and at the exit from it. The equation for determining the exergy efficiency, which characterizes the energy efficiency of the technical system, is presented. The smaller the temperature difference for the technological flows at the exit from the device, the smaller the exergy losses, the higher the value of the exergy efficiency. and, accordingly, the device will have greater energy efficiency. An exergy analysis of granulation processes in granulation towers without a cooler, in granulation towers with a cooler, fluidized bed devices and multi-stage (shelf) devices was carried out. The analysis showed that the exergy efficiency for the specified granulation plants is equal to: 64 %, 71 %, 32 % and 96 %, respectively. The obtained research results can be applied in production conditions where granulation towers and devices of fluidized or suspended layers are used. Enterprises that plan to reduce energy costs and increase the environmental safety of their technological processes can implement improvements based on the proposed methods and equations. The application of research results will contribute to the selection of more rational indicators of the granule production process, which will increase the productivity and quality of the final product.
Supporting Agency
- This project has received funding from the European Union’s Horizon 2020 research and innovation programme under grant agreement No. 871072. Additionally, this research work has been carried out within the project «Fulfillment of tasks of the perspective plan of development of a scientific direction «Technical sciences» Sumy State University» (State Reg. No. 0121U112684) funded by the Ministry of Education and Science of Ukraine.
References
- Arthur, T. B., Chauhan, J., Rahmanian, N. (2022). Process Simulation of Fluidized Bed Granulation: Effect of Process Parameters on Granule Size Distribution. Chemical Engineering Transactions, 95, 241–246. https://doi.org/10.3303/CET2295041
- Artyukhov, A. E., Vakal, S. V., Yanovska, A. O., Shkola, V. Y., Vakal, V. S., Yarova, T. Y. (2020). The Investigation of Nanoporous Structure Morphology and Elemental Composition of Organo-mineral Fertilizer Granules. Journal of Nano- and Electronic Physics, 12 (6). https://doi.org/10.21272/jnep.12(6).06039
- Askarishahi, M., Salehi, M.-S., Radl, S. (2023). Challenges in the Simulation of Drying in Fluid Bed Granulation. Processes, 11 (2), 569. https://doi.org/10.3390/pr11020569
- Azadi, M., Hormozi, F., Sanaei-Moghadam, M., Sarkandy, S. Y. (2024). The role of adding nanoparticles and surfactant to the enzyme liquid binder in fluidized bed granulation process. Powder Technology, 435, 119436. https://doi.org/10.1016/j.powtec.2024.119436
- Jarchow, M. E., Liebman, M. (2012). Nitrogen fertilization increases diversity and productivity of prairie communities used for bioenergy. GCB Bioenergy, 5 (3), 281–289. https://doi.org/10.1111/j.1757-1707.2012.01186.x
- Barrasso, D., Eppinger, T., Pereira, F. E., Aglave, R., Debus, K., Bermingham, S. K., Ramachandran, R. (2015). A multi-scale, mechanistic model of a wet granulation process using a novel bi-directional PBM–DEM coupling algorithm. Chemical Engineering Science, 123, 500–513. https://doi.org/10.1016/j.ces.2014.11.011
- Bellinghausen, S., Gavi, E., Jerke, L., Barrasso, D., Salman, A. D., Litster, J. D. (2022). Model-driven design using population balance modelling for high-shear wet granulation. Powder Technology, 396, 578–595. https://doi.org/10.1016/j.powtec.2021.10.028
- Cotabarren, I. M., Moreno, J., Martínez, A. L., Cabrera, F. A., Piña, J. (2019). Valorization of anaerobic digestion liquid residue through the production of organic fertilizer by fluidized bed granulation. Chemical Engineering Research and Design, 147, 113–121. https://doi.org/10.1016/j.cherd.2019.04.043
- Diez, E., Meyer, K., Bück, A., Tsotsas, E., Heinrich, S. (2018). Influence of process conditions on the product properties in a continuous fluidized bed spray granulation process. Chemical Engineering Research and Design, 139, 104–115. https://doi.org/10.1016/j.cherd.2018.09.032
- Nichvolodin, K., Sklabinskyi, V. (2023). Determination of the heat transfer coefficient between pellets and air during the modernization of a pelletizing tower based on industrial research. Technology Audit and Production Reserves, 6 (3 (74)), 18–21. https://doi.org/10.15587/2706-5448.2023.293264
- Nadhem, A.-K. M., Skydanenko, M., Ostroha, R., Neshta, A., Yukhymenko, M., Yakhnenko, S. et al. (2022). Research of plate granulator operation modes in the production of coarse carbamide granules. Technology Audit and Production Reserves, 1 (3 (63)), 12–15. https://doi.org/10.15587/2706-5448.2022.252367
- Moure Abelenda, A., Amaechi, C. V. (2022). Manufacturing of a Granular Fertilizer Based on Organic Slurry and Hardening Agent. Inventions, 7 (1), 26. https://doi.org/10.3390/inventions7010026
- Yukhimenko, N., Vakal, S. (2016). The exergy analysis of energy efficiency of the technology of granulated phosphorus-potassium fertilizers. Eastern-European Journal of Enterprise Technologies, 5 (6 (83)), 4–10. https://doi.org/10.15587/1729-4061.2016.77182
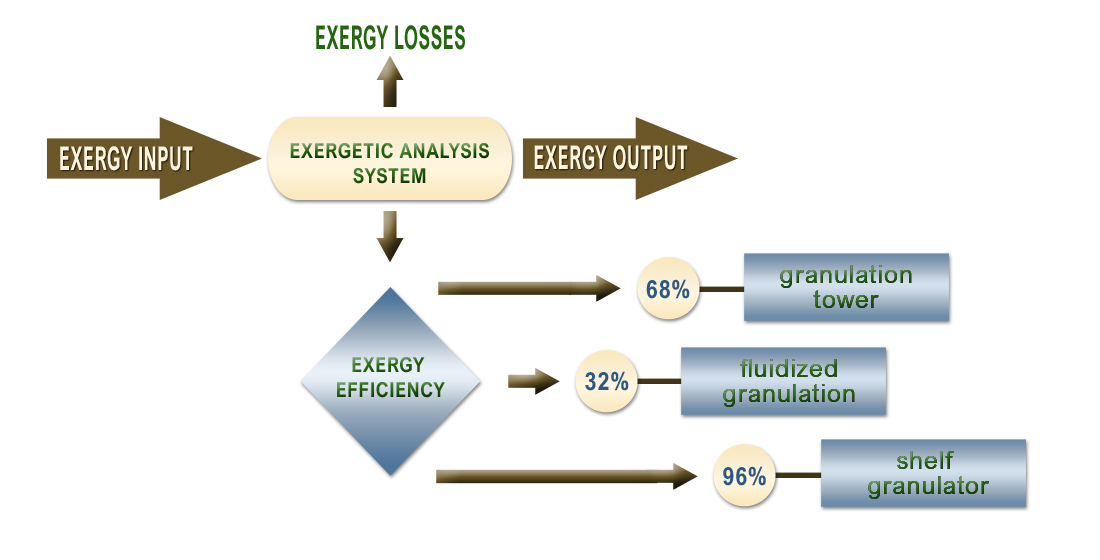
Downloads
Published
How to Cite
Issue
Section
License
Copyright (c) 2024 Ruslan Ostroha, Mykola Yukhymenko, Dmytro Myshchenko, Maksym Skydanenko, Oleksandr Ivchenko, Dmytro Zhyhylii, Liudmyla Ponomarova, Jozef Bocko

This work is licensed under a Creative Commons Attribution 4.0 International License.
The consolidation and conditions for the transfer of copyright (identification of authorship) is carried out in the License Agreement. In particular, the authors reserve the right to the authorship of their manuscript and transfer the first publication of this work to the journal under the terms of the Creative Commons CC BY license. At the same time, they have the right to conclude on their own additional agreements concerning the non-exclusive distribution of the work in the form in which it was published by this journal, but provided that the link to the first publication of the article in this journal is preserved.