Solvents in the industrial synthesis of naphazoline nitrate: implementation of the principles of "Green chemistry" and analysis
DOI:
https://doi.org/10.15587/2519-4852.2024.291468Keywords:
naphazoline nitrate, industrial synthesis, 1,2,4-trichlorobenzene, green chemistry, waste, impurity profile, gas chromatography, ethanolamine, 2-propanol, regenerationAbstract
The aim: implementation of the principles of green chemistry by regenerating the synthesis solvent 1,2,4-trichlorobenzene and reusing it during the synthesis of the Naphazoline nitrate substance. Study of the influence of the regenerated solvent on the quality of the final product by controlling analytical quality parameters. Development of a method for the quantitative determination and validation of synthesis solvents in a substance.
Materials and methods: samples of the substance were synthesized according to the optimized proprietary technology of Farmak JSC. The obtained batches of fresh and regenerated 1,2,4-trichlorobenzene were analyzed according to the monograph of the European Pharmacopoeia on Naphazoline nitrate 0147.
Results: the possibility of using regenerated 1,2,4-trichlorobenzene for the synthesis of the substance Naphazoline nitrate has been proven. It is shown that the regenerated solvent does not have a negative effect on the profile of impurities and the polymorphic form of the substance. Analytical quality parameters met the requirements of the internal specification and the requirements of the European Pharmacopoeia monograph. The developed and validated method of quantitative determination of synthesis solvents makes it possible to determine them at the required level.
Conclusions: the introduction of regenerated 1,2,4-trichlorobenzene into the synthesis scheme made it possible to significantly reduce the amount of waste per 1 kg of product, which in turn significantly reduced the negative impact on the environment. Analytical quality parameters for regenerated 1,2,4-trichlorobenzene meet the requirements of the internal specification. Industrial series obtained on the regenerated solvent meet the requirements of the monograph of the European Pharmacopoeia. The polymorphic form of the substance batches manufactured on regenerated 1,2,4-trichlorobenzene corresponds to the polymorphic form of the substance batches manufactured on the fresh solvent. The obtained results on the influence of the regenerated solvent on the profile of impurities in the finished substance show the similarity of the profile of the series manufactured on both solvents. According to the requirements of ICH Q3C Impurities: Guideline for residual solvents, a method for quantitative determination of the residual content of 1,2,4-trichlorobenzene in the final product by gas chromatography was developed and validated. The absence of synthesis solvents at the limit of detection is shown
Supporting Agency
- JSC Farmak
References
- Cue, B. W., Zhang, J. (2009). Green process chemistry in the pharmaceutical industry. Green Chemistry Letters and Reviews, 2 (4), 193–211. https://doi.org/10.1080/17518250903258150
- Sheldon, R. A. (2017). Metrics of Green Chemistry and Sustainability: Past, Present, and Future. ACS Sustainable Chemistry & Engineering, 6 (1), 32–48. https://doi.org/10.1021/acssuschemeng.7b03505
- Welton, T. (2015). Solvents and sustainable chemistry. Proceedings of the Royal Society A: Mathematical, Physical and Engineering Sciences, 471 (2183), 20150502. https://doi.org/10.1098/rspa.2015.0502
- Constable, D. J. C., Jimenez-Gonzalez, C., Henderson, R. K. (2006). Perspective on Solvent Use in the Pharmaceutical Industry. Organic Process Research & Development, 11 (1), 133–137. https://doi.org/10.1021/op060170h
- Dunn Peter, J., Wells Andrew, S., Williams Michael, T. (2010). Future Trends for Green Chemistry in the Pharmaceutical Industry. Green Chemistry in the Pharmaceutical Industry. Wiley Online Books. https://doi.org/10.1002/9783527629688.ch16
- Cseri, L., Razali, M., Pogany, P., Szekely, G. (2018). Organic solvents in sustainable synthesis and engineering. Green Chemistry. Elsevier, 513–553. https://doi.org/10.1016/b978-0-12-809270-5.00020-0
- Aboagye, E. A., Chea, J. D., Yenkie, K. M. (2021). Systems level roadmap for solvent recovery and reuse in industries. IScience, 24 (10), 103114. https://doi.org/10.1016/j.isci.2021.103114
- Muralikrishna, I. V., Manickam, V. (2017). Hazardous waste management. Environmental Management. Elsevier, 463–494. https://doi.org/10.1016/b978-0-12-811989-1.00017-8
- Chea, J. D., Lehr, A. L., Stengel, J. P., Savelski, M. J., Slater, C. S., Yenkie, K. M. (2020). Evaluation of Solvent Recovery Options for Economic Feasibility through a Superstructure-Based Optimization Framework. Industrial & Engineering Chemistry Research, 59 (13), 5931–5944. https://doi.org/10.1021/acs.iecr.9b06725
- Raymond, M. J., Slater, C. S., Savelski, M. J. (2010). LCA approach to the analysis of solvent waste issues in the pharmaceutical industry. Green Chemistry, 12 (10), 1826. https://doi.org/10.1039/c003666h
- Shores, B. T., Sieg, P. E., Nicosia, A. T., Hu, C., Born, S. C., Shvedova, K. et al. (2020). Design of a Continuous Solvent Recovery System for End-to-End Integrated Continuous Manufacturing of Pharmaceuticals. Organic Process Research & Development, 24 (10), 1996–2003. https://doi.org/10.1021/acs.oprd.0c00092
- Yadav, G., Fabiano, L. A., Soh, L., Zimmerman, J., Sen, R., Seider, W. D. (2020). CO2 process intensification of algae oil extraction to biodiesel. AIChE Journal, 67 (1). https://doi.org/10.1002/aic.16992
- Alder, C. M., Hayler, J. D., Henderson, R. K., Redman, A. M., Shukla, L., Shuster, L. E., Sneddon, H. F. (2016). Updating and further expanding GSK’s solvent sustainability guide. Green Chemistry, 18 (13), 3879–3890. https://doi.org/10.1039/c6gc00611f
- Byrne, F. P., Jin, S., Paggiola, G., Petchey, T. H. M., Clark, J. H., Farmer, T. J. et al. (2016). Tools and techniques for solvent selection: green solvent selection guides. Sustainable Chemical Processes, 4 (1). https://doi.org/10.1186/s40508-016-0051-z
- Henderson, R. K., Jiménez-González, C., Constable, D. J. C., Alston, S. R., Inglis, G. G. A., Fisher, G. et al. (2011). Expanding GSK’s solvent selection guide – embedding sustainability into solvent selection starting at medicinal chemistry. Green Chemistry, 13 (4), 854. https://doi.org/10.1039/c0gc00918k
- Diorazio, L. J., Hose, D. R. J., Adlington, N. K. (2016). Toward a More Holistic Framework for Solvent Selection. Organic Process Research & Development, 20 (4), 760–773. https://doi.org/10.1021/acs.oprd.6b00015
- Chea, J. D., Lehr, A. L., Stengel, J. P., Savelski, M. J., Slater, C. S., Yenkie, K. M. (2020). Evaluation of Solvent Recovery Options for Economic Feasibility through a Superstructure-Based Optimization Framework. Industrial & Engineering Chemistry Research, 59 (13), 5931–5944. https://doi.org/10.1021/acs.iecr.9b06725
- Ooi, J., Ng, D. K. S., Chemmangattuvalappil, N. G. (2019). A Systematic Molecular Design Framework with the Consideration of Competing Solvent Recovery Processes. Industrial & Engineering Chemistry Research, 58 (29), 13210–13226. https://doi.org/10.1021/acs.iecr.9b01894
- Toxicological Profile for Trichlorobenzenes. Agency for Toxic Substances and Disease Registry (ATSDR). Atlanta: U.S. Department of Health and Human Services, Public Health Service. Available at: https://wwwn.cdc.gov/TSP/ToxProfiles/ToxProfiles.aspx?id=1168&tid=255
- HSDB. 2010. 1,2,3-Trichlorobenzene, 1,2,4-trichlorobenzene, and 1,3,5-trichlorobenzene. Hazardous Substances Data Bank. National Library of Medicine
- Rossberg, M., Lendle, W., Pfleiderer, G., Tögel, A., Dreher, E.-L., Langer, E. et al. (2006). Chlorinated Hydrocarbons. Ullmann’s Encyclopedia of Industrial Chemistry. https://doi.org/10.1002/14356007.a06_233.pub2
- European Union risk assessment report. 1,2,4-Trichlorobenzene (2003). European Communities.
- TRI12 2013. TRI explorer: Providing access to EPA’s toxics release inventory data. Washington: Office of Information Analysis and Access. Office of Environmental Information. U.S. Environmental Protection Agency. Toxics Release Inventory
- Title 42-The public health and welfare. Chapter 85-Air pollution prevention and control. Sec. 7412. Hazardous air pollutants (2006). U.S. Environmental Protection Agency. United States Code 42 USC 7412. EPA.
- European Pharmacopoeia, 11th ed. (2023). Strasbourg: Council of Europe.
- ICH Q3C Guideline, Impurities: Residual solvents. Available at: https://www.ema.europa.eu/en/ich-q3c-r8-residual-solvents-scientific-guideline
- Groom, C. R., Bruno, I. J., Lightfoot, M. P., Ward, S. C. (2016). The Cambridge Structural Database. Acta Crystallographica Section B Structural Science, Crystal Engineering and Materials, 72 (2), 171–179. https://doi.org/10.1107/s2052520616003954
- Pat. JPH06345737A. Production of naphazoline or its salt (1994). Published: 20.12.1994. Available at: https://patents.google.com/patent/JPH06345737A/en
- Pat. CN112209880 A. Preparation method of naphazoline hydrochloride (2021). Published: 12.01.2021.
- Pat. CN115636790 A. Preparation of naphazoline hydrochloride (2023). Published: 24.01.2023.
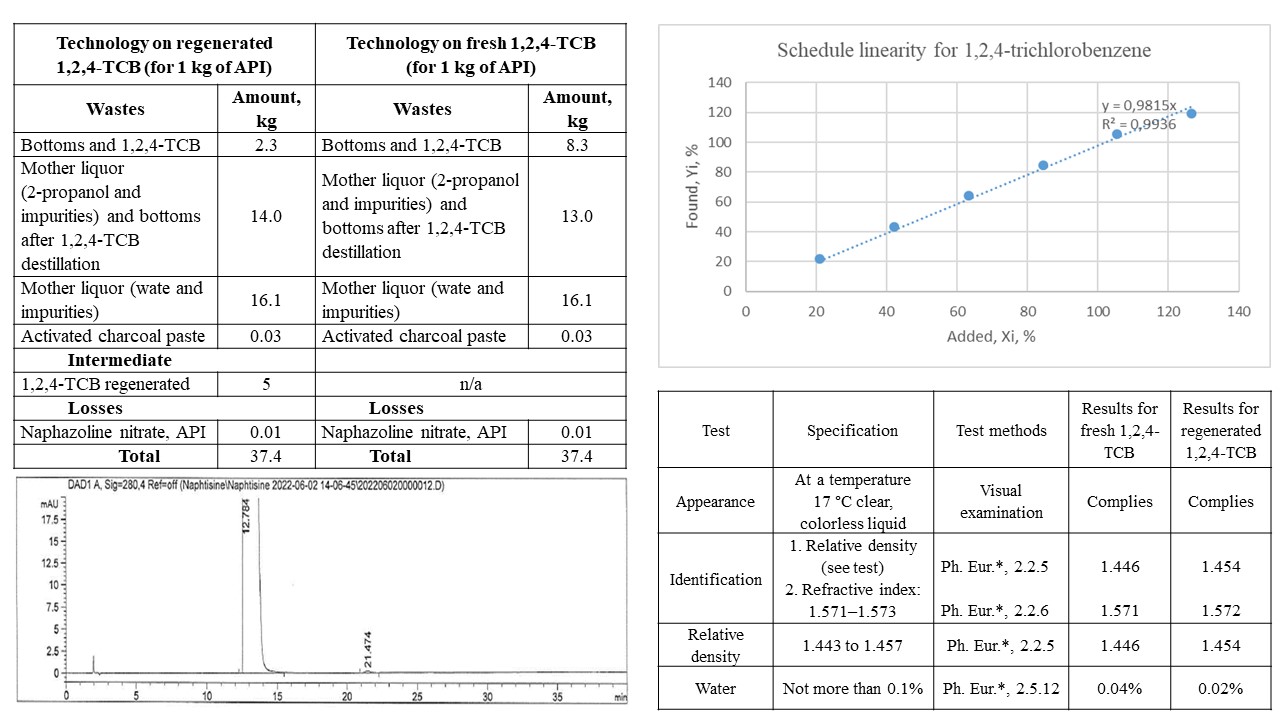
Downloads
Published
How to Cite
Issue
Section
License
Copyright (c) 2024 Tetiana Solominchuk, Vitalii Rudiuk, Lyudmila Sidorenko, Nataliia Kobzar, Maryna Rakhimova, Olha Vislous, Victoriya Georgiyants

This work is licensed under a Creative Commons Attribution 4.0 International License.
Our journal abides by the Creative Commons CC BY copyright rights and permissions for open access journals.