Improvement of cleaning parameters of pipeline elements based on simulation of movement of solid magnetite particles in electrically conductive liquid
DOI:
https://doi.org/10.15587/1729-4061.2023.274699Keywords:
conductive liquid, magnetic field, purification of liquids, numerical calculation, local resistancesAbstract
The unique properties of liquids that can interact with electric and magnetic fields are used in mechanical engineering, technology and medicine. The possibility of the influence of the magnetic field on the solid particles of the liquid in the pipeline allows cleaning of the solid walls of the pipeline, which is the object of the study. Magnetic liquids are solutions of ferromagnets in a liquid, and their physical properties in a magnetic field cause structural transformations in such liquids.
The treatment of electrically conductive liquids in a magnetic field and their use for cleaning water from oil or oil residues are considered. On the basis of numerical modeling, the movement of solid particles of magnetite, which is part of an electrically conductive liquid, was investigated by jointly solving the equations of Reynolds, Maxwell, non-discontinuity and the turbulence model. The physical phenomena of the movement of solid particles of magnetite-based conductive liquid in various elements of the pipeline were determined, which improved the parameters of cleaning liquids contaminated with oil and oil. The magnetic particles of the electrically conductive liquid quite nicely fill the boundaries of the intersection if there is a flow reversal, as it happens in radiators. An increase in the intensity of the magnetic field leads to a change in the velocity profile of the conductive liquid, which prevents magnetite particles from penetrating close to the wall. An increase in the power of the magnetic field makes it possible to detach the contamination from the walls of the pipeline together with the solid particle of magnetite. A 73 % increase in wear in certain sections of the pipeline is due to the effect of the centrifugal force acting on the particle during rotation.
The sudden expansion of the flow makes it difficult for particles to reach the pipe surfaces, which worsens the cleaning conditions. The number of particles on the surface is 82 % less compared to the absence of sudden expansion
References
- Frank, M., Barleon, L., Müller, U. (2001). Visual analysis of two-dimensional magnetohydrodynamics. Physics of Fluids, 13 (8), 2287–2295. doi: https://doi.org/10.1063/1.1383785
- Kim, S. (2021). Hydrodynamics of Anisotropic Liquid Crystals in an Applied Magnetic Field. SIAM Journal on Mathematical Analysis, 53 (3), 3123–3157. doi: https://doi.org/10.1137/19m1310062
- Khan, M. A., Kosel, J. (2021). Integrated Magnetohydrodynamic Pump with Magnetic Composite Substrate and Laser-Induced Graphene Electrodes. Polymers, 13 (7), 1113. doi: https://doi.org/10.3390/polym13071113
- West, D., Taylor, J. A., Krupenkin, T. (2020). Alternating current liquid metal vortex magnetohydrodynamic generator. Energy Conversion and Management, 223, 113223. doi: https://doi.org/10.1016/j.enconman.2020.113223
- Lu, P., Fang, R., Ye, Q., Huang, H. (2020). Numerical Research on the Flow Fields in the Power Generation Channel of a Liquid Metal Magnetohydrodynamic System. ACS Omega, 5 (48), 31164–31170. doi: https://doi.org/10.1021/acsomega.0c04379
- Ko, S., Kim, E. S., Park, S., Daigle, H., Milner, T. E., Huh, C. et al. (2017). RETRACTED ARTICLE: Amine functionalized magnetic nanoparticles for removal of oil droplets from produced water and accelerated magnetic separation. Journal of Nanoparticle Research, 19 (4). doi: https://doi.org/10.1007/s11051-017-3826-6
- Ko, S., Kim, E. S., Park, S., Daigle, H., Milner, T. E., Huh, C. et al. (2016). Oil Droplet Removal from Produced Water Using Nanoparticles and Their Magnetic Separation. SPE Annual Technical Conference and Exhibition. doi: https://doi.org/10.2118/181893-ms
- Hartmann, J., Lazarus, F. (1937). Hg-dynamics II. Experimental investigations on the flow of mercury in a homogeneous magnetic field. København. Available at: http://gymarkiv.sdu.dk/MFM/kdvs/mfm%2010-19/mfm-15-7.pdf
- Alfvén, H. (1958). Magnetohydrodynamics and the thermonuclear problem. Proceedings of the Second Nations International Conference. Available at: http://www-naweb.iaea.org/napc/physics/2ndgenconf/data/Proceedings%201958/papers%20Vol31/Paper01_Vol31.pdf
- Davidson, P. A. (1999). Magnetohydrodynamics in materials processing. Annual Review of Fluid Mechanics, 31 (1), 273–300. doi: https://doi.org/10.1146/annurev.fluid.31.1.273
- Narasimha, R., Sreenivasan, K. R. (1979). Relaminarization of Fluid Flows. Advances in Applied Mechanics, 221–309. doi: https://doi.org/10.1016/s0065-2156(08)70311-9
- Rogovyi, A., Neskorozhenyi, A., Krasnikov, S., Tynyanova, I., Khovanskyi, S. (2022). Improvement of Vortex Chamber Supercharger Performances Using Slotted Rectangular Channel. Advanced Manufacturing Processes IV, 552–561. doi: https://doi.org/10.1007/978-3-031-16651-8_52
- Azimi, N., Rahimi, M., Zangenehmehr, P. (2021). Numerical Study of Mixing and Mass Transfer in a Micromixer by Stimulation of Magnetic Nanoparticles in a Magnetic Field. Chemical Engineering & Technology, 44 (6), 1084–1093. doi: https://doi.org/10.1002/ceat.202000030
- Andrenko, P., Rogovyi, A., Hrechka, I., Khovanskyi, S., Svynarenko, M. (2021). The Influence of the Gas Content in the Working Fluid on Parameters of the the Hydraulic Motor’s Axial Piston. Advances in Design, Simulation and Manufacturing IV, 97–106. doi: https://doi.org/10.1007/978-3-030-77823-1_10
- Chernetskaya-Beletskaya, N., Rogovyi, A., Shvornikova, A., Baranov, I., Miroshnikova, M., Bragin, N. (2018). Study on the Coal-Water Fuel Pipeline Transportation Taking Into Account the Granulometric Composition Parameters. International Journal of Engineering & Technology, 7 (4.3), 240. doi: https://doi.org/10.14419/ijet.v7i4.3.19794
- Widlund, O. (2000). Implementation of MHD model equations in CFX 4.3. Stockholm. Available at: http://ola.widlund.free.fr/doc/TRITA_CFX.pdf
- Chernetskaya-Beletskaya, N., Rogovyi, A., Miroshnykova, M., Shtykov, A. (2021). Verification of electrically conductive fluid flow calculation in circular pipes. Collected Scientific Works of Ukrainian State University of Railway Transport, 196, 87–98. doi: https://doi.org/10.18664/1994-7852.196.2021.242076
- Ahangar Zonouzi, S., Khodabandeh, R., Safarzadeh, H., Aminfar, H., Trushkina, Y., Mohammadpourfard, M. et al. (2018). Experimental investigation of the flow and heat transfer of magnetic nanofluid in a vertical tube in the presence of magnetic quadrupole field. Experimental Thermal and Fluid Science, 91, 155–165. doi: https://doi.org/10.1016/j.expthermflusci.2017.10.013
- Andrenko, P., Rogovyi, A., Hrechka, I., Khovanskyi, S., Svynarenko, M. (2021). Characteristics improvement of labyrinth screw pump using design modification in screw. Journal of Physics: Conference Series, 1741 (1), 012024. doi: https://doi.org/10.1088/1742-6596/1741/1/012024
- Pianykh, A. A., Arkhipov, G. V., Tretyakov, Ya. A. (2020). Mathematical Model of Magnetic Hydrodynamics and Heat Transfer in an Aluminum Reduction Cell. Russian Journal of Non-Ferrous Metals, 61 (1), 65–73. doi: https://doi.org/10.3103/s1067821220010125
- Rogovyi, A., Korohodskyi, V., Khovanskyi, S., Hrechka, I., Medvediev, Y. (2021). Optimal design of vortex chamber pump. Journal of Physics: Conference Series, 1741 (1), 012018. doi: https://doi.org/10.1088/1742-6596/1741/1/012018
- Luo, Y., Fan, X., Kim, C. N. (2021). MHD flows in a U-channel under the influence of the spatially different channel-wall electric conductivity and of the magnetic field orientation. Journal of Mechanical Science and Technology, 35 (10), 4477–4487. doi: https://doi.org/10.1007/s12206-021-0918-0
- Sommerfeld, M., Sgrott, O. L., Taborda, M. A., Koullapis, P., Bauer, K., Kassinos, S. (2021). Analysis of flow field and turbulence predictions in a lung model applying RANS and implications for particle deposition. European Journal of Pharmaceutical Sciences, 166, 105959. doi: https://doi.org/10.1016/j.ejps.2021.105959
- Ansys CFX. Available at: https://www.ansys.com/products/fluids/ansys-cfx
- Rogovyi, A., Korohodskyi, V., Neskorozhenyi, A., Hrechka, I., Khovanskyi, S. (2022). Reduction of Granular Material Losses in a Vortex Chamber Supercharger Drainage Channel. Advances in Design, Simulation and Manufacturing V, 218–226. doi: https://doi.org/10.1007/978-3-031-06044-1_21
- Appadurai, A., Raghavan, V. (2019). Numerical investigations on particle separation in dynamic separators. International Journal of Numerical Methods for Heat & Fluid Flow, 30 (4), 1677–1688. doi: https://doi.org/10.1108/hff-10-2018-0567
- Su, W., Shi, X., Wu, Y., Gao, J., Lan, X. (2020). Simulation on the effect of particle on flow hydrodynamics in a slurry bed. Powder Technology, 361, 1006–1020. doi: https://doi.org/10.1016/j.powtec.2019.10.096
- Hutchings, I. M. (1979). Mechanical and metallurgical aspects of the erosion of metals. Proceedings of the International Conference on Corrosion-Erosion of Coal Conversion System Materials. National Association of Corrosion Engineers, 393–428.
- Dosanjh, S., Humphrey, J. A. C. (1985). The influence of turbulence on erosion by a particle-laden fluid jet. Wear, 102 (4), 309–330. doi: https://doi.org/10.1016/0043-1648(85)90175-9
- Rogovyi, A., Khovanskyy, S., Grechka, I., Pitel, J. (2019). The Wall Erosion in a Vortex Chamber Supercharger Due to Pumping Abrasive Mediums. Advances in Design, Simulation and Manufacturing II, 682–691. doi: https://doi.org/10.1007/978-3-030-22365-6_68
- Voloshina, A., Panchenko, A., Titova, O., Panchenko, I. (2021). Changes in the dynamics of the output characteristics of mechatronic systems with planetary hydraulic motors. Journal of Physics: Conference Series, 1741 (1), 012045. doi: https://doi.org/10.1088/1742-6596/1741/1/012045
- Andrenko, P., Hrechka, I., Khovanskyi, S., Rogovyi, A., Svynarenko, M. (2021). Improving the Technical Level of Hydraulic Machines, Hydraulic Units and Hydraulic Devices using a Definitive Assessment Criterion at the Design Stage. Journal of Mechanical Engineering, 18 (3), 57–76. doi: https://doi.org/10.24191/jmeche.v18i3.15414
- Syomin, D., Rogovyi, A. (2012). Features of a Working Process and Characteristics of Irrotational Centrifugal Pumps. Procedia Engineering, 39, 231–237. doi: https://doi.org/10.1016/j.proeng.2012.07.029
- Sokolov, V., Porkuian, O., Krol, O., Stepanova, O. (2021). Design Calculation of Automatic Rotary Motion Electrohydraulic Drive for Technological Equipment. Advances in Design, Simulation and Manufacturing IV, 133–142. doi: https://doi.org/10.1007/978-3-030-77719-7_14
- Panchenko, A., Voloshina, A., Luzan, P., Panchenko, I., Volkov, S. (2021). Kinematics of motion of rotors of an orbital hydraulic machine. IOP Conference Series: Materials Science and Engineering, 1021 (1), 012045. doi: https://doi.org/10.1088/1757-899x/1021/1/012045
- Takeuchi, J., Satake, S., Morley, N. B., Kunugi, T., Yokomine, T., Abdou, M. A. (2008). Experimental study of MHD effects on turbulent flow of Flibe simulant fluid in circular pipe. Fusion Engineering and Design, 83 (7-9), 1082–1086. doi: https://doi.org/10.1016/j.fusengdes.2008.08.050
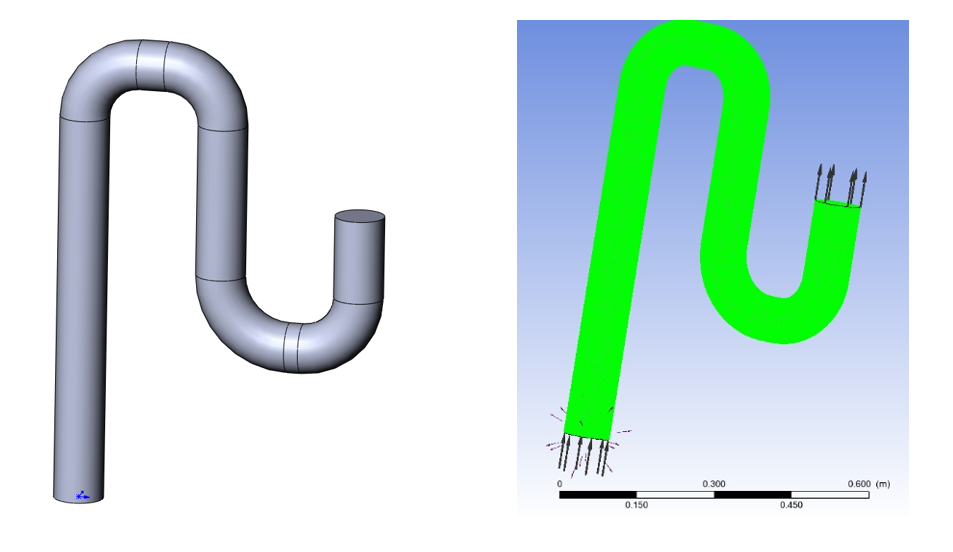
Downloads
Published
How to Cite
Issue
Section
License
Copyright (c) 2023 Andrii Rogovyi, Nataliia Chernetska-Biletska, Mariia Miroshnykova, Ihor Baranov, Yevhen Polupan

This work is licensed under a Creative Commons Attribution 4.0 International License.
The consolidation and conditions for the transfer of copyright (identification of authorship) is carried out in the License Agreement. In particular, the authors reserve the right to the authorship of their manuscript and transfer the first publication of this work to the journal under the terms of the Creative Commons CC BY license. At the same time, they have the right to conclude on their own additional agreements concerning the non-exclusive distribution of the work in the form in which it was published by this journal, but provided that the link to the first publication of the article in this journal is preserved.
A license agreement is a document in which the author warrants that he/she owns all copyright for the work (manuscript, article, etc.).
The authors, signing the License Agreement with TECHNOLOGY CENTER PC, have all rights to the further use of their work, provided that they link to our edition in which the work was published.
According to the terms of the License Agreement, the Publisher TECHNOLOGY CENTER PC does not take away your copyrights and receives permission from the authors to use and dissemination of the publication through the world's scientific resources (own electronic resources, scientometric databases, repositories, libraries, etc.).
In the absence of a signed License Agreement or in the absence of this agreement of identifiers allowing to identify the identity of the author, the editors have no right to work with the manuscript.
It is important to remember that there is another type of agreement between authors and publishers – when copyright is transferred from the authors to the publisher. In this case, the authors lose ownership of their work and may not use it in any way.