Determining the structure and properties of heat-resistant titanium alloys VT3-1 and VT9 obtained by electron-beam melting
DOI:
https://doi.org/10.15587/1729-4061.2022.265014Keywords:
electron beam melting, intermediate capacity, heat-resistant titanium alloy, structure, mechanical propertiesAbstract
This paper reports a comprehensive study that investigated the quality of heat-resistant titanium alloys VT3-1 and VT9 obtained by the method of electron beam melting (EBM). It is shown that EBM makes it possible to produce high-quality metal of ingots of heat-resistant titanium alloys VT9 and VT3-1.
Semi-finished articles were made in the form of bars from ingots obtained by the EBM method. It was established that in the macrostructure of the deformed metal there are no cracks, delamination, cavities, metal and non-metallic inclusions. The macrostructure of the metal of the bars corresponds to 4 points for the alloy VT3-1 and 4–5 points for the alloy VT9 on the 10-point scale of microstructures of instruction 1054-76. It was shown that the metal microstructure of forged bars of VT9 alloy consists of primary β grains with a continuous or intermittent α-rim along the grain boundaries 3–4 μs thick. The structure of the metal in the volume of grain – lamellar type with partially globularized plates of the α phase, plates of α-phase of close orientation form α colonies measuring 10–40 μs. The thickness of the α plates is 1–5 μs, between the plates or globules of the α phase there is a layer of β phase with a thickness of 1–2 μs. The microstructure of the deformed metal of titanium alloy VT3-1 consists of primary β grains, the volume of which contains colonies of lamellar α phases measuring 10–100 μs. The thickness of α plates is 1.5–3 μs, the layer of β phase in the intervals between α-plates is mainly 0.3–0.5 μs. The microstructure of semi-finished articles in the form of deformed bars of alloys VT9 and VT3-1 corresponds to type 4–6 according to the 9-type scale of the microstructure of instruction 1054-76. Studies of the mechanical properties of the obtained semi-finished articles have shown that they meet all the requirements of regulatory standards that are put forward by industry to the quality of the metal of heat-resistant titanium alloys
References
- Narushima, T., Sugizaki, Y. (2020). Recent activities of titanium research and development in Japan. MATEC Web of Conferences, 321, 01004. doi: https://doi.org/10.1051/matecconf/202032101004
- Williams, J. C., Boyer, R. R. (2020). Opportunities and Issues in the Application of Titanium Alloys for Aerospace Components. Metals, 10 (6), 705. doi: https://doi.org/10.3390/met10060705
- Mizukami, H., Kitaura, T., Shirai, Y. (2020). Dissolution Behavior of a Titanium Nitride Sponge in Titanium Alloy Melt. MATEC Web of Conferences, 321, 10005. doi: https://doi.org/10.1051/matecconf/202032110005
- Babenko, E. P., Dolzhenkova, E. V. (2014). Issledovanie prichin razrusheniya krupnogabaritnogo izdeliya iz splava VT23. Metallurgicheskaya i gornorudnaya promyshlennost', 3, 82–85. Available at: http://nbuv.gov.ua/UJRN/MGRP_2014_3_27
- Paton, B. E., Trigub, N. P., Zhuk, G. V. (2008). Crystallization of titanium ingots in the course of electron-beam melting. Materials Science, 44 (3), 328–335. doi: https://doi.org/10.1007/s11003-008-9090-2
- Mantione, J., Garcia-Avila, M., Arnold, M., Bryan, D., Foltz, J. (2020). Properties of Novel High Temperature Titanium Alloys for Aerospace Applications. MATEC Web of Conferences, 321, 04006. doi: https://doi.org/10.1051/matecconf/202032104006
- Khorev, A. I. (2014). Fundamental'nye i prikladnye raboty po konstruktsionnym titanovym splavam i perspektivnye napravleniya ikh razvitiya. Tekhnologiya mashinostroeniya, 11, 5–10.
- Lei, X., Dong, L., Zhang, Z., Liu, Y., Hao, Y., Yang, R., Zhang, L.-C. (2017). Microstructure, Texture Evolution and Mechanical Properties of VT3-1 Titanium Alloy Processed by Multi-Pass Drawing and Subsequent Isothermal Annealing. Metals, 7 (4), 131. doi: https://doi.org/10.3390/met7040131
- Pavlova, T. V., Kashapov, O. S., Nochovnaya, N. A. (2012). Titanovye splavy dlya gazoturbinnykh dvigateley. Vse materialy. Entsiklopedicheskiy spravochnik, 5, 8–14.
- Il'in, A. A., Kolachev, B. A., Pol'kin, I. S. (2009). Titanovye splavy. Sostav, struktura, svoystva. Moscow: VILS-MATI, 520.
- Simonov, Y. V., Ushakov, I. V. (2020). Mechanical properties of surface structures of titanium alloy VT9 after repeated local processing with nanosecond laser pulses. Bulletin of the Moscow State Regional University (Physics and Mathematics), 2, 19–35. doi: https://doi.org/10.18384/2310-7251-2020-2-19-35
- Singh, B. K., Singh, P. N., Singh, V., Ramachandra, C. (1999). Stabilisation Treatment of Titanium Alloy VT9. Defence Science Journal, 49 (2), 169–176. doi: https://doi.org/10.14429/dsj.49.3826
- Akhonin, S. V., Severin, A. Yu., Beresos, V. O., Pikulin, O. M., Erokhin, O. G. (2022). Mathematical modeling of evaporation processes at ebm of alloys based. Sovremennaâ Èlektrometallurgiâ, 2, 10–16. doi: https://doi.org/10.37434/sem2022.02.02
- Akhonin, S. V., Pikulin, O. M. (2019). Investigation of Effect of Electron Beam Surface Treatment of Titanium Alloy Ingots on Structure and Properties of Melted Metal. IOP Conference Series: Materials Science and Engineering, 582 (1), 012047. doi: https://doi.org/10.1088/1757-899x/582/1/012047
- Akhonin, S. V., Pikulin, A. N., Klochai, V. V., Ryabtsev, A. D. (2019). Electron-Beam Surface Treatment of Titanium Alloy Ingots. Part 1. Metallurgist, 63 (1-2), 183–191. doi: https://doi.org/10.1007/s11015-019-00808-9
- Paton, B. E., Akhonin, S. V., Prilutsky, V. P. (2012). Development of welding technologies in titanium component manufacturing. Ti 2011 - Proceedings of the 12th World Conference on Titanium, 2, 1585–1591.
- Borisova, E. A., Bochvar, G. A., Brun, M. Ya. et. al. (1980). Titanovye splavy. Metallografiya titanovykh splavov. Moscow: «Metalurgiya», 464.
- Boer, R. R. (1985). Titanium and Titanium Alloys. Metallography and Microstructures. ASM, Metals Park, OH, 458–475.
- Shved, F. I. (2009). Slitok vakuumnogo dugovogo pereplava. Chelyabinsk: OOO «Izadetl'stvo Tat'yany Lur'e», 428.
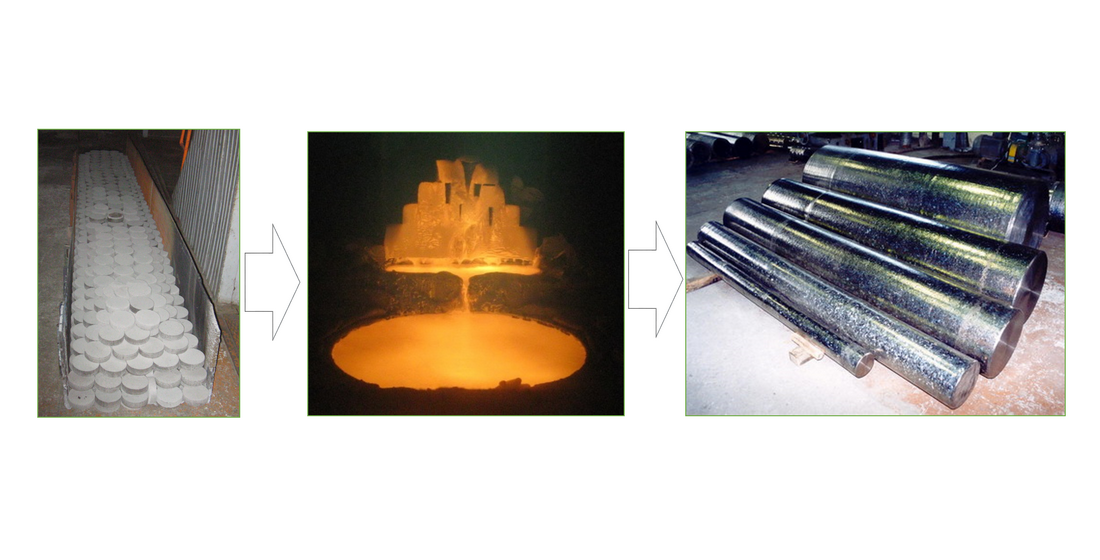
Downloads
Published
How to Cite
Issue
Section
License
Copyright (c) 2022 Serhii Akhonin, Oleksandr Pikulin, Volodymyr Berezos, Andrii Severyn, Oleksiy Erokhin, Vitalii Kryzhanovskyi

This work is licensed under a Creative Commons Attribution 4.0 International License.
The consolidation and conditions for the transfer of copyright (identification of authorship) is carried out in the License Agreement. In particular, the authors reserve the right to the authorship of their manuscript and transfer the first publication of this work to the journal under the terms of the Creative Commons CC BY license. At the same time, they have the right to conclude on their own additional agreements concerning the non-exclusive distribution of the work in the form in which it was published by this journal, but provided that the link to the first publication of the article in this journal is preserved.
A license agreement is a document in which the author warrants that he/she owns all copyright for the work (manuscript, article, etc.).
The authors, signing the License Agreement with TECHNOLOGY CENTER PC, have all rights to the further use of their work, provided that they link to our edition in which the work was published.
According to the terms of the License Agreement, the Publisher TECHNOLOGY CENTER PC does not take away your copyrights and receives permission from the authors to use and dissemination of the publication through the world's scientific resources (own electronic resources, scientometric databases, repositories, libraries, etc.).
In the absence of a signed License Agreement or in the absence of this agreement of identifiers allowing to identify the identity of the author, the editors have no right to work with the manuscript.
It is important to remember that there is another type of agreement between authors and publishers – when copyright is transferred from the authors to the publisher. In this case, the authors lose ownership of their work and may not use it in any way.