Using modern concepts in the design of extrusion dies to improve the mechanical extrusion and fatigue properties for AA1100
DOI:
https://doi.org/10.15587/1729-4061.2022.265712Keywords:
extrusion, die design, mechanical properties, reduction percentage, fatigue strength, corrosionAbstract
In this research work a direct extrusion unit has been designed and manufactured for circular section using the theoretical die design concepts for designing of the die profile, as constancy of the ratio of successive generalized homogeneous strain increment (CRHS). This was carried out by studying the final mechanical properties of the direct extruded products through dies with theoretical concept (ACRHS) and (UCRHS). Commercial alloy AA1100 round section billets was subjected to uniform extruded compressive load using two types of extrusion dies i.e. (ACRHS) and (UCRHS) at room temperature. The product of these dies with as received were conducted to testing under tensile and fatigue tests without corrosion and with corrosion of 90 days fully submersed in 0.35 % NaСl solution. The experimental results show that the reduction percentage (RP) in the main mechanical properties, UTS, YS and BHN due to corrosion were 14.28 %, 5.88 % and 12.12 % for as received samples, 2.74 %, 5.08 % and 6.12 % for the ACRHS samples and 7.79 %, 6.86 % and 8.88 % for UCRHS samples respectively. It was concluded that the less reduction percentage was occurred in the ACRHS samples compared to other samples. Corrosion fatigue testing of the above three samples were made and compared to the same samples without corrosion. The testing results revealed that the corrosion is significantly reduce the fatigue strength at 107 cycles from 40 to 33.65 MPa for as received samples, from 49.47 to 46.73 for ACRHS samples and from 49.5 to 45.89 MPa for UCRHS samples. The results may be lead to the best mechanical and fatigue properties under corrosion action are the ACRHS samples. The obtained results show that the extrusion die (ACRHS) is the most efficient die design
Supporting Agency
- The authors express their gratitude to the Bilad Alrafidain university collage, Diyala – Iraq for their encouragement and support during the research studies.
References
- Gbenebor, O. P., Fayomi, O. S. I., Popoola, A. P. I., Inegbenebor, A. O., Oyawale, F. (2013). Extrusion die geometry effects on the energy absorbing properties and deformation response of 6063-type Al–Mg–Si aluminum alloy. Results in Physics, 3, 1–6. doi: https://doi.org/10.1016/j.rinp.2013.01.002
- Mopon, M. L., Garcia, J. S., Manguerra, D. M., Narisma, C. J. C. (2021). Corrosion Behavior of AA 1100 Anodized in Gallic-Sulfuric Acid Solution. Coatings, 11 (4), 405. doi: https://doi.org/10.3390/coatings11040405
- Nanninga, N. E. (2008). High Cycle Fatigue of AA6082 and AA6063 Aluminum Extrusions. Michigan Technological University. doi: https://doi.org/10.37099/mtu.dc.etds/18
- Fomin, O., Lovska, A., Lytvynenko, A., Sova, S. (2022). Determining the features of loading the bearing structure of a multifunctional car under operating modes. Eastern-European Journal of Enterprise Technologies, 3 (7 (117)), 6–13. doi: https://doi.org/10.15587/1729-4061.2022.258201
- Alhamdany, A. A., Khenyab, A. Y., Mohammed, Q. K., Alalkawi, H. J. M. (2021). Development mechanical and fatigue properties of AA7001 after combined SP with deep cryogenic treatment and UIP with deep cryogenic treatment. Eastern-European Journal of Enterprise Technologies, 5 (1 (113)), 62–69. doi: https://doi.org/10.15587/1729-4061.2021.243391
- Logesh, K., Bupesh Raja, V. K., Nath, N. K. (2017). Experimental Investigation on Formability Analysis, Mechanical and Corrosion Behaviour of AA1100 Sheet Metal. International Journal of Mechanical Engineering and Technology (IJMET), 8 (8), 900–909.
- Laurino, A., Andrieu, E., Harouard, J.-P., Odemer, G., Salabura, J.-C., Blanc, C. (2014). Effect of corrosion on the fatigue life and fracture mechanisms of 6101 aluminum alloy wires for car manufacturing applications. Materials & Design, 53, 236–249. doi: https://doi.org/10.1016/j.matdes.2013.06.079
- Bucci, R. J. (1996). Selecting aluminum alloys to resist failure by Fracture mechanisms. ASM Handbook Committee, 771–812. Available at: https://materialsdata.nist.gov/bitstream/handle/11115/169/Selecting%20%20Al%20Alloys%20%20for%20Resistance%20to%20Fracture.pdf?sequence=3&isAllowed=y
- Ghadban, T. Y. (2020). Design and fabrication of a computerized elevated temperature tensile test rig. University Of Technology, Iraq.
- Ali, S. M. (2002). The effect of geometry of the extrusion die on the fatigue strength for aluminum. University of Technology, Iraq.
- Roberge P. R. (1999). Handbook of corrosion engineering. McGraw Hill. Available at: https://dl.icdst.org/pdfs/files/441d337b7410198db6d96e61a6716302.pdf
- Genel, K. (2007). The effect of pitting on the bending fatigue performance of high-strength aluminum alloy. Scripta Materialia, 57 (4), 297–300. doi: https://doi.org/10.1016/j.scriptamat.2007.04.045
- Betti, Z. A. (2014). Corrosion-fatigue behaviour of 1100 - H12 Al alloy under different shot peening times. Al-Mustansirya University.
- Li, X.-D., Wang, X.-S., Ren, H.-H., Chen, Y.-L., Mu, Z.-T. (2012). Effect of prior corrosion state on the fatigue small cracking behaviour of 6151-T6 aluminum alloy. Corrosion Science, 55, 26–33. doi: https://doi.org/10.1016/j.corsci.2011.09.025
- Pandey, V., Chattopadhyay, K., Santhi Srinivas, N. C., Singh, V. (2016). Low Cycle Fatigue behavior of AA7075 with surface gradient structure produced by Ultrasonic Shot Peening. Procedia Structural Integrity, 2, 3288–3295. doi: https://doi.org/10.1016/j.prostr.2016.06.410
- Vijay Kumar, A., Ratnam, C. H., Kesava Rao, V. V. S., Rohini Kumar, Ch. (2019). Study on influence of Die Angle in Cold Extrusion on Properties of Nano Sic Reinforced 6061 Aluminum Alloy. Materials Today: Proceedings, 18, 4366–4373. doi: https://doi.org/10.1016/j.matpr.2019.07.400
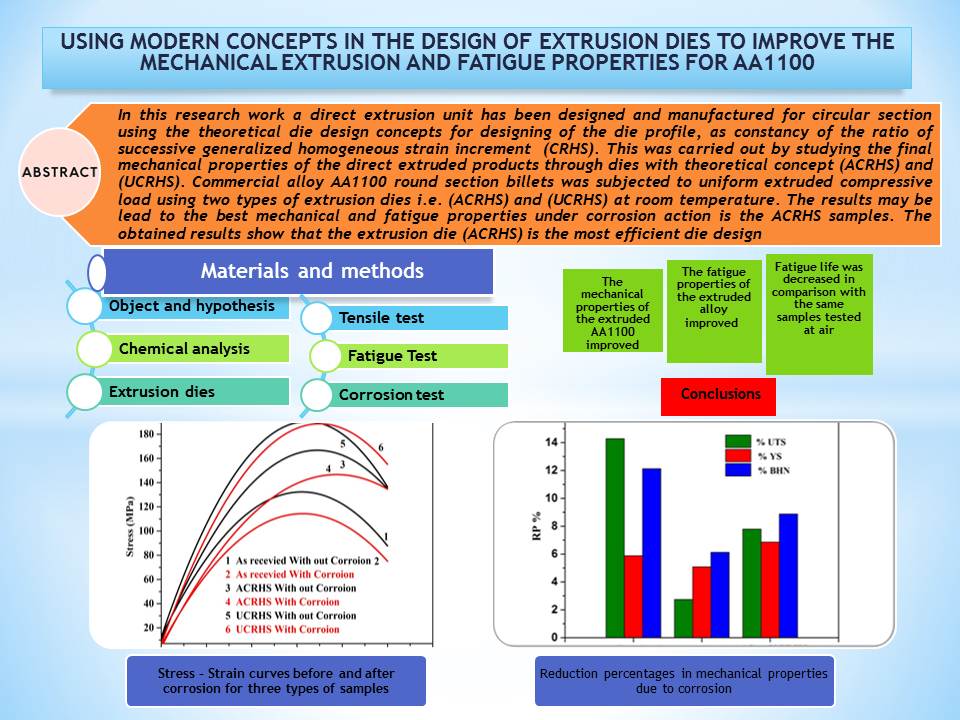
Downloads
Published
How to Cite
Issue
Section
License
Copyright (c) 2022 Abdulwahab M. Al-Mushehdany, Mazin Mahmood Yahya, Batool Kadhim Hmood, Hussain Jasim M. Alalkawi

This work is licensed under a Creative Commons Attribution 4.0 International License.
The consolidation and conditions for the transfer of copyright (identification of authorship) is carried out in the License Agreement. In particular, the authors reserve the right to the authorship of their manuscript and transfer the first publication of this work to the journal under the terms of the Creative Commons CC BY license. At the same time, they have the right to conclude on their own additional agreements concerning the non-exclusive distribution of the work in the form in which it was published by this journal, but provided that the link to the first publication of the article in this journal is preserved.
A license agreement is a document in which the author warrants that he/she owns all copyright for the work (manuscript, article, etc.).
The authors, signing the License Agreement with TECHNOLOGY CENTER PC, have all rights to the further use of their work, provided that they link to our edition in which the work was published.
According to the terms of the License Agreement, the Publisher TECHNOLOGY CENTER PC does not take away your copyrights and receives permission from the authors to use and dissemination of the publication through the world's scientific resources (own electronic resources, scientometric databases, repositories, libraries, etc.).
In the absence of a signed License Agreement or in the absence of this agreement of identifiers allowing to identify the identity of the author, the editors have no right to work with the manuscript.
It is important to remember that there is another type of agreement between authors and publishers – when copyright is transferred from the authors to the publisher. In this case, the authors lose ownership of their work and may not use it in any way.