Identifying the influence of dimensional parameters on the stresses and deformations of two helical gears
DOI:
https://doi.org/10.15587/1729-4061.2022.266261Keywords:
Finite element method, helical gear, pressure angle, helix angle, stress analysisAbstract
In this research paper, focusing on the basic variables of the gear modeling process and setting its dimensions to see which gears are capable of withstanding transmission operations and its rigidity was done. Because one of the most prominent transmission mechanics is gears, as the types of gears are numerous and common, and one of the most prominent types of gears is the helical gear. The helical gear is one of the most widely used and widespread gears in mechanical fields due to the increase in the contact area during the interlock process, as this increase reduces noise during gear rotation. Three main variables were used to establish the results. The first of which is the pressure angle, the helix deflection angle, and the module number, and they made a number of cases to see which one was able to withstand the movement operations with a proven torque. The results proved that the distortion value in the first case at module 1 was 87×10-6 m, while in module 2 the distortion value was 3.75×10-6. The data are useful and important because the values of the stresses that affect the gears must be known by changing the module due to it gives a stronger concept of the extent to which the gears can withstand movement. Pressure angle is one of the basic variables that change the dimensions of wind turbine gears. The value of the greatest stress was 2.13×108 Pa, but at the pressure angle of 20 degrees, the stress value was 1.93×108 Pa. It affects the diameter, stiffness and tensile strength of a wind turbine. The study of this research paper depends on helical gears. It is known that the angles of the helical teeth increase the large contact area between two gears. From the resulting deformation values, it is noted that the deformation value is 4.26×10-6 m when the helix angle is 20 degrees.
References
- Chen, Z., Zeng, M., Fuentes-Aznar, A. (2020). Computerized design, simulation of meshing and stress analysis of pure rolling cylindrical helical gear drives with variable helix angle. Mechanism and Machine Theory, 153, 103962. doi: https://doi.org/10.1016/j.mechmachtheory.2020.103962
- Mohanraj, R., Elangovan, S., Arun Prakash, R., Sanjeev, S., Swetha, R., Agalya, K. (2020). Stress Analysis on Single and Herringbone Helical Gears. Materials Today: Proceedings, 22, 2049–2057. doi: https://doi.org/10.1016/j.matpr.2020.03.219
- Rai, P., Agrawal, A., Saini, M. L., Jodder, C., Barman, A. G. (2018). Volume optimization of helical gear with profile shift using real coded genetic algorithm. Procedia Computer Science, 133, 718–724. doi: https://doi.org/10.1016/j.procs.2018.07.127
- Kim, S., Moon, S., Sohn, J., Park, Y., Choi, C., Lee, G. (2020). Macro geometry optimization of a helical gear pair for mass, efficiency, and transmission error. Mechanism and Machine Theory, 144, 103634. doi: https://doi.org/10.1016/j.mechmachtheory.2019.103634
- Syzrantseva, K. V., Syzrantsev, V. N., Kolbasin, D. S. (2019). Comparative estimation of the failure probability of cylindrical arc and helical gears by tooth bending endurance. AIP Conference Proceedings. doi: https://doi.org/10.1063/1.5135122
- Zouridaki, A.-E., Vasileiou, G. (2020). Investigation of the Effect of Geometry Characteristics on Bending Stress of Asymmetric Helical Gears by Using Finite Elements Analysis. Computation, 8 (1), 19. doi: https://doi.org/10.3390/computation8010019
- Abaid Samawi, K., Abd-Alkuder Salman, E., Abd-Alsatar Alshekhly, B., Fawzi Nassar, M., Yousefzadeh Borzehandani, M., Abdulkareem-Alsultan, G. et al. (2022). Rational design of different π-bridges and their theoretical impact on indolo[3,2,1-jk]carbazole based dye-sensitized solar cells. Computational and Theoretical Chemistry, 1212, 113725. doi: https://doi.org/10.1016/j.comptc.2022.113725
- Zhan, J., Fard, M. (2018). Effects of helix angle, mechanical errors, and coefficient of friction on the time-varying tooth-root stress of helical gears. Measurement, 118, 135–146. doi: https://doi.org/10.1016/j.measurement.2018.01.021
- Choi, C., Ahn, H., Park, Y., Lee, G., Kim, S. (2021). Influence of gear tooth addendum and dedendum on the helical gear optimization considering mass, efficiency, and transmission error. Mechanism and Machine Theory, 166, 104476. doi: https://doi.org/10.1016/j.mechmachtheory.2021.104476
- Rai, P., Barman, A. G. (2019). An approach for design optimization of helical gear pair with balanced specific sliding and modified tooth profile. Structural and Multidisciplinary Optimization, 60 (1), 331–341. doi: https://doi.org/10.1007/s00158-019-02198-7
- Patil, P. J., Patil, M. S., Joshi, K. D. (2017). Dynamic State or Whole Field Analysis of Helical Gear. Journal of The Institution of Engineers (India): Series C, 100 (1), 37–42. doi: https://doi.org/10.1007/s40032-017-0389-3
- Holzapfel, G. A., Linka, K., Sherifova, S., Cyron, C. J. (2021). Predictive constitutive modelling of arteries by deep learning. Journal of The Royal Society Interface, 18 (182), 20210411. doi: https://doi.org/10.1098/rsif.2021.0411
- Quang, N. H., Linh, N. H., Huy, T. Q., Lam, P. D., Tuan, N. A., Ngoc, N. D. et al. (2022). Optimizing the partial gear ratios of the two-stage worm gearbox for minimizing total gearbox cost. Eastern-European Journal of Enterprise Technologies, 1 (1 (115)), 6–15. doi: https://doi.org/10.15587/1729-4061.2022.252301
- Petrakov, Y., Korenkov, V., Myhovych, A. (2022). Technology for programming contour milling on a CNC machine. Eastern-European Journal of Enterprise Technologies, 2 (1 (116)), 55–61. doi: https://doi.org/10.15587/1729-4061.2022.255389
- Slavinska, A., Matiukh, S., Mytsa, V., Syrotenko, O., Dombrovska, O. (2022). Devising a method for the interactive arrangement of structural elements of men’s jacket models. Eastern-European Journal of Enterprise Technologies, 1 (1 (115)), 56–66. doi: https://doi.org/10.15587/1729-4061.2022.251065
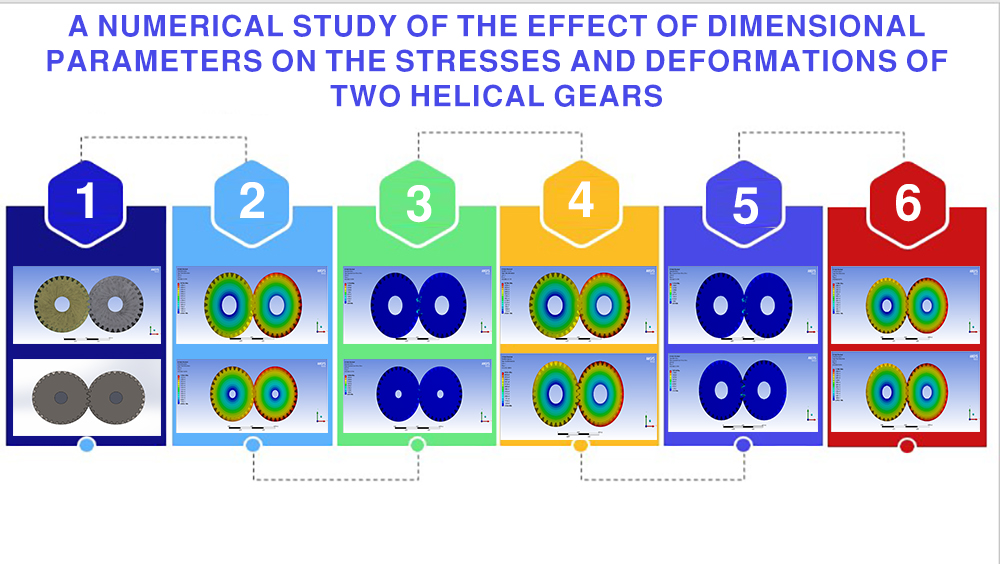
Downloads
Published
How to Cite
Issue
Section
License
Copyright (c) 2022 Bassam Ali Ahmed

This work is licensed under a Creative Commons Attribution 4.0 International License.
The consolidation and conditions for the transfer of copyright (identification of authorship) is carried out in the License Agreement. In particular, the authors reserve the right to the authorship of their manuscript and transfer the first publication of this work to the journal under the terms of the Creative Commons CC BY license. At the same time, they have the right to conclude on their own additional agreements concerning the non-exclusive distribution of the work in the form in which it was published by this journal, but provided that the link to the first publication of the article in this journal is preserved.
A license agreement is a document in which the author warrants that he/she owns all copyright for the work (manuscript, article, etc.).
The authors, signing the License Agreement with TECHNOLOGY CENTER PC, have all rights to the further use of their work, provided that they link to our edition in which the work was published.
According to the terms of the License Agreement, the Publisher TECHNOLOGY CENTER PC does not take away your copyrights and receives permission from the authors to use and dissemination of the publication through the world's scientific resources (own electronic resources, scientometric databases, repositories, libraries, etc.).
In the absence of a signed License Agreement or in the absence of this agreement of identifiers allowing to identify the identity of the author, the editors have no right to work with the manuscript.
It is important to remember that there is another type of agreement between authors and publishers – when copyright is transferred from the authors to the publisher. In this case, the authors lose ownership of their work and may not use it in any way.