Microstructure variation effects influence on characteristics and mechanical properties of Monel 400 and low alloy steel (ASTM 387-Gr.11) GTAW dissimilar joint
DOI:
https://doi.org/10.15587/1729-4061.2022.266264Keywords:
dissimilar weldments, carbon depleted zone, Transition zone, Monel 400, migrated grain boundaryAbstract
Monel 400 with low alloy steel dissimilar joints are widely used in oil industry, petrochemical and nuclear engineering, this kind of applications needs welding joints with good mechanical properties, stable magnetic permeability and good weldability. Difference in mechanical, chemical and physical properties between these unique alloys makes such joint difficult and joints mechanical properties and microstructure will be different from parent metals. In this study, GTAW process has been employed with ERNiCrFe-3 electrode to produce dissimilar welding joints with specifies welding procedure parameters, SEM/EDS microstructure analysis, microstructure optical test, Vickers microhardness and tensile test used to study microstructure details and its impacts on welding joint mechanical properties. Research results according to welding zone microstructure analyses shown formation of Widmanstatten ferrite structures and second phase particles with fine graine structure in low alloy steel side the formation of transion zone (TZ). Moreover, clearly fusion line (FL) clearly marked in Monel 400 side while weld metal solidification microstructure with (MGBs) and (SGBs) respectively and interdendritic microstructure observed in weld zone center. Weldment mechanical and microstructure examination indicated the ability to produce like this dissimilar joint with requirement of design criteria and indicated that the failure in like this joint excepted to be in low alloy steel side. The result and microstructure analyses of this research is very important to understanding the variation in welding zone and HAZ microstructure and its impact in weldment mechanical properties and establish the base to produced best welding procedure according to welding zone microstructure properties.
References
- Sudha, C., Paul, V. T., Terrance, A. L. E., Saroja, S., Vijayalakshmi, M. (2006). Microstructure and microchemistry of hard zone in dissimilar weldments of Cr-Mo steels. Welding Journal, 85 (4), 71s–80s. Available at: http://files.aws.org/wj/supplement/04-2006-SUDHA-s.pdf
- Alexandrov, B. T., Lippold, J. C., Sowards, J. W., Hope, A. T., Saltzmann, D. R. (2012). Fusion boundary microstructure evolution associated with embrittlement of Ni–base alloy overlays applied to carbon steel. Welding in the World, 57 (1), 39–53. doi: https://doi.org/10.1007/s40194-012-0007-1
- Nelson, T. W., Lippold, J. C., Mills, M. J. (1998). Investigation of boundaries and structures in dissimilar metal welds. Science and Technology of Welding and Joining, 3 (5), 249–255. doi: https://doi.org/10.1179/stw.1998.3.5.249
- Nelson, T. W., Lippold, J. C., Mills, M. J. (2000). Nature and evolution of the fusion boundary in ferritic-austenitic dissimilar metal welds – part 2: on-cooling transformations. Welding Journal, 10, 267s–277s. Available at: https://app.aws.org/wj/supplement/WJ_2000_10_s267.pdf
- Baeslack III, W. Y., Lippold, J. C., Savage, W. F. (1979). Unmixed zone formation in austenitic stainless steel weldments. Welding Journal, 58 (6), 168s–176s. Available at: http://files.aws.org/wj/supplement/WJ_1979_06_s168.pdf
- Soysal, T., Kou, S., Tat, D., Pasang, T. (2016). Macrosegregation in dissimilar-metal fusion welding. Acta Materialia, 110, 149–160. https://doi.org/10.1016/j.actamat.2016.03.004
- Rowe, M. D., Nelson, T. W., Lippold, J. C. (1999). Hydrogen-induced cracking along the fusion boundary of dissimilar metal welds. Welding Journal, 78, 31s–37s. Available at: http://files.aws.org/wj/supplement/AREFAE_1/ARTICLE1.pdf
- Nelson, T. W., Lippold, J. C., Mills, M. J. (1999). Nature and Evolution of the Fusion Boundary in Ferritic-Austenitic Dissimilar Weld Metals, Part 1 – Nucleation and Growth. Welding Journal, 78 (10), 329s–337s. Available at: http://files.aws.org/wj/supplement/oct99/NELSON.pdf
- Devendranath Ramkumar, K., Joshi, V., Pandit, S., Agrawal, M., Kumar, O. S., Periwal, S. et al. (2014). Investigations on the microstructure and mechanical properties of multi-pass pulsed current gas tungsten arc weldments of Monel 400 and Hastelloy C276. Materials & Design, 64, 775–782. doi: https://doi.org/10.1016/j.matdes.2014.08.055
- Kou, S. (2003). Welding metallurgy. Wiley. doi: https://doi.org/10.1002/0471434027
- Gubeljak, N. (1999). Fracture behaviour of specimens with surface notch tip in the heat affected zone (HAZ) of strength mis-matched welded joints. International Journal of Fracture, 100 (2), 155–167. doi: https://doi.org/10.1023/a:1018794316336
- Cui, Y., Xu, C., Han, Q. (2006). Effect of ultrasonic vibration on unmixed zone formation. Scripta Materialia, 55 (11), 975–978. doi: https://doi.org/10.1016/j.scriptamat.2006.08.035
- Anand, R., Sudha, C., Paul, V. T., Saroja, S., Vijayalakshmi, M. (2010). Microstructural changes in grade 22 ferritic steel clad successively with Ni-based and 9Cr filler metals. Welding Journal, 89 (4), 65s–74s. Available at: https://www.academia.edu/22040613/Microstructural_Changes_in_Grade_22_Ferritic_Steel_Clad_Successively_with_Ni_Based_and_9Cr_Filler_Metals
- Sudha, C., Anand, R., Saroja, S., Vijayalakshmi, M. (2010). Evaluation of concentration dependant diffusion coefficients of carbon in a dissimilar joint of ferritic steels. Transactions of the Indian Institute of Metals, 63 (4), 739–744. doi: https://doi.org/10.1007/s12666-010-0113-y
- Golovanenko, S. A., Konnova, I. Yu. (1972). Selecting interlayers for corrosion resistant bimetals. Metal Science and Heat Treatment, 13 (7-8), 570–575. doi: https://doi.org/10.1007/bf00648199
- Dehmolaei, R., Shamanian, M., Kermanpur, A. (2008). Microstructural characterization of dissimilar welds between alloy 800 and HP heat-resistant steel. Materials Characterization, 59 (10), 1447–1454. doi: https://doi.org/10.1016/j.matchar.2008.01.013
- Shah Hosseini, H., Shamanian, M., Kermanpur, A. (2011). Characterization of microstructures and mechanical properties of Inconel 617/310 stainless steel dissimilar welds. Materials Characterization, 62 (4), 425–431. doi: https://doi.org/10.1016/j.matchar.2011.02.003
- Naffakh, H., Shamanian, M., Ashrafizadeh, F. (2009). Dissimilar welding of AISI 310 austenitic stainless steel to nickel-based alloy Inconel 657. Journal of Materials Processing Technology, 209 (7), 3628–3639. doi: https://doi.org/10.1016/j.jmatprotec.2008.08.019
- Kuo, T.-Y., Lee, H.-T. (2002). Effects of filler metal composition on joining properties of alloy 690 weldments. Materials Science and Engineering: A, 338 (1-2), 202–212. doi: https://doi.org/10.1016/s0921-5093(02)00063-1
- Sayiram, G., Arivazhagan, N. (2015). Microstructural characterization of dissimilar welds between Incoloy 800H and 321 Austenitic Stainless Steel. Materials Characterization, 102, 180–188. doi: https://doi.org/10.1016/j.matchar.2015.03.006
- Lippold, J. C., Kotecki, D. J. (2005). Welding metallurgy and weldability of stainless steels. Wiley, 376.
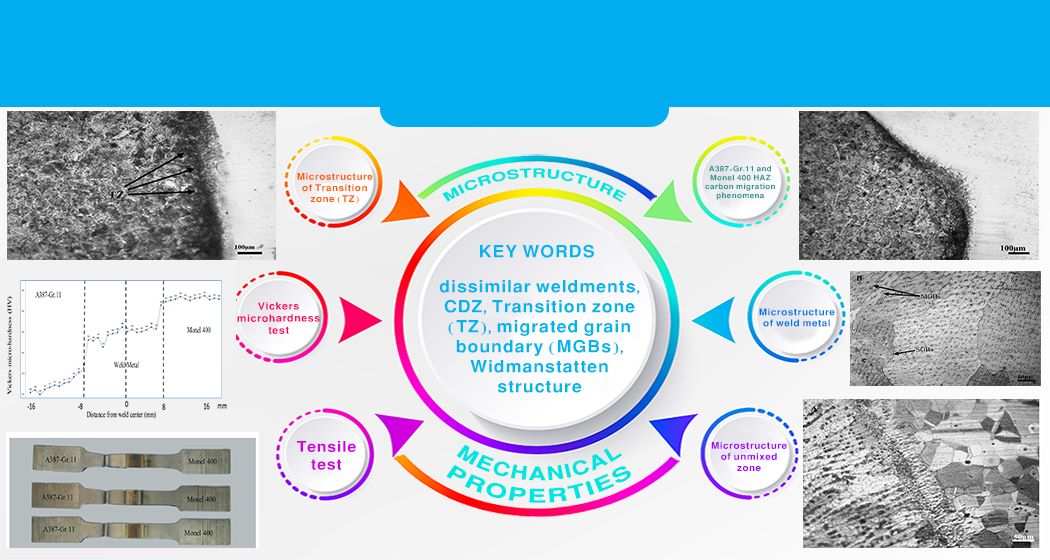
Downloads
Published
How to Cite
Issue
Section
License
Copyright (c) 2022 Ahmed Ghazi, Mohammed Sabeeh, Ahmed Salloum

This work is licensed under a Creative Commons Attribution 4.0 International License.
The consolidation and conditions for the transfer of copyright (identification of authorship) is carried out in the License Agreement. In particular, the authors reserve the right to the authorship of their manuscript and transfer the first publication of this work to the journal under the terms of the Creative Commons CC BY license. At the same time, they have the right to conclude on their own additional agreements concerning the non-exclusive distribution of the work in the form in which it was published by this journal, but provided that the link to the first publication of the article in this journal is preserved.
A license agreement is a document in which the author warrants that he/she owns all copyright for the work (manuscript, article, etc.).
The authors, signing the License Agreement with TECHNOLOGY CENTER PC, have all rights to the further use of their work, provided that they link to our edition in which the work was published.
According to the terms of the License Agreement, the Publisher TECHNOLOGY CENTER PC does not take away your copyrights and receives permission from the authors to use and dissemination of the publication through the world's scientific resources (own electronic resources, scientometric databases, repositories, libraries, etc.).
In the absence of a signed License Agreement or in the absence of this agreement of identifiers allowing to identify the identity of the author, the editors have no right to work with the manuscript.
It is important to remember that there is another type of agreement between authors and publishers – when copyright is transferred from the authors to the publisher. In this case, the authors lose ownership of their work and may not use it in any way.