Constructions of the experimental-estimation model for releasing combustion products at thermal pulse processing
DOI:
https://doi.org/10.15587/1729-4061.2022.267798Keywords:
TEM processing, managed release, numerical modeling, digital twinAbstract
The object of this study are ways to ensure the speed and repeatability of the valve for the release of combustion products from the thermal-pulse unit, which are the most important parameters that enable the precision of the finishing treatment with detonating gas mixtures. The study is aimed at analyzing the process of releasing combustion products in the valve of the proposed design; identification of factors that affect the speed of its opening; establishing the nature of the change in gas dynamic parameters in the combustion chamber. Experimental studies were carried out on a specialized bench simulating the operation of a valve with pressure measurement in gas cavities and controlling the movement of a movable glass of the valve with an incremental encoder. Information on the position of the movable cup is obtained in real time with a decisive ability of 3 microns. The experimental study showed that an increase in the response rate of the valve of the design under consideration to the values required for precision thermal pulse treatment (0.01 s) is possible subject to the use of compressed air. To study the flow processes of high-temperature gases during the operation of the controlled outlet valve, partially immersed in water, a numerical model has been built. A feature of the model is to take into account the real values of the friction force acting on the moving part of the valve, due to the introduction of resistance force acting on the movable glass. The magnitude of this force under the specified initial conditions is assigned from the condition of ensuring the coincidence between the estimated opening time of the valve and its average value obtained from full-scale experiments. For the range of design conditions, based on the lower limit of the working pressure of the combustion products, the water level is determined in the chamber of the thermal pulse equipment, on which the valve must be partially immersed for safe operation
References
- Struckmann, J., Kieser, A. (2020). Thermal deburring. ATL Anlagentechnik Luhden GmbH.
- Plankovskyy, S., Popov, V., Shypul, O., Tsegelnyk, Y., Tryfonov, O., Brega, D. (2021). Advanced thermal energy method for finishing precision parts. Advanced Machining and Finishing, 527–575. doi: https://doi.org/10.1016/b978-0-12-817452-4.00014-2
- Zhao, B., Wei, K., Liu, C., Liu, Q.-Y. (2013). Thermal energy deburring process for parts of hydraulic mechanism in high-voltage switchgear. Gaoya Dianqi/High Voltage Apparatus, 49 (3), 134–138.
- Shypul, O., Myntiuk, V. (2020). Transient Thermoelastic Analysis of a Cylinder Having a Varied Coefficient of Thermal Expansion. Periodica Polytechnica Mechanical Engineering, 64 (4), 273–278. doi: https://doi.org/10.3311/ppme.14733
- Bozhko, V. P., Losev, A. V., Takoriants, M. P., Pleshkov, V. I., Strizhenko, V. E., Levityansky, I. A. et al. (1989). Pat. No. US4802654A. Thermopulse Apparatus for Deburring Parts. No. 4802654. Available at: https://patentimages.storage.googleapis.com/6e/6b/7f/767c65c6595210/US4802654.pdf
- Krivtsov, V. S., Botashev, A. Yu., Maznichenko, S. A. et al. (2005). Impul'snaya rezka goryachego metalla. Kharkiv: Nats. aerokosm. un-t «KhAI», 476.
- Conrad, H.-J., Kaercher, J. (2002). Pat. No. EP1232822A1. Device for thermal deburring of a workpiece. No. 02003311.4; declareted: 13.02.2002; published: 21.08.2002. Available at: https://patents.google.com/patent/EP1232822A1/en
- Plankovskoho, S. I. (Ed.) (2020). Rozroblennia avtomatyzovanoho kompleksu dlia pretsyziynoho termoimpulsnoho obroblennia detonuvalnymy hazovymy sumishamy: naukovi materialy. Kharkiv: Nats. aerokosm. un-t im. M. Ye. Zhukovskoho «Kharkiv. aviats. in-t», 318.
- Gehrmann, C., Gunnarsson, M. (2020). A Digital Twin Based Industrial Automation and Control System Security Architecture. IEEE Transactions on Industrial Informatics, 16 (1), 669–680. doi: https://doi.org/10.1109/tii.2019.2938885
- Kong, K.-J., Jung, S.-H., Jeong, T.-Y., Koh, D.-K. (2019). 1D-3D coupling algorithm for unsteady gas flow analysis in pipe systems. Journal of Mechanical Science and Technology, 33 (9), 4521–4528. doi: https://doi.org/10.1007/s12206-019-0848-2
- Sobieski, W., Grygo, D. (2020). Fluid flow in the impulse valve of a hydraulic ram. Technical Sciences, 3 (22). doi: https://doi.org/10.31648/ts.4965
- Zhu, F., Liu, W., Li, X., Li, Z., Yan, T. (2022). Numerical simulation of gas-liquid two-phase flow on an attitude control system. Journal of Physics: Conference Series, 2276 (1), 012040. doi: https://doi.org/10.1088/1742-6596/2276/1/012040
- Plankovskyy, S. I., Shypul, O. V., Zaklinskyy, S. A., Tryfonov, O. V. (2018). Dynamic method of gas mixtures creation for plasma technologies. Problems of Atomic Science and Technology, 118 (6), 189–193. Available at: https://vant.kipt.kharkov.ua/ARTICLE/VANT_2018_6/article_2018_6_189.pdf
- Philipbar, B. M., Waters, J., Carrington, D. B. (2020). A finite element Menter Shear Stress turbulence transport model. Numerical Heat Transfer, Part A: Applications, 77 (12), 981–997. doi: https://doi.org/10.1080/10407782.2020.1746155
- Raje, P., Sinha, K. (2021). Formulation of advanced SST turbulence model for shock-boundary layer interaction. AIAA AVIATION 2021 FORUM. doi: https://doi.org/10.2514/6.2021-2841
- Ansys, Inc. (2020). ANSYS CFX-Solver Theory Guide Release 2020-R1. ANSYS, Inc., Canonsburg, PA, USA.
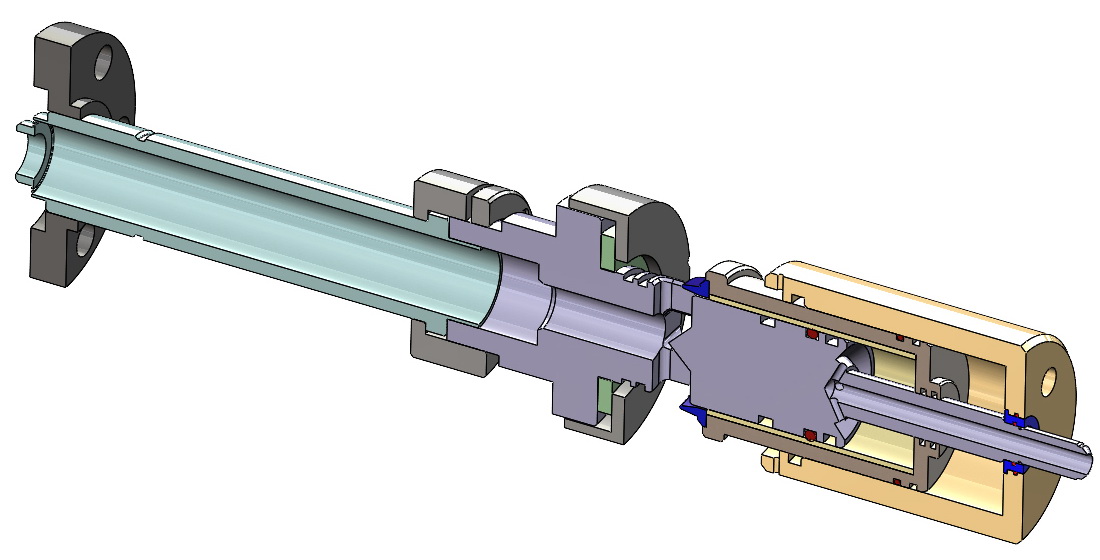
Downloads
Published
How to Cite
Issue
Section
License
Copyright (c) 2022 Oleg Tryfonov, Olga Shypul, Sergiy Plankovsky, Vadym Garin

This work is licensed under a Creative Commons Attribution 4.0 International License.
The consolidation and conditions for the transfer of copyright (identification of authorship) is carried out in the License Agreement. In particular, the authors reserve the right to the authorship of their manuscript and transfer the first publication of this work to the journal under the terms of the Creative Commons CC BY license. At the same time, they have the right to conclude on their own additional agreements concerning the non-exclusive distribution of the work in the form in which it was published by this journal, but provided that the link to the first publication of the article in this journal is preserved.
A license agreement is a document in which the author warrants that he/she owns all copyright for the work (manuscript, article, etc.).
The authors, signing the License Agreement with TECHNOLOGY CENTER PC, have all rights to the further use of their work, provided that they link to our edition in which the work was published.
According to the terms of the License Agreement, the Publisher TECHNOLOGY CENTER PC does not take away your copyrights and receives permission from the authors to use and dissemination of the publication through the world's scientific resources (own electronic resources, scientometric databases, repositories, libraries, etc.).
In the absence of a signed License Agreement or in the absence of this agreement of identifiers allowing to identify the identity of the author, the editors have no right to work with the manuscript.
It is important to remember that there is another type of agreement between authors and publishers – when copyright is transferred from the authors to the publisher. In this case, the authors lose ownership of their work and may not use it in any way.