Identifying features in the structural and phase composition of the products of recycling of the scale of high-speed cutting steel by carbon thermal reduction
DOI:
https://doi.org/10.15587/1729-4061.2022.269507Keywords:
oxide man-made waste, scale of high-speed steels, carbon-thermal reduction, structural-phase transformationsAbstract
This paper reports a study into the features of the structural-phase composition of products from the carbon-thermal reduction of scale of high-speed steels that yields an alloying additive. This is necessary to determine the technological parameters that reduce the loss of target elements in the process of obtaining and using resource-saving alloying material. The study indicates that when the degree of scale reduction changed from 28 % to 67 % and 81 %, an increase in the manifestation of a solid solution of carbon and alloying elements in the α-Fe lattice was observed. At the same time, the intensity of the diffraction maxima of FeO and Fe3O4 decreased. In the reduced products, the presence of Fe3C, FeW3C, Fe3W3C, and WC was traced. With an increase in the degree of scale reduction from 28 % to 67 %, the disordered (of "loose" appearance) microstructure was replaced with the formed particles of round and multifaceted shape with different content of alloying elements. At the reduction stage of 81 %, the microstructure had a finely fibrous structure. Based on the suite of studies, the most acceptable degree of reduction of scale of high-speed steel, followed by the use of the obtained material as an alloying additive, is 81 %. At the same time, ensuring the degree of recovery at the level of 67 % would also suffice. This is due to the fact that residual carbon in the form of carbides provides an increased reducing ability and degree of assimilation of alloying elements with the restoration of the residual oxide component in the liquid metal during doping. Spongy microstructure contributes to faster dissolution, in relation to the corresponding standard ferroalloys. This ensures a reduction in the total smelting time and, as a result, a decrease in the energy consumed
References
- Henckens, M. L. C. M., van Ierland, E. C., Driessen, P. P. J., Worrell, E. (2016). Mineral resources: Geological scarcity, market price trends, and future generations. Resources Policy, 49, 102–111. doi: https://doi.org/10.1016/j.resourpol.2016.04.012
- Poliakov, A., Dzyuba, A., Volokh, V., Petryshchev, A., Tsymbal, B., Yamshinskij, M. et al. (2021). Identification of patterns in the structural and phase composition of the doping alloy derived from metallurgical waste processing. Eastern-European Journal of Enterprise Technologies, 2 (12 (110)), 38–43. doi: https://doi.org/10.15587/1729-4061.2021.230078
- Sekiguchi, N. (2017). Trade specialisation patterns in major steelmaking economies: the role of advanced economies and the implications for rapid growth in emerging market and developing economies in the global steel market. Mineral Economics, 30 (3), 207–227. doi: https://doi.org/10.1007/s13563-017-0110-2
- Mechachti, S, Benchiheub, O., Serrai, S., Shalabi, M. (2013). Preparation of iron Powders by Reduction of Rolling Mill Scale. International Journal of Scientific & Engineering Research, 4 (5), 1467–1472. Available at: https://www.ijser.org/researchpaper/Preparation-of-Iron-Powders-by-Reduction-Rolling-Mill-Scale.pdf
- Grigor’ev, S. M., Petrishchev, A. S. (2012). Assessing the phase and structural features of the scale on P6M5Φ3 and P12M3K5Φ2 steel. Steel in Translation, 42 (3), 272–275. doi: https://doi.org/10.3103/s0967091212030059
- Smirnov, A. N., Petrishchev, A. S., Semiryagin, S. V. (2021). Reduction Smelting of Corrosion-Resistant Steel Waste: Aspects of Structural and Phase Transformations. Steel in Translation, 51 (7), 484–489. doi: https://doi.org/10.3103/s0967091221070093
- Tsymbal, B., Petryshchev, A., Anrieieva, L., Sharovatova, O. (2022). Improving Occupational Safety and Health in the Processing of Metallurgical Waste and Features of their Microstructure Transformation. Key Engineering Materials, 925, 187–196. doi: https://doi.org/10.4028/p-f9x0w1
- Zhu, H., Li, Z., Yang, H., Luo, L. (2013). Carbothermic Reduction of MoO3 for Direct Alloying Process. Journal of Iron and Steel Research International, 20 (10), 51–56. doi: https://doi.org/10.1016/s1006-706x(13)60176-4
- Ryndiaiev, V., Kholodiuk, O., Khmelovskyi, V., Petryshchev, A., Yushchenko, A., Fesenko, H. et al. (2021). Establishing patterns of the structural-phase transformations during the reduction of tungsten-containing ore concentrate with carbon. Eastern-European Journal of Enterprise Technologies, 1 (12 (109)), 16–21. doi: https://doi.org/10.15587/1729-4061.2021.225389
- Shveikin, G. P., Kedin, N. A. (2014). Products of carbothermal reduction of tungsten oxides in argon flow. Russian Journal of Inorganic Chemistry, 59 (3), 153–158. doi: https://doi.org/10.1134/s0036023614030206
- Zhao, L., Wang, L., Chen, D., Zhao, H., Liu, Y., Qi, T. (2015). Behaviors of vanadium and chromium in coal-based direct reduction of high-chromium vanadium-bearing titanomagnetite concentrates followed by magnetic separation. Transactions of Nonferrous Metals Society of China, 25 (4), 1325–1333. doi: https://doi.org/10.1016/s1003-6326(15)63731-1
- Ryabchikov, I. V., Belov, B. F., Mizin, V. G. (2014). Reactions of metal oxides with carbon. Steel in Translation, 44 (5), 368–373. doi: https://doi.org/10.3103/s0967091214050118
- Simonov, V. K., Grishin, A. M. (2013). Thermodynamic analysis and the mechanism of the solid-phase reduction of Cr2O3 with carbon: Part 1. Russian Metallurgy (Metally), 2013 (6), 425–429. doi: https://doi.org/10.1134/s0036029513060153
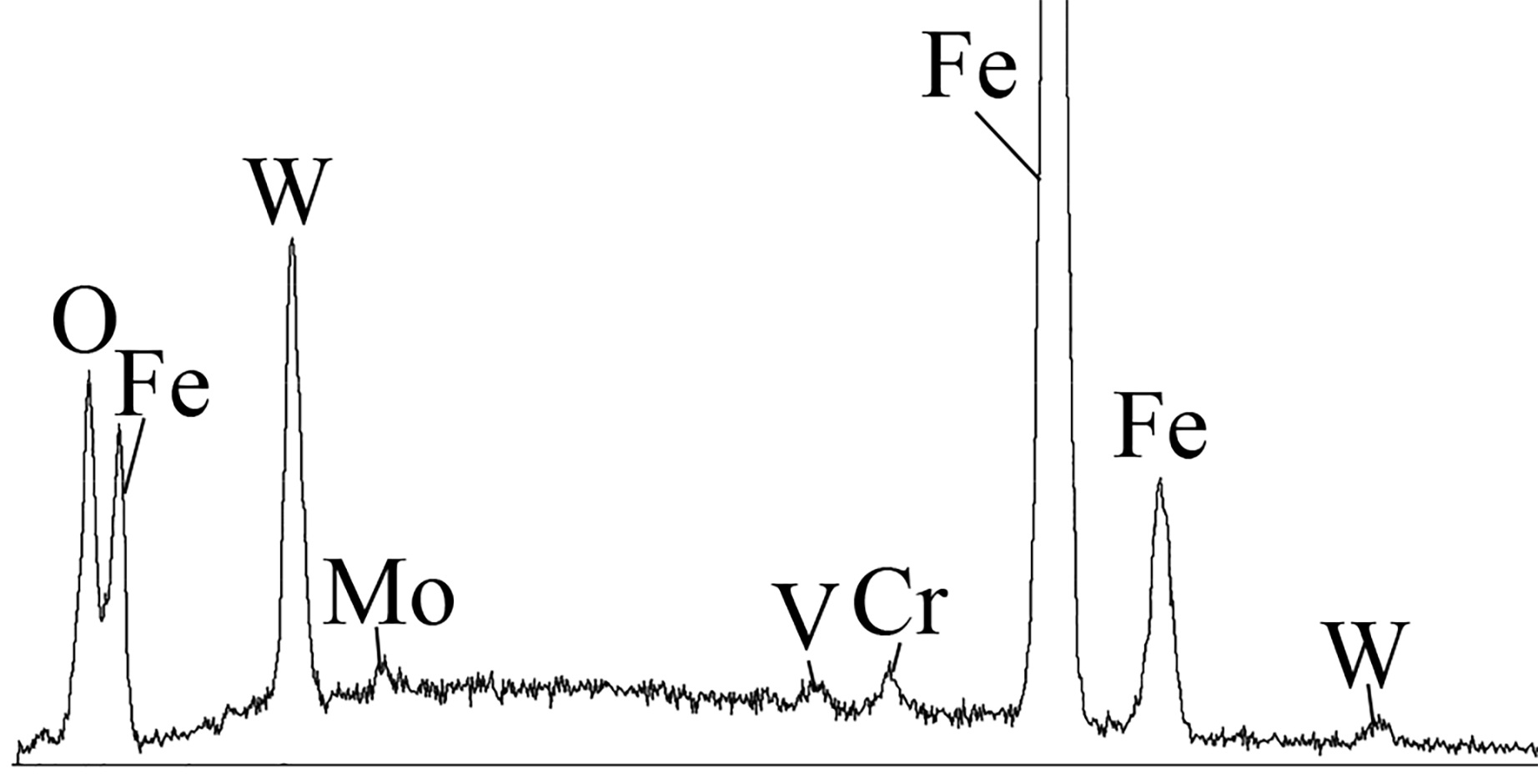
Downloads
Published
How to Cite
Issue
Section
License
Copyright (c) 2022 Viacheslav Borysov, Oleksii Torubara, Vadym Volokh, Anatolii Poliakov, Mykhail Yamshinskij, Ivan Lukianenko, Andrey Andreev, Tamara Bilko, Dmytro Zhuravel, Dmytro Ivanchenko

This work is licensed under a Creative Commons Attribution 4.0 International License.
The consolidation and conditions for the transfer of copyright (identification of authorship) is carried out in the License Agreement. In particular, the authors reserve the right to the authorship of their manuscript and transfer the first publication of this work to the journal under the terms of the Creative Commons CC BY license. At the same time, they have the right to conclude on their own additional agreements concerning the non-exclusive distribution of the work in the form in which it was published by this journal, but provided that the link to the first publication of the article in this journal is preserved.
A license agreement is a document in which the author warrants that he/she owns all copyright for the work (manuscript, article, etc.).
The authors, signing the License Agreement with TECHNOLOGY CENTER PC, have all rights to the further use of their work, provided that they link to our edition in which the work was published.
According to the terms of the License Agreement, the Publisher TECHNOLOGY CENTER PC does not take away your copyrights and receives permission from the authors to use and dissemination of the publication through the world's scientific resources (own electronic resources, scientometric databases, repositories, libraries, etc.).
In the absence of a signed License Agreement or in the absence of this agreement of identifiers allowing to identify the identity of the author, the editors have no right to work with the manuscript.
It is important to remember that there is another type of agreement between authors and publishers – when copyright is transferred from the authors to the publisher. In this case, the authors lose ownership of their work and may not use it in any way.