Визначення динамічних та тягово-енергетичних показників повнопривідної тягово-транспортної машини
DOI:
https://doi.org/10.15587/1729-4061.2023.270988Ключові слова:
кутова швидкість обертання, крутний момент, дотична сила тяги, повнопривідна колісна тягово-транспортна машинаАнотація
Наведено результати дослідження динамічних та тягово-енергетичних показників повнопривідної колісної тягово-транспортної машини. Складено схему динамічної моделі трансмісії повнопривідної колісної тягово-транспортної машини та систему рівнянь динаміки трансмісії у формі Коші. Це дозволило визначити залежності кутових швидкостей обертання елементів трансмісії тягово-транспортної машини, залежності крутних моментів та залежності дотичних сил тяги на колесах від часу. Метод дозволяє визначати оптимальні параметри трансмісії, конструкції диференціалів та передавальні числа для підвищення тягово-зчіпних та паливо-економічних показників машини. Встановлено, що кутові швидкості обертання передніх коліс тягово-транспортної машини 1,29 рад/с, 1,27 рад/с вище за кутові швидкості обертання задніх коліс 1,24 рад/с, 1,25 рад/с, що призводить до появи кінематичної невідповідності та додаткових втрат енергії. Визначені крутні моменти передніх ведучих коліс, що складають 6972 Н×м, задніх ведучих коліс 4622 Н×м. Дотичні сили тяги на передніх колесах машини складають 5478 Н після закінчення розгону машини, на задніх колесах – 3473 Н. Експериментальні дослідження виконані на прикладі повнопривідного колісного трактору з шарнірно-з’єднаною рамою для валідації методу оцінки динаміки трансмісії тягово-транспортної машини. Розбіжність між значеннями кутових швидкостей обертання коліс та дотичних сил тяги на колесах, що визначені теоретично та отримано підчас експериментальних досліджень, складає 2 %. Розроблений метод оцінки динаміки трансмісії повнопривідної тягово-транспортної машини необхідно вважати валідним. Запропонований у роботі метод можна застосовувати для оцінки динаміки колісних автотранспортних засобів
Посилання
- Bulgakov, V., Ivanovs, S., Adamchuk, V., Antoshchenkov, R. (2019). Investigations of the Dynamics of a Four-Element Machine-and-Tractor Aggregate. Acta Technologica Agriculturae, 22 (4), 146–151. doi: https://doi.org/10.2478/ata-2019-0026
- Antoshchenkov, R., Halych, I., Nykyforov, A., Cherevatenko, H., Chyzhykov, I., Sushko, S. et al. (2022). Determining the influence of geometric parameters of the traction-transportation vehicle’s frame on its tractive capacity and energy indicators. Eastern-European Journal of Enterprise Technologies, 2 (7 (116)), 60–61. doi: https://doi.org/10.15587/1729-4061.2022.254688
- Kondratiev, A. (2019). Improving the mass efficiency of a composite launch vehicle head fairing with a sandwich structure. Eastern-European Journal of Enterprise Technologies, 6 (7 (102)), 6–18. doi: https://doi.org/10.15587/1729-4061.2019.184551
- Osadchyy, V., Nazarova, O., Brylystyi, V. (2021). Laboratory Stand for Research of Energy Characteristics of Electric Vehicle Drives. 2021 IEEE International Conference on Modern Electrical and Energy Systems (MEES). doi: https://doi.org/10.1109/mees52427.2021.9598661
- Osadchyy, V., Nazarova, O., Olieinikov, M. (2021). The Research of a Two-Mass System with a PID Controller, Considering the Control Object Identification. 2021 IEEE International Conference on Modern Electrical and Energy Systems (MEES). doi: https://doi.org/10.1109/mees52427.2021.9598542
- Voloshina, A., Panchenko, A., Titova, O., Milaeva, I., Pastushenko, A. (2021). Prediction of Changes in the Output Characteristics of the Planetary Hydraulic Motor. Advanced Manufacturing Processes II, 744–754. doi: https://doi.org/10.1007/978-3-030-68014-5_72
- Panchenko, A., Voloshina, A., Luzan, P., Panchenko, I., Volkov, S. (2021). Kinematics of motion of rotors of an orbital hydraulic machine. IOP Conference Series: Materials Science and Engineering, 1021 (1), 012045. doi: https://doi.org/10.1088/1757-899x/1021/1/012045
- Adamchuk, V., Petrychenko, I., Korenko, M., Beloev, H., Borisov, B. (2018). Study plane-parallel motion movement combined seeding unit. Mechanization in agriculture & Conserving of the resources, 64 (6), 184–187. Available at: https://stumejournals.com/journals/am/2018/6/184
- Awadallah, M., Tawadros, P., Walker, P., Zhang, N. (2017). Dynamic modelling and simulation of a manual transmission based mild hybrid vehicle. Mechanism and Machine Theory, 112, 218–239. doi: https://doi.org/10.1016/j.mechmachtheory.2017.02.011
- Tian, Y., Ruan, J., Zhang, N., Wu, J., Walker, P. (2018). Modelling and control of a novel two-speed transmission for electric vehicles. Mechanism and Machine Theory, 127, 13–32. doi: https://doi.org/10.1016/j.mechmachtheory.2018.04.023
- Dong, H., Zhuang, W., Chen, B., Wang, Y., Lu, Y., Liu, Y. et al. (2022). A comparative study of energy-efficient driving strategy for connected internal combustion engine and electric vehicles at signalized intersections. Applied Energy, 310, 118524. doi: https://doi.org/10.1016/j.apenergy.2022.118524
- Morselli, R., Zanasi, R., Sandoni, G. (2006). Detailed and reduced dynamic models of passive and active limited-slip car differentials. Mathematical and Computer Modelling of Dynamical Systems, 12 (4), 347–362. doi: https://doi.org/10.1080/13873950500066959
- Tajanowskij, G., Tanaś, W. (2012). Analysis of movement kinematics at turn of wheel tractor with semi-trailer with articulated operated draught bar. Journal of Research and Applications in Agricultural Engineering, 57 (2), 190–196. Available at: http://yadda.icm.edu.pl/baztech/element/bwmeta1.element.baztech-article-BAR8-0019-0058/c/httpwww_pimr_poznan_plbiul2012237tt.pdf
- Padureanu, V., Lupu, M. I., Canja, C. M. (2013). Theoretical research to improve traction performance of wheeled tractors by using a suplementary driven axle. Computational Mechanics and Virtual Engineering. Brasov, 410–415. Available at: http://aspeckt.unitbv.ro/jspui/bitstream/123456789/415/1/410%20-%20415%2c%20Padureanu%201.pdf
- Suhane, A., Rana, R. S., Purohit, R. (2018). Prospects of Torsen Differential in Four Wheel Drive Automobile Transmission System. Materials Today: Proceedings, 5 (2), 4036–4045. https://doi.org/10.1016/j.matpr.2017.11.664
- Efimov, A., Polushkin, O., Kireev, S., Korchagina, M. (2021). A Mathematical Model of a Differential Drive with a Limited Gear Ratio. Transportation Research Procedia, 54, 699–711. doi: https://doi.org/10.1016/j.trpro.2021.02.123
- Yin, Z., Dai, Q., Guo, H., Chen, H., Chao, L. (2018). Estimation Road Slope and Longitudinal Velocity for Four-wheel Drive Vehicle. IFAC-PapersOnLine, 51 (31), 572–577. doi: https://doi.org/10.1016/j.ifacol.2018.10.139
- Galych, I., Antoshchenkov, R., Antoshchenkov, V., Lukjanov, I., Diundik, S., Kis, O. (2021). Estimating the dynamics of a machine-tractor assembly considering the effect of the supporting surface profile. Eastern-European Journal of Enterprise Technologies, 1 (7 (109)), 51–62. doi: https://doi.org/10.15587/1729-4061.2021.225117
- Artiomov, N., Antoshchenkov, R., Antoshchenkov, V., Ayubov, A. (2021). Innovative approach to agricultural machinery testing. Engineering for Rural Development. Jelgava, 692–698. doi: https://doi.org/10.22616/ERDev.2021.20.TF150
- Antoshchenkov R. (2017). Dynamika ta enerhetyka rukhu bahatoelementnykh mashynno-traktornykh ahrehativ. Kharkiv: KhNTUSH, 244. Available at: https://www.academia.edu/43129375/ДИНАМІКА_ТА_ЕНЕРГЕТИКА_РУХУ_БАГАТОЕЛЕМЕНТНИХ_МАШИННО_ТРАКТОРНИХ_АГРЕГАТІВ
- Dzyuba, O., Dzyuba, A., Polyakov, A., Volokh, V., Antoshchenkov, R., Mykhailov, A. (2019). Studying the influence of structural-mode parameters on energy efficiency of the plough PLN-3-35. Eastern-European Journal of Enterprise Technologies, 3 (1 (99)), 55–65. doi: https://doi.org/10.15587/1729-4061.2019.169903
- Mittal, A., Misra, A. (2021). A novel mathematical model to estimate the ride frequency of an off road vehicle with experimental validation. Materials Today: Proceedings, 46, 9683–9689. doi: https://doi.org/10.1016/j.matpr.2020.08.022
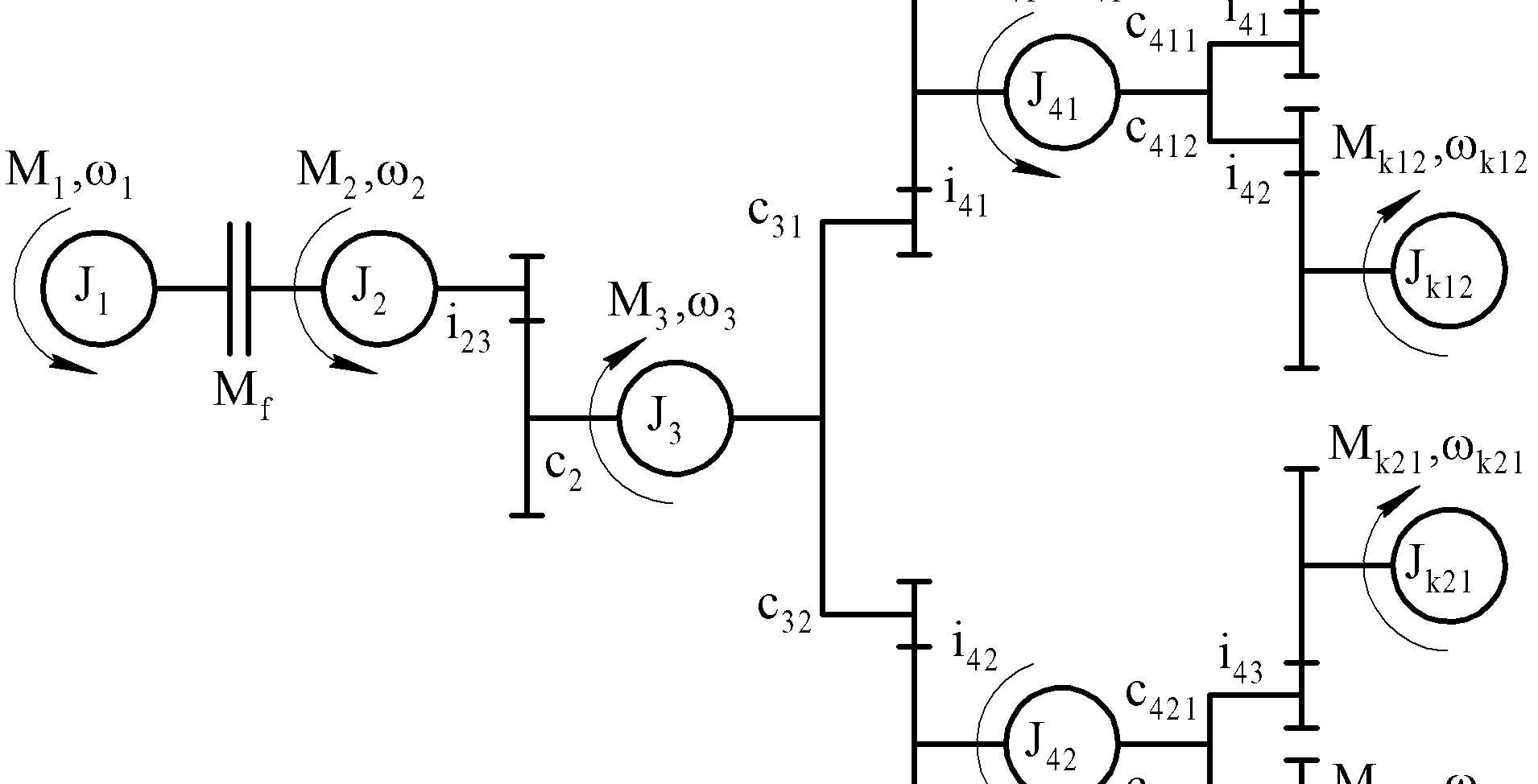
##submission.downloads##
Опубліковано
Як цитувати
Номер
Розділ
Ліцензія
Авторське право (c) 2022 Roman Antoshchenkov, Serhii Bogdanovich, Ivan Halych, Halyna Cherevatenko

Ця робота ліцензується відповідно до Creative Commons Attribution 4.0 International License.
Закріплення та умови передачі авторських прав (ідентифікація авторства) здійснюється у Ліцензійному договорі. Зокрема, автори залишають за собою право на авторство свого рукопису та передають журналу право першої публікації цієї роботи на умовах ліцензії Creative Commons CC BY. При цьому вони мають право укладати самостійно додаткові угоди, що стосуються неексклюзивного поширення роботи у тому вигляді, в якому вона була опублікована цим журналом, але за умови збереження посилання на першу публікацію статті в цьому журналі.
Ліцензійний договір – це документ, в якому автор гарантує, що володіє усіма авторськими правами на твір (рукопис, статтю, тощо).
Автори, підписуючи Ліцензійний договір з ПП «ТЕХНОЛОГІЧНИЙ ЦЕНТР», мають усі права на подальше використання свого твору за умови посилання на наше видання, в якому твір опублікований. Відповідно до умов Ліцензійного договору, Видавець ПП «ТЕХНОЛОГІЧНИЙ ЦЕНТР» не забирає ваші авторські права та отримує від авторів дозвіл на використання та розповсюдження публікації через світові наукові ресурси (власні електронні ресурси, наукометричні бази даних, репозитарії, бібліотеки тощо).
За відсутності підписаного Ліцензійного договору або за відсутністю вказаних в цьому договорі ідентифікаторів, що дають змогу ідентифікувати особу автора, редакція не має права працювати з рукописом.
Важливо пам’ятати, що існує і інший тип угоди між авторами та видавцями – коли авторські права передаються від авторів до видавця. В такому разі автори втрачають права власності на свій твір та не можуть його використовувати в будь-який спосіб.