Features of structure formation when surfacing steel (iron) on titanium with plasma sprayed coatings in the technology of obtaining butt joint of bimetallic plates "titanium – steel"
DOI:
https://doi.org/10.15587/1729-4061.2023.275510Keywords:
titanium–steel bimetal, multi-pass welding, barrier layer, intermetallide phases, section boundaryAbstract
The object of this study is structural formation during the surfacing of steel (iron) on titanium with plasma-sprayed coatings to obtain a butt connection of titanium-steel bimetallic plates. The task to be solved was to devise a technology for applying a barrier layer between titanium and steel to obtain a defect-free butt joint of the edges of bimetallic sheets of carbon steel, clad with a layer of titanium, under conditions of arc or plasma surfacing of carbon steel on titanium. The application of the barrier layer was carried out by plasma spraying of steel wire or iron powder. In this case, a coating with a thickness of 150...750 μm was applied on Grade2 titanium, on which 1–2 mm thick layers of materials similar to the sprayed ones were deposited by arc and plasma deposition. It was established that during spraying with subsequent surfacing of steel wire or iron powder, the main technological factors for eliminating cracks in the resulting compound are the thickness of the sprayed coating and the amount of linear surfacing energy. The thickness of the sprayed coating was selected (at least 400...600 microns) followed by plasma surfacing of ER70S-6 steel wire with a diameter of 1.0 mm or CNPC-Fe200 iron powder with unit energy up to ~200...250 J/mm. A defect-free transition layer from titanium to steel was obtained. It is a continuous layer with a thickness of 50–60 microns, consisting of intermetalides FeTi and FeTi2, as well as a β-phase titanium with an enhanced iron content, which retains certain ductility without cracks and other defects. With the help of the devised approach for connecting titanium-steel bimetallic edges, it is planned to manufacture seam bimetallic pipes for main pipelines to transport oil and gas raw materials extracted from wells.
References
- Pasang, T., Pramana, S., Kracum, M., Misiolek, W., Aziziderouei, M., Mizutani, M., Kamiya, O. (2018). Characterisation of Intermetallic Phases in Fusion Welded Commercially Pure Titanium and Stainless Steel 304. Metals, 8 (11), 863. doi: https://doi.org/10.3390/met8110863
- Korzhyk, V., Khaskin, V., Grynyuk, A., Ganushchak, O., Shcheretskiy, V., Peleshenko, S. et al. (2021). Analyzing metallurgical interaction during arc surfacing of barrier layers on titanium to prevent the formation of intermetallics in titanium-steel compounds. Eastern-European Journal of Enterprise Technologies, 5 (12 (113)), 69–82. doi: https://doi.org/10.15587/1729-4061.2021.240154
- Cheepu, M., Muthupandi, V., Srinivas, B., Sivaprasad, K. (2017). Development of a Friction Welded Bimetallic Joints Between Titanium and 304 Austenitic Stainless Steel. Techno-Societal 2016, 709–717. doi: https://doi.org/10.1007/978-3-319-53556-2_73
- Mo, D., Song, T., Fang, Y., Jiang, X., Luo, C. Q., Simpson, M. D., Luo, Z. (2018). A Review on Diffusion Bonding between Titanium Alloys and Stainless Steels. Advances in Materials Science and Engineering, 2018, 1–15. doi: https://doi.org/10.1155/2018/8701890
- Liu, D., Wang, W., Zha, X., Jiao, H., Zhao, L., Han, S. (2021). Experimental investigation of butt welded Ti/steel bimetallic sheets by using multi-principal powders as a single filler metal. Journal of Materials Research and Technology, 15, 1499–1512. doi: https://doi.org/10.1016/j.jmrt.2021.09.004
- Szymlek, K. (2008). Review of Titanium and Steel Welding Methods. Advances in Materials Sciences, 8 (1). doi: https://doi.org/10.2478/v10077-008-0023-4
- Chu, Q., Bai, R., Zhang, M., Li, J., Lei, Z., Hu, N. et al. (2017). Microstructure and mechanical properties of titanium/steel bimetallic joints. Materials Characterization, 132, 330–337. doi: https://doi.org/10.1016/j.matchar.2017.08.025
- Chu, Q., Tong, X., Xu, S., Zhang, M., Yan, F., Cheng, P., Yan, C. (2020). The formation of intermetallics in Ti/steel dissimilar joints welded by Cu-Nb composite filler. Journal of Alloys and Compounds, 828, 154389. doi: https://doi.org/10.1016/j.jallcom.2020.154389
- Torbati, A. M., Miranda, R. M., Quintino, L., Williams, S. (2010). Welding bimetal pipes in duplex stainless steel. The International Journal of Advanced Manufacturing Technology, 53 (9-12), 1039–1047. doi: https://doi.org/10.1007/s00170-010-2889-7
- Petrov, S. V., Korzhik, V. N. (2011). Ustanovka Plazer 80-PL dlya plazmennogo napyleniya. Svarschik, 3, 22–26.
- Korzhik, V. N., Korob, M. F. (2012). Mekhanizirovannaya liniya PLAZER 30PL-W dlya plazmenno-dugovogo provolochnogo napyleniya pokrytiy na krupnogabaritnye detali tipa "val". Svarschik, 4, 13–15.
- Lunev, V. M., Nemashkalo, O. V. (2010). Adgezionnye kharakteristiki pokrytiy i metody ikh izmereniya. Fizicheskaya inzheneriya poverkhnosti, 8 (1), 64–71. Available at: http://dspace.nbuv.gov.ua/handle/123456789/98847
- Grinyuk, A. A., Korzhik, V. N., Babich, A. A., Tkachuk, V. I., Peleshenko, S. I. (2016). Unifitsirovanniy plazmotron dlya svarki szhatoy dugoy neplavyaschimsya elektrodom. Tekhnologicheskie sistemy, 4, 86–89.
- Korzhik, V. N., Vojtenko, A. N., Peleshenko, S. I., Tkachuk, V. I., Khaskin, V. Yu., Grinyuk, A. A. (2017). Development of automated equipment for manufacturing 3D metal products based on additive technologies. The Paton Welding Journal, 2017 (6), 79–85. doi: https://doi.org/10.15407/tpwj2017.06.15
- Okada, A. (1977). Application of Melting Efficiency and its Problems. Journal of the Japan Welding Society, 46 (2), 53–61. doi: https://doi.org/10.2207/qjjws1943.46.2_53
- Dupont, J. N., Marder, A. R. (1995). Thermal Efficiency of Arc Welding Processes. Welding Journal, 74, 406s–416s. Available at: http://files.aws.org/wj/supplement/WJ_1995_12_s406.pdf
- Fuerschbach, P. W., Knorovsky, G. A. (1991). A Study of Melting Efficiency in Plasma Arc and Gas Tungsten Arc Welding. Welding Journal, 70, 287s–297s. Available at: https://app.aws.org/wj/supplement/WJ_1991_11_s287.pdf
- Ryabtsev, I. A., Soloviov, V. G., Lankin, Yu. N., Babinets, A. A. (2017). Computer system for automatic control of arc surfacing processes using electrode wires. The Paton Welding Journal, 2017 (6), 34–36. doi: https://doi.org/10.15407/tpwj2017.06.07
- Dubovoy, O. M., Karpechenko, A. A., Bobrov, M. M., Gerasin, O. S., Lymar, O. O. (2021). Electric arc spraying of cermet coatings of steel 65G-Tic system. Naukovyi Visnyk Natsionalnoho Hirnychoho Universytetu, 2, 63–68. doi: https://doi.org/10.33271/nvngu/2021-2/063
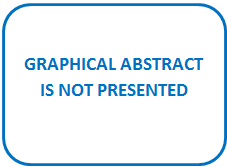
Downloads
Published
How to Cite
Issue
Section
License
Copyright (c) 2023 Volodymyr Korzhyk, Vladyslav Khaskin, Oleg Ganushchak, Dmytro Strohonov, Yevhenii Illiashenko, Nataliia Fialko, Chunfu Guo, Andrii Grynyuk, Sviatoslav Peleshenko, Andrii Aloshyn

This work is licensed under a Creative Commons Attribution 4.0 International License.
The consolidation and conditions for the transfer of copyright (identification of authorship) is carried out in the License Agreement. In particular, the authors reserve the right to the authorship of their manuscript and transfer the first publication of this work to the journal under the terms of the Creative Commons CC BY license. At the same time, they have the right to conclude on their own additional agreements concerning the non-exclusive distribution of the work in the form in which it was published by this journal, but provided that the link to the first publication of the article in this journal is preserved.
A license agreement is a document in which the author warrants that he/she owns all copyright for the work (manuscript, article, etc.).
The authors, signing the License Agreement with TECHNOLOGY CENTER PC, have all rights to the further use of their work, provided that they link to our edition in which the work was published.
According to the terms of the License Agreement, the Publisher TECHNOLOGY CENTER PC does not take away your copyrights and receives permission from the authors to use and dissemination of the publication through the world's scientific resources (own electronic resources, scientometric databases, repositories, libraries, etc.).
In the absence of a signed License Agreement or in the absence of this agreement of identifiers allowing to identify the identity of the author, the editors have no right to work with the manuscript.
It is important to remember that there is another type of agreement between authors and publishers – when copyright is transferred from the authors to the publisher. In this case, the authors lose ownership of their work and may not use it in any way.