Development of a virtual hardware temperature observer for frequency-controlled asynchronous electric motors
DOI:
https://doi.org/10.15587/1729-4061.2023.280357Keywords:
asynchronous electric motor, renewable energy, temperature observer, resistance, thermal protectionAbstract
One of the most common types of AC electric machines are asynchronous electric motors. Because of their simple and reliable design, they are used in many industries. In this paper, the object of research is an asynchronous electric motor with a short-circuited rotor. To ensure the normal operation of an asynchronous electric motor, the heating temperature of its active parts should not exceed the maximum permissible values, which are determined by the corresponding class of heat resistance of the insulation system used in the electric motor. In asynchronous electric motors, the stator winding is the most thermally vulnerable node, which is the first to fail when the temperature of the electric motor increases. Thermal protection devices protect an asynchronous electric motor from emergency operating modes accompanied by an unacceptable excess of the temperature of their windings.
In order to build an indirect system of protection against overheating of the stator windings, a temperature observer has been developed using already available signals in a frequency-controlled electric drive. Simulation studies were performed in Matlab/Simulink application software packages. Simulation studies were carried out on the basis of asynchronous electric motors of the 4A series with a capacity of 30, 75 and 110 kW in the temperature range from 20 °C to 250 °C. As a result of the research, it was found that the error of indirect calculation of the temperature of electric motors, taking into account the correction factor, does not exceed 1 %. The proposed temperature observer can be used to build protections for asynchronous electric drives
Supporting Agency
- We would like to express our great gratitude to the Doctor of Technical Sciences, Professor Boris Nikolaevich Yashin and Doctor of Technical Sciences Irina Yuryevna Semykina for making a great contribution to the research and development of thermal protection systems of an asynchronous electric motor
References
- Bochkarev, I. V. (2016). Development of device for temperature protection of alternating current electrical machines. Problems of Automation and Control, 2 (31), 84–88.
- Mikhalev, S. V. (2011). Otsenka variantov ispolneniya teplovoy zaschity vysokovol'tnykh elektrodvigateley i puti ee sovershenstvovaniya. Available at: https://energoboard.ru/post/460/
- ABB Ability™ Smart Sensor. Condition monitoring solution for low voltage motors. Service note. ABB. Available at: https://automationdistribution.com/content/ABB-Smart-Sensor%20-Leaflet.pdf
- Issenov, S., Iskakov, R., Tergemes, K., Issenov, Z. (2022). Development of mathematical description of mechanical characteristics of integrated multi-motor electric drive for drying plant. Eastern-European Journal of Enterprise Technologies, 1 (8 (115)), 46–54. doi: https://doi.org/10.15587/1729-4061.2021.251232
- Breido, I. V., Semykina, I. Yu., Nurmaganbetova, G. S. (2018). Method of indirect protection against overheating for electric drives of mining installations. Proceedings of the Tomsk Polytechnic University Engineering of Georesources, 329 (2), 65–71.
- SHamanov, R. S., Perekusikhina, I. A. (2014). Induktivniy pervichniy izmeritel'niy preobrazovatel' zadannogo znacheniya temperatury. Internet-zhurnal «Naukovedenie», 3, 1–8.
- DS18B20 – datchik temperatury s interfeysom 1-Wire. Opisanie na russkom yazyke. Available at: http://mypractic.ru/ds18b20-datchik-temperatury-s-interfejsom-1-wire-opisanie-na-russkom-yazyke.html
- Low voltage. General performance motors (2016). ABB.
- Derevyago, T. M., Mikhal'tsevich, G. A. (2017). Osobennosti konstruktsii i primeneniya termorezistorov v elektricheskikh tsepyakh. Aktual'nye problemy energetiki: materialy 73-y nauchno-tekhnicheskoy konferentsii studentov i aspirantov. Minsk: BNTU, 865–870.
- Yurieva, E. Y., Shayda, V. P., Patsula, A. F. (2011). Verification of adequacy of graphic method of determining the final temperature of induction motor heating. Material of International scientific conference MicroCAD. Kharkiv, 58–61.
- Petrushin, V. (2017). Asinkhronnye korotkozamknutye dvigateli v reguliruemom elektroprivode. Moscow: LAP Lambert Academic Publishing, 344.
- Firago, B. I., Vasil'ev, D. S. (2016). Vektornye sistemy upravleniya elektroprivodami. Minsk: Vysh. shk., 159.
- Martin, W., Eason, A., Patel, A. G. (2016). Low Voltage Motor Protection. Rockwell Automation, 30.
- Kireeva, E. A., Tsyruk, S. A. (2013). Releynaya zaschita i avtomatika elektroenergeticheskikh sistem. Moscow: Akademiya, 288.
- Plesca, A. T. (2013). Thermal Analysis of Overload Protection Relays using Finite Element Method. Indian Journal of Science and Technology, 6 (8), 1–6. doi: https://doi.org/10.17485/ijst/2013/v6i8.3
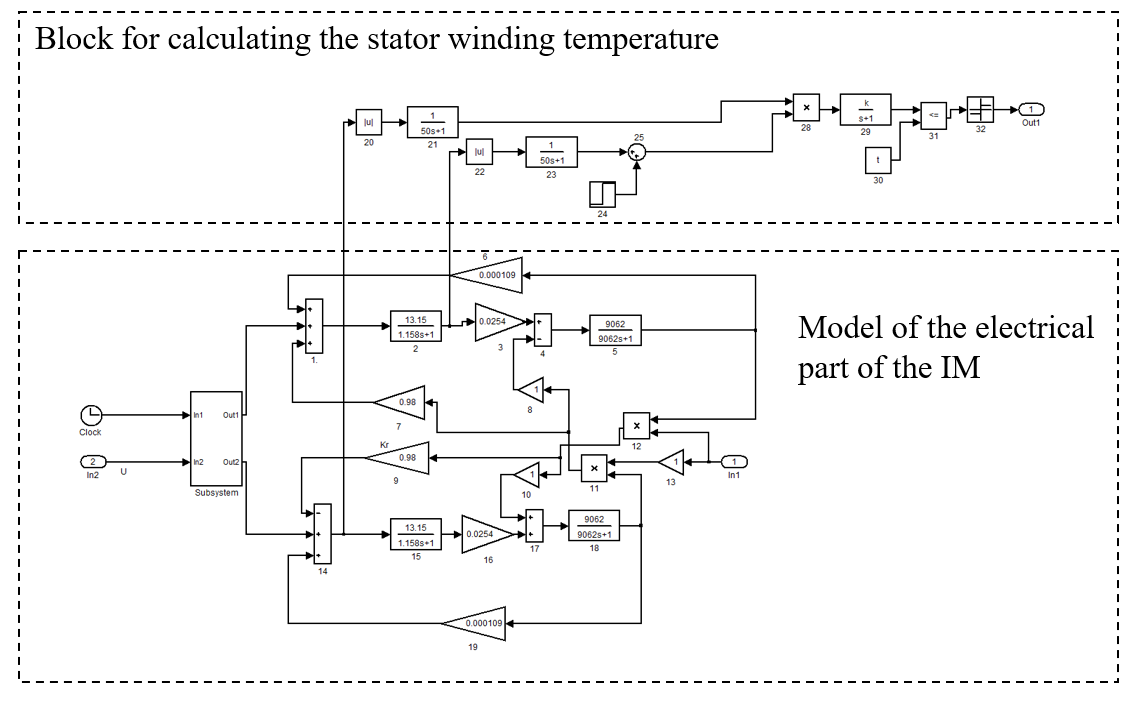
Downloads
Published
How to Cite
Issue
Section
License
Copyright (c) 2023 Gulim Nurmaganbetova, Sultanbek Issenov, Vladimir Kaverin, Zhanat Issenov

This work is licensed under a Creative Commons Attribution 4.0 International License.
The consolidation and conditions for the transfer of copyright (identification of authorship) is carried out in the License Agreement. In particular, the authors reserve the right to the authorship of their manuscript and transfer the first publication of this work to the journal under the terms of the Creative Commons CC BY license. At the same time, they have the right to conclude on their own additional agreements concerning the non-exclusive distribution of the work in the form in which it was published by this journal, but provided that the link to the first publication of the article in this journal is preserved.
A license agreement is a document in which the author warrants that he/she owns all copyright for the work (manuscript, article, etc.).
The authors, signing the License Agreement with TECHNOLOGY CENTER PC, have all rights to the further use of their work, provided that they link to our edition in which the work was published.
According to the terms of the License Agreement, the Publisher TECHNOLOGY CENTER PC does not take away your copyrights and receives permission from the authors to use and dissemination of the publication through the world's scientific resources (own electronic resources, scientometric databases, repositories, libraries, etc.).
In the absence of a signed License Agreement or in the absence of this agreement of identifiers allowing to identify the identity of the author, the editors have no right to work with the manuscript.
It is important to remember that there is another type of agreement between authors and publishers – when copyright is transferred from the authors to the publisher. In this case, the authors lose ownership of their work and may not use it in any way.