Using of microsilica for improvement of physical and mechanical properties of epoxide-based composite material
DOI:
https://doi.org/10.15587/1729-4061.2023.280474Keywords:
filler, microsilica, epoxy resin, composite material, impact strength, tensile modulusAbstract
Utilization of industrial waste and secondary raw materials, in particular, in the production of metallic silicon and silicon-containing alloys, which include silica vapors (microsilica), is the main task of implementing environmental policy and solves the problem of their storage and negative impact on the environment, in order to reuse them in polymer composites. The use of microsilica as a filler in composite materials based on epoxy resins contributes to a positive effect on the basic properties of the resin, and also makes it possible to use the composite material as coatings and parts in the repair of machinery and equipment. The aim of the work was to establish the positive effect of microsilica as a filler in composite materials based on ED-20 epoxy resin on improving the physical and mechanical properties of composite materials. Within the framework of this work, studies were conducted to test composite materials based on ED-20 epoxy resin, differing in different filler content of 2, 5, 10, 15 wt. % on impact strength, tensile strength and modulus of elasticity, adhesion and impact strength of the coating.
The analysis of the obtained results showed a positive effect of microsilica as a filler in composite materials based on ED-20 epoxy resin on the physical and mechanical properties of the composite material. The optimal filler content was determined, which is 2 % of the mass of the ED-20 epoxy resin, while an increase in adhesion, toughness of the composite material by 45 %, tensile strength and modulus of elasticity by 21 % and 5 %, respectively, and the strength of the coating on impact by 32 %, compared with the addition of microsilica in ED-20, which shows the prospects of using microsilica as a filler in composite materials
Supporting Agency
- This study was conducted within the framework of a funded scientific project by the Ministry of Science and Higher Education of the Republic of Kazakhstan (grant no. AP09058166). The study was conducted in the laboratory of the Kazakh Agrotechnical Research University.
References
- Sun W., Xu X., Lv Z., Mao H., Wu J. (2019). Environmental impact assessment of wastewater discharge with multi pollutants from iron and steel industry. Journal of Environmental Management (Vol. 245, p. 210-215).
- Doifode S., Matani A.G. (2015). Effective industrial waste utilization technologies towards cleaner environment. International Journal of Chemical and Physical Science (Vol. 4., p. 536-540).
- Andrzejuk W., Barnat-Hunek D., Gora J. (2019). Physical properties of mineral and recycled aggregates used to mineral-asphalt mixtures. Materials (Vol. 12, p.3437).
- Gil D.M., Golewski G.L. (2018). Potential of siliceous fly ash and silica fume as a substitute for binder in cementitious concretes. SOLINA 2018 - VII Conference SOLINA Sustainable Development: Architecture - Building Construction - Environmental Engineering and Protection Innovative Energy-Efficient Technologies - Utilization of Renewable Energy Sources (Vol. 49, p.00030).
- Wan J., Li C., Bu Z.-Y., Xu C.-J., Li B.-G., Fan H. (2012). A comparative study of epoxy resin cured with a linear diamine and a branched polyamine. Chemical Engineering Journal (Vol. 188, p. 160-172).
- Gómez-del Río T., Rodríguez J., Pearson R.A. (2014). Compressive properties of nanoparticle modified epoxy resin at different strain rates. Composites Part B: Engineering (Vol. 57, p. 173-179).
- Sukanto H., Raharjo W.W., Ariawan D., Triyono J., Kaavesina M. (2021). Epoxy resins thermosetting for mechanical engineering. Open Engineering (Vol. 11(1), pp. 797-814).
- Unnikrishnan K.P., Thachil E.T. Toughening of epoxy resins. Designed Monomers and Polymers (Vol. 9(2), pp. 129-152).
- Lou C., Liu X. (2018). Functional dendritic curing agent for epoxy resin: processing, mechanical performance and curing/toughening mechanism. Composites Part B: Engineering (Vol. 136, pp. 20-27).
- Sun Z., Xu L., Chen Z. (2019). Enhancing the mechanical and thermal properties of epoxy resin via blending with thermoplastic polysulfone. Polymers (Vol. 11(3), p. 461).
- Fernández Zapico G., Ohtake N., Akasaka H., Munoz-Guijosa J.M. (2019). Epoxy toughening through high pressure and shear rate preprocessing. Scientific Reports (Vol. 9(1), p. 17343).
- Farooq U., Teuwen J., Dransfeld C. (2020). Toughening of epoxy systems with interpenetrating polymer network (IPN): a review. Polymers (Vol. 12(9), p. 1908).
- Mohammad Nejad S., Srivastava R., Bellussi F.M., Chávez Thielemann H., Asinari P., Fasano M. (2021). Nanoscale thermal properties of carbon nanotubes/epoxy composites by atomistic simulations. International Journal of Thermal Sciences (Vol. 159, p. 106588).
- Wu S., Peng S., Wang C.H. (2018). Multifunctional polymer nanocomposites reinforced by aligned carbon nanomaterials. Polymers (Vol. 10(5), p. 542).
- Li L., Wang M., Wu X., Yi W., Xiao Q. (2021). Bio-based polyurethane nanocomposite thin coatings from two comparable POSS with eight same vertex groups for controlled release urea. Scientific Reports (Vol. 11(1), p. 9917).
- Li S., Lin Q., Cui C. (2016). The effect of core-shell particles on the mechanical performance of epoxy resins modified with hyperbranched polymers. Journal of Materials Research (Vol. 31(10), pp. 1393-1402).
- Wang J., Liu R., Jian X. (2016). Introduction to epoxy/thermoplastic blends. Handbook of Epoxy Blends, Springer International Publishing, Cham. (pp. 1-29).
- Pavlycheva E.A. (2021). Development of a polymer composition for obtaining materials and products with improved dielectric characteristics. International Journal of Applied and Fundamental Research (Vol.12, pp. 60-64).
- Pavlycheva E.A. (2020). Development of a protective polymer coating with high hydrophobic and adhesive properties. Engineering Bulletin of the Don. (Vol. 5, p. 33).
- Lobanov M.V., Gulyaev A.I., Babin A.N. (2016). Increasing the impact and crack resistance of epoxy reactoplastics and composites based on them using additives of thermoplastics as modifiers. High-molecular compounds. Series B (Vol. 58(1), pp. 3-15).
- Muthalif M.P.A., Choe Y. (2022). Adhesive and impact-peel strength improvement of epoxy resins modified with mono and diamine functionalized elastomers. Advances in Polymer Technology (pp. 1-9).
- Sprenger S. (2013). Epoxy resins modified with elastomers and surface-modified silica nanoparticles. Polymer (Vol. 54(18), pp. 4790-4797).
- Ammar Sh., Cheng Ch.H., Wonnie Ma I.A., Shahid B.B., Ramesh K., Ramesh S., Vengadaesvaran B. (2020). Effects of TiO2 nanoparticles on the overall performance and corrosion protection ability of neat epoxy and PDMS modified epoxy coating systems. Frontiers in Materials (Vol. 6, p. 19).
- Majeed A.H. (2018). Enforcement of epoxy with silica fume and carbon fiber. Tikrit Journal of Engineering Sciences (Vol. 25, pp. 74-77).
- Tkach E.V., Temirkanov R.I., Tkach S.A. (2021). A comprehensive study of modified concrete based on activated silica in conjunction with micro-reinforcing fiber to improve performance. Izvestiya Tomsk Polytechnic University. Georesource engineering (Vol. 332(5), pp. 215-226).
- Szewczak A., Szelag M. (2020). Physico-mechanical and rheological properties of epoxy adhesives modified by microsilica and sonication process. Materials (Vol. 13, pp. 20-25).
- Massana J., Reyes E., Bernal J., Leon N., Sanchez-Espinosa E. (2018). Influence of nano- and micro-silica additions on the durability of a high-performance self-compacting concrete. Construction and Building Materials (Vol.165, pp. 93-103).
- Kononova O.V., Smirnov A.O. (2017). Investigation of the features of the formation of the strength of quasi-self-compacting concrete with silica. Fundamental Research (Vol.7, pp. 327-331).
- Serekpayeva M.A., Kokayeva G.А., Niyazbekova R.K., Kardybai S. (2021). Investigation of the properties of composite materials based on epoxy resins with microsilica additives. Complex Use of Mineral Resources (Vol.3(318), p.63-70).
- GOST 31993-2013 (2014). Paint and varnish materials. Determination of the coating thickness. M.: Standartinform (p. 16).
- GOST 4647-2015 (2017). Plastics. The method of determining the impact strength by Sharpie. M.: Standartinform (p. 20).
- GOST 11262-2017 (2018). Plastics. The method of tensile testing. M.: Standartinform (p.19).
- GOST 9550-81 (2004). Plastics. Methods for determining the modulus of elasticity in tension, compression and bending. M.: Publishing House of Standards (p. 6).
- GOST 15140-78 (2009). Paint and varnish materials. Methods for determining adhesion. M.: Standartinform (p. 9).
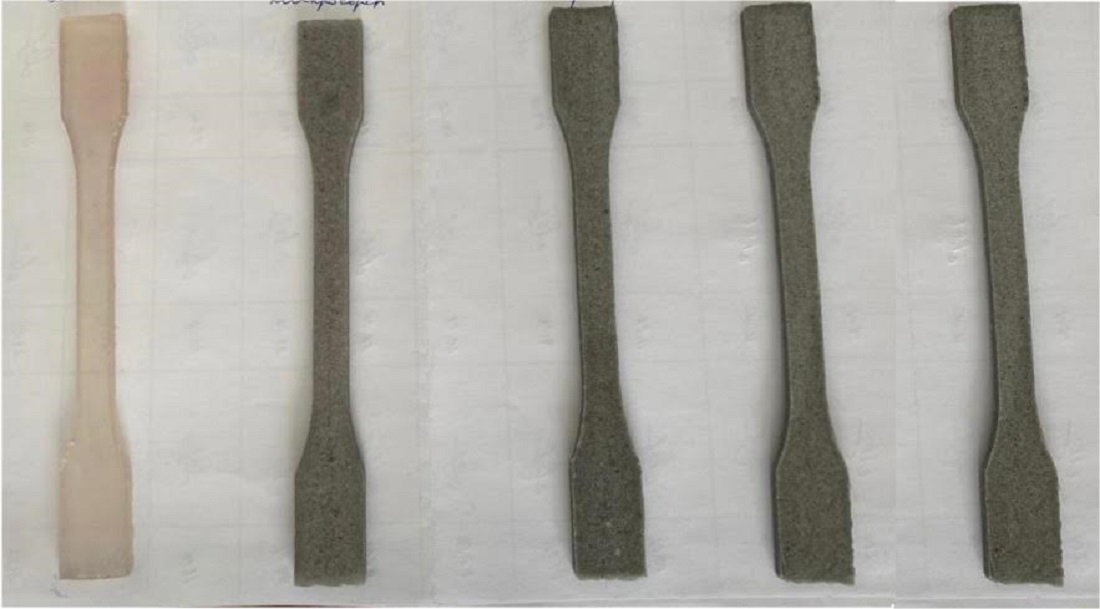
Downloads
Published
How to Cite
Issue
Section
License
Copyright (c) 2023 Gulnara Kokayeva, Rimma Niyazbekova, Mira Serekpayeva, Ainur Ibzhanova, Amirbek Bekeshev

This work is licensed under a Creative Commons Attribution 4.0 International License.
The consolidation and conditions for the transfer of copyright (identification of authorship) is carried out in the License Agreement. In particular, the authors reserve the right to the authorship of their manuscript and transfer the first publication of this work to the journal under the terms of the Creative Commons CC BY license. At the same time, they have the right to conclude on their own additional agreements concerning the non-exclusive distribution of the work in the form in which it was published by this journal, but provided that the link to the first publication of the article in this journal is preserved.
A license agreement is a document in which the author warrants that he/she owns all copyright for the work (manuscript, article, etc.).
The authors, signing the License Agreement with TECHNOLOGY CENTER PC, have all rights to the further use of their work, provided that they link to our edition in which the work was published.
According to the terms of the License Agreement, the Publisher TECHNOLOGY CENTER PC does not take away your copyrights and receives permission from the authors to use and dissemination of the publication through the world's scientific resources (own electronic resources, scientometric databases, repositories, libraries, etc.).
In the absence of a signed License Agreement or in the absence of this agreement of identifiers allowing to identify the identity of the author, the editors have no right to work with the manuscript.
It is important to remember that there is another type of agreement between authors and publishers – when copyright is transferred from the authors to the publisher. In this case, the authors lose ownership of their work and may not use it in any way.