Revealing the effect of changing the operating parameters of a double hydrostatic bearing on its characteristics
DOI:
https://doi.org/10.15587/1729-4061.2023.281936Keywords:
double bearing, bearing capacity, dynamic characteristics, non-stationary loading, motion trajectoryAbstract
The object of research is hydrostatic processes in sliding bearings with several layers of lubricant.
The task addressed was the influence of the structural and operational parameters of dual hydrostatic plain bearings on their static and dynamic characteristics. As a static characteristic, the bearing capacities of dual and conventional sleeve hydrostatic bearings were considered. When analyzing the dynamic characteristics, the amplitude-frequency characteristics were determined. They were obtained by calculation and as a result of experimental studies. When calculating the amplitude-frequency characteristics, the trajectory method was used. As external forces in the equations of motion of the rotor, hydrodynamic forces, the weight of the rotor, and its unbalance were considered.
Experimental determination of the trajectories of the rotor was carried out on a special bench.
It has been established that the bearing capacity of a double type bearing is approximately 1.75–1.85 times higher than the bearing capacity of a conventional sleeve bearing. The range of stable operation of the rotor on double-type bearings is approximately 1.4 times greater in comparison with the range of stable operation of the rotor on sleeve hydrostatic bearings. The vibration amplitudes in the resonance region for double bearings were approximately 1.5 times less than the rotor vibration amplitudes for sleeve bearings.
The results make it possible to recommend dual-type hydrostatic bearings for rotor bearings of nuclear power plants, in powerful aircraft engines with a gearbox, various types of pumps, and other power plant units. The derived theoretical dependences make it possible to carry out practical calculation of hydrostatic bearings of a double type
References
- Xu, H., Yang, J., Gao, L., An, Q. (2020). The influences of bump foil structure parameters on the static and dynamic characteristics of bump-type gas foil bearings. Proceedings of the Institution of Mechanical Engineers, Part J: Journal of Engineering Tribology, 234 (10), 1642–1657. doi: https://doi.org/10.1177/1350650120912609
- Hu, Z., Wang, Z., Huang, W., Wang, X. (2019). Supporting and friction properties of magnetic fluids bearings. Tribology International, 130, 334–338. doi: https://doi.org/10.1016/j.triboint.2018.10.006
- Xiang, G., Han, Y., He, T., Wang, J., Xiao, K., Li, J. (2020). Wear and fluid-solid-thermal transient coupled model for journal bearings. Applied Mathematical Modelling, 85, 19–45. doi: https://doi.org/10.1016/j.apm.2020.03.037
- Santos, I. (2018). Controllable Sliding Bearings and Controllable Lubrication Principles – An Overview. Lubricants, 6 (1), 16. doi: https://doi.org/10.3390/lubricants6010016
- EL-Said, A. KH., EL-Souhily, B. M., Crosby, W. A., EL-Gamal, H. A. (2017). The performance and stability of three-lobe journal bearing textured with micro protrusions. Alexandria Engineering Journal, 56 (4), 423–432. doi: https://doi.org/10.1016/j.aej.2017.08.003
- Summer, F., Bergmann, P., Grün, F. (2017). Damage Equivalent Test Methodologies as Design Elements for Journal Bearing Systems. Lubricants, 5 (4), 47. doi: https://doi.org/10.3390/lubricants5040047
- Zernin, M. V., Mishin, A. V., Rybkin, N. N., Shil’ko, S. V., Ryabchenko, T. V. (2017). Consideration of the multizone hydrodynamic friction, the misalignment of axes, and the contact compliance of a shaft and a bush of sliding bearings. Journal of Friction and Wear, 38 (3), 242–251. doi: https://doi.org/10.3103/s1068366617030163
- Zhang, J., Tan, A., Spikes, H. (2016). Effect of Base Oil Structure on Elastohydrodynamic Friction. Tribology Letters, 65 (1). doi: https://doi.org/10.1007/s11249-016-0791-7
- Villaverde, R. (2016). Base isolation with sliding hydromagnetic bearings: concept and feasibility study. Structure and Infrastructure Engineering, 13 (6), 709–721. doi: https://doi.org/10.1080/15732479.2016.1187634
- Polyakov, R., Savin, L., Fetisov, A. (2018). Analysis of the conditions for the occurrence of the effect of a minimum of friction in hybrid bearings based on the load separation principle. Proceedings of the Institution of Mechanical Engineers, Part J: Journal of Engineering Tribology, 233 (2), 271–280. doi: https://doi.org/10.1177/1350650118777143
- Schüler, E., Berner, O. (2021). Improvement of Tilting-Pad Journal Bearing Operating Characteristics by Application of Eddy Grooves. Lubricants, 9 (2), 18. doi: https://doi.org/10.3390/lubricants9020018
- Avishai, D., Morel, G. (2021). Experimental Investigation of Lubrication Regimes of a Water-Lubricated Bearing in the Propulsion Train of a Marine Vessel. Journal of Tribology, 143 (4). doi: https://doi.org/10.1115/1.4048382
- Amann, T., Chen, W., Baur, M., Kailer, A., Rühe, J. (2020). Entwicklung von galvanisch gekoppelten Gleitlagern zur Reduzierung von Reibung und Verschleiß. Forschung Im Ingenieurwesen, 84 (4), 315–322. doi: https://doi.org/10.1007/s10010-020-00416-z
- Gheisari, R., Lan, P., Polycarpou, A. A. (2020). Efficacy of surface microtexturing in enhancing the tribological performance of polymeric surfaces under starved lubricated conditions. Wear, 444–445, 203162. doi: https://doi.org/10.1016/j.wear.2019.203162
- Liu, Y., Zou, J., Deng, Y., Ji, H. (2020). Research on the seawater-lubricated sliding bearing of a novel buoyancy-regulating seawater pump considering the working depth. Australian Journal of Mechanical Engineering, 20 (2), 469–488. doi: https://doi.org/10.1080/14484846.2020.1716510
- Zhao, Y., Jianxi, Y. (2019). Influence of interface slip on the surface frictional force of texturing sliding bearing. Industrial Lubrication and Tribology, 72 (6), 735–742. doi: https://doi.org/10.1108/ilt-01-2018-0032
- Nazin, V. I. (2013). Theory of double radial bearing in gidrostatodinamicheskogo stationary external load. Aviatsionno-kosmicheskaya tekhnika i tekhnologiya, 8 (105), 160–166. Available at: http://nti.khai.edu:57772/csp/nauchportal/Arhiv/AKTT/2013/AKTT813/Nazin.pdf
- Nazin, V. I. (2014). Stand, pilot plant and method of experimental researches of hydrostatodynamic bearings of the doubled type. Aviatsionno-kosmicheskaya tekhnika i tekhnologiya, 8 (115), 100–103. Available at: http://nbuv.gov.ua/UJRN/aktit_2014_8_19
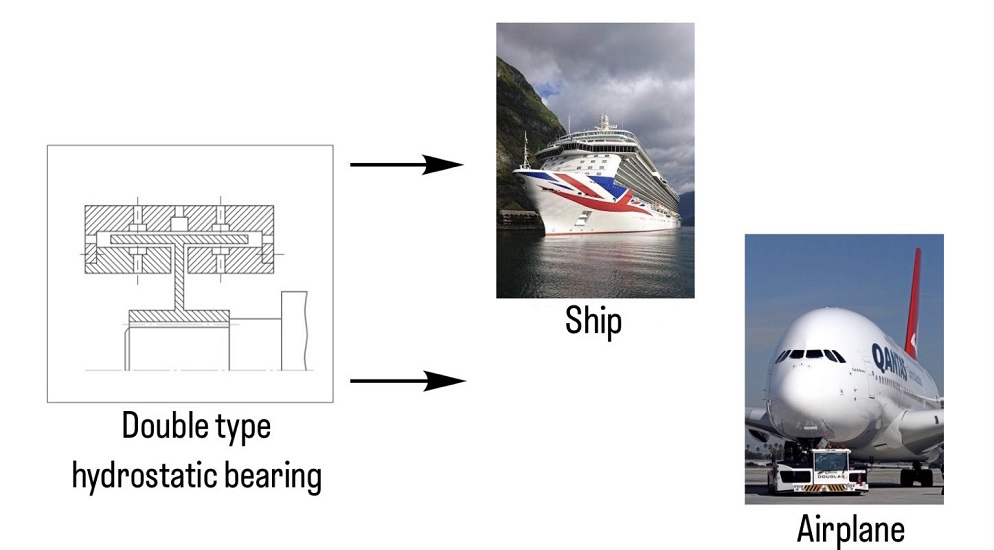
Downloads
Published
How to Cite
Issue
Section
License
Copyright (c) 2023 Vladimir Nazin

This work is licensed under a Creative Commons Attribution 4.0 International License.
The consolidation and conditions for the transfer of copyright (identification of authorship) is carried out in the License Agreement. In particular, the authors reserve the right to the authorship of their manuscript and transfer the first publication of this work to the journal under the terms of the Creative Commons CC BY license. At the same time, they have the right to conclude on their own additional agreements concerning the non-exclusive distribution of the work in the form in which it was published by this journal, but provided that the link to the first publication of the article in this journal is preserved.
A license agreement is a document in which the author warrants that he/she owns all copyright for the work (manuscript, article, etc.).
The authors, signing the License Agreement with TECHNOLOGY CENTER PC, have all rights to the further use of their work, provided that they link to our edition in which the work was published.
According to the terms of the License Agreement, the Publisher TECHNOLOGY CENTER PC does not take away your copyrights and receives permission from the authors to use and dissemination of the publication through the world's scientific resources (own electronic resources, scientometric databases, repositories, libraries, etc.).
In the absence of a signed License Agreement or in the absence of this agreement of identifiers allowing to identify the identity of the author, the editors have no right to work with the manuscript.
It is important to remember that there is another type of agreement between authors and publishers – when copyright is transferred from the authors to the publisher. In this case, the authors lose ownership of their work and may not use it in any way.