Розробка гофрованих металевих прокладок з алюмінію A1100
DOI:
https://doi.org/10.15587/1729-4061.2023.284502Ключові слова:
розробка прокладки, кінцево-елементний аналіз, гофрована металева прокладка, холодне формування, алюмінієві матеріали, випробування тиском водиАнотація
Гофровані металеві прокладки (ГМП), виготовлені з SUS304, були розроблені раніше, однак для оптимальної конструкції необхідний процес покриття з більш м’якого матеріалу. Процес нанесення покриття трудомісткий і дорогий. Це дослідження спрямоване на розробку ГМП з алюмінію шляхом аналізу моделювання та формування конструкції ГМП з алюмінію A1100. Оптимальна товщина CMG аналізується за допомогою ANSYS Finite Element Analysis (FEA). Контрольними змінними, які досліджуються, є площа контакту та контактна напруга. Незалежною змінною, яка досліджується, є товщина матеріалу ГМП. Потім за допомогою процесу холодного формування на основі оптимальної конструкції виготовляється алюмінієва прокладка. Контрольними змінними у випробуванні на витік є осьова сила та тиск води. Були також проведені експерименти для перевірки алюмінієвої прокладки на герметичність. Випробування на герметичність проводиться за допомогою випробування тиском води. Аналіз моделювання показав результати, які відповідають експериментальним тестам на витік. Результати моделювання FEA показують, що оптимальна товщина прокладки становить від 3 до 5 мм, причому 5 мм є оптимальною. Однак ГМП товщиною 4 і 5 мають однакові контактне напруження та площу контакту. Результати випробування на витік також показують схожість з результатами моделювання. Найкращі характеристики має ГМП товщиною 5 мм. Експериментальні результати показують, що ГМП з алюмінію A1100 підходить для використання в якості прокладки для запобігання витоку, він запобігає витоку при тиску рідини до 12 МПа та осьовому зусиллі 100 кН. Результати показують, що алюмінієва ГМП працює на одному рівні з SUS304 ГМП з покриттям нікелю або міді. Це дослідження дозволило розробити ГМП з алюмінію
Посилання
- Saeed, H. A., Izumi, S., Sakai, S., Haruyama, S., Nagawa, M., Noda, H. (2008). Development of New Metallic Gasket and its Optimum Design for Leakage Performance. Journal of Solid Mechanics and Materials Engineering, 2 (1), 105–114. doi: https://doi.org/10.1299/jmmp.2.105
- Karohika, I. M. G., Antara, I. N. G. (2019). The metal gasket sealing performance of bolted flanged with fem analysis. IOP Conference Series: Materials Science and Engineering, 539 (1), 012018. doi: https://doi.org/10.1088/1757-899x/539/1/012018
- Choiron, M. A., Haruyama, S., Kaminishi, K. (2011). Optimization of New Metal Gasket Design Based on Contact Width Involving Contact Stress Consideration. Applied Mechanics and Materials, 110-116, 4780–4787. doi: https://doi.org/10.4028/www.scientific.net/amm.110-116.4780
- Haruyama, S., Nurhadiyanto, D., Choiron, M. A., Kaminishi, K. (2013). Influence of surface roughness on leakage of new metal gasket. International Journal of Pressure Vessels and Piping, 111-112, 146–154. doi: https://doi.org/10.1016/j.ijpvp.2013.06.004
- Haruyama, S., Nurhadiyanto, D., Kaminishi, K. (2013). Contact Width Analysis of Corrugated Metal Gasket Based on Surface Roughness. Advanced Materials Research, 856, 92–97. doi: https://doi.org/10.4028/www.scientific.net/amr.856.92
- Haruyama, S., Choiron, Moch. A., Nurhadiyanto, D. (2019). Optimum Design of Laminated Corrugated Metal Gasket Using Computer Simulation. International Journal of Integrated Engineering, 11 (5). doi: https://doi.org/10.30880/ijie.2019.11.05.004
- Choiron, Moch. A., Purnowidodo, A. (2015). Sealing Performance of Thin Corrugated Metal Gasket. Applied Mechanics and Materials, 789-790, 246–250. doi: https://doi.org/10.4028/www.scientific.net/amm.789-790.246
- Nurhadiyanto, D., Mujiyono, Sutopo, Amri Ristadi, F. (2018). Simulation Analysis of 25A-Size Corrugated Metal Gasket Coated Copper to Increase Its Performance. IOP Conference Series: Materials Science and Engineering, 307, 012005. doi: https://doi.org/10.1088/1757-899x/307/1/012005
- Nurhadiyanto, D., Haruyama, S., Mujiyono, Sutopo, Ristadi, F. A. (2020). The performance of nickel and copper as coating materials for corrugated metal gaskets. Journal of Engineering Science and Technology, 15 (4), 2450–2463. Available at: https://jestec.taylors.edu.my/Vol%2015%20issue%204%20August%202020/15_4_23.pdf
- Nurhadiyanto, D., Haruyama, S., Mujiyono, M., Sutopo, S., Yunaidi, Y., Surahmanto, F. et al. (2021). Improved performance of corrugated metal gaskets in boiler’s piping system through multilayered coating. Eastern-European Journal of Enterprise Technologies, 6 (1 (114)), 13–20. doi: https://doi.org/10.15587/1729-4061.2021.245360
- Karohika, I. M. G., Antara, I. N. G., Budiana, I. M. D. (2019). Influence of dies type for gasket forming shape. IOP Conference Series: Materials Science and Engineering, 539 (1), 012019. doi: https://doi.org/10.1088/1757-899x/539/1/012019
- Gothivarekar, S., Coppieters, S., Van de Velde, A., Debruyne, D. (2020). Advanced FE model validation of cold-forming process using DIC: Air bending of high strength steel. International Journal of Material Forming, 13 (3), 409–421. doi: https://doi.org/10.1007/s12289-020-01536-1
- He, L., Lu, X., Zhu, X., Chen, Q. (2021). Influence of Structural Parameters of Shape Memory Alloy Corrugated Gaskets on the Contact Pressure of Bolted Flange Joints. Advances in Materials Science and Engineering, 2021, 1–19. doi: https://doi.org/10.1155/2021/5552569
- Jianjun, S., Chenbo, M., Jianhua, L., Qiuping, Y. (2018). A leakage channel model for sealing interface of mechanical face seals based on percolation theory. Tribology International, 118, 108–119. doi: https://doi.org/10.1016/j.triboint.2017.09.013
- Liu, Y., Du, H., Ren, X., Li, B., Qian, J., Yan, F. (2022). A Leakage Rate Model for Metal-to-Metal Seals Based on the Fractal Theory of Porous Medium. Aerospace, 9 (12), 779. doi: https://doi.org/10.3390/aerospace9120779
- Du, P., Lu, J., Tuo, J., Wang, X. (2019). Research on the Optimization Design of Metallic Gasket Based on DOE Methodology. IOP Conference Series: Materials Science and Engineering, 569 (3), 032027. doi: https://doi.org/10.1088/1757-899x/569/3/032027
- Zhan, Y., Lan, M., Zhu, X., Lu, X. (2022). Research on Prediction Models for the Compression-Resilience Performance of Corrugated Metal Gaskets With Residual Stress. Journal of Pressure Vessel Technology, 144 (5). doi: https://doi.org/10.1115/1.4053602
- JIS Z 2241. Metallic Material-Tensile testing-Method of test at room temperature. Japanese Standards Association. Available at: https://global.ihs.com/doc_detail.cfm?&item_s_key=00127867&item_key_date=770310&input_doc_number=JISZ2241&input_doc_title
- Materials Data Book (2019). Cambridge University Engineering Department. Available at: http://teaching.eng.cam.ac.uk/sites/teaching.eng.cam.ac.uk/files/Documents/Databooks/MATERIALS%20DATABOOK%20(2011)%20version%20for%20Moodle.pdf
- Karohika, I. M. G., Artha, I. G. A. G. K., Azkandri, M. H. A. G. (2023). An overview of the corrugated metal gasket. AIP Conference Proceedings. doi: https://doi.org/10.1063/5.0115569
- Karohika, I. M. G., Antara, I. N. G. (2019). Gasket Process Parameter in Metal Forming. IOP Conference Series: Earth and Environmental Science, 248, 012044. doi: https://doi.org/10.1088/1755-1315/248/1/012044
- JIS B 2404:2006. Dimensions of gaskets for use with pipe flanges. Japanese Standards Association. Available at: https://infostore.saiglobal.com/en-us/standards/jis-b-2404-2006-622826_saig_jsa_jsa_2891706/
- JIS B 2220:2004. Steel Pipe Flanges. Japanese Standards Association. Available at: https://infostore.saiglobal.com/en-us/standards/jis-b-2220-2004-633314_saig_jsa_jsa_1452418/
- Tatarkanov, A., Aleksandrov, I., Mihaylov, M., Muranov, A. (2021). Development of algorithm for automated assessment of the tightness of contact sealing connections of isolation valves. Bulletin of Bryansk State Technical University, 10, 27–37. doi: https://doi.org/10.30987/1999-8775-2021-10-27-37
- Bhosale, R. S., Kumbhar, P. P., Mahajan, K. S., Yachkal, A. K., Katarkar, A., (2017). Study on Leak Testing Methods. International Journal for Scientific Research & Development, 5 (1), 1618–1621. Available at: https://www.researchgate.net/publication/323219717_Study_on_Leak_Testing_Methods#fullTextFileContent
- Feng, X., Gu, B., Zhang, P. (2018). Prediction of Leakage Rates Through Sealing Connections with Metallic Gaskets. IOP Conference Series: Earth and Environmental Science, 199, 032090. doi: https://doi.org/10.1088/1755-1315/199/3/032090
- Karohika, I. M. G., Haruyama, S., Choiron, Moch. A., Nurhadiyanto, D., Antara, I. N. G. et al. (2020). An Approach to Optimize the Corrugated Metal Gasket Design Using Taguchi Method. International Journal on Advanced Science, Engineering and Information Technology, 10 (6), 2435. doi: https://doi.org/10.18517/ijaseit.10.6.12992
- Karohika, I. M. G., Haruyama, S. (2022). Analysis of three-layer gasket performance affected by flange surface. EUREKA: Physics and Engineering, 4, 57–66. doi: https://doi.org/10.21303/2461-4262.2022.002290
- Karohika, I. M. G., Haruyama, S. (2022). The real contact width evaluation of a three-layer metal gasket. SINERGI, 26 (3), 311. doi: https://doi.org/10.22441/sinergi.2022.3.006
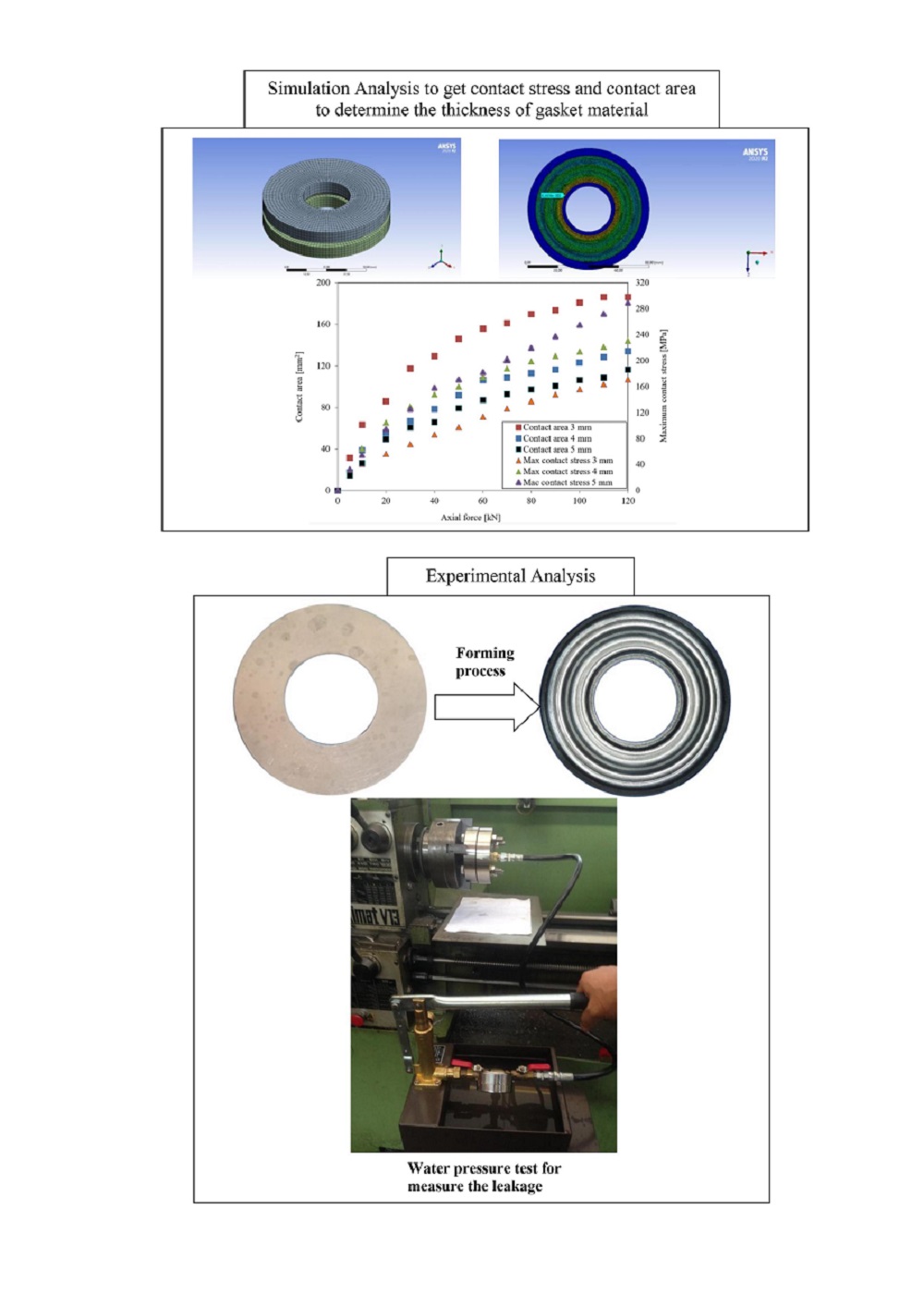
##submission.downloads##
Опубліковано
Як цитувати
Номер
Розділ
Ліцензія
Авторське право (c) 2023 Didik Nurhadiyanto, Mujiyono, Febrianto Amri Ristadi, Ardani Ahsanul Fakhri, Gewa Ardeva, Muhammad Iqbal Kusnantoro, Shigeyuki Haruyama, Isti Yunita, Alexander Panichkin

Ця робота ліцензується відповідно до Creative Commons Attribution 4.0 International License.
Закріплення та умови передачі авторських прав (ідентифікація авторства) здійснюється у Ліцензійному договорі. Зокрема, автори залишають за собою право на авторство свого рукопису та передають журналу право першої публікації цієї роботи на умовах ліцензії Creative Commons CC BY. При цьому вони мають право укладати самостійно додаткові угоди, що стосуються неексклюзивного поширення роботи у тому вигляді, в якому вона була опублікована цим журналом, але за умови збереження посилання на першу публікацію статті в цьому журналі.
Ліцензійний договір – це документ, в якому автор гарантує, що володіє усіма авторськими правами на твір (рукопис, статтю, тощо).
Автори, підписуючи Ліцензійний договір з ПП «ТЕХНОЛОГІЧНИЙ ЦЕНТР», мають усі права на подальше використання свого твору за умови посилання на наше видання, в якому твір опублікований. Відповідно до умов Ліцензійного договору, Видавець ПП «ТЕХНОЛОГІЧНИЙ ЦЕНТР» не забирає ваші авторські права та отримує від авторів дозвіл на використання та розповсюдження публікації через світові наукові ресурси (власні електронні ресурси, наукометричні бази даних, репозитарії, бібліотеки тощо).
За відсутності підписаного Ліцензійного договору або за відсутністю вказаних в цьому договорі ідентифікаторів, що дають змогу ідентифікувати особу автора, редакція не має права працювати з рукописом.
Важливо пам’ятати, що існує і інший тип угоди між авторами та видавцями – коли авторські права передаються від авторів до видавця. В такому разі автори втрачають права власності на свій твір та не можуть його використовувати в будь-який спосіб.