Investigating cavity formation in an electric arc zone during out-of-furnace processing of steel
DOI:
https://doi.org/10.15587/1729-4061.2023.284884Keywords:
physical modeling, «ladle-furnace» installation, graphitized hollow electrode, geometric parameters of the cavityAbstract
The object of this study is the interaction zone between a graphitized hollow electrode (GHE) and a metal bath on the «ladle-furnace» installation.
The regularities of the formation of the geometric parameters of the hole were established for the purpose of further evaluation of the heat exchange under the electrode in the arc combustion zone under different operating conditions of the «ladle-furnace» installation.
An experimental methodology was devised, and a laboratory setup was built for physical simulation on a cold model. The values of the geometric parameters of the cavity formed by the electric arc discharge in the sub-electrode zone were calculated. In particular, the area of the curved surface of the cavity is about 0.2 m2 at a depth of 40 mm. The regularities of formation of the geometry of the cavity during gas injection through the GHE channel have been established, in particular with regard to the area and depth of the cavity. Thus, with a gas consumption of 3–20 m3/h and a slag cover height of 100 mm, the area reaches 0.28–0.5 m2, while the depth of the cavity ranged from 5 cm to 19 cm, respectively. Rational flow rates of gas supplied through the channel of the graphitized hollow electrode were established, which for a slag cover of 100 mm are 3–6 m3/h and for a slag cover of 200 mm – 6–10 m3/h.
The peculiarities of the formation of a metal cavity in the sub-electrode zone under the conditions of gas supply through the channel of a graphitized hollow electrode during out-of-furnace processing of steel at the «ladle-furnace» installation were investigated.
The patterns of the formation of the geometry of the cavity in the arc combustion zone, which were obtained using cold modeling, could subsequently make it possible to perform calculations of heat transfer from the electric arc discharge to the metal bath. That will also make it possible to determine the share of heat absorbed by slag and metal under the conditions of using a conventional electrode, and a hollow one with gas supply through its channel during out-of-furnace processing of steel at the «ladle-furnace» installation
References
- Zhan, D. P., Zhang, H. S., Jiang, Z. H., Gong, W., Li, H. B., Chen, Z. P. (2011). Influence of Hollow Electrode Ar-CO2 Injection on Carbon Content in Ladle Furnace. Advanced Materials Research, 250-253, 3864–3867. doi: https://doi.org/10.4028/www.scientific.net/amr.250-253.3864
- Zhan, D. P., Zhang, H. S., Jiang, Z. H., Gong, W., Chen, Z. P. (2011). Influence of Electrode Argon-Hydrogen Co-Injection on Carbon Content in a Alternating Current Ladle Furnace. Advanced Materials Research, 239-242, 2361–2364. doi: https://doi.org/10.4028/www.scientific.net/amr.239-242.2361
- Bigelow, L. K., Flemings, M. C. (1975). Sulfide inclusions in steel. Metallurgical Transactions B, 6 (2), 275–283. doi: https://doi.org/10.1007/bf02913570
- Payandeh, Y., Soltanieh, M. (2007). Oxide Inclusions at Different Steps of Steel Production. Journal of Iron and Steel Research International, 14 (5), 39–46. doi: https://doi.org/10.1016/s1006-706x(07)60072-7
- Okhotskiy, V. B. (2010). Non-metallic inclusions in steel in the process of deoxidation. Theory. Metallurgical and Mining Industry, 2 (4), 260–261. Available at: https://www.metaljournal.com.ua/assets/Uploads/attachments/Okhotskiy261.pdf
- Gubenko, S. I., Parusov, V. V., Derevyanchenko, I. V. (2005). Nemetallicheskie vklyucheniya v stali. Dnepropetrovsk: ART-PRESS, 536.
- Pribulová, A., Futáš, P., Bureš, R. (2007). Influence of steel blowing with inert gas on steel cleanness. Acta Metallurgica Slovaca. 13 (4), 133–136.
- Hudzieczek, Z., Michalek, K., Gryc, K. (2010). Methodology development and first results of transfer processes results between metal and slag. In Theory and Practice of steel production and processing. Ostrava: TANGER.
- Strasäk, P. (2009). Numerical Modelling of liquid steel behaviour in the ladle during the argon blowing through the three hole lance. Technical report for V§B-TU Ostrava, FMME, Department of Metallurgy, TechSoft Eng.
- Michalek, K., Tkadleôkovâ, M., Gryc, K., Klus, P., Hudzieczeka, Z., Sikoraa, V., Strasâk, P. (2011). Optimization of argon blowing conditions for the steel homogenization in a ladle using numerical modelling. Metal.
- Jardón Pérez, L. E., Amaro-Villeda, A., Conejo, A. N., González-Rivera, C., Ramírez-Argáez, M. A. (2017). Optimizing gas stirred ladles by physical modeling and PIV measurements. Materials and Manufacturing Processes, 33 (8), 882–890. doi: https://doi.org/10.1080/10426914.2017.1401722
- Haida, O., Brimacombe, J. K. (1985). Physical-model study of the effect of gas kinetic energy in injection refining processes. Transactions of the Iron and Steel Institute of Japan, 25 (1), 14–20. doi: https://doi.org/10.2355/isijinternational1966.25.14
- Conejo, A. N., Mishra, R., Mazumdar, D. (2019). Effects of Nozzle Radial Position, Separation Angle, and Gas Flow Partitioning on the Mixing, Eye Area, and Wall Shear Stress in Ladles Fitted with Dual Plugs. Metallurgical and Materials Transactions B, 50 (3), 1490–1502. doi: https://doi.org/10.1007/s11663-019-01546-8
- Nizyaev, K. G., Dusha, V. M., Kernitskiy, V. V. (2002). Osobennosti nagreva stali nezavisimoy elektricheskoy dugoy. Metallurgicheskaya i gornorudnaya promyshlennost', 7, 147–149.
- Yachnikov, I. M., Portnova, I. V., Bystrov, M. V. (2018). Modelirovanie teplovogo sostoyaniya grafitirovannogo elektroda pri podache gaza v osevoy kanal. Kongress Staleplavil'schikov: Magnitogorskiy gosudarstvennyy tekhnicheskiy universitet im. G.I. Nosova, 180–186.
- Egorov, A. V. (1985). Elektroplavil'nye pechi chernoy metallurgii. Moscow: Metallurgiya, 280.
- Shtapura, E. V., Zhavoronkov, Yu. I., Boychenko, B.M., Nizyaev, K. G., Kharchenko, S. V. (2008). Modelirovanie produvki zhidkoy stali v kovshe neytral'nym gazom. Novosti nauki Pridneprov'ya, 1, 112–114.
- Kazantsev, I. G. (1952). Issledovanie dinamiki gazoobraznoy strui vtekayuschey v zhidkost'. Termicheskaya i plasticheskaya obrabotka metallov: Sb. nauch. tr. Zhdanovskogo metallurgicheskogo instituta. V. 2. Moscow: Metallurgizdat, 56–68.
- Efimov, L. M. (1957). Trudy nauchno-tekhnicheskogo obschestva chernoy metallurgii. Materialy vsesoyuznogo soveschaniya staleplavil'schikov. Vol. XVIII, Ch. 1. Moscow: Metallurgiya, 40–57.
- Baptizmanskiy, V. I., Schedrin, G. A., Prosvirin, K. S. (1975). Razmery reaktsionnoy zony pri produvke metalla kislorodom sverkhu. Izv. VUZov. Chernaya metallurgiya, 10, 44–48.
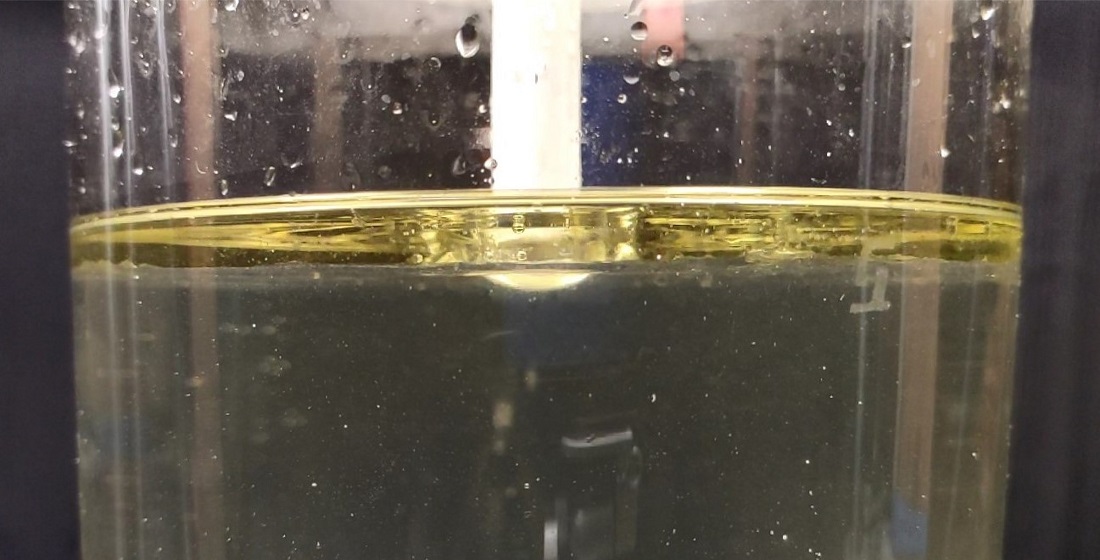
Downloads
Published
How to Cite
Issue
Section
License
Copyright (c) 2023 Volodymyr Ruban, Oleksandr Stoianov, Kostiantyn Niziaiev, Yevhen Synehin, Svitlana Zhuravlova, Khrystyna Malii

This work is licensed under a Creative Commons Attribution 4.0 International License.
The consolidation and conditions for the transfer of copyright (identification of authorship) is carried out in the License Agreement. In particular, the authors reserve the right to the authorship of their manuscript and transfer the first publication of this work to the journal under the terms of the Creative Commons CC BY license. At the same time, they have the right to conclude on their own additional agreements concerning the non-exclusive distribution of the work in the form in which it was published by this journal, but provided that the link to the first publication of the article in this journal is preserved.
A license agreement is a document in which the author warrants that he/she owns all copyright for the work (manuscript, article, etc.).
The authors, signing the License Agreement with TECHNOLOGY CENTER PC, have all rights to the further use of their work, provided that they link to our edition in which the work was published.
According to the terms of the License Agreement, the Publisher TECHNOLOGY CENTER PC does not take away your copyrights and receives permission from the authors to use and dissemination of the publication through the world's scientific resources (own electronic resources, scientometric databases, repositories, libraries, etc.).
In the absence of a signed License Agreement or in the absence of this agreement of identifiers allowing to identify the identity of the author, the editors have no right to work with the manuscript.
It is important to remember that there is another type of agreement between authors and publishers – when copyright is transferred from the authors to the publisher. In this case, the authors lose ownership of their work and may not use it in any way.