Забезпечення сталості процесу обробки кінцевими фрезами
DOI:
https://doi.org/10.15587/1729-4061.2023.287009Ключові слова:
кінцеве фрезерування, сталість процесу різання, ідентифікація динамічних параметрів обробної системи, діаграма сталостіАнотація
Представлено новий підхід до забезпечення сталості процесу кінцевого фрезерування, за рахунок безвібраційних режимів різання, які визначаються з діаграми сталості динамічної обробної системи. Розроблена прикладна програма автоматичного розрахунку діаграми сталості в координатах «швидкість шпинделя фрези – подача», яка є інструментом технолога-програміста при проєктуванні управляючих програм для верстатів з числовим програмним управлінням. Математична модель, що покладена в основу прикладної програми, представляє динамічну обробну систему як одномасову з двома степенями свободи, що охоплена негативними зворотними зв’язками за напрямом двох координат. Оброблення за слідом представлене у вигляді позитивних зворотних зв’язків з функцією запізнення в кожному. Математична модель представлена у формі змінних стану, що дозволяє застосовувати чисельні методи моделювання для визначення як перехідних, так і частотних характеристик. В розробленій програмі передбачений окремий модуль автоматичного проєктування діаграми сталості, алгоритм функціонування якого використовує ознаки розташування діаграми Найквіста на комплексній площині. Оскільки функціонування розробленої програми вимагає апріорну інформацію про динамічні параметри обробної системи, представлена методика їх експериментальної ідентифікації. Жорсткості обробної системи за двома координатами визначалися за допомогою динамометра, а частотні характеристики – за імпульсною характеристикою, яка була отримана ударним молотком. Результати досліджень були підтверджені експериментально, як комп’ютерним моделюванням, так і фрезеруванням на верстаті, і можуть бути рекомендовані для призначення режиму різання при кінцевому фрезеруванні
Посилання
- Quintana, G., Ciurana, J. (2011). Chatter in machining processes: A review. International Journal of Machine Tools and Manufacture, 51 (5), 363–376. doi: https://doi.org/10.1016/j.ijmachtools.2011.01.001
- Yue, C., Gao, H., Liu, X., Liang, S. Y., Wang, L. (2019). A review of chatter vibration research in milling. Chinese Journal of Aeronautics, 32 (2), 215–242. doi: https://doi.org/10.1016/j.cja.2018.11.007
- Altintas, Y. (2012). Manufacturing Automation. Cambridge: Cambridge University Press. doi: https://doi.org/10.1017/cbo9780511843723
- Koh, M. H. (2012). Identification of system parameters for end milling force simulation with tool and workpiece compliance. University of New Hampshire, 761. Available at: https://scholars.unh.edu/thesis/761/
- Xia, Y., Wan, Y., Luo, X., Liu, Z., Song, Q. (2021). An improved numerical integration method to predict the milling stability based on the Lagrange interpolation scheme. The International Journal of Advanced Manufacturing Technology, 116 (7-8), 2111–2123. doi: https://doi.org/10.1007/s00170-021-07311-z
- Petrakov, Y., Sikailo, M. (2022). Simulation modeling of 2.5D milling dynamics by end mills. Bulletin of the National Technical University «KhPI» Series: New Solutions in Modern Technologies, 2 (12), 17–24. doi: https://doi.org/10.20998/2413-4295.2022.02.03
- Sreenivasa Rao, A., Venkata Rao, K. (2017). A Study on Machining Characteristics in Milling of Ti-6Al-4V using Experimental and Finite Element Analysis. International Journal of Civil Engineering and Technology, 8 (7), 457–469. Available at: http://iaeme.com/Home/issue/IJCIET?Volume=8&Issue=7
- Li, H. Z., Zhang, W. B., Li, X. P. (2001). Modelling of cutting forces in helical end milling using a predictive machining theory. International Journal of Mechanical Sciences, 43 (8), 1711–1730. doi: https://doi.org/10.1016/s0020-7403(01)00020-0
- Stephenson, D. A., Agapiou, J. S. (2018). Metal Cutting Theory and Practice. CRC Press. doi: https://doi.org/10.1201/9781315373119
- Quintana, G., Ciurana, J., Teixidor, D. (2008). A new experimental methodology for identification of stability lobes diagram in milling operations. International Journal of Machine Tools and Manufacture, 48 (15), 1637–1645. doi: https://doi.org/10.1016/j.ijmachtools.2008.07.006
- Petrakov, Y., Danylchenko, M. (2022). A time-frequency approach to ensuring stability of machining by turning. Eastern-European Journal of Enterprise Technologies, 6 (2 (120)), 85–92. doi: https://doi.org/10.15587/1729-4061.2022.268637
- Liang, S. Y. (2000). Manufacturing processes and equipment. Machining Science and Technology, 4 (2), 317–318. doi: https://doi.org/10.1080/10940340008945713
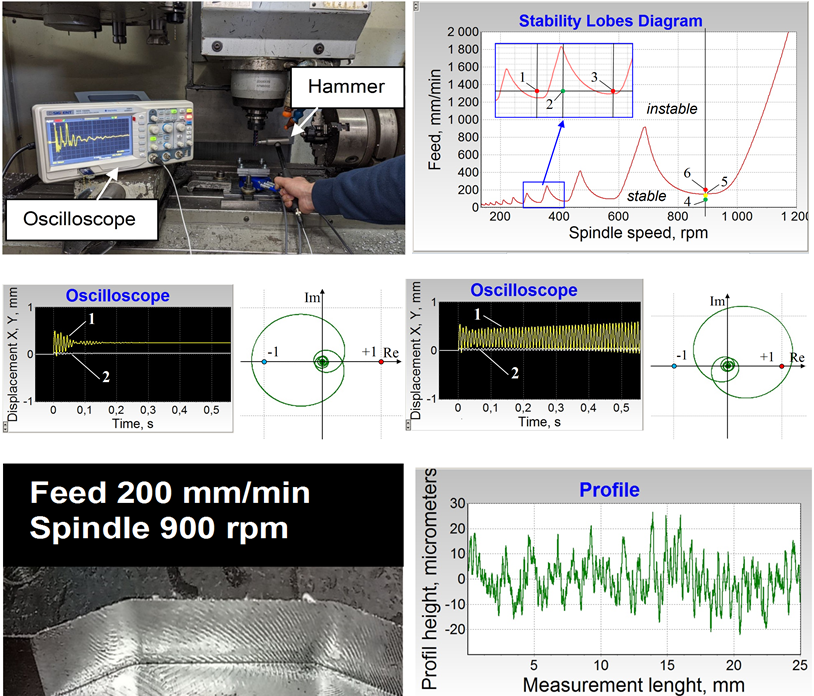
##submission.downloads##
Опубліковано
Як цитувати
Номер
Розділ
Ліцензія
Авторське право (c) 2023 Yuri Petrakov, Olexander Ohrimenko, Maxim Sikailo

Ця робота ліцензується відповідно до Creative Commons Attribution 4.0 International License.
Закріплення та умови передачі авторських прав (ідентифікація авторства) здійснюється у Ліцензійному договорі. Зокрема, автори залишають за собою право на авторство свого рукопису та передають журналу право першої публікації цієї роботи на умовах ліцензії Creative Commons CC BY. При цьому вони мають право укладати самостійно додаткові угоди, що стосуються неексклюзивного поширення роботи у тому вигляді, в якому вона була опублікована цим журналом, але за умови збереження посилання на першу публікацію статті в цьому журналі.
Ліцензійний договір – це документ, в якому автор гарантує, що володіє усіма авторськими правами на твір (рукопис, статтю, тощо).
Автори, підписуючи Ліцензійний договір з ПП «ТЕХНОЛОГІЧНИЙ ЦЕНТР», мають усі права на подальше використання свого твору за умови посилання на наше видання, в якому твір опублікований. Відповідно до умов Ліцензійного договору, Видавець ПП «ТЕХНОЛОГІЧНИЙ ЦЕНТР» не забирає ваші авторські права та отримує від авторів дозвіл на використання та розповсюдження публікації через світові наукові ресурси (власні електронні ресурси, наукометричні бази даних, репозитарії, бібліотеки тощо).
За відсутності підписаного Ліцензійного договору або за відсутністю вказаних в цьому договорі ідентифікаторів, що дають змогу ідентифікувати особу автора, редакція не має права працювати з рукописом.
Важливо пам’ятати, що існує і інший тип угоди між авторами та видавцями – коли авторські права передаються від авторів до видавця. В такому разі автори втрачають права власності на свій твір та не можуть його використовувати в будь-який спосіб.