Mathematical modeling of the melt flow in the cone-ring channel of the extruder matrix
DOI:
https://doi.org/10.15587/1729-4061.2024.290692Keywords:
mathematical model, FlowVision, combined feed, cone-ring channel, extruder matrixAbstract
The peculiarity of the work is to develop a mathematical model of the melt flow in the cone-annular channel of the extruder die, which will allow you to choose the optimal geometric shape of the annular channel, as well as the angular rotation speed of the extruder screw. The object of the study is the cone-ring channel of the extruder matrix.
To solve the three-dimensional problem of turbulent and laminar unsteady motion, the FlowVision software package was used, which allows solving partial differential equations using the finite volume method. The correct choice of the geometric shape of the annular gap made it possible to change the molecular structure of the product by creating a maximum pressure value. The optimally selected angular rotation speed of the extruder screw made it possible to carry out deep melting of the product due to the conversion of the mechanical energy of the screw into thermal energy.
In the process of designing the forming of the cone-ring channel, the three volumes of the changing geometry of the stamp were selected, at the borders of the transition of which extreme points were observed. Deviations between the analyzed and experimental values of velocity and pressure were found in the limits of 9–12 % and 17–22 %, respectively.
Based on the analysis of the obtained results of modeling, the optimal geometric shape of the annular gap and the recommended angular rotation speed of the extruder screw were revealed.
The mathematical model proposed formed the basis of the developed design of the six-zone extruder. In the extruder, the geometric characteristics of the screw (variable pitch of the turns) were substantiated and selected, which provide the maximum effect of dissipation, i.e. autogenous mode of operation
References
- Alimkulov, Zh. S., Veliamov, M. T., Fazylova, K. N., Shauliyeva, K. T., Bektursunova, M. J. (2020). Optimization mathematical models of raw material crushing in the production of compound feeds based on enriching feed concentrate. Bulletin of the South Ural State University. Ser. Food and Biotechnology, 8 (2), 29–36.
- Borovsky, A. Yu., Kizatova, M., Sultanova, M., Abdrakhmanov, H. (2019). Mathematical foundations of the technological process of obtaining combined feeds. Actual problems of modernity, 3, 155–159.
- Enayati, S., Ayoub, A. (2018). Applying Mathematical Optimization To Efficiently Make Better Decisions for Extrusion Technology: State-of-the-Art and Opportunities. Biomass Extrusion and Reaction Technologies: Principles to Practices and Future Potential, 243–260. https://doi.org/10.1021/bk-2018-1304.ch013
- Malik, M., Kalyon, D. M., Golba, J. C. (2014). Simulation of Co-Rotating Twin Screw Extrusion Process Subject to Pressure-Dependent Wall Slip at Barrel and Screw Surfaces: 3D FEM Analysis for Combinations of Forward- and Reverse-Conveying Screw Elements. International Polymer Processing, 29 (1), 51–62. https://doi.org/10.3139/217.2802
- Wu, K., Sun, Y., Peng, B., Ding, W., Wang, S. (2013). Modeling and experiment on rotary extrusion torque in ring-die pelleting process. Nongye Gongcheng Xuebao/Transactions of the Chinese Society of Agricultural Engineering, 29 (24), 33–39. https://doi.org/10.3969/j.issn.1002-6819.2013.24.005
- Chaturvedi, E., Rajput, N. S., Upadhyaya, S., Pandey, P. K. (2017). Experimental Study and Mathematical Modeling for Extrusion using High Density Polyethylene. Materials Today: Proceedings, 4 (2), 1670–1676. https://doi.org/10.1016/j.matpr.2017.02.006
- Nahemiah, D. (2016). Application of Response Surface Methodology (RSM) for the Production and Optimization of Extruded Instant Porridge from Broken Rice Fractions Blended with Cowpea. International Journal of Nutrition and Food Sciences, 5 (2), 105. https://doi.org/10.11648/j.ijnfs.20160502.13
- Atukuri, J., Odong, B. B., Muyonga, J. H. (2019). Multi‐response optimization of extrusion conditions of grain amaranth flour by response surface methodology. Food Science & Nutrition, 7 (12), 4147–4162. https://doi.org/10.1002/fsn3.1284
- Kizatova, M. Y., Sultanova, M. Zh., Borovsky, A. Y., Muslimov, N. Zh., Nokusheva, Z. A., Aitzhanov, Y. S. (2020). Mathematical planning of a multi-factor experiment and optimization of the feed extrusion process. IOP Conference Series: Materials Science and Engineering, 994, 012022. https://doi.org/10.1088/1757-899x/994/1/012022
- Schittny, A., Ogawa, H., Huwyler, J., Puchkov, M. (2018). A combined mathematical model linking the formation of amorphous solid dispersions with hot-melt-extrusion process parameters. European Journal of Pharmaceutics and Biopharmaceutics, 132, 127–145. https://doi.org/10.1016/j.ejpb.2018.09.011
- Ostrikov, A., Ospanov, A., Vasilenko, V., Muslimov, N., Timurbekova, A., Jumabekova, G. (2019). Melt flow of biopolymer through the cavities of an extruder die: Mathematical modelling. Mathematical Biosciences and Engineering, 16 (4), 2875–2905. https://doi.org/10.3934/mbe.2019142
- Adekola, K. A. (2016). Engineering Review Food Extrusion Technology and Its Applications. Journal of Food Science and Engineering, 6 (3). https://doi.org/10.17265/2159-5828/2016.03.005
- Mushtruk, M., Gudzenko, M., Palamarchuk, I., Vasyliv, V., Slobodyanyuk, N., Kuts, A. et al. (2020). Mathematical modeling of the oil extrusion process with pre-grinding of raw materials in a twin-screw extruder. Potravinarstvo Slovak Journal of Food Sciences, 14, 937–944. https://doi.org/10.5219/1436
- Kushnir, V., Gavrilov, N., Kim, S. (2017). Experimental Studies on Grain Material Extruding Process. Procedia Engineering, 206, 1611–1617. https://doi.org/10.1016/j.proeng.2017.10.686
- Lela, B., Musa, A., Zovko, O. (2014). Model-based controlling of extrusion process. The International Journal of Advanced Manufacturing Technology, 74 (9-12), 1267–1273. https://doi.org/10.1007/s00170-014-6054-6
- Gomes, K. S., Berwian, G. F., Batistella, V. M. C., Bender, L. E., Reinehr, C. O., Colla, L. M. (2022). Nutritional and Technological Aspects of the Production of Proteic Extruded Snacks Added of Novel Raw Materials. Food and Bioprocess Technology, 16 (2), 247–267. https://doi.org/10.1007/s11947-022-02887-0
- Xu, M., Zhang, X., Zhang, Y., Wang, J., Li, J., Hu, Y. et al. (2023). Effect of screw speed, temperature and moisture on physicochemical properties of corn gluten meal extrudate. Journal of the Science of Food and Agriculture, 103 (12), 5782–5790. https://doi.org/10.1002/jsfa.12649
- Okunola, A. A., Dottie, E. P., Moses, O. I., Adekanye, T. A., Okonkwo, C. E., Kaveh, M. et al. (2023). Development and Process Optimization of a Ready-to-Eat Snack from Rice-Cowpea Composite by a Twin Extruder. Processes, 11 (7), 2159. https://doi.org/10.3390/pr11072159
- Altan, A., Yağci, S. (2023). Physicochemical characteristics and structural changes of fermented faba bean extrudates prepared by twin-screw extrusion. Food Chemistry, 411, 135502. https://doi.org/10.1016/j.foodchem.2023.135502
- Bachurina, M., Kazakov, A., Trufanova, N. (2014). Mathematical modelling of stratified flow of polymer melts in an axisymmetric formulation. PNRPU Mechanics Bulletin, 2, 102–124. https://doi.org/10.15593/perm.mech/2014.2.05
- Ostrikov, A. N., Afanasiev, V. A., Frolova, L. N., Nesterov, D. A., Sizikov, K. A. (2021). Pat. RF No. 2750158. Extruder.
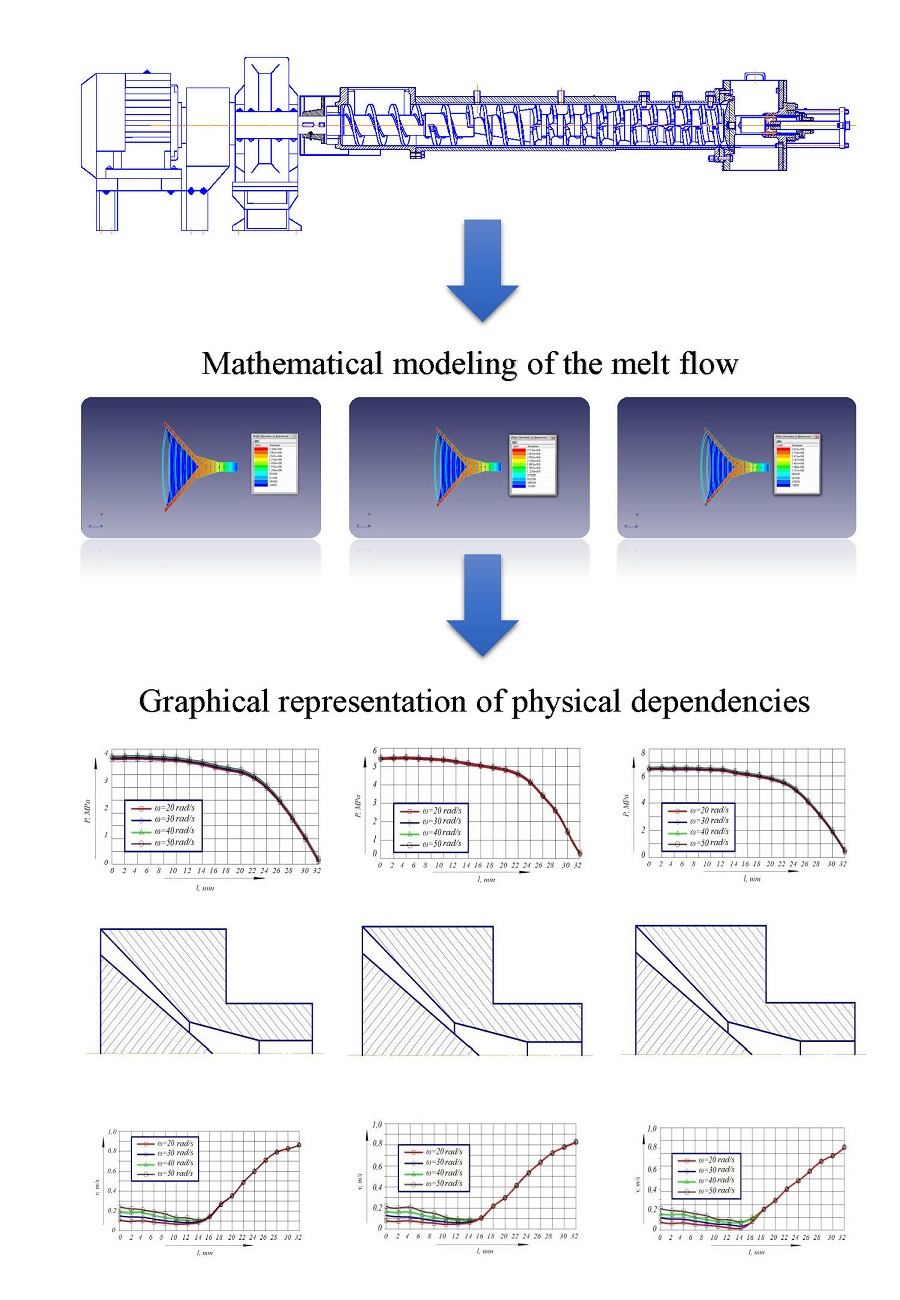
Downloads
Published
How to Cite
Issue
Section
License
Copyright (c) 2024 Abdymanap Ospanov, Aigul Timurbekova, Dulat Zhalelov

This work is licensed under a Creative Commons Attribution 4.0 International License.
The consolidation and conditions for the transfer of copyright (identification of authorship) is carried out in the License Agreement. In particular, the authors reserve the right to the authorship of their manuscript and transfer the first publication of this work to the journal under the terms of the Creative Commons CC BY license. At the same time, they have the right to conclude on their own additional agreements concerning the non-exclusive distribution of the work in the form in which it was published by this journal, but provided that the link to the first publication of the article in this journal is preserved.
A license agreement is a document in which the author warrants that he/she owns all copyright for the work (manuscript, article, etc.).
The authors, signing the License Agreement with TECHNOLOGY CENTER PC, have all rights to the further use of their work, provided that they link to our edition in which the work was published.
According to the terms of the License Agreement, the Publisher TECHNOLOGY CENTER PC does not take away your copyrights and receives permission from the authors to use and dissemination of the publication through the world's scientific resources (own electronic resources, scientometric databases, repositories, libraries, etc.).
In the absence of a signed License Agreement or in the absence of this agreement of identifiers allowing to identify the identity of the author, the editors have no right to work with the manuscript.
It is important to remember that there is another type of agreement between authors and publishers – when copyright is transferred from the authors to the publisher. In this case, the authors lose ownership of their work and may not use it in any way.