Identifying regularities of fluid throttling of an inertial hydrodynamic installation
DOI:
https://doi.org/10.15587/1729-4061.2023.292522Keywords:
process water, pressure, angular velocity, throttle nozzles, fluid flow, hydrodynamic heaterAbstract
The article presents the results of experimental research conducted on a specially designed setup for pressurizing various types of fluids through throttle orifices. To determine the optimal operating mode of the thermal system, throttle nozzles of different diameters, specifically 1.5 mm, 2 mm, and 3 mm, were utilized.
One of the primary advantages of vortex heaters is their high heat exchange efficiency. This is attributed to the vortical motions and turbulence generated within the device, which promote more vigorous fluid mixing, thus enhancing heat transfer efficiency.
However, vortex heaters do have certain drawbacks. Vortical components may experience wear and require regular maintenance and replacement.
Subsequently, during the course of experimental work, an alternative inertia-based hydrodynamic system for heating heat carriers was developed and installed in a laboratory experimental facility. The research focus was on technical water. The results indicated that the static pre-pressure generated by the supply of water from the water main into the system decreases as the rotor's angular velocity increases. Experimental investigations demonstrated that rotor rotation leads to a redistribution of flow characteristics in throttle orifices for both static and dynamic inertial fluid discharge. Given that any static column of liquid results in level flow through throttle orifices, their flow static parameters were established.
Furthermore, the research revealed that with the increase in rotor angular velocity, the fluid pressure at the throttle orifices rises, while the share of fluid discharge from the initial static pressure decreases in the overall fluid flow
References
- Ruonan, W., Bin, L., Haodong, L. (2021). Experimental results and analysis of throttling refrigeration with ternary mixed refrigerant. E3S Web of Conferences, 236, 01008. doi: https://doi.org/10.1051/e3sconf/202123601008
- Guo, G., Lu, K., Xu, S., Yuan, J., Bai, T., Yang, K., He, Z. (2023). Effects of in-nozzle liquid fuel vortex cavitation on characteristics of flow and spray: Numerical research. International Communications in Heat and Mass Transfer, 148, 107040. doi: https://doi.org/10.1016/j.icheatmasstransfer.2023.107040
- Alia, M. A. K. (2010). Hydraulic Domestic Heating by Throttling. Engineering, 02 (06), 461–465. doi: https://doi.org/10.4236/eng.2010.26060
- Polášek, T., Hružík, L., Bureček, A., Ledvoň, M. (2022). Experimental Analysis of Flow Through Throttle Valve During Gaseous Cavitation. MATEC Web of Conferences, 369, 02008. doi: https://doi.org/10.1051/matecconf/202236902008
- Vasina, M., Hruzik, L., Burecek, A. (2018). Energy and Dynamic Properties of Hydraulic Systems. Tehnicki Vjesnik - Technical Gazette, 25, 382–390. doi: https://doi.org/10.17559/tv-20131209081056
- Mokhammad, A. A., Khorosh, I. A., Titov, M. A., Kulikova, N. P. (2015). The calculation of the throttle device heating working fluid of hydraulic drive having a temperature dependence. Vestn. Kras GAU, 12, 38–44.
- Shumilov, I. (2016). Fluid Temperature of Aero Hydraulic Systems. Machines and Plants: Design and Exploiting, 16 (02). doi: https://doi.org/10.7463/aplts.0216.0837432
- Marinin, M. G., Mosalev, S. M., Naumov, V. I., Sysa, V. P. (2007). Pat. No. RU2357161C1. Throttle Type Heat Generator. declareted: 06.11.2007; published: 27.05.2009.
- Saleh, H., Hashim, I. (2013). Unsteady heat transfer in an enclosure with a time-periodic rotating cylinder. Heat Transfer Research, 44 (2), 145–161. doi: https://doi.org/10.1615/heattransres.2012005450
- Alpeissov, Y., Iskakov, R., Issenov, S., Ukenova, А. (2022). Obtaining a formula describing the interaction of fine particles with an expanding gas flow in a fluid layer. Eastern-European Journal of Enterprise Technologies, 2 (1 (116)), 87–97. doi: https://doi.org/10.15587/1729-4061.2022.255258
- Maiorova, K., Vorobiov, I., Andrieiev, O., Lupkin, B., Sikulskiy, V. (2022). Forming the geometric accuracy and roughness of holes when drilling aircraft structures made from polymeric composite materials. Eastern-European Journal of Enterprise Technologies, 2 (1 (116)), 71–80. doi: https://doi.org/10.15587/1729-4061.2022.254555
- Aghakashi, V., Saidi, M. H. (2018). Turbulent decaying swirling flow in a pipe. Heat Transfer Research, 49 (16), 1559–1585. doi: https://doi.org/10.1615/heattransres.2018021519
- Oshanov, Y., Ovcharov, M., Nussupbekov, B., Stoev, M. (2020). The influence of the main properties of the liquid on the temperature indicators of the inertial heat generator. Bulgarian Chemical Communications, 52, 188–191. Available at: http://www.bcc.bas.bg/BCC_Volumes/Volume_52_Special_A_2020/BCC-52-A.pdf
- Bashta, T. M. (1972). Engineering Hydraulics. Moscow: Mashinostroenie.
- Nussupbekov, B., Oshanov, Y., Ovcharov, M., Mussenova, E., Ospanova, D., Bolatbekova, M. (2022). Development and creation of a hydrodynamic liquid heating unit. Eastern-European Journal of Enterprise Technologies, 5 (8 (119)), 62–69. doi: https://doi.org/10.15587/1729-4061.2022.264227
- Oshanov, Y. Z., Ovcharov, M. S., Nusupbekov, B. R. (2022). Influence of inertial forces on the flow rate velocity of fluid outflow through the throttle bores of the rotor. Heat Transfer Research, 53 (14), 1–8. doi: https://doi.org/10.1615/heattransres.2022038753
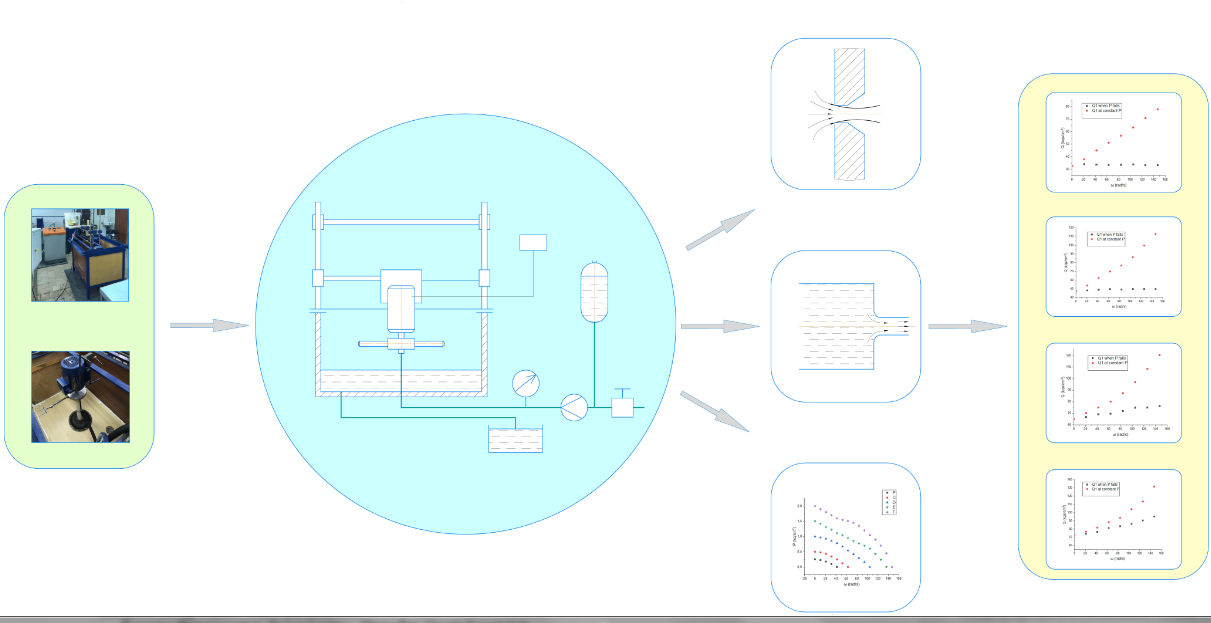
Downloads
Published
How to Cite
Issue
Section
License
Copyright (c) 2023 Bekbolat Nussupbekov, Yerlan Oshanov, Michael Ovcharov, Bayan Kutum, Мoldir Duisenbayeva, Aitkul Kongyrbayeva

This work is licensed under a Creative Commons Attribution 4.0 International License.
The consolidation and conditions for the transfer of copyright (identification of authorship) is carried out in the License Agreement. In particular, the authors reserve the right to the authorship of their manuscript and transfer the first publication of this work to the journal under the terms of the Creative Commons CC BY license. At the same time, they have the right to conclude on their own additional agreements concerning the non-exclusive distribution of the work in the form in which it was published by this journal, but provided that the link to the first publication of the article in this journal is preserved.
A license agreement is a document in which the author warrants that he/she owns all copyright for the work (manuscript, article, etc.).
The authors, signing the License Agreement with TECHNOLOGY CENTER PC, have all rights to the further use of their work, provided that they link to our edition in which the work was published.
According to the terms of the License Agreement, the Publisher TECHNOLOGY CENTER PC does not take away your copyrights and receives permission from the authors to use and dissemination of the publication through the world's scientific resources (own electronic resources, scientometric databases, repositories, libraries, etc.).
In the absence of a signed License Agreement or in the absence of this agreement of identifiers allowing to identify the identity of the author, the editors have no right to work with the manuscript.
It is important to remember that there is another type of agreement between authors and publishers – when copyright is transferred from the authors to the publisher. In this case, the authors lose ownership of their work and may not use it in any way.