Ідентифікація впливу умов зварювального середовища на вплив пару та якість зварювання на газових металах дугового зварювання алюмінієвого сплаву AA5083-H112
DOI:
https://doi.org/10.15587/1729-4061.2024.296784Ключові слова:
газове дугове зварювання, AA5083, середовище зварювання, вплив диму, межа міцності, енергія ударуАнотація
У цьому дослідженні досліджувалися механічні властивості зварного з’єднання та вплив зварювального диму, пов’язані з газовим дуговим зварюванням алюмінію AA5083-H112 у 27 різних умовах зварювального приміщення. Ці умови складаються з коливань температури, а також швидкості вітру на вході та вихлопі. Температура коливається від 19 °C, 27 °C і 35 °C. Швидкість як на вході, так і на випуску змінюється на 0 м/с, 3,1 м/с і 5,5 м/с. Експериментальні результати підкреслюють виражений вплив цих факторів як на якість зварювання, так і на вплив диму на зварника. Примітно, що швидкість вітру надходження є найбільш критичним фактором, який значно впливає на 47,68 % міцності зварного з’єднання на розрив. Температура є найменш критичним фактором з 12,02 % внеску. Проте температура стала найбільш критичним фактором для енергії удару зварного з’єднання з 54,89 % внеску, тоді як швидкість вихлопного вітру стала найменшою з 3,89 %. Моніторинг якості повітря підкреслює важливість оптимальної конфігурації впускного та витяжного вентиляторів для ефективного зменшення впливу диму. Усі досліджені умови середовища зварювального приміщення вважаються безпечними для зварювальника, оскільки вони не перевищують порогове граничне значення, за винятком умов, коли у зварювальному приміщенні не вистачає циркуляції повітря на вході та витяжці зі швидкістю вітру 0 м/с. Визначені оптимальні умови зварювального приміщення забезпечують температуру 27 °C, швидкість впускного та витяжного вітру 0 м/с та 3,1 м/с відповідно. Ця умова не тільки забезпечує встановлені стандарти якості зварювальних швів, але й забезпечує дотримання норм щодо впливу диму. Це дослідження дає цінну інформацію щодо оптимізації середовища зварювального приміщення, щоб одночасно підтримувати якість зварювання та гарантувати добробут зварювальників
Посилання
- Gou, G., Zhang, M., Chen, H., Chen, J., Li, P., Yang, Y. P. (2015). Effect of humidity on porosity, microstructure, and fatigue strength of A7N01S-T5 aluminum alloy welded joints in high-speed trains. Materials & Design, 85, 309–317. https://doi.org/10.1016/j.matdes.2015.06.177
- Wang, C. G., Liu, Y., Wang, X. M., Gou, G. Q., Chen, H. (2014). Effects of Environment Temperatures on the Microstructures and Mechanical Properties for Welding Joints of A5083-H111 Alloy. Advanced Materials Research, 936, 1701–1706. https://doi.org/10.4028/www.scientific.net/amr.936.1701
- Kuk, J.-M., Jang, K.-C., Lee, D.-G., Kim, I.-S. (2004). Effect of shielding gas composition on low temperature toughness of Al5083–O gas metal arc welds. Science and Technology of Welding and Joining, 9 (6), 519–524. https://doi.org/10.1179/136217104225021607
- Sabau, A. S., Viswanathan, S. (2002). Microporosity prediction in aluminum alloy castings. Metallurgical and Materials Transactions B, 33 (2), 243–255. https://doi.org/10.1007/s11663-002-0009-2
- Suzuki, R., Sasakura, S., Yokota, Y., Sato, T., Shigemori, Y., Uenaka, A. et al. (2016). Study of wind-toughness of metal arc welding with reference to multi-pass weld metal quality. Welding International, 31 (1), 17–27. https://doi.org/10.1080/09507116.2016.1223188
- Huang, L., Hua, X., Wu, D., Jiang, Z., Ye, Y. (2019). A study on the metallurgical and mechanical properties of a GMAW-welded Al-Mg alloy with different plate thicknesses. Journal of Manufacturing Processes, 37, 438–445. https://doi.org/10.1016/j.jmapro.2018.12.017
- Jang, K. C., Lee, D. G., Kuk, J. M., Kim, I. S. (2005). Welding and environmental test condition effect in weldability and strength of Al alloy. Journal of Materials Processing Technology, 164–165, 1038–1045. https://doi.org/10.1016/j.jmatprotec.2005.02.193
- Prokic-Cvetkovic, R., Kastelec-Macura, S., Milosavljevic, A., Popovic, O., Burzic, M. (2010). The effect of shielding gas composition on the toughness and crack growth parameters of AlMg4,5Mn weld metals. Journal of Mining and Metallurgy, Section B: Metallurgy, 46 (2), 193–202. https://doi.org/10.2298/jmmb1002193p
- Han, Q., Viswanathan, S. (2002). Hydrogen evolution during directional solidification and its effect on porosity formation in aluminum alloys. Metallurgical and Materials Transactions A, 33 (7), 2067–2072. https://doi.org/10.1007/s11661-002-0038-0
- Flynn, M. R., Susi, P. (2012). Local Exhaust Ventilation for the Control of Welding Fumes in the Construction Industry—A Literature Review. The Annals of Occupational Hygiene, 56 (7), 764–776. https://doi.org/10.1093/annhyg/mes018
- Dueck, M. E., Rafiee, A., Mino, J., Nair, S. G., Kamravaei, S., Pei, L., Quémerais, B. (2021). Welding Fume Exposure and Health Risk Assessment in a Cohort of Apprentice Welders. Annals of Work Exposures and Health, 65 (7), 775–788. https://doi.org/10.1093/annweh/wxab016
- Pourhassan, B., Beigzadeh, Z., Nasirzadeh, N., Karimi, A. (2023). Application of Multiple Occupational Health Risk Assessment Models for Metal Fumes in Welding Process. Biological Trace Element Research, 202 (3), 811–823. https://doi.org/10.1007/s12011-023-03717-w
- Chinakhov, D. A., Vorobyev, A. V., Grigorieva, E. G., Mayorova, E. I. (2015). Study of Wind Velocity Impact upon the Quality of Shielding and upon the Thermal Processes under MAG Welding. Applied Mechanics and Materials, 770, 253–257. https://doi.org/10.4028/www.scientific.net/amm.770.253
- Lee, M.-H., McClellan, W. J., Candela, J., Andrews, D., Biswas, P. (2006). Reduction of nanoparticle exposure to welding aerosols by modification of the ventilation system in a workplace. Journal of Nanoparticle Research, 9 (1), 127–136. https://doi.org/10.1007/s11051-006-9181-7
- Maslak, M., Pazdanowski, M., Stankiewicz, M., Wassilkowska, A., Zajdel, P., Zielina, M. (2023). Impact Fracture Surfaces as the Indicators of Structural Steel Post-Fire Susceptibility to Brittle Cracking. Materials, 16 (8), 3281. https://doi.org/10.3390/ma16083281
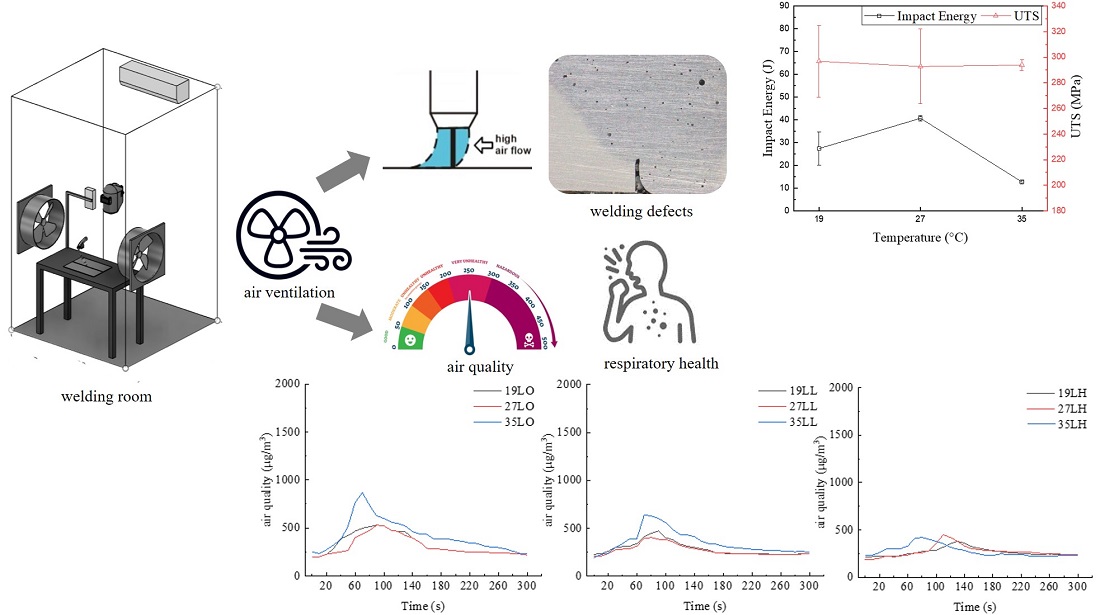
##submission.downloads##
Опубліковано
Як цитувати
Номер
Розділ
Ліцензія
Авторське право (c) 2024 Triyono, Anton Harseno, Nurul Muhayat

Ця робота ліцензується відповідно до Creative Commons Attribution 4.0 International License.
Закріплення та умови передачі авторських прав (ідентифікація авторства) здійснюється у Ліцензійному договорі. Зокрема, автори залишають за собою право на авторство свого рукопису та передають журналу право першої публікації цієї роботи на умовах ліцензії Creative Commons CC BY. При цьому вони мають право укладати самостійно додаткові угоди, що стосуються неексклюзивного поширення роботи у тому вигляді, в якому вона була опублікована цим журналом, але за умови збереження посилання на першу публікацію статті в цьому журналі.
Ліцензійний договір – це документ, в якому автор гарантує, що володіє усіма авторськими правами на твір (рукопис, статтю, тощо).
Автори, підписуючи Ліцензійний договір з ПП «ТЕХНОЛОГІЧНИЙ ЦЕНТР», мають усі права на подальше використання свого твору за умови посилання на наше видання, в якому твір опублікований. Відповідно до умов Ліцензійного договору, Видавець ПП «ТЕХНОЛОГІЧНИЙ ЦЕНТР» не забирає ваші авторські права та отримує від авторів дозвіл на використання та розповсюдження публікації через світові наукові ресурси (власні електронні ресурси, наукометричні бази даних, репозитарії, бібліотеки тощо).
За відсутності підписаного Ліцензійного договору або за відсутністю вказаних в цьому договорі ідентифікаторів, що дають змогу ідентифікувати особу автора, редакція не має права працювати з рукописом.
Важливо пам’ятати, що існує і інший тип угоди між авторами та видавцями – коли авторські права передаються від авторів до видавця. В такому разі автори втрачають права власності на свій твір та не можуть його використовувати в будь-який спосіб.