Implementing surface treatment and adhesive variations for bonded joints between composite gfrp and aluminum at 200 °C
DOI:
https://doi.org/10.15587/1729-4061.2024.297904Keywords:
GFRP, Aluminum, surface treatment, joint, roughness, adhesive, high temperature, strengthAbstract
Bonding dissimilar materials, specifically Glass Fiber Reinforced Polymer (GFRP) and Aluminum 6061 T651, at elevated temperatures, such as in fire accidents is challenging, where structural integrity and reliability are critical. We studied how surface roughness treatment affects the joint strength of three common adhesives in aircraft (Click Bond CB394-43, Loctite A9396, A9394) at 200 °C. The GFRP, composed of Gurit Prime 37 epoxy resin and E-Glass 7781 fibers produced through vacuum infusion with dimensions following ASTM D5868 standards, was lap shear tested with 2 mm/s stroke. Findings showed a substantial enhancement in joint strength due to surface treatment, sanding with 100-grid sandpaper for 20 seconds in parallel with the fiber direction, for all adhesives. A9396, A9394, and CB394-43 exhibited remarkable improvements of 1091.67 %, 45.92 %, and 30.09 %, respectively. The strain at break showed significant increases of 51.61 %, 121.95 %, and 100 %, respectively. Both surface-treated and untreated A9394 samples showed the highest strength among the adhesives. A9396 exhibited lower strength than CB394-43 without surface treatment, but it outperformed when surface-treated, highlighting its response to surface modification. Adhesive viscosity influences penetration on material surfaces, with A9396 being stiffer than the other adhesives. The analysis of ISO 4287 Ra values revealed that surface treatment led to increased roughness on the Aluminum surface while reducing roughness on the GFRP surface. These results offer valuable insights for optimizing GFRP-Aluminum bonding under elevated temperature conditions. Adjusting surface roughness significantly improves the interaction between Aluminum and GFRP with adhesives, resulting in enhanced joint strength. This knowledge can be applied in various engineering applications, particularly in industries where the performance and reliability of bonded joints are critical under high-temperature environments
Supporting Agency
- The study was conducted in the laboratory of the National Research and Innovation Agency (BRIN).
References
- Burshukova, G., Kanazhanov, A., Abuova, R., Joldassov, A. (2023). Analysis of Using Damping Alloys to Improve Vibration and Strength Characteristics in the Automotive Industry. Evergreen, 10 (2), 742–751. https://doi.org/10.5109/6792824
- Chandra, A., Yadav, A., Singh, S. (2023). Optimisation of Machining Parameters for CNC Milling of Fibre Reinforced Polymers. Evergreen, 10 (2), 765–773. https://doi.org/10.5109/6792826
- Gupta, M. K., Singhal, V., Rajput, N. S. (2022). Applications and Challenges of Carbon-fibres reinforced Composites: A Review. Evergreen, 9 (3), 682–693. https://doi.org/10.5109/4843099
- Rout, D., Nayak, R. K., Praharaj, S. (2021). Aerospace and vehicle industry. Handbook of Polymer Nanocomposites for Industrial Applications, 399–417. https://doi.org/10.1016/b978-0-12-821497-8.00013-7
- Sakib, Md. N., Asif Iqba, A. (2021). Epoxy Based Nanocomposite Material for Automotive Application- A Short Review. International Journal of Automotive and Mechanical Engineering, 18 (3). https://doi.org/10.15282/ijame.18.3.2021.24.0701
- Jawaid, M., Siengchin, S. (2019). Hybrid Composites: A Versatile Materials for Future. Applied Science and Engineering Progress, 12 (4). https://doi.org/10.14416/j.asep.2019.09.002
- Cui, X., Tian, L., Wang, D. S., Dong, J. P. (2021). Summary of thermosetting composite material welding. Journal of Physics: Conference Series, 1765, 012021. https://doi.org/10.1088/1742-6596/1765/1/012021
- Maggiore, S., Banea, M. D., Stagnaro, P., Luciano, G. (2021). A Review of Structural Adhesive Joints in Hybrid Joining Processes. Polymers, 13 (22), 3961. https://doi.org/10.3390/polym13223961
- Fiore, V., Alagna, F., Di Bella, G., Valenza, A. (2013). On the mechanical behavior of BFRP to aluminum AA6086 mixed joints. Composites Part B: Engineering, 48, 79–87. https://doi.org/10.1016/j.compositesb.2012.12.009
- Pohlit, D. J., Dillard, D. A., Jacob, G. C., Starbuck, J. M. (2008). Evaluating the Rate-Dependent Fracture Toughness of an Automotive Adhesive. The Journal of Adhesion, 84 (2), 143–163. https://doi.org/10.1080/00218460801952825
- Marques, E. A. S., da Silva, L. F. M., Banea, M. D Carbas, R. J. C. (2014). Adhesive Joints for Low- and High-Temperature Use: An Overview. The Journal of Adhesion, 91 (7), 556–585. https://doi.org/10.1080/00218464.2014.943395
- F M da Silva, L., D Adams, R. (2007). Techniques to reduce the peel stresses in adhesive joints with composites. International Journal of Adhesion and Adhesives, 27 (3), 227–235. https://doi.org/10.1016/j.ijadhadh.2006.04.001
- Papakonstantinou, C. G., Balaguru, P., Lyon, R. E. (2001). Comparative study of high temperature composites. Composites Part B: Engineering, 32 (8), 637–649. https://doi.org/10.1016/s1359-8368(01)00042-7
- Tang, S., Hu, C. (2017). Design, Preparation and Properties of Carbon Fiber Reinforced Ultra-High Temperature Ceramic Composites for Aerospace Applications: A Review. Journal of Materials Science & Technology, 33 (2), 117–130. https://doi.org/10.1016/j.jmst.2016.08.004
- Na, J., Mu, W., Qin, G., Tan, W., Pu, L. (2018). Effect of temperature on the mechanical properties of adhesively bonded basalt FRP-aluminum alloy joints in the automotive industry. International Journal of Adhesion and Adhesives, 85, 138–148. https://doi.org/10.1016/j.ijadhadh.2018.05.027
- Kwon, D.-J., Kim, J.-H., Kim, Y.-J., Kim, J.-J., Park, S.-M., Kwon, I.-J. et al. (2019). Comparison of interfacial adhesion of hybrid materials of aluminum/carbon fiber reinforced epoxy composites with different surface roughness. Composites Part B: Engineering, 170, 11–18. https://doi.org/10.1016/j.compositesb.2019.04.022
- Denti, L., Sola, A. (2019). On the Effectiveness of Different Surface Finishing Techniques on A357.0 Parts Produced by Laser-Based Powder Bed Fusion: Surface Roughness and Fatigue Strength. Metals, 9 (12), 1284. https://doi.org/10.3390/met9121284
- Buckwalter, C. Q., Pederson, L. R., McVay, G. L. (1982). The effects of surface area to solution volume ratio and surface roughness on glass leaching. Journal of Non-Crystalline Solids, 49 (1-3), 397–412. https://doi.org/10.1016/0022-3093(82)90135-1
- Nasreen, A., Shaker, K., Nawab, Y. (2021). Effect of surface treatments on metal–composite adhesive bonding for high-performance structures: an overview. Composite Interfaces, 28 (12), 1221–1256. https://doi.org/10.1080/09276440.2020.1870192
- LOCTITE EA 9394 AERO Epoxy Paste Adhesive (KNOWN AS Hysol EA 9394). Technical Process Bulletin. Available at: https://www.heatcon.com/wp-content/uploads/2015/08/HCS2407-141_Henkel-Resin-Kit-LOCTITE-EA-9394-AERO.pdf
- LOCTITE EA 9396 AERO Epoxy Paste Adhesive (KNOWN AS Hysol EA 9396). Technical Process Bulletin. Available at: https://www.aero-consultants.ch/view/data/3285/Produkte/Henkel%20Adhesive/LOCTITE%20EA%209396%20AERO.pdf
- CB394-43 - CB394 43ml High-Temperature Epoxy Adhesive Cartridge. Clik Bond. Available at: https://www.clickbond.com/product-detail/adhesives/cb394-43ml-epoxy-adhesive-cartridge
- Awaja, F., Gilbert, M., Kelly, G., Fox, B., Pigram, P. J. (2009). Adhesion of polymers. Progress in Polymer Science, 34 (9), 948–968. https://doi.org/10.1016/j.progpolymsci.2009.04.007
- Average Roughness basics. Michigan Metrology. Available at: https://michmet.com/average-roughness-basics/
- ISO, 4287: Geometrical Product Specifications (GPS)-Surface Texture: Profile Method. Terms, Definitions and Surface Texture Parameters.
- Gadelmawla, E. S., Koura, M. M., Maksoud, T. M. A., Elewa, I. M., Soliman, H. H. (2002). Roughness parameters. Journal of Materials Processing Technology, 123 (1), 133–145. https://doi.org/10.1016/s0924-0136(02)00060-2
- Guo, L., Liu, J., Xia, H., Li, X., Zhang, X., Yang, H. (2021). Effects of surface treatment and adhesive thickness on the shear strength of precision bonded joints. Polymer Testing, 94, 107063. https://doi.org/10.1016/j.polymertesting.2021.107063
- Boutar, Y., Naïmi, S., Mezlini, S., Ali, M. B. S. (2016). Effect of surface treatment on the shear strength of aluminium adhesive single-lap joints for automotive applications. International Journal of Adhesion and Adhesives, 67, 38–43. https://doi.org/10.1016/j.ijadhadh.2015.12.023
- Kim, J. K., Kim, H. S., Lee, D. G. (2003). Investigation of optimal surface treatments for carbon/epoxy composite adhesive joints. Journal of Adhesion Science and Technology, 17 (3), 329–352. https://doi.org/10.1163/156856103762864651
- Uehara, K., Sakurai, M. (2002). Bonding strength of adhesives and surface roughness of joined parts. Journal of Materials Processing Technology, 127 (2), 178–181. https://doi.org/10.1016/s0924-0136(02)00122-x
- Budhe, S., Ghumatkar, A., Birajdar, N., Banea, M. D. (2015). Effect of surface roughness using different adherend materials on the adhesive bond strength. Applied Adhesion Science, 3 (1). https://doi.org/10.1186/s40563-015-0050-4
- Golru, S. S., Attar, M. M., Ramezanzadeh, B. (2015). Effects of different surface cleaning procedures on the superficial morphology and the adhesive strength of epoxy coating on aluminium alloy 1050. Progress in Organic Coatings, 87, 52–60. https://doi.org/10.1016/j.porgcoat.2015.05.005
- Sharma, A., Chawla, H., Srinivas, K. (2023). Prediction of Surface Roughness of Mild Steel finished with Viscoelastic Magnetic Abrasive Medium. Evergreen, 10 (2), 1061–1067. https://doi.org/10.5109/6793663
- Sheikh Md. Fadzullah, S. H., Nasaruddin, M. M., Mustafa, Z., Rahman, W. A. W. A., Omar, G., Salim, M. A., Mansor, M. R. (2020). The Effect of Chemical Surface Treatment on Mechanical Performance of Electrically Conductive Adhesives. Evergreen, 7 (3), 444–451. https://doi.org/10.5109/4068625
- Sanghvi, M. R., Tambare, O. H., More, A. P. (2022). Performance of various fillers in adhesives applications: a review. Polymer Bulletin, 79 (12), 10491–10553. https://doi.org/10.1007/s00289-021-04022-z
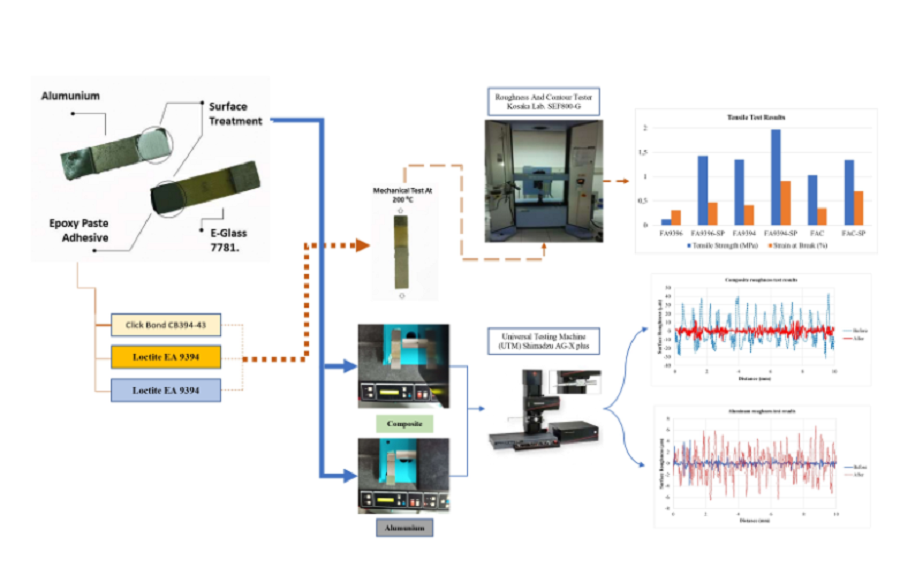
Downloads
Published
How to Cite
Issue
Section
License
Copyright (c) 2024 Herry Purnomo, Muhammad Johan Rifa’i, Purwoko, David Natanael Vicarneltor, Mahfud Ibadi, Muhamad Hananuputra Setianto, Maulana Yudanto, Ara Gradiniar Rizkyta

This work is licensed under a Creative Commons Attribution 4.0 International License.
The consolidation and conditions for the transfer of copyright (identification of authorship) is carried out in the License Agreement. In particular, the authors reserve the right to the authorship of their manuscript and transfer the first publication of this work to the journal under the terms of the Creative Commons CC BY license. At the same time, they have the right to conclude on their own additional agreements concerning the non-exclusive distribution of the work in the form in which it was published by this journal, but provided that the link to the first publication of the article in this journal is preserved.
A license agreement is a document in which the author warrants that he/she owns all copyright for the work (manuscript, article, etc.).
The authors, signing the License Agreement with TECHNOLOGY CENTER PC, have all rights to the further use of their work, provided that they link to our edition in which the work was published.
According to the terms of the License Agreement, the Publisher TECHNOLOGY CENTER PC does not take away your copyrights and receives permission from the authors to use and dissemination of the publication through the world's scientific resources (own electronic resources, scientometric databases, repositories, libraries, etc.).
In the absence of a signed License Agreement or in the absence of this agreement of identifiers allowing to identify the identity of the author, the editors have no right to work with the manuscript.
It is important to remember that there is another type of agreement between authors and publishers – when copyright is transferred from the authors to the publisher. In this case, the authors lose ownership of their work and may not use it in any way.