Indirect temperature protection of an asynchronous generator by stator winding resistance measurement with superimposition of high-frequency pulse signals
DOI:
https://doi.org/10.15587/1729-4061.2024.302872Keywords:
asynchronous generator, indirect thermal protection, simulation model, stator resistance, constant current componentsAbstract
The article deals with the indirect methods for calculating the temperature of asynchronous generators with the introduction of a pulse component in the power supply circuit of the stator windings of asynchronous generators with squirrel-cage rotor. The relevance of this issue is determined by the need to improve asynchronous energy converters to increase their reliability and safety.
The object of the study is an asynchronous generator with squirrel-cage rotor, which consume 40 % of the total electricity generated, and are the most affordable. One of the dangerous modes of asynchronous generators is their overheating as a result of increased currents and temperatures.
The thermal protection of the stator winding of asynchronous generators relies primarily on measuring or determining the winding temperature.
An indirect method for determining temperature based on measuring the resistance of the stator of an asynchronous generator with squirrel-cage rotor is proposed. The method is based on superimposing pulse signals of small amplitude and high frequency of 600 Hz on an alternating sinusoidal voltage with a frequency of 50 Hz. A simulation model for a 3 kW asynchronous generator has been developed. There were given the simulation results. The estimated values of the active resistances of the stator can be used to indirectly determine the temperature of the windings in thermal protection devices of asynchronous generators, as well as for control, monitoring and diagnostics of the technical condition. The research results confirm the possibility of indirect temperature determination and the creation of a thermal protection system for asynchronous energy converters based on the use of estimation methods.
References
- Huaao, X. (2012). Pat. CN102487191A. Motor overheating protection relay. Application filed: 05.12.2010. Priority: 06.12.2010; Publication: 06.06.2012.
- Fish, M. W., Alexander, D. F. (1949). Pat. US2463935A. Thermal motor protector. Application filed: 19.07.1945; Priority: 09.07.1945; Publication: 08.03.1949.
- Geravandi, M., Moradi CheshmehBeigi, H. (2023). Stator Windings Resistance Estimation Methods of In-Service Induction Motors-A Review. 2023 31st International Conference on Electrical Engineering (ICEE). Tehran, 356–361. https://doi.org/10.1109/icee59167.2023.10334685
- Hassan, A. Y., Elzalik, M. (2022). Signal Injection Based Sensorless Online Monitoring of Induction Motor Temperature. 2022 23rd International Middle East Power Systems Conference (MEPCON). https://doi.org/10.1109/mepcon55441.2022.10021694
- Singh, G., Saleh, A., Amos, J., Sundaram, K., Kapat, J. (2018). IC6A1A6 vs. IC3A1 Squirrel Cage Induction Generator Cooling Configuration Challenges and Advantages for Wind Turbine Application. ASME 2018 Power Conference collocated with the ASME 2018 12th International Conference on Energy Sustainability and the ASME 2018 Nuclear Forum. https://doi.org/10.1115/power2018-7159
- Singh, G. (2020). Wind Turbine Generator Overheating Solution. [Doctoral Dissertation; College of Engineering and Computer Science]. Available at: https://stars.library.ucf.edu/etd2020/133
- Shipurkar, U., Ma, K., Polinder, H., Blaabjerg, F., Ferreira, J. A. (2015). A review of failure mechanisms in wind turbine generator systems. 2015 17th European Conference on Power Electronics and Applications (EPE’15 ECCE-Europe). https://doi.org/10.1109/epe.2015.7311669
- Danikas, M. G., Sarathi, R. (2014). Electrical machine insulation: Traditional insulating materials, nanocomposite polymers and the question of electrical trees. Funktechnikplus# Journal, 5.
- Jeong, Y.-S., Lee, J.-Y. (2011). Parameter Identification of an Induction Motor Drive with Magnetic Saturation for Electric Vehicle. Journal of Power Electronics, 11 (4), 418–423. https://doi.org/10.6113/jpe.2011.11.4.418
- Kopylov, I. P. (2019). Proektirovanie elektricheskikh mashin. Moscow: Iurait, 828.
- Nurmaganbetova, G., Issenov, S., Kaverin, V., Issenov, Z. (2023). Development of a virtual hardware temperature observer for frequency-controlled asynchronous electric motors. Eastern-European Journal of Enterprise Technologies, 3 (1 (123)), 68–75. https://doi.org/10.15587/1729-4061.2023.280357
- Breido, I. V., Semykina, I. Yu., Nurmaganbetova, G. S. (2018). Method of indirect overheating protection for electric drives of mining installations. Bulletin of the Tomsk Polytechnic University, Geo Assets Engineering, 329 (2), 65–71. Available at: https://www.scopus.com/record/display.uri?eid=2-s2.0-85043512914&origin=resultslist&sort=plf-f&src=s&sid=251776237e9a5415cb8d392ab523e260&sot=b&sdt=b&s=FIRSTAUTH%28breido%29&sl=234&sessionSearchId=251776237e9a5415cb8d392ab523e260&relpos=14
- Ishchenko, O. Iu., Remenev, V. Z. (2016). Universalnyi metod kontrolia prevysheniia temperatury elektrodvigatelia. Elektroenergetika i informatcionnye tekhnologii, 9, 39–42.
- Fesenko, O. V., Tereshin, V. N., Ratnikov, A. I., Chernov, V. A., Frolov, Yu. A. (1999). Pat. No. RU2130224C1. Ustroistvo temperaturnoi zashchity asinkhronnykh elektrodvigatelei. MPK7: H02H7/085, H02H6, H02H5/04. declareted: 18.10.1995; published: 10.05.1999.
- Chandra, A., Singh, G. K., Pant, V. (2021). Protection of AC microgrid integrated with renewable energy sources – A research review and future trends. Electric Power Systems Research, 193, 107036. https://doi.org/10.1016/j.epsr.2021.107036
- Zakladnyi, O. (2019). Algorithms of protection of electric motors by means of modern systems of diagnostic of their states. Power Engineering: Economics, Technique, Ecology, 2, 75–84. https://doi.org/10.20535/1813-5420.2.2019.190027
- Kosmodamianskii, A. S. (2005). Avtomaticheskoe regulirovanie temperatury obmotok tiagovykh elektricheskikh mashin lokomotivov. Moscow: Marshrut, 256.
- Pugachev, A. A. (2014). Identifikatciia soprotivleniia i temperatury obmotki rotora asinkhronnogo dvigatelia. Avtomatizirovannyi elektroprivod i promyshlennaia elektronika. Novokuznetck: Izd-vo SibGIU, 192–198.
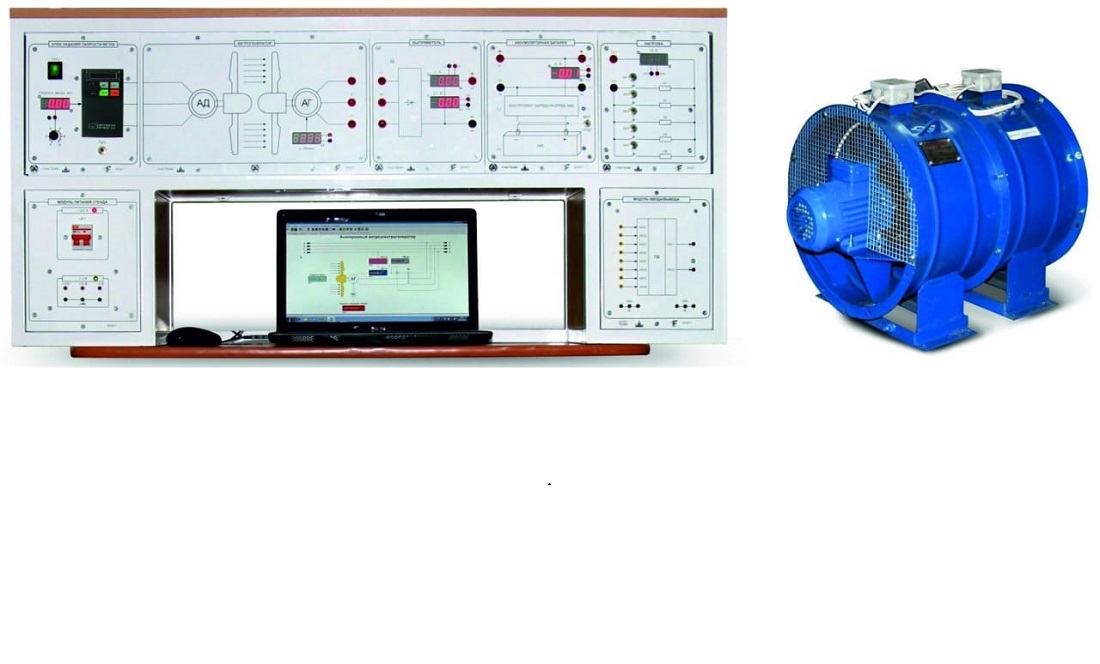
Downloads
Published
How to Cite
Issue
Section
License
Copyright (c) 2024 Gulim Nurmaganbetova, Sultanbek Issenov, Vladimir Kaverin, Gennady Em, Gibrat Asainov, Zhanara Nurmaganbetova, Yuliya Bulatbayeva, Ruslan Kassym

This work is licensed under a Creative Commons Attribution 4.0 International License.
The consolidation and conditions for the transfer of copyright (identification of authorship) is carried out in the License Agreement. In particular, the authors reserve the right to the authorship of their manuscript and transfer the first publication of this work to the journal under the terms of the Creative Commons CC BY license. At the same time, they have the right to conclude on their own additional agreements concerning the non-exclusive distribution of the work in the form in which it was published by this journal, but provided that the link to the first publication of the article in this journal is preserved.
A license agreement is a document in which the author warrants that he/she owns all copyright for the work (manuscript, article, etc.).
The authors, signing the License Agreement with TECHNOLOGY CENTER PC, have all rights to the further use of their work, provided that they link to our edition in which the work was published.
According to the terms of the License Agreement, the Publisher TECHNOLOGY CENTER PC does not take away your copyrights and receives permission from the authors to use and dissemination of the publication through the world's scientific resources (own electronic resources, scientometric databases, repositories, libraries, etc.).
In the absence of a signed License Agreement or in the absence of this agreement of identifiers allowing to identify the identity of the author, the editors have no right to work with the manuscript.
It is important to remember that there is another type of agreement between authors and publishers – when copyright is transferred from the authors to the publisher. In this case, the authors lose ownership of their work and may not use it in any way.