Synthesis of NiCrAlY nano-scale powder by high-energy ball milling process for thermal spray coating application
DOI:
https://doi.org/10.15587/1729-4061.2024.307040Keywords:
coating, high-velocity oxygen fuel (HVOF), NiCrAlY, nano-scale powder, high-energy ball millingAbstract
These days, during the issues of climate change, there has been a shift in the energy industry from using fossil fuels to more environmentally friendly fuels such as biomass fuels. Biomass fuel is considered CO2 neutral because the carbon produced during combustion in the form of CO2 emissions can be used for new plant growth. However, besides the advantages of using biomass fuel, a problem arises when biomass fuel contains a high concentration of corrosive agents, which can be released along with hot fuel gas. These corrosive agents can damage the boiler components. Coating technology is one of the solutions to protect components that work at high temperatures against the corrosion threat. One type of coating that can be used in high-temperature applications is NiCrAlY coating by the high-velocity oxide (HVOF) process. One interesting topic that people are developing is using nano-scale coating to increase the coating’s resistance against hot corrosion and cracking. Nano-scale powder feedstock is needed to produce nano-scale coating material. In this research, top-down method is used to synthesis nano-scale powder. One of top down method, the high-energy ball milling processs, is a promising method to synthesize nano-scale powder material. Therefore, in this research, the ball milling process is used to prepare nano-scale product. The results showed that this method was successful to make the nano-scale powder. The nano-scale powder was characterized by several methods to investigate the morphology and properties of the powders. However, there are still many challenges in producing nano-scale powder that meets HVOF feedstock powder requirements. In the long run, it is expected that this research can answer those challenges so that at the end, the good quality of nano-scale powder can be achieved
References
- Wu, D., Yuan, Z., Liu, S., Zheng, J., Wei, X., Zhang, C. (2020). Recent Development of Corrosion Factors and Coating Applications in Biomass Firing Plants. Coatings, 10 (10), 1001. https://doi.org/10.3390/coatings10101001
- Sadeghimeresht, E. (2018). Ni-based coatings for high temperature corrosion protection. University West. Available at: https://www.diva-portal.org/smash/get/diva2:1203387/FULLTEXT02.pdf
- Szymański, K., Hernas, A., Moskal, G., Myalska, H. (2015). Thermally sprayed coatings resistant to erosion and corrosion for power plant boilers - A review. Surface and Coatings Technology, 268, 153–164. https://doi.org/10.1016/j.surfcoat.2014.10.046
- Vasudev, H., Thakur, L., Bansal, A., Singh, H., Zafar, S. (2019). High temperature oxidation and erosion behaviour of HVOF sprayed bi-layer Alloy-718/NiCrAlY coating. Surface and Coatings Technology, 362, 366–380. https://doi.org/10.1016/j.surfcoat.2019.02.012
- Lv, P., Sun, X., Cai, J., Zhang, C., Liu, X., Guan, Q. (2017). Microstructure and high temperature oxidation resistance of nickel based alloy GH4169 irradiated by high current pulsed electron beam. Surface and Coatings Technology, 309, 401–409. https://doi.org/10.1016/j.surfcoat.2016.11.041
- Yang, H.-Z., Zou, J.-P., Shi, Q., Dai, M.-J., Lin, S.-S., Du, W., Lv, L. (2019). Analysis of the microstructural evolution and interface diffusion behavior of NiCoCrAlYTa coating in high temperature oxidation. Corrosion Science, 153, 162–169. https://doi.org/10.1016/j.corsci.2019.03.022
- An, Q., Huang, L., Wei, S., Zhang, R., Rong, X., Wang, Y., Geng, L. (2019). Enhanced interfacial bonding and superior oxidation resistance of CoCrAlY-TiB2 composite coating fabricated by air plasma spraying. Corrosion Science, 158, 108102. https://doi.org/10.1016/j.corsci.2019.108102
- Luo, L., Zhang, H., Chen, Y., Zhao, C., Alavi, S., Guo, F. et al. (2018). Effects of the β phase size and shape on the oxidation behavior of NiCoCrAlY coating. Corrosion Science, 145, 262–270. https://doi.org/10.1016/j.corsci.2018.10.008
- Quadakkers, W. J., Shemet, V., Sebold, D., Anton, R., Wessel, E., Singheiser, L. (2005). Oxidation characteristics of a platinized MCrAlY bond coat for TBC systems during cyclic oxidation at 1000 °C. Surface and Coatings Technology, 199 (1), 77–82. https://doi.org/10.1016/j.surfcoat.2004.11.038
- Pint, B. A., More, K. L. (2009). Characterization of alumina interfaces in TBC systems. Journal of Materials Science, 44 (7), 1676–1686. https://doi.org/10.1007/s10853-008-3221-x
- Shourgeshty, M., Aliofkhazraei, M., Alipour, M. M. (2016). Introduction to High‐Temperature Coatings. High Temperature Corrosion. https://doi.org/10.5772/64282
- Shi, P., Wang, W., Wan, S., Gao, Q., Sun, H., Feng, X. et al. (2021). Tribological performance and high temperature oxidation behaviour of thermal sprayed Ni- and NiCrAlY-based composite coatings. Surface and Coatings Technology, 405, 126615. https://doi.org/10.1016/j.surfcoat.2020.126615
- Suryanarayana, C. (2001). Mechanical alloying and milling. Progress in Materials Science, 46 (1-2), 1–184. https://doi.org/10.1016/s0079-6425(99)00010-9
- Zakeri, A., Bahmani, E., Aghdam, A. S. R. (2020). Impact of MCrAlY feedstock powder modification by high-energy ball milling on the microstructure and high-temperature oxidation performance of HVOF-sprayed coatings. Surface and Coatings Technology, 395, 125935. https://doi.org/10.1016/j.surfcoat.2020.125935
- Khodsiani, Z., Mansuri, H., Mirian, T. (2013). The effect of cryomilling on the morphology and particle size distribution of the NiCoCrAlYSi powders with and without nano-sized alumina. Powder Technology, 245, 7–12. https://doi.org/10.1016/j.powtec.2013.04.010
- Borchers, C., Stoltenhoff, T., Hahn, M., Schulze, M., Assadi, H., Suryanarayana, C. et al. (2014). Strain‐Induced Phase Transformation of MCrAlY. Advanced Engineering Materials, 17 (5), 723–731. https://doi.org/10.1002/adem.201400174
- Kaplin, C., Brochu, M. (2014). The effect of grain size on the oxidation of NiCoCrAlY. Applied Surface Science, 301, 258–263. https://doi.org/10.1016/j.apsusc.2014.02.056
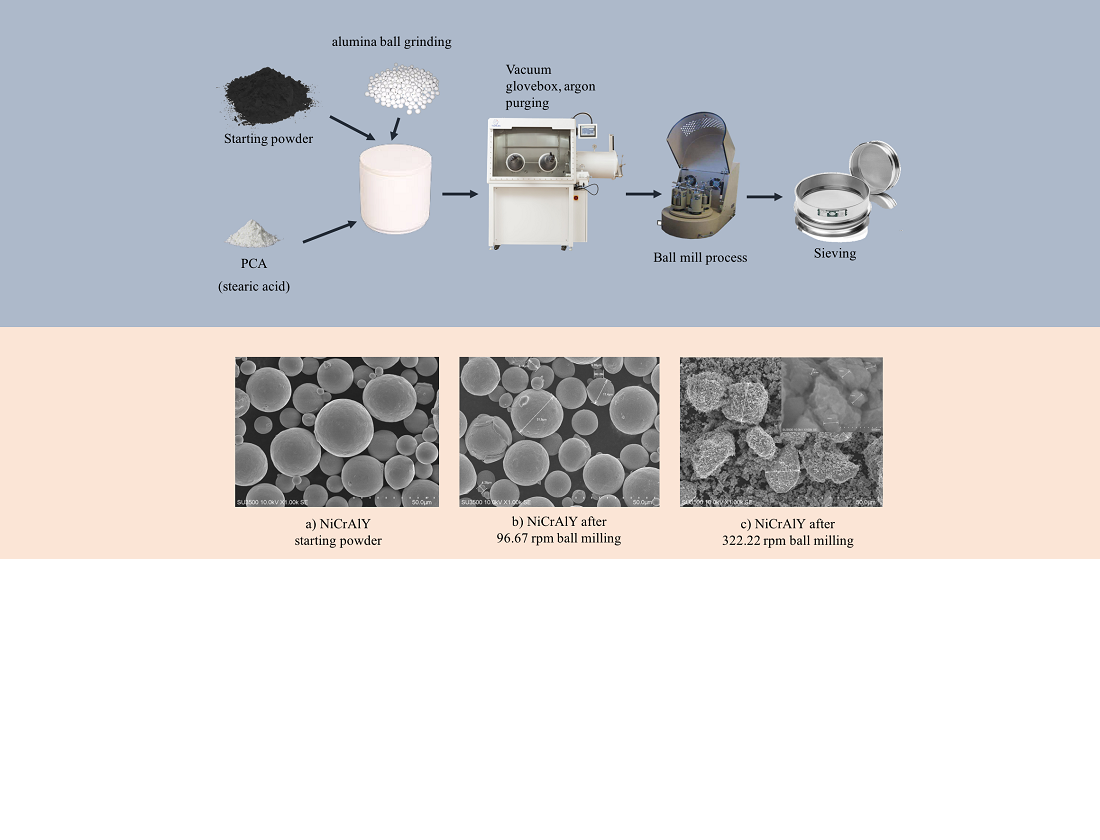
Downloads
Published
How to Cite
Issue
Section
License
Copyright (c) 2024 Irma Pratiwi, Husaini Ardy, Budi Prawara, Raden Dadan Ramdan, Fahdzi Muttaqien

This work is licensed under a Creative Commons Attribution 4.0 International License.
The consolidation and conditions for the transfer of copyright (identification of authorship) is carried out in the License Agreement. In particular, the authors reserve the right to the authorship of their manuscript and transfer the first publication of this work to the journal under the terms of the Creative Commons CC BY license. At the same time, they have the right to conclude on their own additional agreements concerning the non-exclusive distribution of the work in the form in which it was published by this journal, but provided that the link to the first publication of the article in this journal is preserved.
A license agreement is a document in which the author warrants that he/she owns all copyright for the work (manuscript, article, etc.).
The authors, signing the License Agreement with TECHNOLOGY CENTER PC, have all rights to the further use of their work, provided that they link to our edition in which the work was published.
According to the terms of the License Agreement, the Publisher TECHNOLOGY CENTER PC does not take away your copyrights and receives permission from the authors to use and dissemination of the publication through the world's scientific resources (own electronic resources, scientometric databases, repositories, libraries, etc.).
In the absence of a signed License Agreement or in the absence of this agreement of identifiers allowing to identify the identity of the author, the editors have no right to work with the manuscript.
It is important to remember that there is another type of agreement between authors and publishers – when copyright is transferred from the authors to the publisher. In this case, the authors lose ownership of their work and may not use it in any way.