Determining patterns of the vertical load on a covered wagon roof with a frame in the form of a triangular arch
DOI:
https://doi.org/10.15587/1729-4061.2024.308905Keywords:
railroad transport, covered wagon, wagon roof, roof load, roof strengthAbstract
The object of this paper is the processes of perception and redistribution of loads in the roof of a railroad covered wagon with a frame in the form of a triangular arch.
To reduce the tare of the covered wagon, it is proposed to improve the structure of its roof. A feature of this improvement is that the roof frame is made in the form of a triangular arch with a reinforcing belt. This contributes to the reduction of the total mass of the roof compared to a typical structure. The selection of execution profiles of the beams forming the arch is carried out according to the maximum values of the moments that act in their cross-section. Taking into account the chosen profile of the arches, the calculation of the strength of the roof when it receives vertical loads was carried out. It was established that the strength of the roof under the considered load schemes is within the permissible stress values. Since the improvement of the roof structure contributes to the reduction of its weight by 1.8 % compared to the prototype, the movement of the covered wagon was evaluated under conditions of moving while empty. To this end, a mathematical modeling of the load of the covered wagon in the vertical plane during its movement along the joint unevenness was carried out. On the basis of the performed calculation, it was established that the movement of the wagon is assessed as "good".
Special feature of the results is that the reduction of the tare of the supporting structure of the wagon was achieved by improving its roof, as the least loaded unit.
The field of practical application of the results is railroad transport, including other areas of mechanical engineering. The conditions for the practical use of the results are a symmetrical roof load scheme in operation.
The results of this research could contribute to advancements related to the design of modern structures of freight wagons with improved technical and economic indicators
References
- Lovska, A. (2018). Simulation of Loads on the Carrying Structure of an Articulated Flat Car in Combined Transportation. International Journal of Engineering & Technology, 7 (4.3), 140. https://doi.org/10.14419/ijet.v7i4.3.19724
- Dižo, J., Blatnický, M., Steišūnas, S., Skočilasová, B. (2018). Assessment of a rail vehicle running with the damaged wheel on a ride comfort for passengers. MATEC Web of Conferences, 157, 03004. https://doi.org/10.1051/matecconf/201815703004
- Dizo, J., Blatnicky, M., Harusinec, J., Falendysh, A. (2018). Modification and analyses of structural properties of a goods wagon bogie frame. Diagnostyka, 20 (1), 41–48. https://doi.org/10.29354/diag/99853
- Fomin, O., Lovska, A. (2021). Justification of the use of square pipes in the frame of the removable roof of the open wagon. Eastern-European Journal of Enterprise Technologies, 4 (7 (112)), 18–25. https://doi.org/10.15587/1729-4061.2021.237157
- Sepe, R., Pozzi, A. (2015). Static and modal numerical analyses for the roof structure of a railway freight refrigerated car. Frattura Ed Integrità Strutturale, 9 (33), 451–462. https://doi.org/10.3221/igf-esis.33.50
- Cuartero, J., Miravete, A., Sanz, R. (2011). Design and calculation of a railway car composite roof under concrete cube crash. International Journal of Crashworthiness, 16 (1), 41–47. https://doi.org/10.1080/13588265.2010.501163
- Fomin, O., Stetsko, A. (2018). Determination of means of contraindication of operative damage of superior wagon-thermal systems of the model TN 4-201. Collection of Scientific Works of the State University of Infrastructure and Technologies Series “Transport Systems and Technologies,” 32 (1), 135–146. Internet Archive. https://doi.org/10.32703/2617-9040-2018-32-1-135-146
- Saeedi, A., Motavalli, M., Shahverdi, M. (2023). Recent advancements in the applications of fiber‐reinforced polymer structures in railway industry – A review. Polymer Composites, 45 (1), 77–97. https://doi.org/10.1002/pc.27817
- Chandra Prakash Shukla, Bharti, P. K. (2015). Study and Analysis of Doors of BCNHL Wagons. International Journal of Engineering Research And, 4 (04). https://doi.org/10.17577/ijertv4is041031
- Levchenko, S. V., Tatianich, E. M., Konopatskyi, Yu. P., Yablonskyi, A. V., Shkabrov, O. A., Kryzhanovskyi, A. Yu. (2016). Pat. No. 109202 UA. Znimnyi dakh vantazhnoho vahona. No. u2016 03361; declareted: 31.03.2016; published: 10.08.2016. Available at: https://uapatents.com/8-109202-znimnijj-dakh-vantazhnogo-vagona.html
- Kondratiev, A., Píštěk, V., Smovziuk, L., Shevtsova, M., Fomina, A., Kučera, P. (2021). Stress–Strain Behaviour of Reparable Composite Panel with Step-Variable Thickness. Polymers, 13 (21), 3830. https://doi.org/10.3390/polym13213830
- Kondratiev, A., Gaidachuk, V., Nabokina, T., Kovalenko, V. (2019). Determination of the influence of deflections in the thickness of a composite material on its physical and mechanical properties with a local damage to its wholeness. Eastern-European Journal of Enterprise Technologies, 4 (1 (100)), 6–13. https://doi.org/10.15587/1729-4061.2019.174025
- Lee, W. G., Kim, J.-S., Sun, S.-J., Lim, J.-Y. (2016). The next generation material for lightweight railway car body structures: Magnesium alloys. Proceedings of the Institution of Mechanical Engineers, Part F: Journal of Rail and Rapid Transit, 232 (1), 25–42. https://doi.org/10.1177/0954409716646140
- Olmos Irikovich, Z., Rustam Vyacheslavovich, R., Mahmod Lafta, W., Yadgor Ozodovich, R. (2020). Development of new polymer composite materials for the flooring of rail carriage. International Journal of Engineering & Technology, 9 (2), 378–381. https://doi.org/10.14419/ijet.v9i2.30519
- Fantuzzi, N., Bacciocchi, M., Benedetti, D., Agnelli, J. (2021). The use of sustainable composites for the manufacturing of electric cars. Composites Part C: Open Access, 4, 100096. https://doi.org/10.1016/j.jcomc.2020.100096
- Horbenko, A. P., Martynov, I. E. (2007). Konstruiuvannia ta rozrakhunky vahoniv. Kharkiv: UkrDAZT, 150.
- Vidy visyachih stropil'nyh sistem primenyaemyh v stroitel'stve. Available at: https://www.pinterest.com/pin/509610514079263558/
- Chausov, M. H., Bondar, M. M., Pylypenko, A. P., Kutsenko, A. H. (2019). Prykladna mekhanika (opir materialiv). Kyiv. Available at: https://dglib.nubip.edu.ua/server/api/core/bitstreams/be589d1e-4513-4caf-8792-ebb016171ab2/content
- Shvabiuk, V. I. (2016). Opir materialiv. Kyiv: Znannia, 400. Available at: https://btpm.nmu.org.ua/ua/download/navch-posib/%D0%A8%D0%B2%D0%B0%D0%B1%D1%8E%D0%BA.%D0%9E%D0%9C.%D0%9F%D1%96%D0%B4%D1%80%D1%83%D1%87%D0%BD%D0%B8%D0%BA.pdf
- DSTU 7598:2014. Freight Wagons. General reguirements to calculation and designing of the new and modernized 1520 mm gauge wagons (non-self-propelled). Kyiv. Available at: https://online.budstandart.com/ua/catalog/doc-page.html?id_doc=73763
- BDS EN 12663-2: 2010. Railway applications - Structural requirements of railway vehicle bodies - Part 2: Freight wagons (EN 12663-2: 2010).
- Pustiulha, S. I., Samostian, V. R., Klak, Yu. V. (20189). Inzhenerna hrafika v SolidWorks. Lutsk: Vezha, 172. Available at: https://lib.lntu.edu.ua/sites/default/files/2021-02/%D0%86%D0%BD%D0%B6%D0%B5%D0%BD%D0%B5%D1%80%D0%BD%D0%B0%20%D0%B3%D1%80%D0%B0%D1%84%D1%96%D0%BA%D0%B0%20%D0%B2%20SolidWorks.pdf
- Koziar, M. M., Feshchuk, Yu. V., Parfeniuk, O. V. (2018). Kompiuterna hrafika: SolidWorks. Kherson: Oldi-plius, 252. Available at: https://ep3.nuwm.edu.ua/22175/1/%D0%9A%D0%BE%D0%BC%D0%BF%27%D1%8E%D1%82%D0%B5%D1%80%D0%BD%D0%B0%20%D0%B3%D1%80%D0%B0%D1%84%D1%96%D0%BA%D0%B0.pdf
- Caban, J., Nieoczym, A Gardyński, L. (2021). Strength analysis of a container semi-truck frame. Engineering Failure Analysis, 127, 105487. https://doi.org/10.1016/j.engfailanal.2021.105487
- Lovskaya, A. (2015). Computer simulation of wagon body bearing structure dynamics during transportation by train ferry. Eastern-European Journal of Enterprise Technologies, 3 (7 (75)), 9–14. https://doi.org/10.15587/1729-4061.2015.43749
- Dižo, J. (2016). Analysis of a Goods Wagon Running on a Railway Test Track. Manufacturing Technology, 16 (4), 667–672. https://doi.org/10.21062/ujep/x.2016/a/1213-2489/mt/16/4/667
- Vatulia, G., Lovska, A., Pavliuchenkov, M., Nerubatskyi, V., Okorokov, A., Hordiienko, D. et al. (2022). Determining patterns of vertical load on the prototype of a removable module for long-size cargoes. Eastern-European Journal of Enterprise Technologies, 6 (7 (120)), 21–29. https://doi.org/10.15587/1729-4061.2022.266855
- Panchenko, S., Gerlici, J., Vatulia, G., Lovska, A., Rybin, A., Kravchenko, O. (2023). Strength Assessment of an Improved Design of a Tank Container under Operating Conditions. Communications - Scientific Letters of the University of Zilina, 25 (3), B186–B193. https://doi.org/10.26552/com.c.2023.047
- Soukup, J., Skočilas, J., Skočilasová, B., Dižo, J. (2017). Vertical Vibration of Two Axle Railway Vehicle. Procedia Engineering, 177, 25–32. https://doi.org/10.1016/j.proeng.2017.02.178
- Domin, Yu. V., Cherniak, H. Yu. (2003). Osnovy dynamiky vahoniv. Kyiv: KUETT, 269.
- Gerlici, J., Lovska, A., Vatulia, G., Pavliuchenkov, M., Kravchenko, O., Solčanský, S. (2023). Situational Adaptation of the Open Wagon Body to Container Transportation. Applied Sciences, 13 (15), 8605. https://doi.org/10.3390/app13158605
- Lovska, A., Dižo, J., Prokopovych, I., Zharovа, O., Voronenko, S. (2023). Detecting the effect of an intermediate adapter on the load of the bearing structure of an open wagon. Eastern-European Journal of Enterprise Technologies, 6 (7 (126)), 19–25. https://doi.org/10.15587/1729-4061.2023.291247
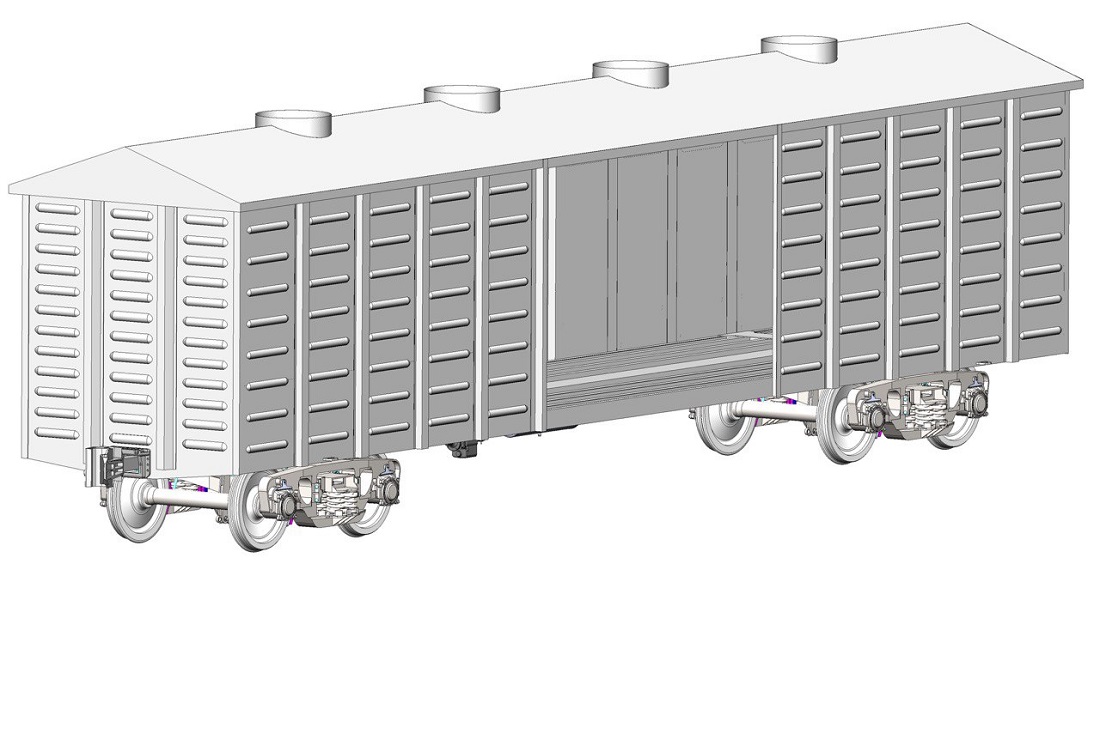
Downloads
Published
How to Cite
Issue
Section
License
Copyright (c) 2024 Alyona Lovska, Iraida Stanovska, Ihor Prokopovych, Ihor Sydorenko, Arsen Muradian

This work is licensed under a Creative Commons Attribution 4.0 International License.
The consolidation and conditions for the transfer of copyright (identification of authorship) is carried out in the License Agreement. In particular, the authors reserve the right to the authorship of their manuscript and transfer the first publication of this work to the journal under the terms of the Creative Commons CC BY license. At the same time, they have the right to conclude on their own additional agreements concerning the non-exclusive distribution of the work in the form in which it was published by this journal, but provided that the link to the first publication of the article in this journal is preserved.
A license agreement is a document in which the author warrants that he/she owns all copyright for the work (manuscript, article, etc.).
The authors, signing the License Agreement with TECHNOLOGY CENTER PC, have all rights to the further use of their work, provided that they link to our edition in which the work was published.
According to the terms of the License Agreement, the Publisher TECHNOLOGY CENTER PC does not take away your copyrights and receives permission from the authors to use and dissemination of the publication through the world's scientific resources (own electronic resources, scientometric databases, repositories, libraries, etc.).
In the absence of a signed License Agreement or in the absence of this agreement of identifiers allowing to identify the identity of the author, the editors have no right to work with the manuscript.
It is important to remember that there is another type of agreement between authors and publishers – when copyright is transferred from the authors to the publisher. In this case, the authors lose ownership of their work and may not use it in any way.