Determining the mechanism for generating cavitation pressure fluctuations in throttle devices at high-head throttling of liquid
DOI:
https://doi.org/10.15587/1729-4061.2024.309656Keywords:
cavitation flow, pressure pulsations, pressure drop, discrete jet, high-head throttlingAbstract
The object of this study is the process of generating cavitation pressure fluctuations behind the throttle device at high-head throttling of liquid. This paper addressed the problem of calculating the amplitude of cavitation pressure fluctuations at high-pressure liquid throttling. It was established that cavitation pressure fluctuations are a consequence of collisions of discrete masses of a transiting liquid jet in the region of pressure recovery. The range of cavitation pressure fluctuations reaches the pressure values at the inlet to the throttle device. The frequency band of cavitation pressure fluctuations is in the range from 1.5 to 20 kHz and higher. At high-head throttling of the liquid, caverns attached to the surface of the throttle channel, moving caverns and small bubbles in the transit flow are formed. Moving caverns compress the transit flow and divide it into separate fluid blocks. In the region of pressure restoration, the moving caverns are slammed shut and discrete fluid blocks collide. This causes high-frequency pressure fluctuations. Special feature of the results is the possibility of estimating the range of cavitation pressure fluctuations depending on the pressure drop on the throttle device. When the back pressure on the throttle device increases, the amplitude of cavitation pressure fluctuations decreases, and the frequency band shifts to the high-frequency region. The results make it possible to calculate the range of cavitation oscillations, to predict the development of cavitation erosion of materials depending on the parameters of throttling of the working fluid. The results of the work are used to design devices for cleaning products from contamination, for determining the volume content of water in aviation fuel, for intensification of technological processes in the chemical and food industries.
References
- Glazkov, M., Lanetskiy, V., Makarenko, N., Chelyukanov, I. (1987). Kavitatsiya v zhidkostnyh sistemah vozdushnyh sudov. Kyiv: KIIGA, 64.
- Zheng, X., Wang, X., Lu, X., Zhang, Y., Zhang, Y., Yu, J. (2023). An Experimental Study of Cavitation Bubble Dynamics near a Complex Wall with a Continuous Triangular Arrangement. Symmetry, 15 (3), 693. https://doi.org/10.3390/sym15030693
- Ohl, C., Linbau, O., Lauterborn, W., Philipp, A. (1998). Details of asymmetric bubble collapse. Third international Symposium on Cavitation. Band 1. Grenoble, 39–44.
- Osterland, S., Müller, L., Weber, J. (2021). Influence of Air Dissolved in Hydraulic Oil on Cavitation Erosion. International Journal of Fluid Power, 22 (3), 373–392. https://doi.org/10.13052/ijfp1439-9776.2234
- Glazkov, M., Tarasenko, T. (2003). Vliyanie rezhimov drosselirovaniya na lokalizatsiyu i intensivnost' erozii gidroapparatury v potoke zhidkosti. Promyslova hidravlika i pnevmatyka, 2, 43–46.
- Knepp, R., Deyli, L., Hemmit, F. (1974). Kavitatsiya. Moscow: Mir, 679.
- Tarasenko, T., Badakh, V. (2017). Cavitation Liquid Leakage through Throttle Device. Mechanics and Advanced Technologies, 3 (81), 82–91. https://doi.org/10.20535/2521-1943.2017.81.117480
- Hlazkov, M., Lanetskyi, V., Tarasenko, T. (2007). Matematychna model rozmakhu kavitatsiynykh pulsatsiy tysku. Materialy IX mizhnarodnoi naukovo-tekhnichnoi konferentsiyi «Avia - 2007». Vol. 2. Kyiv: NAU, 60–62.
- Soyama, H., Hoshino, J. (2016). Enhancing the aggressive intensity of hydrodynamic cavitation through a Venturi tube by increasing the pressure in the region where the bubbles collapse. AIP Advances, 6 (4). https://doi.org/10.1063/1.4947572
- Tarasenko, T., Badach, V., Puzik, O. (2013). Functional units based on cavitation effects for hydraulic systems of vehicles. Science – Future of Lithuania: 16th Conference for Junior Researchers. Vilnius, 50–54.
- Xu, X., Fang, L., Li, A., Wang, Z., Li, S. (2021). Numerical Analysis of the energy loss mechanism in cavitation flow of a control valve. International Journal of Heat and Mass Transfer, 174, 121331. https://doi.org/10.1016/j.ijheatmasstransfer.2021.121331
- Li, M., Yang, G., Wu, G., Li, X. (2020). Oxidative Deterioration Effect of Cavitation Heat Generation on Hydraulic Oil. IEEE Access, 8, 119720–119727. https://doi.org/10.1109/access.2020.3005636
- Zhang, H., Chen, G., Wu, Q., Huang, B. (2022). Experimental investigation of unsteady attached cavitating flow induced pressure fluctuation. Journal of Hydrodynamics, 34 (1), 31–42. https://doi.org/10.1007/s42241-022-0003-x
- Ferrari, A. (2017). Fluid dynamics of acoustic and hydrodynamic cavitation in hydraulic power systems. Proceedings of the Royal Society A: Mathematical, Physical and Engineering Sciences, 473 (2199), 20160345. https://doi.org/10.1098/rspa.2016.0345
- Simpson, A., Ranade, V. V. (2018). Modeling hydrodynamic cavitation in venturi: influence of venturi configuration on inception and extent of cavitation. AIChE Journal, 65 (1), 421–433. https://doi.org/10.1002/aic.16411
- Echouchene, F., Belmabrouk, H. (2022). Analysis of Geometric Parameters of the Nozzle Orifice on Cavitating Flow and Entropy Production in a Diesel Injector. Applications of Computational Fluid Dynamics Simulation and Modeling. https://doi.org/10.5772/intechopen.99404
- Pilipenko, V. (1989). Kavitatsionnye kolebaniya. Kyiv: Naukova dumka, 316.
- Oba, R., Ito, Y., Miyakura, H., Higuchi, J., Sato, K. (1987). Stochastic behavior (randomness) of acoustic pressure pulses in the near-subcavitating range. JSME International Journal, 30 (262), 581–586. https://doi.org/10.1299/jsme1987.30.581
- Khozaei, M. H., Favrel, A., Miyagawa, K. (2022). On the generation mechanisms of low-frequency synchronous pressure pulsations in a simplified draft-tube cone. International Journal of Heat and Fluid Flow, 93, 108912. https://doi.org/10.1016/j.ijheatfluidflow.2021.108912
- Tarasenko, T. V., Badach, V. M. (2019). Investigation of localization and intensity of calculative erosion in high-speed droselidation of liquid in hydrocontrol devices. Problems of Friction and Wear, 2 (83), 93–103. https://doi.org/10.18372/0370-2197.2(83).13697
- Khavari, M., Priyadarshi, A., Morton, J., Porfyrakis, K., Pericleous, K., Eskin, D., Tzanakis, I. (2023). Cavitation-induced shock wave behaviour in different liquids. Ultrasonics Sonochemistry, 94, 106328. https://doi.org/10.1016/j.ultsonch.2023.106328
- Melissaris, T., Schenke, S., van Terwisga, T. J. C. (2023). Cavitation erosion risk assessment for a marine propeller behind a Ro–Ro container vessel. Physics of Fluids, 35 (1). https://doi.org/10.1063/5.0131914
- Joshi, S., Franc, J. P., Ghigliotti, G., Fivel, M. (2019). SPH modelling of a cavitation bubble collapse near an elasto-visco-plastic material. Journal of the Mechanics and Physics of Solids, 125, 420–439. https://doi.org/10.1016/j.jmps.2018.12.016
- Magnotti, G. M., Battistoni, M., Saha, K., Som, S. (2020). Development and validation of the cavitation-induced erosion risk assessment tool. Transportation Engineering, 2, 100034. https://doi.org/10.1016/j.treng.2020.100034
- Shi, H., Li, M., Nikrityuk, P., Liu, Q. (2019). Experimental and numerical study of cavitation flows in venturi tubes: From CFD to an empirical model. Chemical Engineering Science, 207, 672–687. https://doi.org/10.1016/j.ces.2019.07.004
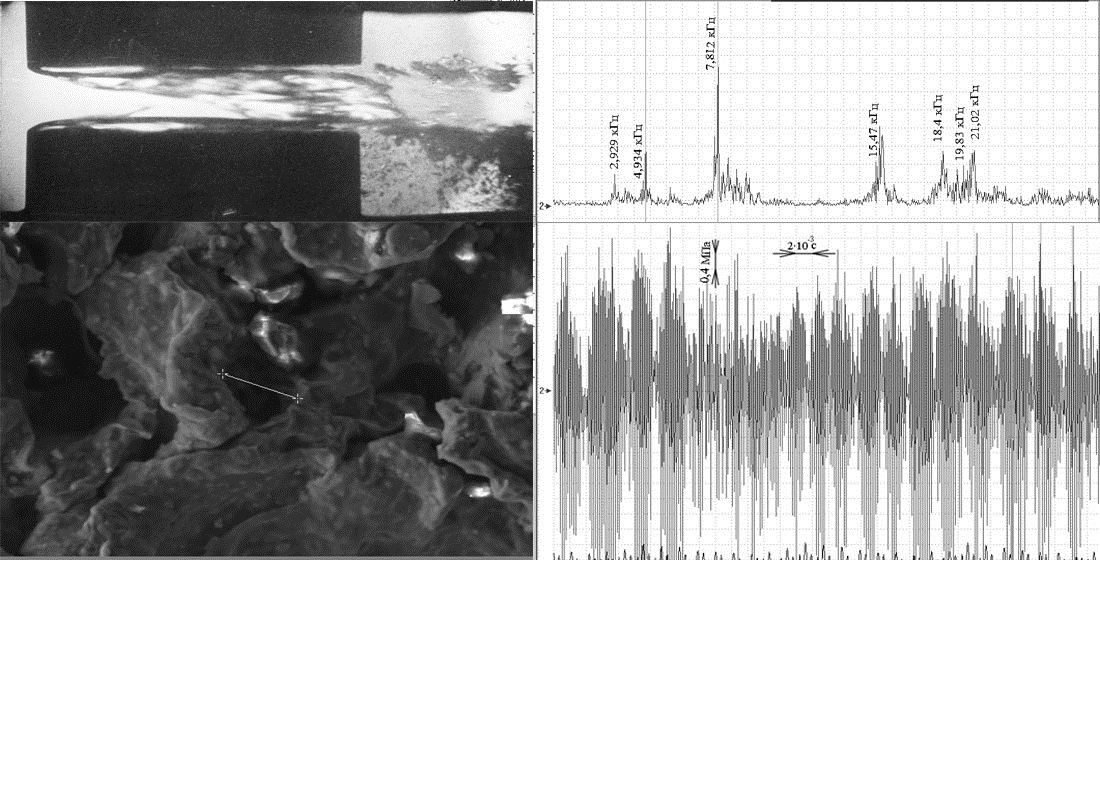
Downloads
Published
How to Cite
Issue
Section
License
Copyright (c) 2024 Taras Tarasenko, Valerii Badakh, Mykola Makarenko, Pavel Lukianov, Igor Dubkovetskiy

This work is licensed under a Creative Commons Attribution 4.0 International License.
The consolidation and conditions for the transfer of copyright (identification of authorship) is carried out in the License Agreement. In particular, the authors reserve the right to the authorship of their manuscript and transfer the first publication of this work to the journal under the terms of the Creative Commons CC BY license. At the same time, they have the right to conclude on their own additional agreements concerning the non-exclusive distribution of the work in the form in which it was published by this journal, but provided that the link to the first publication of the article in this journal is preserved.
A license agreement is a document in which the author warrants that he/she owns all copyright for the work (manuscript, article, etc.).
The authors, signing the License Agreement with TECHNOLOGY CENTER PC, have all rights to the further use of their work, provided that they link to our edition in which the work was published.
According to the terms of the License Agreement, the Publisher TECHNOLOGY CENTER PC does not take away your copyrights and receives permission from the authors to use and dissemination of the publication through the world's scientific resources (own electronic resources, scientometric databases, repositories, libraries, etc.).
In the absence of a signed License Agreement or in the absence of this agreement of identifiers allowing to identify the identity of the author, the editors have no right to work with the manuscript.
It is important to remember that there is another type of agreement between authors and publishers – when copyright is transferred from the authors to the publisher. In this case, the authors lose ownership of their work and may not use it in any way.