The influence of the rotor shape on the efficiency of the hydrodynamic heater
DOI:
https://doi.org/10.15587/1729-4061.2024.310140Keywords:
rotor drum, liquid temperature, cylinder rotation, liquid level, thermal energyAbstract
The paper discusses issues related to the design of a hydrodynamic throttle type heater. The maximum angular velocities for cylindrical and conical shapes are determined from the condition of non-spilling of liquid from a rotating vessel.
Theoretical studies have shown that the conical shape of the skirt is more optimal, since with an increase in the liquid level in the vessel within 0.02–0.09 m, the angular velocity decreases from 37.566 rad/s to 17.709 rad/s, respectively. In addition, with a taper of the vessel walls of 5° and a liquid level height of 0.02 m, the volume of the liquid is 11.0·10–5 m3. If to increase the liquid level to 0.09 m, then the volume of liquid will increase to 55.0·10–5 m3. At a taper of 10°, respectively, there is also an increase in the volume of liquid from 6.0·10–5 m3 to 42.0·10–5 m3.
To establish a small increase in the temperature of the liquid when it is forced through the throttle holes, a transparent mock-up was made. Experimental studies have shown the locking of air during the formation of a ring of liquid in the rotor cavity. In addition, it was found that the smaller the inner radius of the liquid ring, the higher the temperature of the pressed liquid through the throttle openings. For this purpose, a system for removing air from its rotor was provided in the hydrodynamic heater.
When the rotor is running, the lateral outer walls of the conical skirt interact with the liquid, forcing it to rotate. The rotating liquid, rising along the walls of the housing, begins to interact with the lower part of the rotor, which negatively affects the operation of the hydrodynamic heater as a whole. For this purpose, a special flow directing cylinder was provided in the housing.
When the liquid is forced through the throttle opening, there is a decrease in pressure and an increase in the velocity of the liquid. This leads to an increase in its kinetic energy, which is then converted into thermal energy due to friction between the liquid molecules. This principle is used in various systems such as heating systems, industrial processes or laboratory research. However, creating pressure in front of the throttle openings using the inertial forces of a rotating mass of liquid is a promising direction
References
- Tergemes, K. T., Duisembaev, M. S. (2014). Vortex heat generator with an adjustable energy conversion coefficient for heating farmhouses. Research, results. Available at: https://articlekz.com/article/12654
- Guo, G., Lu, K., Xu, S., Yuan, J., Bai, T., Yang, K., He, Z. (2023). Effects of in-nozzle liquid fuel vortex cavitation on characteristics of flow and spray: Numerical research. International Communications in Heat and Mass Transfer, 148, 107040. https://doi.org/10.1016/j.icheatmasstransfer.2023.107040
- Usychenko, V. G. (2012). The Ranque effect as a self-organization phenomenon. Technical Physics, 57 (3), 379–385. https://doi.org/10.1134/s1063784212030164
- Aghakashi, V., Saidi, M. H. (2018). Turbulent decaying swirling flow in a pipe. Heat Transfer Research, 49 (16), 1559–1585. https://doi.org/10.1615/heattransres.2018021519
- Yurchenko, V. V., Isaev, V. L., Kuchin, V. N., Kalinin, A. A., Zeynullin, A. A. (2014). Pat. No. 31003 KZ. Mechanical heat generator. declareted: 13.10.2014; published: 15.03.2016. Available at: https://kzpatents.com/4-31003-teplogenerator-mehanicheskijj.html
- Kalinin, A. A., Kuchin, V. N., Breydo, I. V., Isaev, V. L., Yurchenko, V. V. (2016). Pat. No. 31624 KZ. Cavitation vortex heat generator. declareted: 04.12.2014; published: 30.09.2016. Available at: https://kzpatents.com/4-31624-teplogenerator-kavitacionno-vihrevojj.html
- Mujtaba, M., Cuntang, W., Yasin, F. M., Xie, F. (2018). Throttle Valve as a Heating Element in Wind Hydraulic Thermal System. Journal of Advance Research in Mechanical & Civil Engineering (ISSN: 2208-2379), 5 (2), 01–11. https://doi.org/10.53555/nnmce.v5i2.304
- Ved, V., Nikolsky, V., Oliynyk, O., Lipeev, A. (2017). Examining a cavitation heat generator and the control method over the efficiency of its operation. Eastern-European Journal of Enterprise Technologies, 4 (8 (88)), 22–28. https://doi.org/10.15587/1729-4061.2017.108580
- Casiano, M. J., Hulka, J. R., Yang, V. (2010). Liquid-Propellant Rocket Engine Throttling: A Comprehensive Review. Journal of Propulsion and Power, 26 (5), 897–923. https://doi.org/10.2514/1.49791
- Kapranova, A. B., Lebedev, A. E., Melzer, A. M., Neklyudov, S. V. (2019). About Formation of Elements of a Cyber-Physical System for Efficient Throttling of Fluid in an Axial Valve. Cyber-Physical Systems: Advances in Design & Modelling, 109–119. https://doi.org/10.1007/978-3-030-32579-4_9
- Kapranova, A. B., Lebedev, A. E., Meltser, A. M., Neklyudov, S. V. (2018). On the influence of the throughput of the axial valve on the parameters of the stochastic model of cavitation. RHJ Journal of the Chemical Society named after D.I. Mendeleev, 62 (4), 51–53.
- Kireev, V., Nizamova, A., Urmancheev, S. (2019). The hydraulic resistance of thermoviscous liquid flow in a plane channel with a variable cross-section. Journal of Physics: Conference Series, 1158, 032014. https://doi.org/10.1088/1742-6596/1158/3/032014
- Qian, J., Liu, C., Qiu, C., Li, W., Chen, D. (2024). Liquid hydrogen cavitation analysis inside an oblique globe valve. Flow Measurement and Instrumentation, 97, 102599. https://doi.org/10.1016/j.flowmeasinst.2024.102599
- Hwang, S., Kim, H., Choi, H., Kim, T., Kim, H. (2024). Design evaluation of an immersion heater using a fluid with low Prandtl number based on computation fluid dynamics analysis. Journal of Mechanical Science and Technology, 38 (4), 2151–2159. https://doi.org/10.1007/s12206-024-0343-2
- Ghahramani, E., Ström, H., Bensow, R. E. (2021). Numerical simulation and analysis of multi-scale cavitating flows. Journal of Fluid Mechanics, 922. https://doi.org/10.1017/jfm.2021.424
- Oshanov, E., Abdirova, N., Tusuphanova, A. (2023). Determination of the maximum angular speed rotation of inertial heating hydrodynamic installation rotor. Abstracts of I International Scientific and Practical Conference. Varna, 222–226.
- Nussupbekov, B., Oshanov, Y., Ovcharov, M., Mussenova, E., Ospanova, D., Bolatbekova, M. (2022). Development and creation of a hydrodynamic liquid heating unit. Eastern-European Journal of Enterprise Technologies, 5 (8 (119)), 62–69. https://doi.org/10.15587/1729-4061.2022.264227
- Hoppe, F., Breuer, M. (2020). A deterministic breakup model for Euler–Lagrange simulations of turbulent microbubble-laden flows. International Journal of Multiphase Flow, 123, 103119. https://doi.org/10.1016/j.ijmultiphaseflow.2019.103119
- Nussupbekov, B. R., Ovcharov, M. S., Oshanov, E. Z., Yesbergenov, U. B., Duisenbayeva, M. S., Tishbekov, A. A., Amanzholova, M. K. (2023). Determination of the effects of the diameters of the throttle holes on the fluid flow of an inertial hydrodynamic installation. Bulletin of the Karaganda University “Physics Series,” 112 (4), 82–90. https://doi.org/10.31489/2023ph4/82-90
- Nussupbekov, B., Oshanov, Y., Ovcharov, M., Kutum, B., Duisenbayeva, М., Kongyrbayeva, A. (2023). Identifying regularities of fluid throttling of an inertial hydrodynamic installation. Eastern-European Journal of Enterprise Technologies, 6 (7 (126)), 26–32. https://doi.org/10.15587/1729-4061.2023.292522
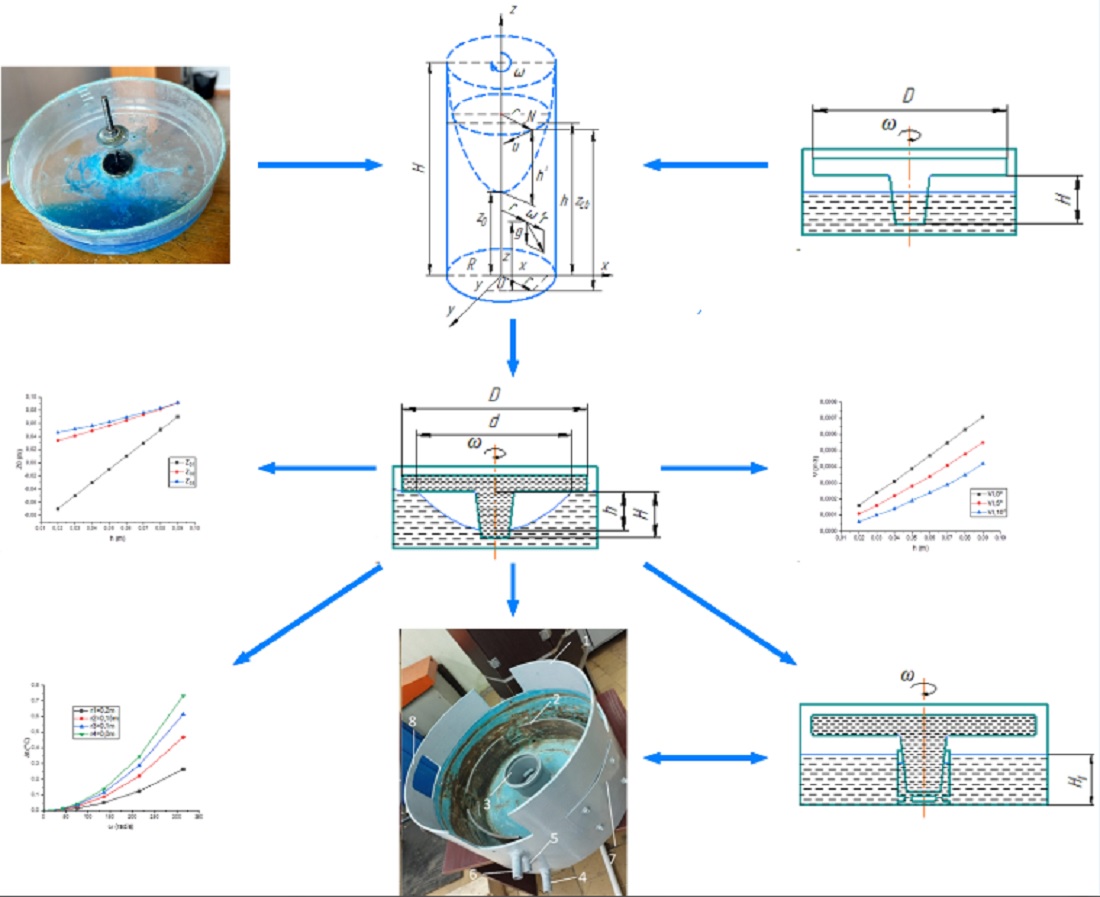
Downloads
Published
How to Cite
Issue
Section
License
Copyright (c) 2024 Bekbolat Nussupbekov, Yerlan Oshanov, Mihail Ovcharov, Moldir Duisenbayeva, Adilzada Sharzadin, Aitkul Kongyrbayeva, Makpal Amanzholova

This work is licensed under a Creative Commons Attribution 4.0 International License.
The consolidation and conditions for the transfer of copyright (identification of authorship) is carried out in the License Agreement. In particular, the authors reserve the right to the authorship of their manuscript and transfer the first publication of this work to the journal under the terms of the Creative Commons CC BY license. At the same time, they have the right to conclude on their own additional agreements concerning the non-exclusive distribution of the work in the form in which it was published by this journal, but provided that the link to the first publication of the article in this journal is preserved.
A license agreement is a document in which the author warrants that he/she owns all copyright for the work (manuscript, article, etc.).
The authors, signing the License Agreement with TECHNOLOGY CENTER PC, have all rights to the further use of their work, provided that they link to our edition in which the work was published.
According to the terms of the License Agreement, the Publisher TECHNOLOGY CENTER PC does not take away your copyrights and receives permission from the authors to use and dissemination of the publication through the world's scientific resources (own electronic resources, scientometric databases, repositories, libraries, etc.).
In the absence of a signed License Agreement or in the absence of this agreement of identifiers allowing to identify the identity of the author, the editors have no right to work with the manuscript.
It is important to remember that there is another type of agreement between authors and publishers – when copyright is transferred from the authors to the publisher. In this case, the authors lose ownership of their work and may not use it in any way.