Implementation of reengineering technology in the technological preparation for general aviation airplane wing tip manufacturing based on the construction of a digital mock-up
DOI:
https://doi.org/10.15587/1729-4061.2024.311478Keywords:
technological preparation of production, reverse engineering, digital mock-up, 3D scanning, geometric accuracy, aerodynamic airfoilAbstract
The object of this study is the technological preparation of the production of a light aircraft wing using reverse engineering technology. The subject of research is a quality indicator – the geometric accuracy of manufacturing the convex-concave parts of aerospace technology. Calculations of geometric accuracy were performed for the program-instrumental method of co-ordination. As the experimental part it was taken the worn out wing tip of a light aircraft. The following results were obtained. An approach for specifying the aerodynamic airfoil and cross sections of the wing tip when constructing its digital model has been proposed. A 3D scanning of the wing tip with the formation of a digital portrait in STL format, as well as its refinement into a STEP format, using organic and mechanical methods, was accomplished. A digital mock-up of the wing tip was built taking into account the geometry of the aerodynamic airfoil in cross sections as well as a digital mock-up of the form (mould) for its manufacture according to the polygonal model, which was created by the organic method due to it had the highest dimensional accuracy. It was determined that the maximum deviation of the actual wing contour from the theoretical one was as follows: the upper deviation was 0.84 mm, the lower deviation was –0.65 mm. The maximum deviation of the actual wing contour from the theoretical one was ±0.3 mm. The expected (calculated) errors did not exceed the specified value of the tolerance on the wing outer contour that equal to ±1.0 mm, thus, the adopted method of assembling the wing under the conditions of co-ordination by the program-instrumental method ensured the specified geometric accuracy. The results of experimental studies confirmed the adequacy of the proposed approach for determining the aerodynamic airfoil of the cross-sections of the digital mock-up of convex-concave parts for aerospace technology during their technological preparation for production with the use of reverse engineering.
References
- Alcácer, V., Cruz-Machado, V. (2019). Scanning the Industry 4.0: A Literature Review on Technologies for Manufacturing Systems. Engineering Science and Technology, an International Journal, 22 (3), 899–919. https://doi.org/10.1016/j.jestch.2019.01.006
- Stojkic, Z., Culjak, E., Saravanja, L. (2020). 3D Measurement - Comparison of CMM and 3D Scanner. Proceedings of the 31st International DAAAM Symposium 2020, 0780–0787. https://doi.org/10.2507/31st.daaam.proceedings.108
- Javaid, M., Haleem, A., Pratap Singh, R., Suman, R. (2021). Industrial perspectives of 3D scanning: Features, roles and it’s analytical applications. Sensors International, 2, 100114. https://doi.org/10.1016/j.sintl.2021.100114
- Buonamici, F., Carfagni, M., Furferi, R., Governi, L., Lapini, A., Volpe, Y. (2017). Reverse engineering modeling methods and tools: a survey. Computer-Aided Design and Applications, 15 (3), 443–464. https://doi.org/10.1080/16864360.2017.1397894
- Saiga, K., Ullah, A. S., Kubo, A., Tashi. (2021). A Sustainable Reverse Engineering Process. Procedia CIRP, 98, 517–522. https://doi.org/10.1016/j.procir.2021.01.144
- Onopchenko, A., Horbachov, O., Sorokin, V., Dudukalov, Y., Kurin, M. (2022). Optimal Conditions for Deformation of Stamping-Drawing Process from Aviation Materials. Advanced Manufacturing Processes IV, 109–118. https://doi.org/10.1007/978-3-031-16651-8_11
- Onopchenko, A. V., Kurin, M. O., Shyrokyi, Yu. V. (2024). Ensuring Quality of Stamping Sheet Aviation Parts. Progress in Physics of Metals, 25 (2), 320–363. https://doi.org/10.15407/ufm.25.02.320
- Subeshan, B., Abdulaziz, A., Khan, Z., Uddin, Md. N., Rahman, M. M., Asmatulu, E. (2022). Reverse Engineering of Aerospace Components Utilizing Additive Manufacturing Technology. TMS 2022 151st Annual Meeting & Exhibition Supplemental Proceedings, 238–246. https://doi.org/10.1007/978-3-030-92381-5_21
- Helle, R. H., Lemu, H. G. (2021). A case study on use of 3D scanning for reverse engineering and quality control. Materials Today: Proceedings, 45, 5255–5262. https://doi.org/10.1016/j.matpr.2021.01.828
- Andrei, I.-C., Stroe, G.-L., Berbente, S., Stoica, G. F., Crisan, N., Prisecaru, D. et al. (2023). Applications of design and reverse engineering for the development of digital and smart tools for composite additive manufacturing. INCAS BULLETIN, 15 (4), 19–34. https://doi.org/10.13111/2066-8201.2023.15.4.2
- Faizin, M., Paryanto, P., Cahyo, N., Rusnaldy, R. (2024). Investigating the accuracy of boat propeller blade components with reverse engineering approach using photogrammetry method. Results in Engineering, 22, 102293. https://doi.org/10.1016/j.rineng.2024.102293
- Zhang, Z., Zhao, M., Shen, Z., Wang, Y., Jia, X., Yan, D.-M. (2024). Interactive reverse engineering of CAD models. Computer Aided Geometric Design, 111, 102339. https://doi.org/10.1016/j.cagd.2024.102339
- Maiorova, K., Kapinus, O., Skyba, O. (2024). Study of the features of permanent and usual reverse-engineering methods of details of complex shapes. Technology Audit and Production Reserves, 1 (1 (75)), 19–25. https://doi.org/10.15587/2706-5448.2024.297768
- Kyaw, A. C., Nagengast, N., Usma-Mansfield, C., Fuss, F. K. (2023). A Combined Reverse Engineering and Multi-Criteria Decision-Making Approach for Remanufacturing a Classic Car Part. Procedia CIRP, 119, 222–228. https://doi.org/10.1016/j.procir.2023.02.133
- Zhang, C., Pinquié, R., Polette, A., Carasi, G., De Charnace, H., Pernot, J.-P. (2023). Automatic 3D CAD models reconstruction from 2D orthographic drawings. Computers & Graphics, 114, 179–189. https://doi.org/10.1016/j.cag.2023.05.021
- Maiorova, K., Kapinus, O., Nikichanov, V., Skyba, O., Suslov, A. (2024). Devising a methodology for prototyping convex-concave parts using reverse-engineering technology providing the predefined geometric accuracy of their manufacturing. Engineering Technological Systems, 4 (1 (130)), 112–120. https://doi.org/10.15587/1729-4061.2024.308047
- Pliuhin, V., Zaklinskyy, S., Plankovskyy, S., Tsegelnyk, Y., Aksonov, O., Kombarov, V. (2023). A Digital Twin Design of Induction Motor with Squirrel-Cage Rotor for Insulation Condition Prediction. International Journal of Mechatronics and Applied Mechanics, 14, 185–191. https://doi.org/10.17683/ijomam/issue14.22
- Phua, A., Davies, C. H. J., Delaney, G. W. (2022). A digital twin hierarchy for metal additive manufacturing. Computers in Industry, 140, 103667. https://doi.org/10.1016/j.compind.2022.103667
- Technical specifications. Artec 3D. Available at: https://www.artec3d.com/portable-3d-scanners/artec-spider#specifications
- Agoston, M. K. (2005). Computer Graphics and Geometric Modelling. Springer-Verlag London, 908. https://doi.org/10.1007/b138805
- Langetepe, E., Zachmann, G. (2006). Geometric Data Structures for Computer Graphics. A K Peters/CRC Press. https://doi.org/10.1201/9780367803735
- Agarwal, P. K., Arge, L., Danner, A. (2006). From Point Cloud to Grid DEM: A Scalable Approach. Progress in Spatial Data Handling, 771–788. https://doi.org/10.1007/3-540-35589-8_48
- Aboshweita, I. M., Masood, M. A., Idris, A. A. M., Abotbina, W. (2024). Evaluation of the Freeform Feature of Solid works Parametric. International Journal of Latest Engineering and Management Research (IJLEMR), 9 (5), 35–44. https://doi.org/10.56581/ijlemr.9.05.35-44
- Pajerová, N., Koptiš, M. (2024). Shape functions to scanner comparison. The International Journal of Advanced Manufacturing Technology, 132 (7-8), 3889–3902. https://doi.org/10.1007/s00170-024-13520-z
- Sullivan, J. M. (2008). Curvatures of Smooth and Discrete Surfaces. Discrete Differential Geometry, 175–188. https://doi.org/10.1007/978-3-7643-8621-4_9
- Burns, M. (1993). Automated Fabrication: Improving Productivity in Manufacturing. PTR Prentice Hall, 369.
- Szilvśi-Nagy, M., Mátyási, Gy. (2003). Analysis of STL files. Mathematical and Computer Modelling, 38 (7-9), 945–960. https://doi.org/10.1016/s0895-7177(03)90079-3
- Airfoil Tools. Available at: http://airfoiltools.com/
- Krivov, G. A., Matvienko, V. A., Vorobev, Yu. A. (2007). Tehnologiya sborki uzlov i agregatov planera samoleta s ispolzovaniem otverstiy v kachestve sborochnyh baz: SOU MPP 49.035-90:2007. Kyiv, 156.
- Sikulskiy, V., Boborykin, Yu., Vasilchenko, S., Pyankov, A., Demenko, V. (2006). Technology of airplane and helicopter manufacturing. Fundamentals of aircraft manufacturing. Kharkiv: National Aerospace University «Kharkiv Aviation Institute», 206.
- Pekarsh, A. I., Tarasov, Yu. M., Krivov, G. A. et al. (2006). Sovremennye tehnologii agregatno-sborochnogo proizvodstva samoletov. Moscow: Agraf-press, 304.
- Kryvtsov, V. S., Vorobiov, Yu. A., Bukin, Yu. M. et al. (2009). Tekhnolohiya vyrobnytstva litalnykh aparativ (skladalno-montazhni roboty). Kharkiv: Nats. aerokosm. un-t «Khark. aviats. in-t», 80.
- Sikulskiy, V., Maiorova, K., Vorobiov, I., Boiko, M., Komisarov, O. (2022). Implementation of reengineering technology to reduce the terms of the technical preparation of manufacturing of aviation technology assemblies. Eastern-European Journal of Enterprise Technologies, 3 (1 (117)), 25–32. https://doi.org/10.15587/1729-4061.2022.258550
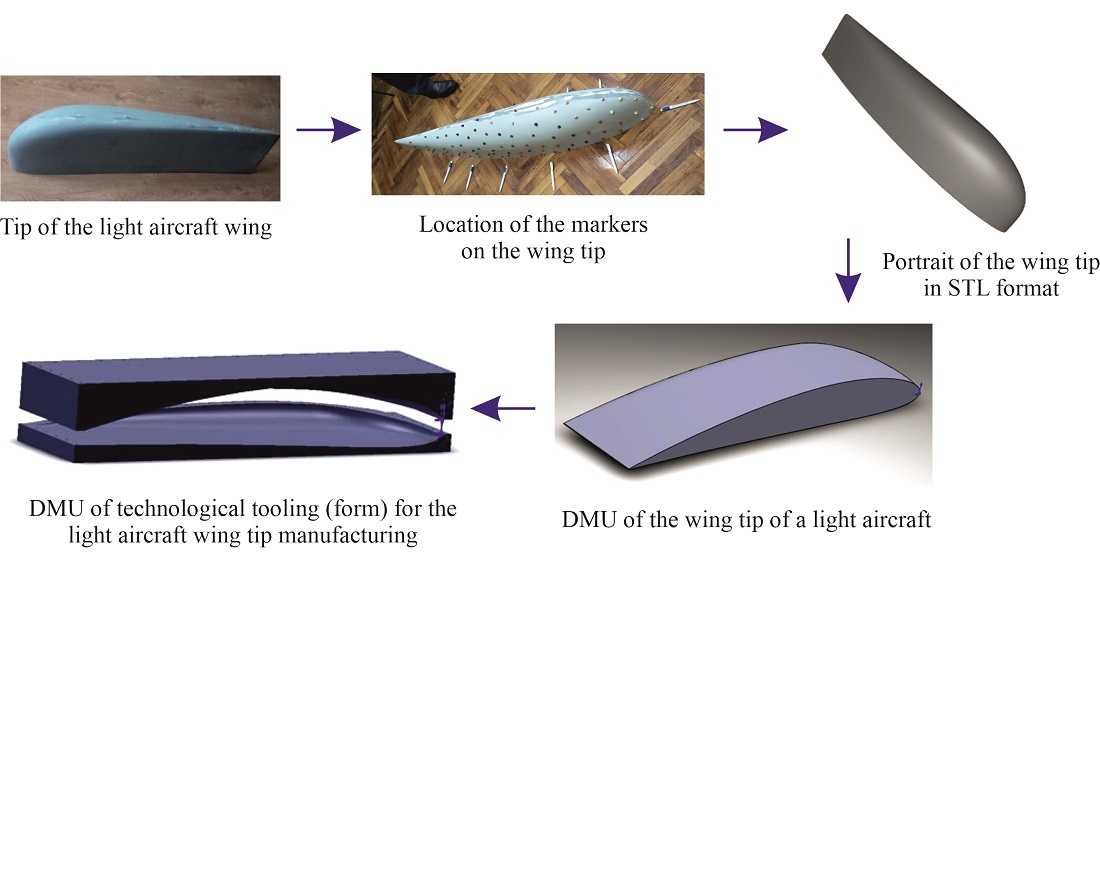
Downloads
Published
How to Cite
Issue
Section
License
Copyright (c) 2024 Kateryna Maiorova, Viacheslav Nikichanov, Ihor Lysochenko, Svitlana Myronova

This work is licensed under a Creative Commons Attribution 4.0 International License.
The consolidation and conditions for the transfer of copyright (identification of authorship) is carried out in the License Agreement. In particular, the authors reserve the right to the authorship of their manuscript and transfer the first publication of this work to the journal under the terms of the Creative Commons CC BY license. At the same time, they have the right to conclude on their own additional agreements concerning the non-exclusive distribution of the work in the form in which it was published by this journal, but provided that the link to the first publication of the article in this journal is preserved.
A license agreement is a document in which the author warrants that he/she owns all copyright for the work (manuscript, article, etc.).
The authors, signing the License Agreement with TECHNOLOGY CENTER PC, have all rights to the further use of their work, provided that they link to our edition in which the work was published.
According to the terms of the License Agreement, the Publisher TECHNOLOGY CENTER PC does not take away your copyrights and receives permission from the authors to use and dissemination of the publication through the world's scientific resources (own electronic resources, scientometric databases, repositories, libraries, etc.).
In the absence of a signed License Agreement or in the absence of this agreement of identifiers allowing to identify the identity of the author, the editors have no right to work with the manuscript.
It is important to remember that there is another type of agreement between authors and publishers – when copyright is transferred from the authors to the publisher. In this case, the authors lose ownership of their work and may not use it in any way.