Identifying patterns in the structural-phase transformations when processing oxide doped waste with the use of carbon reducer
DOI:
https://doi.org/10.15587/1729-4061.2024.313449Keywords:
oxide man-made waste, high-speed steel, slag, carbon reduction, structural-phase transformationsAbstract
The object of this study is the structural and phase transformations during the carbon reduction of tungsten high-speed steel slag in order to obtain a resource-saving alloying additive. The problem is the loss of precious elements when obtaining and using alloying material from man-made raw materials. Solving the problem is related to the definition of technological parameters to enable the reduction of losses of the corresponding elements. As a result of increasing the degree of scale reduction from 33 % to 72 % and 85 %, the strengthening of the manifestation of the solid solution of carbon and alloying elements in α-Fe relative to FeWO4, FeO and Fe3O4 was revealed. Fe3C, WC, W2C, FeW3C, Fe3W3C, Fe6W6C, VC, V2C, Cr3C2, Cr7C3 and Cr23C6 also appeared. Along with this, rounded and multifaceted particles with different chemical composition and the formation of a spongy microstructure were found. It was established that the most acceptable degree of recovery is 85 %. But achieving a recovery rate of 72 % is also sufficient. This is explained by the fact that the residual carbon in the carbides provides an increased reducing capacity, which is realized during the further reduction of oxides in the liquid metal during alloying. The spongy microstructure results in faster dissolution in contrast to standard ferroalloys, which provides a reduction in melting time while reducing spent resources. No phases with an increased tendency to sublimation were found in the obtained alloying material. That is, no additional conditions are needed that restrain the loss of alloying elements during evaporation with a gaseous phase, which provides an increase in the degree of extraction of the corresponding elements. The properties of the resulting alloying material make it possible to use it in metallurgical production when smelting alloyed steel grades in an electric arc furnace, the composition of which does not have strict restrictions on the carbon content
References
- Henckens, M. L. C. M., van Ierland, E. C., Driessen, P. P. J., Worrell, E. (2016). Mineral resources: Geological scarcity, market price trends, and future generations. Resources Policy, 49, 102–111. https://doi.org/10.1016/j.resourpol.2016.04.012
- Petryshchev, A., Milko, D., Borysov, V., Tsymbal, B., Hevko, I., Borysova, S., Semenchuk, A. (2019). Studying the physicalchemical transformations at resourcesaving reduction melting of chrome–nickelcontaining metallurgical waste. Eastern-European Journal of Enterprise Technologies, 2 (12 (98)), 59–64. https://doi.org/10.15587/1729-4061.2019.160755
- Sekiguchi, N. (2017). Trade specialisation patterns in major steelmaking economies: the role of advanced economies and the implications for rapid growth in emerging market and developing economies in the global steel market. Mineral Economics, 30 (3), 207–227. https://doi.org/10.1007/s13563-017-0110-2
- Mechachti, S, Benchiheub, O., Serrai, S., Shalabi, M. (2013). Preparation of iron Powders by Reduction of Rolling Mill Scale. International Journal of Scientific & Engineering Research, 4 (5), 1467–1472. Available at: https://www.ijser.org/researchpaper/Preparation-of-Iron-Powders-by-Reduction-Rolling-Mill-Scale.pdf
- Grigor’ev, S. M., Petrishchev, A. S. (2012). Assessing the phase and structural features of the scale on P6M5Φ3 and P12M3K5Φ2 steel. Steel in Translation, 42 (3), 272–275. https://doi.org/10.3103/s0967091212030059
- Smirnov, A., Petryshchev, A., Bilko, T., Andreev, A., Semenko, A., Skorobagatko, Y. (2023). Development of the Recycling of Alloyed Metallurgical Waste: Features of Phase and Structural Transformations. Minerals, 13 (9), 1171. https://doi.org/10.3390/min13091171
- Tsymbal, B., Petryshchev, A., Anrieieva, L., Sharovatova, O. (2022). Improving Occupational Safety and Health in the Processing of Metallurgical Waste and Features of their Microstructure Transformation. Key Engineering Materials, 925, 187–196. https://doi.org/10.4028/p-f9x0w1
- Borysov, V., Torubara, O., Volokh, V., Poliakov, A., Yamshinskij, M., Lukianenko, I. et al. (2022). Identifying features in the structural and phase composition of the products of recycling of the scale of high-speed cutting steel by carbon thermal reduction. Eastern-European Journal of Enterprise Technologies, 6 (12 (120)), 46–51. https://doi.org/10.15587/1729-4061.2022.269507
- Kozyrev, N. A., Galevsky, G. V., Valuev, D. V., Shurupov, V. M., Kozyreva, O. E. (2015). Surfacing With Tungsten-containing Ores. IOP Conference Series: Materials Science and Engineering, 91, 012009. https://doi.org/10.1088/1757-899x/91/1/012009
- Islam, M., Martinez-Duarte, R. (2017). A sustainable approach for tungsten carbide synthesis using renewable biopolymers. Ceramics International, 43 (13), 10546–10553. https://doi.org/10.1016/j.ceramint.2017.05.118
- Hryhoriev, S., Petryshchev, A., Sergienko, O., Milko, D., Stepanenko, A., Kozhemiakin, G. et al. (2018). The study of physicalchemical patterns of resourcesaving recycling of tungstencontaining ore raw materials by solidphase reduction. Eastern-European Journal of Enterprise Technologies, 1 (12 (91)), 4–9. https://doi.org/10.15587/1729-4061.2018.122743
- Zhao, L., Wang, L., Chen, D., Zhao, H., Liu, Y., Qi, T. (2015). Behaviors of vanadium and chromium in coal-based direct reduction of high-chromium vanadium-bearing titanomagnetite concentrates followed by magnetic separation. Transactions of Nonferrous Metals Society of China, 25 (4), 1325–1333. https://doi.org/10.1016/s1003-6326(15)63731-1
- Chen, S. Y., Chu, M. S. (2014). A new process for the recovery of iron, vanadium, and titanium from vanadium titanomagnetite. The Journal of the Southern African Institute of Mining and Metallurgy, 114, 481–487. Available at: https://www.scielo.org.za/pdf/jsaimm/v114n6/14.pdf
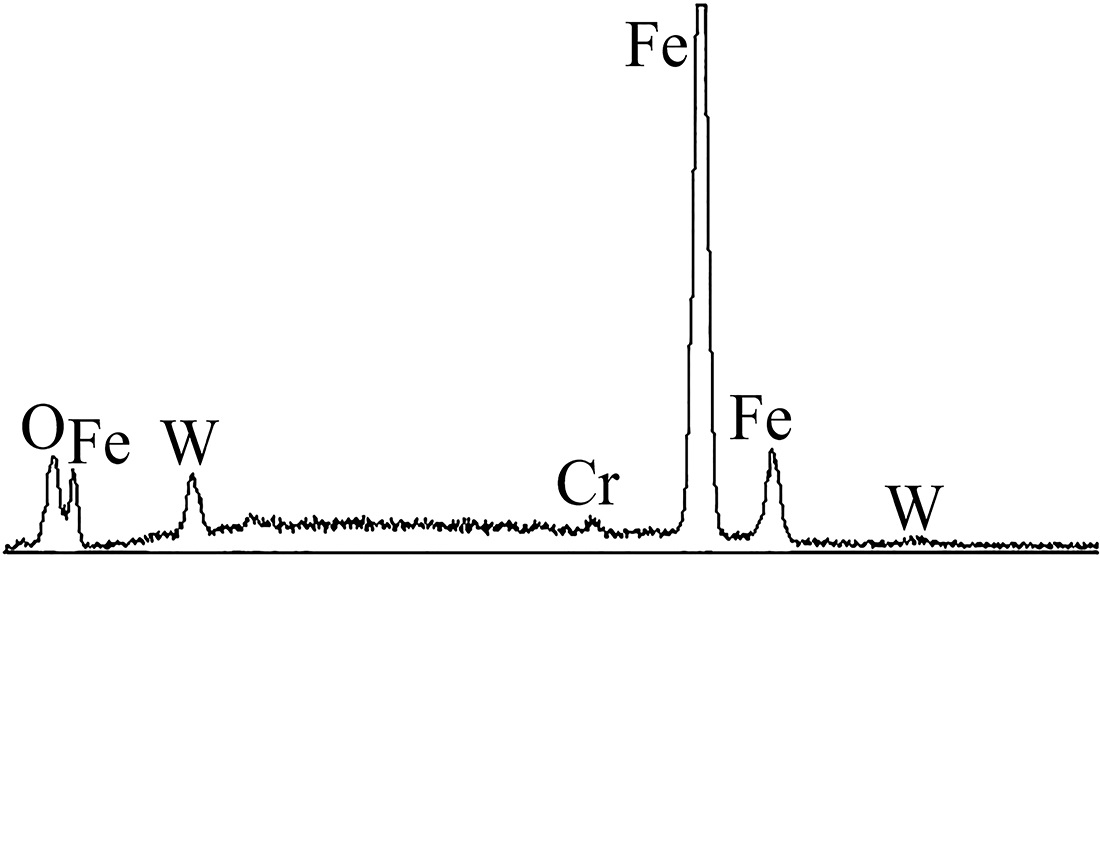
Downloads
Published
How to Cite
Issue
Section
License
Copyright (c) 2024 Anatolii Poliakov, Vadym Volokh, Andrey Andreev, Victor Rebenko, Viacheslav Kurlov, Mykhail Yamshinskij, Ivan Lukianenko, Dmytro Ivanchenko, Dmytro Zhuravel, Iryna Kovalenko

This work is licensed under a Creative Commons Attribution 4.0 International License.
The consolidation and conditions for the transfer of copyright (identification of authorship) is carried out in the License Agreement. In particular, the authors reserve the right to the authorship of their manuscript and transfer the first publication of this work to the journal under the terms of the Creative Commons CC BY license. At the same time, they have the right to conclude on their own additional agreements concerning the non-exclusive distribution of the work in the form in which it was published by this journal, but provided that the link to the first publication of the article in this journal is preserved.
A license agreement is a document in which the author warrants that he/she owns all copyright for the work (manuscript, article, etc.).
The authors, signing the License Agreement with TECHNOLOGY CENTER PC, have all rights to the further use of their work, provided that they link to our edition in which the work was published.
According to the terms of the License Agreement, the Publisher TECHNOLOGY CENTER PC does not take away your copyrights and receives permission from the authors to use and dissemination of the publication through the world's scientific resources (own electronic resources, scientometric databases, repositories, libraries, etc.).
In the absence of a signed License Agreement or in the absence of this agreement of identifiers allowing to identify the identity of the author, the editors have no right to work with the manuscript.
It is important to remember that there is another type of agreement between authors and publishers – when copyright is transferred from the authors to the publisher. In this case, the authors lose ownership of their work and may not use it in any way.