Identifying failure factors due to corrosion erosion on pressured steam pipe elbow in geothermal power plant
DOI:
https://doi.org/10.15587/1729-4061.2024.313972Keywords:
corrosion erosion, elbow pipe, turbulence, tubercles, fibrous fractures, thinning thicknessAbstract
This paper presents the findings of a corrosion erosion failure analysis of elbow pipe materials used to flow high-pressure water from underground. The failed elbow pipe material was above the wellhead forming a straight line in the longitudinal direction with a pipe length of 6200 feet below the ground surface. The working fluid in the elbow pipe was 25 % steam and 75 % water, flowing in the elbow pipe with a media flow rate of 180 tons per hour, a pressure of 22 bar, and a temperature of 220 °C. Elbow tubes were made of low carbon steel with Standard ASTM A234 having an outer diameter of 304.8 mm and a wall thickness of 9.271 mm. Macroscopic testing, chemical composition analysis, metallographic testing, hardness testing, X-ray diffraction testing, SEM, and EDS are a few of the test types conducted. The study's findings showed that the elbow tubes experienced a thinning process on the inner wall of the outer curvature side with a rough and wavy surface texture or appearance. This type of failure is known as erosion-corrosion. The level of erosion-corrosion failure that occurs is greatly influenced by the pH of the fluid being flowed reaching 2.67–2.91, this is due to the very high Cl- of 1290 ppm, so the higher the rate of erosion-corrosion that occurs. These materials are the most popular and widely used in the oil and gas sector. However, this pipe has weaknesses because it is susceptible to erosion-corrosion Therefore, it is very important to choose the right material, namely, a material that is resistant to erosion-corrosion
References
- Tawancy, H. M., Al-Hadhrami, L. M., Al-Yousef, F. K. (2013). Analysis of corroded elbow section of carbon steel piping system of an oil–gas separator vessel. Case Studies in Engineering Failure Analysis, 1 (1), 6–14. https://doi.org/10.1016/j.csefa.2012.11.001
- Zhu, M., Sun, L., Ou, G., Wang, K., Wang, K., Sun, Y. (2016). Erosion corrosion failure analysis of the elbow in sour water stripper overhead condensing reflux system. Engineering Failure Analysis, 62, 93–102. https://doi.org/10.1016/j.engfailanal.2016.01.002
- Kusmono, Khasani (2017). Analysis of a failed pipe elbow in geothermal production facility. Case Studies in Engineering Failure Analysis, 9, 71–77. https://doi.org/10.1016/j.csefa.2017.08.001
- Lospa, A. M., Dudu, C., Ripeanu, R. G., Dinita, A. (2019). CFD Evaluation of sand erosion wear rate in pipe bends used in technological installations. IOP Conference Series: Materials Science and Engineering, 514 (1), 012009. https://doi.org/10.1088/1757-899x/514/1/012009
- Khan, R., Ya, H. H., Pao, W., Khan, A. (2019). Erosion–Corrosion of 30°, 60°, and 90° Carbon Steel Elbows in a Multiphase Flow Containing Sand Particles. Materials, 12 (23), 3898. https://doi.org/10.3390/ma12233898
- Zeng, L., Zhang, G. A., Guo, X. P. (2014). Erosion–corrosion at different locations of X65 carbon steel elbow. Corrosion Science, 85, 318–330. https://doi.org/10.1016/j.corsci.2014.04.045
- Dooley, R. B. (2008). Flow-accelerated corrosion in fossil and combined cycle/HRSG plants. Power Plant Chemistry, 10 (2), 68–89. Available at: http://competitivepower.us/pub/pdfs/flow-accelerated-corrosion-in-fossil-and-cc-hrsg-plants.pdf
- Haribhakti, P., Joshi, P. B., Kumar, R. (2018). Failure Investigation of Boiler Tubes. ASM International. https://doi.org/10.31399/asm.tb.fibtca.9781627082532
- Tomarov, G. V., Kolesnikov, D. V., Semenov, V. N., Podverbny, V. M., Shipkov, A. A. (2015). Prevention of Corrosion and Scaling in Geothermal Power Plants Equipment. Proceedings World Geothermal Congress 2015. Available at: https://www.geothermal-energy.org/pdf/IGAstandard/WGC/2015/27032.pdf
- Nogara, J., Zarrouk, S. J. (2018). Corrosion in geothermal environment Part 2: Metals and alloys. Renewable and Sustainable Energy Reviews, 82, 1347–1363. https://doi.org/10.1016/j.rser.2017.06.091
- Adnyana, D. N. (2020). Cavitation-erosion study in elbow tubes of a low-pressure evaporator outlet header. Metalurgi, 35 (1), 33. https://doi.org/10.14203/metalurgi.v35i1.561
- Chen, J., Zhang, Q., Li, Q., Fu, S., Wang, J. (2014). Corrosion and tribocorrosion behaviors of AISI 316 stainless steel and Ti6Al4V alloys in artificial seawater. Transactions of Nonferrous Metals Society of China, 24 (4), 1022–1031. https://doi.org/10.1016/s1003-6326(14)63157-5
- Aribo, S., Barker, R., Hu, X., Neville, A. (2013). Erosion–corrosion behaviour of lean duplex stainless steels in 3.5% NaCl solution. Wear, 302 (1-2), 1602–1608. https://doi.org/10.1016/j.wear.2012.12.007
- Rajahram, S. S., Harvey, T. J., Walker, J. C., Wang, S. C., Wood, R. J. K. (2012). Investigation of erosion–corrosion mechanisms of UNS S31603 using FIB and TEM. Tribology International, 46 (1), 161–173. https://doi.org/10.1016/j.triboint.2011.05.012
- Jones, M., Llewellyn, R. J. (2009). Erosion–corrosion assessment of materials for use in the resources industry. Wear, 267 (11), 2003–2009. https://doi.org/10.1016/j.wear.2009.06.025
- Hussain, E. A. M., Robinson, M. J. (2007). Erosion–corrosion of 2205 duplex stainless steel in flowing seawater containing sand particles. Corrosion Science, 49 (4), 1737–1754. https://doi.org/10.1016/j.corsci.2006.08.023
- Wood, R. J. K. (2006). Erosion–corrosion interactions and their effect on marine and offshore materials. Wear, 261 (9), 1012–1023. https://doi.org/10.1016/j.wear.2006.03.033
- Neville, A., Hodgkiess, T., Dallas, J. T. (1995). A study of the erosion-corrosion behaviour of engineering steels for marine pumping applications. Wear, 186-187, 497–507. https://doi.org/10.1016/0043-1648(95)07145-8
- Watson, S. W., Friedersdorf, F. J., Madsen, B. W., Cramer, S. D. (1995). Methods of measuring wear-corrosion synergism. Wear, 181-183, 476–484. https://doi.org/10.1016/0043-1648(95)90161-2
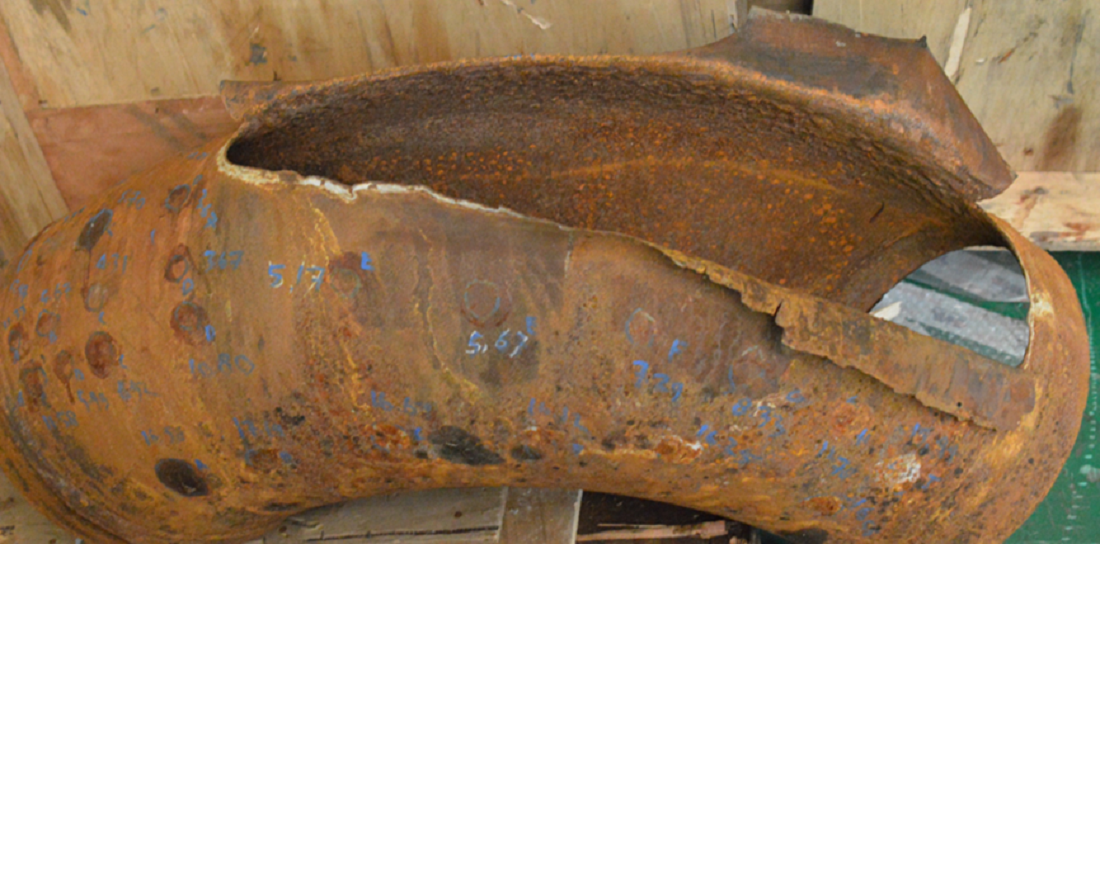
Downloads
Published
How to Cite
Issue
Section
License
Copyright (c) 2024 Iskandar Muda, Bambang Widyanto

This work is licensed under a Creative Commons Attribution 4.0 International License.
The consolidation and conditions for the transfer of copyright (identification of authorship) is carried out in the License Agreement. In particular, the authors reserve the right to the authorship of their manuscript and transfer the first publication of this work to the journal under the terms of the Creative Commons CC BY license. At the same time, they have the right to conclude on their own additional agreements concerning the non-exclusive distribution of the work in the form in which it was published by this journal, but provided that the link to the first publication of the article in this journal is preserved.
A license agreement is a document in which the author warrants that he/she owns all copyright for the work (manuscript, article, etc.).
The authors, signing the License Agreement with TECHNOLOGY CENTER PC, have all rights to the further use of their work, provided that they link to our edition in which the work was published.
According to the terms of the License Agreement, the Publisher TECHNOLOGY CENTER PC does not take away your copyrights and receives permission from the authors to use and dissemination of the publication through the world's scientific resources (own electronic resources, scientometric databases, repositories, libraries, etc.).
In the absence of a signed License Agreement or in the absence of this agreement of identifiers allowing to identify the identity of the author, the editors have no right to work with the manuscript.
It is important to remember that there is another type of agreement between authors and publishers – when copyright is transferred from the authors to the publisher. In this case, the authors lose ownership of their work and may not use it in any way.