Identifying the parameters and operation modes of the cavitation apparatus taking into account the influence of the processing material
DOI:
https://doi.org/10.15587/1729-4061.2024.314141Keywords:
cavitation apparatus, discrete-continuous model, contact zone, pressure, displacement amplitude, wave coefficient, synergy coefficientAbstract
The object of this study is dynamic pressure that takes into account the main parameters of technological process. Under real conditions of cavitation apparatus operation, a discrepancy between actual and calculated parameters of 30–50 % was found, which significantly reduces the efficiency and quality of material processing. The problem was solved through a joint study of the movement of the acoustic apparatus and the technological environment as a single structured system taking into account the influence of materials. This is a peculiarity of the approach and distinctive features of the results in comparison with existing ones, in which the research was conducted separately for the processing material and the cavitation apparatus. The model proposed in the work reflects the elastic, inertial, and dissipative parameters in the equations of motion, provided that their changes are taken into account, both in the acoustic apparatus and in the technological material. This approach has made it possible to reveal the physical essence of the interaction and analytically describe their joint movement. The resulting analytical dependences made it possible to calculate and propose numerical values of vibration amplitudes in the range of 4.0...20.0 μm, sound pressure values in the range of 5.0...30.0∙105 Pa for media with a viscosity of (10–200)∙10-3 Pa∙s. With the set value of the amplitude, it is possible to assign the necessary parameters for the implementation of the cavitation process. The developed calculation algorithm ensures the reliability of the accepted models and parameters of the cavitation apparatus. The proposed approach of joint study of the movement of the acoustic apparatus and the environment is expedient to use for the practical implementation of ultrasonic treatment. In particular, such processes as dispersion, emulsification, mixing, extraction, and others, in order to increase their efficiency
References
- Nazarenko, I., Bernyk, I. (2021). Research of the processes of acoustic cavitation technology for processing dispersed media. DYNAMIC PROCESSES IN Technological Technical Systems, 94–109. https://doi.org/10.15587/978-617-7319-49-7.ch6
- Bernyk, I., Luhovskyi, O., Nazarenko, I. (2018). Effect of rheological properties of materials on their treatment with ultrasonic cavitation. Materiali in Tehnologije, 52 (4), 465–468. https://doi.org/10.17222/mit.2017.021
- Wood, R. J., Lee, J., Bussemaker, M. J. (2017). A parametric review of sonochemistry: Control and augmentation of sonochemical activity in aqueous solutions. Ultrasonics Sonochemistry, 38, 351–370. https://doi.org/10.1016/j.ultsonch.2017.03.030
- Droździel, P., Vitenko, T., Voroshchuk, V., Narizhnyy, S., Snizhko, O. (2021). Discrete-Impulse Energy Supply in Milk and Dairy Products Processing. https://doi.org/10.20944/preprints202103.0308.v1
- Vitenko, T, Droździel, P, Horodyskyi, N. (2016). Erosive impact of vapor-gas phase on the working surface in hydrodynamic type cavitation mode. ADiagnostyka, 17 (1), 3–8. Available at: http://www.diagnostyka.net.pl/Erosive-impact-of-vapor-gas-phase-on-the-working-surface-in-hydrodynamic-type-cavitation,81492,0,2.html
- Sugita, N., Yamamoto, S., Tomioka, K., Shinshi, T. (2024). A Flexural Ultrasonic Transducer for Inducing Acoustic Cavitation on Material Surfaces. Journal of Vibration Engineering & Technologies. https://doi.org/10.1007/s42417-024-01482-1
- Movchanyuk, A., Luhovskyi, O., Fesich, V., Sushko, I., Lashchevska, N. (2020). Ultrasonic Cavitation Equipment with a Liquid Pressure Transformer. Advances in Hydraulic and Pneumatic Drives and Control 2020, 282–292. https://doi.org/10.1007/978-3-030-59509-8_25
- Pavlenko, A. M., Koshlak, H. (2021). Application of Thermal and Cavitation Effects for Heat and Mass Transfer Process Intensification in Multicomponent Liquid Media. Energies, 14 (23), 7996. https://doi.org/10.3390/en14237996
- Tong, W., Li, L. (2024). Experimental Research of Ultrasonic Cavitation Evolution Mechanism and Model Optimization of RUREMM on Cylindrical Surface. Processes, 12 (5), 884. https://doi.org/10.3390/pr12050884
- Niţoi, D., Apostolescu, Z., Petriceanu, C., Rontescu, C. (2019). Designing the ultrasonic system used in industrial air filtration based on the ultrasonic cavitation phenomenon. MATEC Web of Conferences, 290, 11009. https://doi.org/10.1051/matecconf/201929011009
- Sharifishourabi, M., Dincer, I., Mohany, A. (2024). Implementation of experimental techniques in ultrasound-driven hydrogen production: A comprehensive review. International Journal of Hydrogen Energy, 62, 1183–1204. https://doi.org/10.1016/j.ijhydene.2024.03.013
- Guo, C., Liu, J., Li, X., Yang, S. (2021). Effect of cavitation bubble on the dispersion of magnetorheological polishing fluid under ultrasonic preparation. Ultrasonics Sonochemistry, 79, 105782. https://doi.org/10.1016/j.ultsonch.2021.105782
- Park, S., Son, G. (2021). Numerical study of the effect of liquid compressibility on acoustic droplet vaporization. Ultrasonics Sonochemistry, 79, 105769. https://doi.org/10.1016/j.ultsonch.2021.105769
- Peng, K., Qu, W., Li, C. (2024). Rayleigh-Taylor instability of collapsing bubbles in cryogenic liquids. Ultrasonics Sonochemistry, 109, 106987. https://doi.org/10.1016/j.ultsonch.2024.106987
- Nazarenko, I., Dedov, O., Bernyk, I., Bondarenko, A., Zapryvoda, A., Nazarenko, M. et al.; Nazarenko, I. (Ed.) (2021). Dynamic processes in technological technical systems. Kharkiv: РС ТЕСHNOLOGY СЕNTЕR, 196. https://doi.org/10.15587/978-617-7319-49-7
- Nazarenko, I., Dedov, O., Bernyk, I., Bondarenko, A., Onyshchenko, A., Lisnevskyi, R., Slyusar, V. (2023). Determining the influence of higher harmonics of nonlinear technological load in dynamic action systems. Eastern-European Journal of Enterprise Technologies, 4 (7 (124)), 79–88. https://doi.org/10.15587/1729-4061.2023.285419
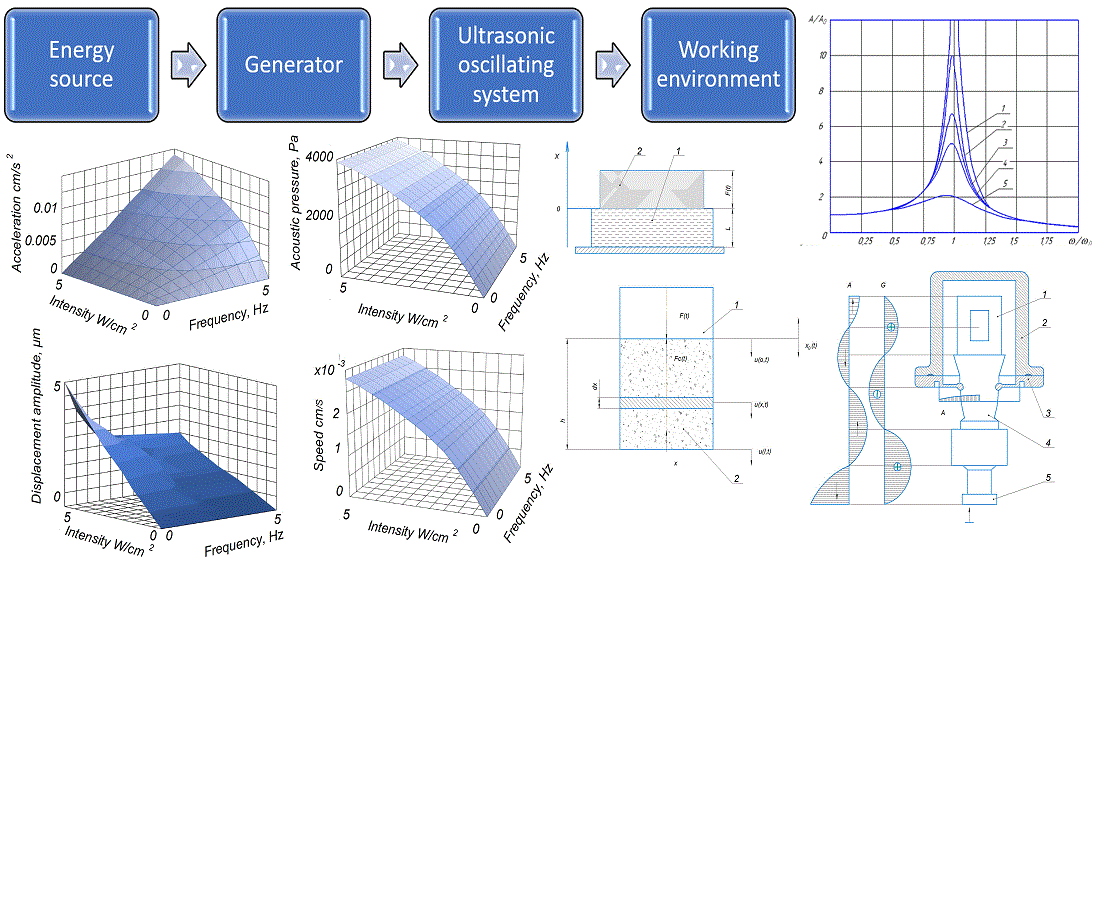
Downloads
Published
How to Cite
Issue
Section
License
Copyright (c) 2024 Iryna Bernyk, Ivan Nazarenko, Andrii Zapryvoda, Mykola Ruchynskyi, Natalia Bolharova, Tetiana Nesterenko

This work is licensed under a Creative Commons Attribution 4.0 International License.
The consolidation and conditions for the transfer of copyright (identification of authorship) is carried out in the License Agreement. In particular, the authors reserve the right to the authorship of their manuscript and transfer the first publication of this work to the journal under the terms of the Creative Commons CC BY license. At the same time, they have the right to conclude on their own additional agreements concerning the non-exclusive distribution of the work in the form in which it was published by this journal, but provided that the link to the first publication of the article in this journal is preserved.
A license agreement is a document in which the author warrants that he/she owns all copyright for the work (manuscript, article, etc.).
The authors, signing the License Agreement with TECHNOLOGY CENTER PC, have all rights to the further use of their work, provided that they link to our edition in which the work was published.
According to the terms of the License Agreement, the Publisher TECHNOLOGY CENTER PC does not take away your copyrights and receives permission from the authors to use and dissemination of the publication through the world's scientific resources (own electronic resources, scientometric databases, repositories, libraries, etc.).
In the absence of a signed License Agreement or in the absence of this agreement of identifiers allowing to identify the identity of the author, the editors have no right to work with the manuscript.
It is important to remember that there is another type of agreement between authors and publishers – when copyright is transferred from the authors to the publisher. In this case, the authors lose ownership of their work and may not use it in any way.