Development of a mobile hydraulic press machine using finite element analysis
DOI:
https://doi.org/10.15587/1729-4061.2025.316584Keywords:
hydraulic press machine, stress distribution, total deformation, structural optimizationAbstract
Mobile hydraulic press machines provide significant benefits in field-based applications such as construction, agriculture, and maintenance, all of which mobility and versatility are of utmost importance. The design and development of mobile hydraulic press machines are responsible for these advantages, which can be attributed to them. The primary focus of this study is to evaluate the structural performance of a mobile hydraulic press machine while it is subjected to operational loads. Formulation, modeling, and simulation of the machine are all carried out with the assistance of finite element analysis (FEA). Cutting-edge computer-aided design (CAD) technologies were applied to develop a model of the machine. This model was then analyzed to ascertain essential parameters such as the distribution of stress, the overall deformation, and the safety aspects. The data imply that the hydraulic telescopic cylinder, press machine frame, waste press, and waste press door all perform within an acceptable safety factor larger than two. In addition, the stress levels are lower than 550 MPa, and the deformation values vary from 0.20 mm to 0.40 mm, significantly lower than the standards for the material. When doing the safety factor analysis, it is essential to locate areas that could benefit from a slight strengthening to enhance the product's dependability and durability. In addition, the waste press section had an excessively planned safety margin, which indicated room for improvement in material optimization. The structural integrity of the machine is ensured by this all-encompassing approach, which also provides the machine's efficiency and versatility for various field applications. Future attempts to enhance the concept will focus on prototyping and testing
References
- Awasthi, A., Saxena, K. K., Arun, V. (2021). Sustainable and smart metal forming manufacturing process. Materials Today: Proceedings, 44, 2069–2079. https://doi.org/10.1016/j.matpr.2020.12.177
- Lu, X., Huang, M. (2018). Modeling, Analysis and Control of Hydraulic Actuator for Forging. Springer Singapore. https://doi.org/10.1007/978-981-10-5583-6
- Khatib, M. I., Ahmed, R. Z., Uddin, M. S., Abdul Rahman, M., Shareef, M. R., Akber, S. et al. (2020). Design and Fabrication of 5 Ton Hydraulic Press Machine. International Journal of Scientific Research in Science, Engineering and Technology, 7 (2), 22–30. https://doi.org/10.32628/ijsrset207210
- Valldecabres Pérez, C. (2017). Design of a modular and transportable product. Universitat Politècnica de València. Available at: http://hdl.handle.net/10251/144745
- Werner, C. D. M. (2013). Transformable and transportable architecture: analysis of buildings components and strategies for project design. Barcelona.
- Van Hieu, T., Hong, N. T. (2024). Mechanical Engineering Excellence: Design and Optimization of Two-Dimensional Fatigue Testing Machines. Quarterly Journal of Emerging Technologies and Innovations, 9 (1). Available at: https://vectoral.org/index.php/QJETI/article/view/62
- Ashby, M. F., Johnson, K. (2013). Materials and design: the art and science of material selection in product design. Butterworth-Heinemann. https://doi.org/10.1016/c2011-0-05518-7
- Dyshyn, O., Habibov, I., Suleymanova, A., Abasova, S., Malikov, R., Khankishiyeva, T. (2023). Identifying of the mechanism formation of a natural nanocomposite in polymer composite materials. Eastern-European Journal of Enterprise Technologies, 2 (6 (122)), 24–31. https://doi.org/10.15587/1729-4061.2023.277587
- Soori, M., Jough, F. K. G. (2024). Artificial Intelligent in Optimization of Steel Moment Frame Structures: A Review. International Journal of Structural and Construction Engineering, 18 (3). Available at: https://www.researchgate.net/publication/379372249_Artificial_Intelligent_in_Optimization_of_Steel_Moment_Frame_Structures_A_Review
- Havrylenko, O., Kulinich, S. (2019). Analyzing an error in the synchronization of hydraulic motor speed under transient operating conditions. Eastern-European Journal of Enterprise Technologies, 4 (7 (100)), 30–37. https://doi.org/10.15587/1729-4061.2019.175033
- Kurowski, P. M. (2022). Finite element analysis for design engineers. SAE International. https://doi.org/10.4271/9781468605365
- Li, H., Zeng, J., Almadhor, A., Riahi, A., Almujibah, H., Abbas, M. et al. (2024). A study on improving energy flexibility in building engineering through generalized prediction models: Enhancing local bearing capacity of concrete for engineering structures. Engineering Structures, 303, 117051. https://doi.org/10.1016/j.engstruct.2023.117051
- Vaishnav, A., Lathiya, P., Sarvaiya, M. (2016). Design optimization of hydraulic press plate using finite element analysis. International Journal of Engineering Research and Applications, 6 (5), 58–66. Available at: https://www.researchgate.net/publication/305411837_Design_Optimization_of_Hydraulic_Press_Plate_using_Finite_Element_Analysis
- Luo, J., Qin, J., Qin, G. (2018). Research on Mechanical Characteristics and Optimization of Important Parts of Hydraulic Press Based on Finite Element in Slow Loading Condition. Proceedings of the International Symposium on Big Data and Artificial Intelligence, 178–181. https://doi.org/10.1145/3305275.3305310
- Fadlullah, Y. A., Yahya, M. Y. D., Setiawan, R. J., Solekhan, I., Ma’ruf, K. (2024). Optimizing the Design Structure of Recycled Aluminum Pressing Machine using the Finite Element Method. Pakistan Journal of Engineering and Technology, 7 (01), 13–21. https://doi.org/10.51846/vol7iss01pp13-21
- Groh, R. M. J., Pirrera, A. (2019). On the role of localizations in buckling of axially compressed cylinders. Proceedings of the Royal Society A: Mathematical, Physical and Engineering Sciences, 475 (2224), 20190006. https://doi.org/10.1098/rspa.2019.0006
- Nie, S., Huo, L., Ji, H., Lan, Y., Wu, Z. (2022). Bending deformation characteristics of high-pressure soft actuator driven by water-hydraulics for underwater manipulator. Sensors and Actuators A: Physical, 344, 113736. https://doi.org/10.1016/j.sna.2022.113736
- Boye, T., Adeyemi, O., Emagbetere, E. (2017). Design and finite element analysis of double-acting, double-ends hydraulic cylinder for industrial automation application. American Journal of Engineering Research (AJER), 6 (3), 131–138. Available at: https://www.researchgate.net/profile/Thankgod-Boye/publication/315658107_Design_and_Finite_Element_Analysis_of_Double_-_Acting_Double_-_Ends_Hydraulic_Cylinder_for_Industrial_Automation_Application/links/5f4caa5e458515a88b961113/Design-and-Finite-Element-Analysis-of-Double-Acting-Double-Ends-Hydraulic-Cylinder-for-Industrial-Automation-Application.pdf
- Vaezi, H., Moonaghi, H. K., Golbaf, R. (2019). Design-Based Research: Definition, Characteristics, Application and Challenges. Journal of Education in Black Sea Region, 5 (1), 26–35. https://doi.org/10.31578/jebs.v5i1.185
- Zindani, D., Maity, S. R., Bhowmik, S. (2020). Decision making tools for optimal material selection: A review. Journal of Central South University, 27 (3), 629–673.https://doi.org/10.1007/s11771-020-4322-1
- Hu, K., Lin, K., Gu, D., Yang, J., Wang, H., Yuan, L. (2019). Mechanical properties and deformation behavior under compressive loading of selective laser melting processed bio-inspired sandwich structures. Materials Science and Engineering: A, 762, 138089. https://doi.org/10.1016/j.msea.2019.138089
- Alves, A. C., Alves, S., Peixinho, N., Carneiro, V. H., Mendonça, J. P., Rodrigues, O. (2022). Simulation Strategies for Dynamic and Static Behaviour of Composite Beams. Materials Design and Applications IV, 29–45. https://doi.org/10.1007/978-3-031-18130-6_3
- Nie, S., Liu, X., Ji, H., Ma, Z., Yin, F. (2020). Simulation and Experiment Study on Deformation Characteristics of the Water Hydraulic Flexible Actuator Used for the Underwater Gripper. IEEE Access, 8, 191447–191459. https://doi.org/10.1109/access.2020.3032179
- Akinade, O. O., Oyedele, L. O., Ajayi, S. O., Bilal, M., Alaka, H. A., Owolabi, H. A. et al. (2017). Design for Deconstruction (DfD): Critical success factors for diverting end-of-life waste from landfills. Waste Management, 60, 3–13. https://doi.org/10.1016/j.wasman.2016.08.017
- Stryczek, P. (2023). Research on Deformation of Hydraulic Cylinders Made of Plastics. Energies, 16 (15), 5708. https://doi.org/10.3390/en16155708
- Gad, O. (2020). Dynamic modeling and simulation of impact in hydraulic cylinders. Proceedings of the Institution of Mechanical Engineers, Part C: Journal of Mechanical Engineering Science, 235 (21), 5216–5233. https://doi.org/10.1177/0954406220980477
- Vullo, V. (2014). Circular Cylinders and Pressure Vessels. In Springer Series in Solid and Structural Mechanics. Springer International Publishing. https://doi.org/10.1007/978-3-319-00690-1
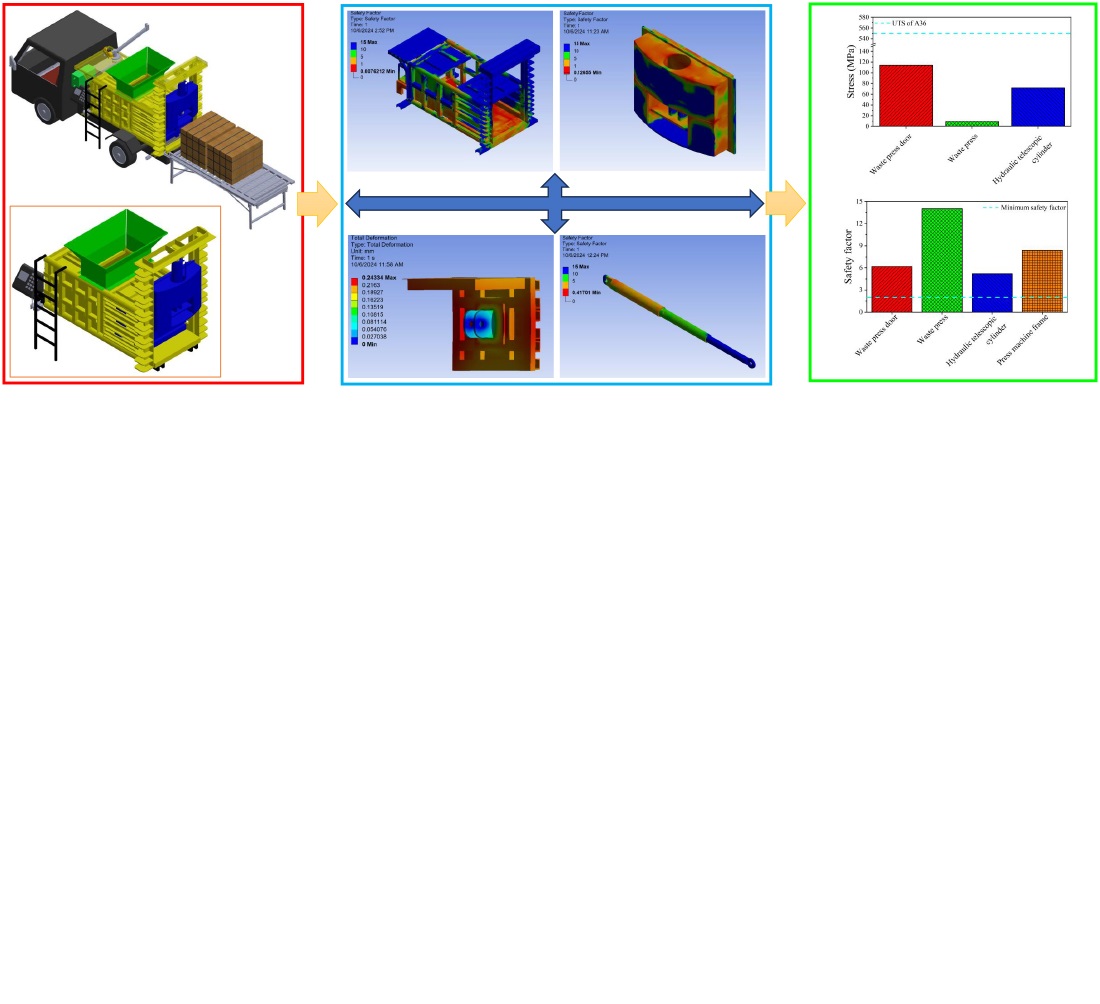
Downloads
Published
How to Cite
Issue
Section
License
Copyright (c) 2025 Agus Widyianto, Wahyu Arozzi, Yoga Guntur Sampurno, Paryanto Paryanto, Asri Widowati, Tien Aminatun, Sunarta Sunarta

This work is licensed under a Creative Commons Attribution 4.0 International License.
The consolidation and conditions for the transfer of copyright (identification of authorship) is carried out in the License Agreement. In particular, the authors reserve the right to the authorship of their manuscript and transfer the first publication of this work to the journal under the terms of the Creative Commons CC BY license. At the same time, they have the right to conclude on their own additional agreements concerning the non-exclusive distribution of the work in the form in which it was published by this journal, but provided that the link to the first publication of the article in this journal is preserved.
A license agreement is a document in which the author warrants that he/she owns all copyright for the work (manuscript, article, etc.).
The authors, signing the License Agreement with TECHNOLOGY CENTER PC, have all rights to the further use of their work, provided that they link to our edition in which the work was published.
According to the terms of the License Agreement, the Publisher TECHNOLOGY CENTER PC does not take away your copyrights and receives permission from the authors to use and dissemination of the publication through the world's scientific resources (own electronic resources, scientometric databases, repositories, libraries, etc.).
In the absence of a signed License Agreement or in the absence of this agreement of identifiers allowing to identify the identity of the author, the editors have no right to work with the manuscript.
It is important to remember that there is another type of agreement between authors and publishers – when copyright is transferred from the authors to the publisher. In this case, the authors lose ownership of their work and may not use it in any way.