Determining rational complex modifying and alloying additives to improve the mechanical characteristics of gray cast iron
DOI:
https://doi.org/10.15587/1729-4061.2024.318552Keywords:
mechanical characteristics of cast iron, modifiers of cast iron, alloying, microstructure of cast iron, graphitizing and carbide-forming elementsAbstract
The object of this study is the mechanical properties and parameters of the cast iron microstructure. The task to solve was to ensure high mechanical properties of cast iron for mechanical engineering part. To this end, a working hypothesis was put forward, which assumed the possibility of increasing mechanical properties by selecting complex additives based on modifiers and alloying ferroalloys.
The effect of 4 groups of additives was investigated: group 1 – ferrochrome (FeCr025) and silicocalcium (SiCa-30), group 2 – ferrotitanium (FТі35) and ferroboral (FEB6), group 3 – ferrotitanium (FТі35) and ferrochrome (FeCr025), group 4 – ferroboral (FEB6) and silicocalcium (SiCa-30). They were introduced into the liquid metal in different percentages in the amount of 3 % of the mass of liquid cast iron. The following mechanical characteristics were selected: flexural strength (σ, MPa), tensile strength (UTS, MPa), deflection arrow (f, mm), hardness (HB), and whitening.
It was determined that the strength characteristics of cast iron treated with ferroalloys of group 1 reach a maximum at about 40 % silicocalcium in the composition of the additive. The tensile strength of cast iron reaches about 320 MPa, the bending strength is about 710 MPa, the deflection arrow is 4.5 mm, and the hardness corresponds to the HB250 level. The fact of competition of hardness and other mechanical properties was established in the range of silicocalcium content in the modifier composition up to 40 %. Thus, it was established that it is the combination FeCr025+SiCa-30 with the ratio of components of 40:60, respectively, that is rational.
The revealed regularities of changes in the amount of carbides, the size of graphite, and the amount of ferrite when using different additives allow us to explain patterns in the formation of mechanical properties of cast irons. Owing to this, it becomes possible to identify the mechanism of formation of properties, ensuring purposeful regulation of the quality of cast iron
References
- Хільчевський, В. В. (2002). Матеріалознавство і технологія конструкційних матеріалів. К.: Либідь, 328.
- Demin, D. A., Pelikh, V. F., Ponomarenko, O. I. (1995). Optimization of the method of adjustment of chemical composition of flake graphite iron. Litejnoe Proizvodstvo, 7-8, 42–43.
- Demin, D. A., Pelikh, V. F., Ponomarenko, O. I. (1998). Complex alloying of grey cast iron. Litejnoe Proizvodstvo, 10, 18–19.
- Demin, D. A. (1998). Change in cast iron’s chemical composition in inoculation with a Si-V-Mn master alloy. Litejnoe Proizvodstvo, 6, 35.
- Riposan, I., Chisamera, M., Stan, S. (2014). New developments in high quality grey cast irons. China Foundry, 11 (4), 351–364.
- Demin, D. (2020). Constructing the parametric failure function of the temperature control system of induction crucible furnaces. EUREKA: Physics and Engineering, 6, 19–32. https://doi.org/10.21303/2461-4262.2020.001489
- Demin, D., Domin, O. (2021). Adaptive technology for constructing the kinetic equations of reduction reactions under conditions of a priori uncertainty. EUREKA: Physics and Engineering, 4, 14–29. https://doi.org/10.21303/2461-4262.2021.001959
- Fourlakidis, V., Diószegi, A. (2014). A generic model to predict the ultimate tensile strength in pearlitic lamellar graphite iron. Materials Science and Engineering: A, 618, 161–167. https://doi.org/10.1016/j.msea.2014.08.061
- Dymko, I. (2018). Choice of the optimal control strategy for the duplex-process of induction melting of constructional iron. EUREKA: Physics and Engineering, 4, 3–13. https://doi.org/10.21303/2461-4262.2018.00669
- Borsato, T., Berto, F., Ferro, P., Carollo, C. (2016). Effect of in-mould inoculant composition on microstructure and fatigue behaviour of heavy section ductile iron castings. Procedia Structural Integrity, 2, 3150–3157. https://doi.org/10.1016/j.prostr.2016.06.393
- Demin, D. (2017). Strength analysis of lamellar graphite cast iron in the «carbon (C) – carbon equivalent (Ceq)» factor space in the range of C = (3,425-3,563) % and Ceq = (4,214-4,372) %. Technology Audit and Production Reserves, 1 (1 (33)), 24–32. https://doi.org/10.15587/2312-8372.2017.93178
- Demin, D. (2017). Synthesis of nomogram for the calculation of suboptimal chemical composition of the structural cast iron on the basis of the parametric description of the ultimate strength response surface. ScienceRise, 8, 36–45. https://doi.org/10.15587/2313-8416.2017.109175
- Demin, D. (2018). Investigation of structural cast iron hardness for castings of automobile industry on the basis of construction and analysis of regression equation in the factor space «carbon (C) - carbon equivalent (Ceq)». Technology Audit and Production Reserves, 3 (1 (41)), 29–36. https://doi.org/10.15587/2312-8372.2018.109097
- Thilak, G., Chandramohan, P., Saravanan, V. S. (2023). Influence of alloying elements and its effect on austempering of compacted graphite iron – A review. Materials Today: Proceedings. https://doi.org/10.1016/j.matpr.2023.09.119
- Demin, D., Frolova, L. (2024). Construction of a logical-probabilistic model of casting quality formation for managing technological operations in foundry production. EUREKA: Physics and Engineering, 6, 104–118. https://doi.org/10.21303/2461-4262.2024.003518
- Aubakirov, D. R., Issagulov, A. Z., Akberdin, A. A., Kvon, Sv. S., Kulikov, V. Yu., Arinova, S. K. et al. (2022). Influence of boron- and barium-containing modifiers on the structure of low-chromium cast iron. Heliyon, 8 (11), e11496. https://doi.org/10.1016/j.heliyon.2022.e11496
- Aguado, E., Ferrer, M., Larrañaga, P., Stefanescu, D. M., Suárez, R. (2019). The Effect of the Substitution of Silicon by Aluminum on the Properties of Lamellar Graphite Iron. International Journal of Metalcasting, 13 (3), 536–545. https://doi.org/10.1007/s40962-018-00303-y
- Frolova, L., Shevchenko, R., Shpyh, A., Khoroshailo, V., Antonenko, Y. (2021). Selection of optimal Al–Si combinations in cast iron for castings for engineering purposes. EUREKA: Physics and Engineering, 2, 99–107. https://doi.org/10.21303/2461-4262.2021.001694
- Popov, S., Frolova, L., Rebrov, O., Naumenko, Y., Postupna, О., Zubko, V., Shvets, P. (2022). Increasing the mechanical properties of structural cast iron for machine-building parts by combined Mn – Al alloying. EUREKA: Physics and Engineering, 1, 118–130. https://doi.org/10.21303/2461-4262.2022.002243
- Lysenkov, V., Demin, D. (2022). Reserves of resource saving in the manufacture of brake drums of cargo vehicles. ScienceRise, 3, 14–23. https://doi.org/10.21303/2313-8416.2022.002551
- Nikolaiev, D. (2022). Procedure for selecting a rational technological mode for the processing of cast iron melt on the basis of graph-analytical processing of the data of serial smeltings. ScienceRise, 5, 3–13. https://doi.org/10.21303/2313-8416.2022.002774
- Frolova, L., Barsuk, A., Nikolaiev, D. (2022). Revealing the significance of the influence of vanadium on the mechanical properties of cast iron for castings for machine-building purpose. Technology Audit and Production Reserves, 4 (1 (66)), 6–10. https://doi.org/10.15587/2706-5448.2022.263428
- Nikolaev, D. (2024). The choice of rational adjustment of the chemical composition of iron melted in an electric arc furnace on the basis of technological audit of serial films. Technology Audit and Production Reserves, 2 (1 (76)), 22–26. https://doi.org/10.15587/2706-5448.2024.301259
- Demin, D. (2017). Synthesis of optimal control of technological processes based on a multialternative parametric description of the final state. Eastern-European Journal of Enterprise Technologies, 3 (4 (87)), 51–63. https://doi.org/10.15587/1729-4061.2017.105294
- Верховлюк, А. М., Нарівський, А. В., Могилатенко, В. Г. (2016). Технології одержання металів та сплавів для ливарного виробництва. К.: Видавничий дім «Вініченко», 224. Available at: https://foundry.kpi.ua/wp-content/uploads/2020/03/tehnologiyi-oderzhannya-metaliv.pdf
- Білецький, В. С. (Ред.) (2004). Мала гірнича енциклопедія. Т. 1. Донецьк: Донбас, 670.
- References +++
- Khilchevskyi, V. V. (2002). Materialoznavstvo i tekhnolohiya konstruktsiynykh materialiv. Kyiv: Lybid, 328.
- Demin, D. A., Pelikh, V. F., Ponomarenko, O. I. (1995). Optimization of the method of adjustment of chemical composition of flake graphite iron. Litejnoe Proizvodstvo, 7-8, 42–43.
- Demin, D. A., Pelikh, V. F., Ponomarenko, O. I. (1998). Complex alloying of grey cast iron. Litejnoe Proizvodstvo, 10, 18–19.
- Demin, D. A. (1998). Change in cast iron’s chemical composition in inoculation with a Si-V-Mn master alloy. Litejnoe Proizvodstvo, 6, 35.
- Riposan, I., Chisamera, M., Stan, S. (2014). New developments in high quality grey cast irons. China Foundry, 11 (4), 351–364.
- Demin, D. (2020). Constructing the parametric failure function of the temperature control system of induction crucible furnaces. EUREKA: Physics and Engineering, 6, 19–32. https://doi.org/10.21303/2461-4262.2020.001489
- Demin, D., Domin, O. (2021). Adaptive technology for constructing the kinetic equations of reduction reactions under conditions of a priori uncertainty. EUREKA: Physics and Engineering, 4, 14–29. https://doi.org/10.21303/2461-4262.2021.001959
- Fourlakidis, V., Diószegi, A. (2014). A generic model to predict the ultimate tensile strength in pearlitic lamellar graphite iron. Materials Science and Engineering: A, 618, 161–167. https://doi.org/10.1016/j.msea.2014.08.061
- Dymko, I. (2018). Choice of the optimal control strategy for the duplex-process of induction melting of constructional iron. EUREKA: Physics and Engineering, 4, 3–13. https://doi.org/10.21303/2461-4262.2018.00669
- Borsato, T., Berto, F., Ferro, P., Carollo, C. (2016). Effect of in-mould inoculant composition on microstructure and fatigue behaviour of heavy section ductile iron castings. Procedia Structural Integrity, 2, 3150–3157. https://doi.org/10.1016/j.prostr.2016.06.393
- Demin, D. (2017). Strength analysis of lamellar graphite cast iron in the «carbon (C) – carbon equivalent (Ceq)» factor space in the range of C = (3,425-3,563) % and Ceq = (4,214-4,372) %. Technology Audit and Production Reserves, 1 (1 (33)), 24–32. https://doi.org/10.15587/2312-8372.2017.93178
- Demin, D. (2017). Synthesis of nomogram for the calculation of suboptimal chemical composition of the structural cast iron on the basis of the parametric description of the ultimate strength response surface. ScienceRise, 8, 36–45. https://doi.org/10.15587/2313-8416.2017.109175
- Demin, D. (2018). Investigation of structural cast iron hardness for castings of automobile industry on the basis of construction and analysis of regression equation in the factor space «carbon (C) - carbon equivalent (Ceq)». Technology Audit and Production Reserves, 3 (1 (41)), 29–36. https://doi.org/10.15587/2312-8372.2018.109097
- Thilak, G., Chandramohan, P., Saravanan, V. S. (2023). Influence of alloying elements and its effect on austempering of compacted graphite iron – A review. Materials Today: Proceedings. https://doi.org/10.1016/j.matpr.2023.09.119
- Demin, D., Frolova, L. (2024). Construction of a logical-probabilistic model of casting quality formation for managing technological operations in foundry production. EUREKA: Physics and Engineering, 6, 104–118. https://doi.org/10.21303/2461-4262.2024.003518
- Aubakirov, D. R., Issagulov, A. Z., Akberdin, A. A., Kvon, Sv. S., Kulikov, V. Yu., Arinova, S. K. et al. (2022). Influence of boron- and barium-containing modifiers on the structure of low-chromium cast iron. Heliyon, 8 (11), e11496. https://doi.org/10.1016/j.heliyon.2022.e11496
- Aguado, E., Ferrer, M., Larrañaga, P., Stefanescu, D. M., Suárez, R. (2019). The Effect of the Substitution of Silicon by Aluminum on the Properties of Lamellar Graphite Iron. International Journal of Metalcasting, 13 (3), 536–545. https://doi.org/10.1007/s40962-018-00303-y
- Frolova, L., Shevchenko, R., Shpyh, A., Khoroshailo, V., Antonenko, Y. (2021). Selection of optimal Al–Si combinations in cast iron for castings for engineering purposes. EUREKA: Physics and Engineering, 2, 99–107. https://doi.org/10.21303/2461-4262.2021.001694
- Popov, S., Frolova, L., Rebrov, O., Naumenko, Y., Postupna, О., Zubko, V., Shvets, P. (2022). Increasing the mechanical properties of structural cast iron for machine-building parts by combined Mn – Al alloying. EUREKA: Physics and Engineering, 1, 118–130. https://doi.org/10.21303/2461-4262.2022.002243
- Lysenkov, V., Demin, D. (2022). Reserves of resource saving in the manufacture of brake drums of cargo vehicles. ScienceRise, 3, 14–23. https://doi.org/10.21303/2313-8416.2022.002551
- Nikolaiev, D. (2022). Procedure for selecting a rational technological mode for the processing of cast iron melt on the basis of graph-analytical processing of the data of serial smeltings. ScienceRise, 5, 3–13. https://doi.org/10.21303/2313-8416.2022.002774
- Frolova, L., Barsuk, A., Nikolaiev, D. (2022). Revealing the significance of the influence of vanadium on the mechanical properties of cast iron for castings for machine-building purpose. Technology Audit and Production Reserves, 4 (1 (66)), 6–10. https://doi.org/10.15587/2706-5448.2022.263428
- Nikolaev, D. (2024). The choice of rational adjustment of the chemical composition of iron melted in an electric arc furnace on the basis of technological audit of serial films. Technology Audit and Production Reserves, 2 (1 (76)), 22–26. https://doi.org/10.15587/2706-5448.2024.301259
- Demin, D. (2017). Synthesis of optimal control of technological processes based on a multialternative parametric description of the final state. Eastern-European Journal of Enterprise Technologies, 3 (4 (87)), 51–63. https://doi.org/10.15587/1729-4061.2017.105294
- Verkhovliuk, A. M., Narivskyi, A. V., Mohylatenko, V. H. (2016). Tekhnolohiyi oderzhannia metaliv ta splaviv dlia lyvarnoho vyrobnytstva. Kyiv: Vydavnychyi dim «Vinichenko», 224. Available at: https://foundry.kpi.ua/wp-content/uploads/2020/03/tehnologiyi-oderzhannya-metaliv.pdf
- Biletskyi, V. S. (Ed.) (2004). Mala hirnycha entsyklopediya. Vol. 1. Donetsk: Donbas, 670.
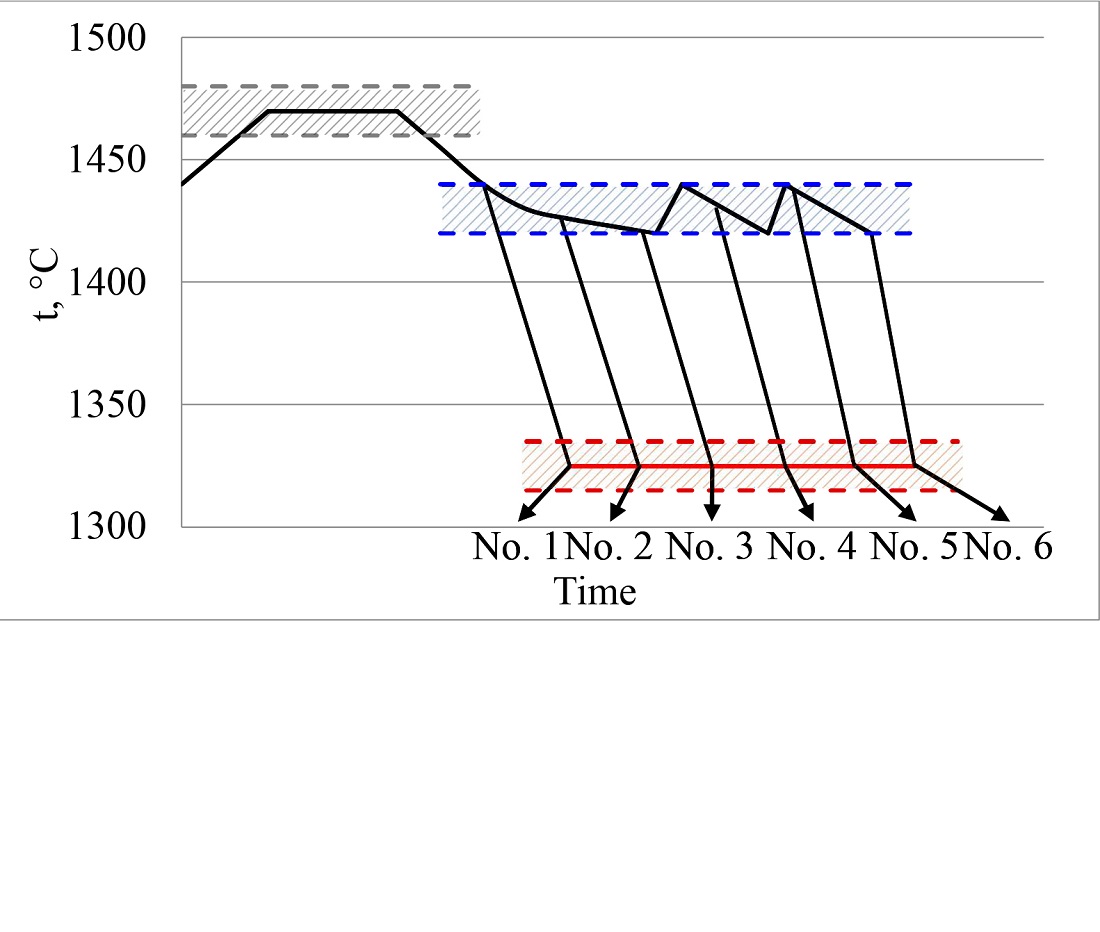
Downloads
Published
How to Cite
Issue
Section
License
Copyright (c) 2024 Stepan Klymenko, Anatolii Verkhovliuk, Artur Sevoian, Oleg Akimov, Olga Ponomarenko, Pavlo Penziev

This work is licensed under a Creative Commons Attribution 4.0 International License.
The consolidation and conditions for the transfer of copyright (identification of authorship) is carried out in the License Agreement. In particular, the authors reserve the right to the authorship of their manuscript and transfer the first publication of this work to the journal under the terms of the Creative Commons CC BY license. At the same time, they have the right to conclude on their own additional agreements concerning the non-exclusive distribution of the work in the form in which it was published by this journal, but provided that the link to the first publication of the article in this journal is preserved.
A license agreement is a document in which the author warrants that he/she owns all copyright for the work (manuscript, article, etc.).
The authors, signing the License Agreement with TECHNOLOGY CENTER PC, have all rights to the further use of their work, provided that they link to our edition in which the work was published.
According to the terms of the License Agreement, the Publisher TECHNOLOGY CENTER PC does not take away your copyrights and receives permission from the authors to use and dissemination of the publication through the world's scientific resources (own electronic resources, scientometric databases, repositories, libraries, etc.).
In the absence of a signed License Agreement or in the absence of this agreement of identifiers allowing to identify the identity of the author, the editors have no right to work with the manuscript.
It is important to remember that there is another type of agreement between authors and publishers – when copyright is transferred from the authors to the publisher. In this case, the authors lose ownership of their work and may not use it in any way.