Devising a technology for manufacturing hollow cast steel structures with composite and reinforced non-metallic functional filler
DOI:
https://doi.org/10.15587/1729-4061.2024.318553Keywords:
reinforced steel casting, computer simulation, lost foam castingAbstract
The object of this study is the structure of hollow steel modules filled with various types of functional materials, as well as the technology of their production using lost foam casting.
Computer simulation of hydrodynamic and heat-mass exchange processes and solidification was carried out to establish the laws and prerequisites for designing state-of-the-art hollow cast structures and to devise their production technology. The study investigated the influence of reinforced steel elements and reinforcement directly from the liquid alloy of the shell on the peculiarities of hydrodynamic, heat-mass transfer processes, and solidification during the production of hollow steel structures with functional fillers.
It has been determined that the presence of polystyrene membranes in the functional filler for subsequent reinforcement from the liquid phase of the shell metal affects the hydrodynamics of filling the casting. In the thin channels formed in the filler, the metal flow rate increases from 2 m/s to 8 m/s in the upper channels, and from 3 m/s to 12 m/s in the lower channels, which is associated with an increase in metallostatic pressure.
The presence of metal reinforcement in the functional filler and the reinforcement of the functional material from the liquid phase of the shell metal accelerates the heating of the non-metallic filler by 1.2–1.4 and 1.4–1.8 times, respectively. Reinforcement also helps increase the maximum heating temperature of the functional filler by 200–300 °C, which creates better conditions for its sintering.
The grades of steels for their use as a matrix alloy in the production of hollow cast castings were determined; their structure and physical-mechanical properties were studied. The recommended modes of heat treatment of low-alloy steel to obtain the required properties have been determined.
The study reported here is a theoretical prerequisite for verification in the manufacture of experimental cast hollow structures with metallic and non-metallic reinforcing phase
References
- Singla, Y. K., Maughan, M. R., Arora, N., Dwivedi, D. K. (2024). Enhancing the wear resistance of iron-based alloys: A comprehensive review of alloying element effects. Journal of Manufacturing Processes, 120, 135–160. https://doi.org/10.1016/j.jmapro.2024.04.038
- Bhadeshia, H. K. D. H., Honeycombe, R. W. K. (2024). Stainless steel. Steels, 347–381. https://doi.org/10.1016/b978-0-44-318491-8.00018-6
- Azeem Ullah, M., Cao, Q. P., Wang, X. D., Ding, S. Q., Abubaker Khan, M., Zhang, D. X., Jiang, J. Z. (2024). Carbon effect on tensile and wear behaviors for a dual-phase Fe61.5Cr17.5Ni13Al8 alloy. Materials Science and Engineering: A, 914, 147128. https://doi.org/10.1016/j.msea.2024.147128
- Kvasnytska, Y. H., Shalevska, I. A., Balitskii, A. I., Ivaskevich, L. M., Maksiuta, І. І., Kvasnytska, K. H. (2024). Influence of Refractory Elements on Phase–Structural Stability of Heat-Resistant Corrosion-Resistant Alloys for Gas Turbine Blades. Metallofizika i Noveishie Tekhnologii, 45 (8), 975–992. https://doi.org/10.15407/mfint.45.08.0975
- Raabe, D., Sun, B., Kwiatkowski Da Silva, A., Gault, B., Yen, H.-W., Sedighiani, K. et al. (2020). Current Challenges and Opportunities in Microstructure-Related Properties of Advanced High-Strength Steels. Metallurgical and Materials Transactions A, 51 (11), 5517–5586. https://doi.org/10.1007/s11661-020-05947-2
- Wakai, E., Noto, H., Shibayama, T., Furuya, K., Ando, M., Kamada, T. et al. (2024). Microstructures and hardness of BCC phase iron-based high entropy alloy Fe-Mn-Cr-V-Al-C. Materials Characterization, 211, 113881. https://doi.org/10.1016/j.matchar.2024.113881
- Glotka, A., Byelikov, S., Lysytsya, O. (2024). Modeling of carbide formation in alloy of the Ni-Cr-Co-W-Mo-Al-Ti-C system. Acta Metallurgica Slovaca, 30 (1), 15–18. https://doi.org/10.36547/ams.30.1.1991
- ASTM A732/A732M-20. Specification for Castings, Investment, Carbon and Low Alloy Steel for General Application, and Cobalt Alloy for High Strength at Elevated Temperatures. https://doi.org/10.1520/a0732_a0732m-20
- Zewdie, F., Srivastava, A., Punia, R., Bhatnagar, N. (2024). Experimental investigation on the development of hybrid composite metal foam reinforced with steel hollow spheres for higher energy absorption applications. Journal of Manufacturing Processes, 123, 60–82. https://doi.org/10.1016/j.jmapro.2024.05.046
- Kaliuzhnyi, P., Shalevska, I., Sliusarev, V. (2023). Microstructure of Reinforced Cast Iron Produced by Lost Foam Casting. Archives of Metallurgy and Materials, 68 (4), 1369–1375. https://doi.org/10.24425/amm.2023.146202
- Kota, N., Charan, M. S., Laha, T., Roy, S. (2022). Review on development of metal/ceramic interpenetrating phase composites and critical analysis of their properties. Ceramics International, 48 (2), 1451–1483. https://doi.org/10.1016/j.ceramint.2021.09.232
- Dulska, A., Studnicki, A., Cholewa, M., Szajnar, J. (2018). Cast Iron Reinforced with Foaming Ceramic Insert. Archives of Foundry Engineering, 18 (2), 137–140. https://doi.org/10.24425/122516
- Wróbel, T., Przyszlak, N., Dulska, A. (2019). Technology of Alloy Layers on Surface of Castings. International Journal of Metalcasting, 13 (3), 604–610. https://doi.org/10.1007/s40962-018-00304-x
- Dulska, A., Szajnar, J., Król, M. (2020). Analysis of the Mechanical Properties of the Titanium Layer Obtained by the Mold Cavity Preparation Method. Archives of Metallurgy and Materials, 66 (1), 51–56. https://doi.org/10.24425/amm.2021.134758
- Narivskiy, A., Shinsky, O., Shalevska, I., Kvasnytska, J., Kaliuzhnyi, P., Polivoda, S. (2023). Modern technological processes of obtaining cast products and structures of responsible purpose from aluminum, ferrous carbon and heat-resistant alloys. Structural Materials: Manufacture, Properties, Conditions of Use, 32–67. https://doi.org/10.15587/978-617-7319-97-8.ch2
- Narivskiy, A., Shinsky, O., Shalevska, I., Kvasnytska, J., Kaliuzhnyi, P., Polivoda, S. (2023). The influence of external actions and methods of alloying alloys on the operational characteristics of cast products. Structural Materials: Manufacture, Properties, Conditions of Use, 121–157. https://doi.org/10.15587/978-617-7319-97-8.ch4
- Shinsky, O., Shalevska, I., Kaliuzhnyi, P., Shinsky, V., Lysenko, T., Shevchuk, T. et al. (2018). Principles of construction and identification of a multilevel system for monitoring parameters of technological cycle of casting. Eastern-European Journal of Enterprise Technologies, 5 (1 (95)), 25–32. https://doi.org/10.15587/1729-4061.2018.141303
- Steel and steel products: Location and preparation of samples and test pieces for mechanical testing (1997). ISO 37:1997. ISO. Available at: https://cdn.standards.iteh.ai/samples/4356/857afeb6d0754ba69790e97261f95488/ISO-377-1997.pdf
- Steels: Micrographic determination of the ferritic or austenitic grain size (1983). ISO 643:1983. ISO. Available at: https://cdn.standards.iteh.ai/samples/4773/6ad7e45fca0d4daa86654405f6e2d12e/ISO-643-1983.pdf
- DSTU 8966:2019. Stal. Metalohrafichni metody vyznachennia nemetalevykh vkliuchen. Available at: https://online.budstandart.com/ua/catalog/doc-page.html?id_doc=88067
- DSTU 8972:2019. Stali ta splavy. Metody vyiavlennia ta vyznachennia velychyny zerna. Available at: https://online.budstandart.com/ua/catalog/doc-page.html?id_doc=88073
- Steel castings – General technical delivery requirements (2023). ISO 4990:2023. ISO. Available at: https://cdn.standards.iteh.ai/samples/84185/33d9639ba3db417ab01fe2a41751f295/ISO-4990-2023.pdf
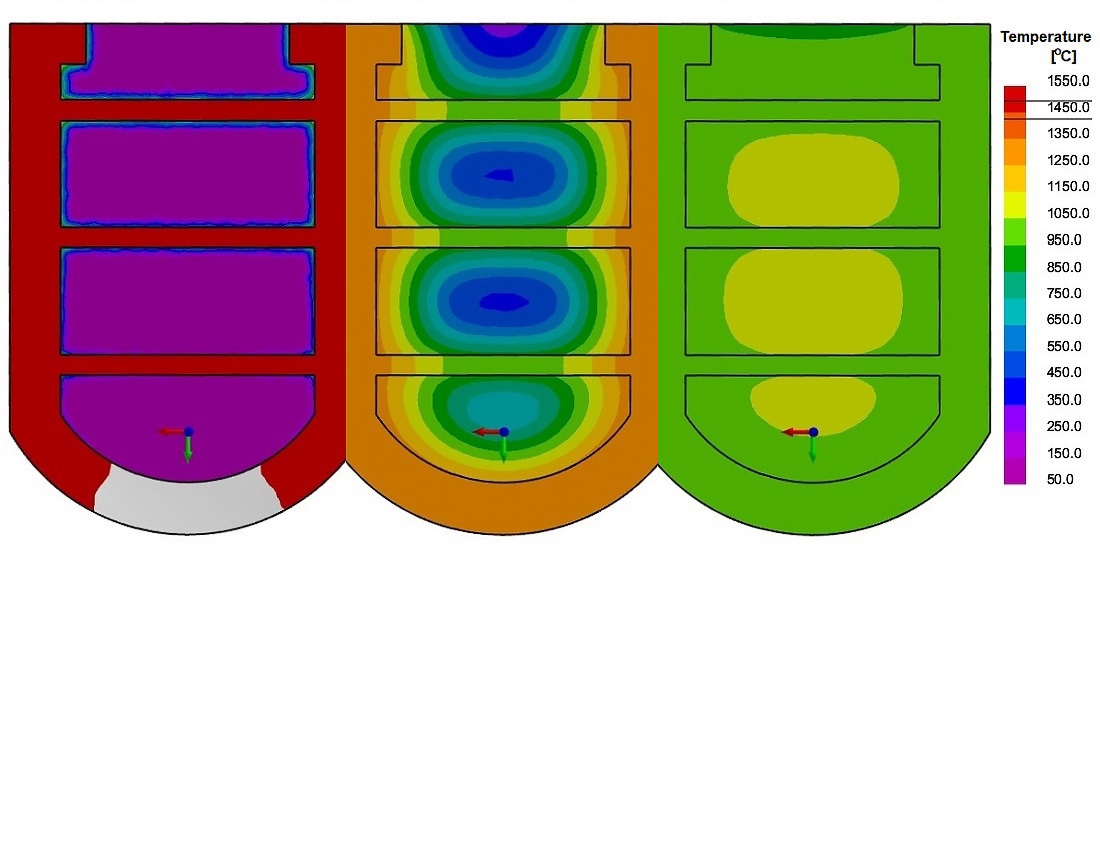
Downloads
Published
How to Cite
Issue
Section
License
Copyright (c) 2024 Oleg Shinsky, Iuliia Kvasnytska, Inna Shalevska, Pavlo Kaliuzhnyi, Oleksandr Neima

This work is licensed under a Creative Commons Attribution 4.0 International License.
The consolidation and conditions for the transfer of copyright (identification of authorship) is carried out in the License Agreement. In particular, the authors reserve the right to the authorship of their manuscript and transfer the first publication of this work to the journal under the terms of the Creative Commons CC BY license. At the same time, they have the right to conclude on their own additional agreements concerning the non-exclusive distribution of the work in the form in which it was published by this journal, but provided that the link to the first publication of the article in this journal is preserved.
A license agreement is a document in which the author warrants that he/she owns all copyright for the work (manuscript, article, etc.).
The authors, signing the License Agreement with TECHNOLOGY CENTER PC, have all rights to the further use of their work, provided that they link to our edition in which the work was published.
According to the terms of the License Agreement, the Publisher TECHNOLOGY CENTER PC does not take away your copyrights and receives permission from the authors to use and dissemination of the publication through the world's scientific resources (own electronic resources, scientometric databases, repositories, libraries, etc.).
In the absence of a signed License Agreement or in the absence of this agreement of identifiers allowing to identify the identity of the author, the editors have no right to work with the manuscript.
It is important to remember that there is another type of agreement between authors and publishers – when copyright is transferred from the authors to the publisher. In this case, the authors lose ownership of their work and may not use it in any way.