Визначення впливу різної концентрації кислоти та співвідношення твердого/рідкого у вилуговуванні магнію з феронікелевого шлаку
DOI:
https://doi.org/10.15587/1729-4061.2024.319045Ключові слова:
феронікелевий шлак, переробка, лужне злиття, смаження, вилуговування води, вилуговування кислоти, екстракція, магній, концентрація кислоти, співвідношення твердого/рідиниАнотація
Індонезія – країна з найбільшими резервами нікелю та рівнями виробництва у світі. Кожна тонна виробництва нікелю може виробляти вісім тон побічних продуктів у вигляді феронікелевого шлаку, який продовжує збільшуватися через мінімальний процес переробки цих побічних продуктів. Це дослідження мало на меті визначити вплив змін концентрації кислоти та співвідношення твердого/рідкого на вилучення магнію з феронікелевого шлаку та характеризувати трансформацію феронікелевого шлаку на кожній стадії процесу. Дослідження проводили за допомогою методу злиття лугу і продовжували вилуговування води та вилуговування кислоти за допомогою соляної кислоти (HCL) як розчинника. Першим кроком у дослідженні було фрезерування, щоб отримати порошок з розміром частинок ≤127 мкм. Порошок зразка згодом змішували з добавкою NA2CO3 у співвідношенні 50:50 (мас./мас.) і обсмажували протягом 60 хвилин при 1000 ° С. Потім процедуру вилуговування води проводили протягом 60 хвилин при 100 ° С, коефіцієнт 1:10 (мас./Об.) та перемішувальна швидкість 400 об/хв. Потім фільтрат і залишок відокремлювали за допомогою процесу фільтрації. Вилуговування кислоти, що використовує HCl з варіаціями концентрації 0,5, 1 та 1,5 м, співвідношення твердого/рідини (т/р) 1:20, 1:30 та 1:40 (мас./об.) було проведено на залишках. Результати вилуговування кислоти потім знову фільтрували. Потім фільтрат характеризувався тестуванням ICP-OES. Виходячи з результатів аналізу, можна зазначити, що відсоток екстракції магнію збільшується у міру збільшення співвідношення твердого/рідини (т/р), але зменшується зі збільшенням концентрації HCL. Оптимальний відсоток вилучення магнію становить 64,12 %, що було досягнуто при умовах вилуговування твердого/рідкого співвідношення (т/р) 1:40 (мас./об.) та концентрації HCL 0,5 м
Посилання
- Nickel Statistics and Information. USGS. Available at: https://www.usgs.gov/centers/national-minerals-information-center/nickel-statistics-and-information
- Nurjaman, F., Astuti, W., Bahfie, F., Suharno, B. (2021). Study of selective reduction in lateritic nickel ore: Saprolite versus limonite. Materials Today: Proceedings, 44, 1488–1494. https://doi.org/10.1016/j.matpr.2020.11.687
- Sun, W., Li, X., Liu, R., Zhai, Q., Li, J. (2021). Recovery of Valuable Metals from Nickel Smelting Slag Based on Reduction and Sulfurization Modification. Minerals, 11 (9), 1022. https://doi.org/10.3390/min11091022
- Ulum, R. M., Natalin, Riastuti, R., Mayangsari, W., Prasetyo, A. B., Soedarsono, J. W., Maksum, A. (2023). Pyro-Hydrometallurgy Routes to Recover Silica from Indonesian Ferronickel Slag. Recycling, 8 (1), 13. https://doi.org/10.3390/recycling8010013
- Zulhan, Z., Agustina, N. (2021). A novel utilization of ferronickel slag as a source of magnesium metal and ferroalloy production. Journal of Cleaner Production, 292, 125307. https://doi.org/10.1016/j.jclepro.2020.125307
- Prasetyo, A. B., Khaerul, A., Mayangsari, W., Febriana, E., Maksum, A., Andinie, J. et al. (2021). Magnesium extraction of ferronickel slag processed by alkali fusion and hydrochloric acid leaching. Journal of Mining and Metallurgy, Section B: Metallurgy, 57 (2), 225–233. https://doi.org/10.2298/jmmb200224018p
- Yan, P., Shen, Y., Du, X., Chong, J. (2020). Microwave Absorption Properties of Magnetite Particles Extracted from Nickel Slag. Materials, 13 (9), 2162. https://doi.org/10.3390/ma13092162
- Li, B., Rong, T., Du, X., Shen, Y., Shen, Y. (2021). Preparation of Fe3O4 particles with unique structures from nickel slag for enhancing microwave absorption properties. Ceramics International, 47 (13), 18848–18857. https://doi.org/10.1016/j.ceramint.2021.03.224
- Gao, F., Huang, Z., Li, H., Li, X., Wang, K., Hamza, M. F. et al. (2021). Recovery of magnesium from ferronickel slag to prepare hydrated magnesium sulfate by hydrometallurgy method. Journal of Cleaner Production, 303, 127049. https://doi.org/10.1016/j.jclepro.2021.127049
- Gu, F., Peng, Z., Tang, H., Ye, L., Tian, W., Liang, G. et al. (2018). Preparation of Refractory Materials from Ferronickel Slag. Characterization of Minerals, Metals, and Materials 2018, 633–642. https://doi.org/10.1007/978-3-319-72484-3_67
- Abdul, F., Adachi, K., Ho, H.-J., Iizuka, A., Shibata, E. (2024). Magnesium recovery from ferronickel slag by reaction with sodium hydroxide. Journal of Environmental Chemical Engineering, 12 (3), 112516. https://doi.org/10.1016/j.jece.2024.112516
- Song, H.-Y., Seo, J.-B., Kang, S.-K., Kim, I.-D., Choi, B.-W., Oh, K.-J. (2014). CO2Fixation by Magnesium Hydroxide from Ferro-Nickel Slag. Clean Technology, 20 (1), 42–50. https://doi.org/10.7464/ksct.2014.20.1.042
- Mubarok, M. Z., Yudiarto, A. (2017). Synthesis of Magnesium Oxide from Ferronickel Smelting Slag Through Hydrochloric Acid Leaching-Precipitation and Calcination. Energy Technology 2017, 247–258. https://doi.org/10.1007/978-3-319-52192-3_24
- Yang, J., Duan, X., Liu, L., Yang, H., Jiang, X. (2021). Recovery of Magnesium from Ferronickel Slag to Prepare Magnesium Oxide by Sulfuric Acid Leaching. Minerals, 11 (12), 1375. https://doi.org/10.3390/min11121375
- Pangaribuan, R. H., Patrick, J., Prasetyo, A. B., Maksum, A., Munir, B., Soedarsono, J. W. (2018). The effect of NaOH (natrium hydroxide) to slag nickel pyrometallurgy in different temperature and additive ratio. E3S Web of Conferences, 67, 03052. https://doi.org/10.1051/e3sconf/20186703052
- Patrick, J., Prasetyo, A. B., Munir, B., Maksum, A., Soedarsono, J. W. (2018). The effect of addition of sodium sulphate (Na2SO4) to nickel slag pyrometallurgical process with temperature and additives ratio as variables. E3S Web of Conferences, 67, 03053. https://doi.org/10.1051/e3sconf/20186703053
- Mufakhir, F. R., Mubarok, M. Z., Ichlas, Z. T. (2018). Leaching of silicon from ferronickel (FeNi) smelting slag with sodium hydroxide solution at atmospheric pressure. IOP Conference Series: Materials Science and Engineering, 285, 012003. https://doi.org/10.1088/1757-899x/285/1/012003
- Prasetyo, A. B., Darmawansyah, R., Mayangsari, W., Febriana, E., Permana, S., Maksum, A. et al. (2020). Reverse leaching of magnesium from ferronickel slag using alkali solvent NaOH. Eastern-European Journal of Enterprise Technologies, 1 (12 (103)), 6–14. https://doi.org/10.15587/1729-4061.2020.193885
- Xiao, Q., Chen, Y., Gao, Y., Xu, H., Zhang, Y. (2010). Leaching of silica from vanadium-bearing steel slag in sodium hydroxide solution. Hydrometallurgy, 104 (2), 216–221. https://doi.org/10.1016/j.hydromet.2010.06.007
- Qian, B., Liu, H., Ma, B., Wang, Q., Lu, J., Hu, Y. et al. (2022). Bulk trash to nano treasure: Synthesis of two-dimensional brucite nanosheet from high-magnesium nickel slag. Journal of Cleaner Production, 333, 130196. https://doi.org/10.1016/j.jclepro.2021.130196
- Mayangsari, W., Avifah, I. N., Prasetyo, A. B., Febriana, E., Maksum, A., Ulum, R. M. et al. (2021). Decomposition of ferronickel slag through alkali fusion in the roasting process. Eastern-European Journal of Enterprise Technologies, 2 (12 (110)), 44–51. https://doi.org/10.15587/1729-4061.2021.217579
- Prasetyo, A. B., Maksum, A., Soedarsono, J. W., Firdiyono, F. (2019). Thermal characteristics of ferronickel slag on roasting process with addition of sodium carbonate (Na2CO3). IOP Conference Series: Materials Science and Engineering, 541 (1), 012037. https://doi.org/10.1088/1757-899x/541/1/012037
- Raschman, P., Špáková, M., Fedoročková, A. (2010). Effect of hydrochloric acid concentration on the selectivity of leaching of high-calcium dead-burned magnesite. Acta Montanistica Slovaca, 15 (3), 232–237. Available at: https://actamont.tuke.sk/pdf/2010/n3/09_Raschman.pdf
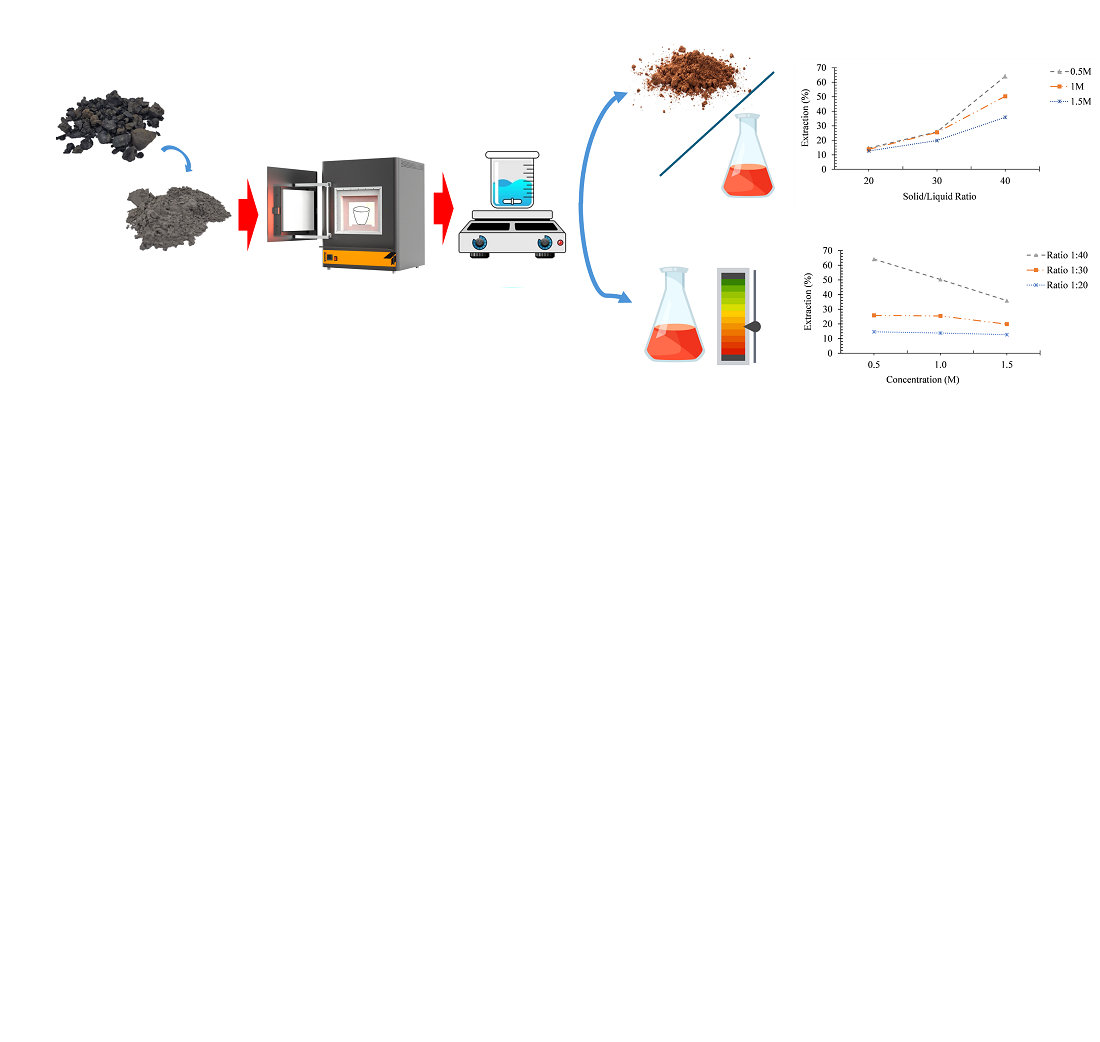
##submission.downloads##
Опубліковано
Як цитувати
Номер
Розділ
Ліцензія
Авторське право (c) 2024 Eni Febriana, Aldo Yansen Tambor Napitupulu, Johny Wahyuadi Soedarsono, Badrul Munir, Eddy Sumarno Siradj, Agus Paul Setiawan Kaban, Martina Yttria Mertoprawiro, Kadek Ambara Jaya

Ця робота ліцензується відповідно до Creative Commons Attribution 4.0 International License.
Закріплення та умови передачі авторських прав (ідентифікація авторства) здійснюється у Ліцензійному договорі. Зокрема, автори залишають за собою право на авторство свого рукопису та передають журналу право першої публікації цієї роботи на умовах ліцензії Creative Commons CC BY. При цьому вони мають право укладати самостійно додаткові угоди, що стосуються неексклюзивного поширення роботи у тому вигляді, в якому вона була опублікована цим журналом, але за умови збереження посилання на першу публікацію статті в цьому журналі.
Ліцензійний договір – це документ, в якому автор гарантує, що володіє усіма авторськими правами на твір (рукопис, статтю, тощо).
Автори, підписуючи Ліцензійний договір з ПП «ТЕХНОЛОГІЧНИЙ ЦЕНТР», мають усі права на подальше використання свого твору за умови посилання на наше видання, в якому твір опублікований. Відповідно до умов Ліцензійного договору, Видавець ПП «ТЕХНОЛОГІЧНИЙ ЦЕНТР» не забирає ваші авторські права та отримує від авторів дозвіл на використання та розповсюдження публікації через світові наукові ресурси (власні електронні ресурси, наукометричні бази даних, репозитарії, бібліотеки тощо).
За відсутності підписаного Ліцензійного договору або за відсутністю вказаних в цьому договорі ідентифікаторів, що дають змогу ідентифікувати особу автора, редакція не має права працювати з рукописом.
Важливо пам’ятати, що існує і інший тип угоди між авторами та видавцями – коли авторські права передаються від авторів до видавця. В такому разі автори втрачають права власності на свій твір та не можуть його використовувати в будь-який спосіб.