Advanced design of a small-scale mini gerotor pump in a high-temperature and high-viscosity fluid thermal system
DOI:
https://doi.org/10.15587/1729-4061.2023.272674Keywords:
gerotor, slip coefficient, small-scale, thermal system, trochoid pump, VDI 2221Abstract
In this research, the development of a small-scale heat transfer gerotor pump with an advanced arrangement for high-viscosity and high-temperature fluids is described comprehensively. The small-scale pump design aims to meet the needs of modular components for industry and research, especially for small-scale heat transfer applications such as residential heating systems. VDI 2221 approach was used to construct an advanced gerotor pump with an internal reservoir unit that can generate additional pressure and minimize the slip factor, thereby increasing its volumetric efficiency. The developed small-scale pump was designed in a smart arrangement, which required fewer components than a typical heat transfer pump. This helps to reduce the maintenance of the pump and its components. Experimental tests were performed using a testing apparatus equipped with a heater, a control system using Pulse Width Modulation (PWM) adjustment, valves, pressure, and temperature gauges. The instruments in the apparatus test were used to control the flow rate and pump speed and monitor the temperature of the working fluid. The results of the experiment show that the advanced gerotor pump was able to deliver fluid with a viscosity of 307 ml/min and a temperature of up to 230 °C. The components arrangement minimizes the slip factor, which is mostly the main challenge of positive displacement pumps. The maximum slip coefficient of the advanced gerotor pump design is 0.095. The volumetric efficiency was in the range of 0.803–0.905 when the pump operated at 2,100 RPM and 230 °C. The experiment and analysis results show that the pump can be implemented for the actual application of the thermal system, for research and industry
References
- Ostos, I., Ruiz, I., Gajic, M., Gómez, W., Bonilla, A., Collazos, C. (2019). A modified novel blade configuration proposal for a more efficient VAWT using CFD tools. Energy Conversion and Management, 180, 733–746. doi: https://doi.org/10.1016/j.enconman.2018.11.025
- Ismail, I., Mulyanto, A. T., Rahman, R. A. (2022). Development of free water knock-out tank by using internal heat exchanger for heavy crude oil. EUREKA: Physics and Engineering, 4, 77–85. doi: https://doi.org/10.21303/2461-4262.2022.002502
- Ismail, I., Pane, E. A., Haryanto, G., Okviyanto, T., Rahman, R. A. (2021). A Better Approach for Modified Bach-Type Savonius Turbine Optimization. International Review of Aerospace Engineering (IREASE), 14 (3), 159. doi: https://doi.org/10.15866/irease.v14i3.20612
- Rahman, R. A., Lahuri, A. H., Ismail. (2023). Thermal stress influence on the long-term performance of fast-charging paraffin-based thermal storage. Thermal Science and Engineering Progress, 37, 101546. doi: https://doi.org/10.1016/j.tsep.2022.101546
- Lingayat, A., Chandramohan, V. P., Raju, V. R. K., Kumar, A. (2020). Development of indirect type solar dryer and experiments for estimation of drying parameters of apple and watermelon. Thermal Science and Engineering Progress, 16, 100477. doi: https://doi.org/10.1016/j.tsep.2020.100477
- Khademi, A., Shank, K., Mehrjardi, S. A. A., Tiari, S., Sorrentino, G., Said, Z. et al. (2022). A brief review on different hybrid methods of enhancement within latent heat storage systems. Journal of Energy Storage, 54, 105362. doi: https://doi.org/10.1016/j.est.2022.105362
- Ismail, Syahbana, M. S. L., Rahman, R. A. (2022). Thermal Performance Assessment for an Active Latent Heat Storage Tank by Using Various Finned-Coil Heat Exchangers. International Journal of Heat and Technology, 40 (6), 1470–1477. doi: https://doi.org/10.18280/ijht.400615
- Afgan, S., Khushnood, R. A., Memon, S. A., Iqbal, N. (2019). Development of structural thermal energy storage concrete using paraffin intruded lightweight aggregate with nano-refined modified encapsulation paste layer. Construction and Building Materials, 228, 116768. doi: https://doi.org/10.1016/j.conbuildmat.2019.116768
- Pointner, H., Steinmann, W.-D. (2016). Experimental demonstration of an active latent heat storage concept. Applied Energy, 168, 661–671. doi: https://doi.org/10.1016/j.apenergy.2016.01.113
- Karademir, H., Özçelik, G., Açikgöz, Ö., Dalkiliç, A. S., İnce, İ. T., Meyer, J., Wongwises, S. (2021). Comprehensive review on the flow characteristics of two-phase flows in inclined tubes. Journal of Thermal Engineering, 7 (3), 483–549. doi: https://doi.org/10.18186/thermal.887821
- Suyitno, B. M., Rahmalina, D., Rahman, R. A. (2023). Increasing the charge/discharge rate for phase-change materials by forming hybrid composite paraffin/ash for an effective thermal energy storage system. AIMS Materials Science, 10 (1), 70–85. doi: https://doi.org/10.3934/matersci.2023005
- Tunggul Ismail, A., Ismail, I., Abdu Rahman, R. (2022). Increasing the reliability of biomass solid fuel combustion using a combined regenerative heat exchanger as an indirect burner. Eastern-European Journal of Enterprise Technologies, 5 (8 (119)), 53–61. doi: https://doi.org/10.15587/1729-4061.2022.265803
- Orchard, B. (2014). Pumps for heat transfer applications. World Pumps, 2014 (10), 36–40. doi: https://doi.org/10.1016/s0262-1762(14)70244-5
- Oueslati, A., Megriche, A. (2017). The effect of liquid temperature on the performance of an airlift pump. Energy Procedia, 119, 693–701. doi: https://doi.org/10.1016/j.egypro.2017.07.096
- Benato, A., Stoppato, A. (2018). Heat transfer fluid and material selection for an innovative Pumped Thermal Electricity Storage system. Energy, 147, 155–168. doi: https://doi.org/10.1016/j.energy.2018.01.045
- Rahmanian, S., Hamzavi, A. (2020). Effects of pump power on performance analysis of photovoltaic thermal system using CNT nanofluid. Solar Energy, 201, 787–797. doi: https://doi.org/10.1016/j.solener.2020.03.061
- Bonandrini, G., Mimmi, G., Rottenbacher, C. (2012). Design and simulation of meshing of a particular internal rotary pump. Mechanism and Machine Theory, 49, 104–116. doi: https://doi.org/10.1016/j.mechmachtheory.2011.11.001
- Hao, C., Wenming, Y., Guangming, L. (2015). Design of gerotor oil pump with new rotor profile for improving performance. Proceedings of the Institution of Mechanical Engineers, Part C: Journal of Mechanical Engineering Science, 230 (4), 592–601. doi: https://doi.org/10.1177/0954406215618228
- Gamez-Montero, P. J., Codina, E., Castilla, R. (2019). A Review of Gerotor Technology in Hydraulic Machines. Energies, 12 (12), 2423. doi: https://doi.org/10.3390/en12122423
- Lee, S., Kwak, H., Han, G., Kim, C. (2019). Design of Gerotor Oil Pump with 2-Expanded Cardioids Lobe Shape for Noise Reduction. Energies, 12 (6), 1126. doi: https://doi.org/10.3390/en12061126
- Ismail, I., John, J., Pane, E. A., Maulana, R., Rahman, R. A., Suwandi, A. (2021). Experimental Evaluation for the Feasibility of Test Chamber in The Open-Loop Wind Tunnel. WSEAS TRANSACTIONS ON FLUID MECHANICS, 16, 120–126. doi: https://doi.org/10.37394/232013.2021.16.12
- Stryczek, J., Bednarczyk, S., Codina, E., Gamez-Montero, P. J., Ivanovic, L., Matejic, M. (2019). Gears or rotors - three approaches to design of working units of hydraulic machines. IOP Conference Series: Materials Science and Engineering, 659 (1), 012006. doi: https://doi.org/10.1088/1757-899x/659/1/012006
- Devendran, R. S., Vacca, A. (2017). Theoretical analysis for variable delivery flow external gear machines based on asymmetric gears. Mechanism and Machine Theory, 108, 123–141. doi: https://doi.org/10.1016/j.mechmachtheory.2016.10.001
- VDI 2221 Blatt 2. Design of technical products and systems - Configuration of individual product design processes (2019). Engl. VDI-Gesellschaft Produkt- und Prozessgestaltung.
- Jaluria, Y. (2019). Design and Optimization of Thermal Systems. CRC Press, 614. doi: https://doi.org/10.1201/9780429085789
- Rahman, R. A., Suwandi, A., Nurtanto, M. (2021). Experimental investigation on the effect of thermophysical properties of a heat transfer fluid on pumping performance for a convective heat transfer system. Journal of Thermal Engineering, 7 (7), 1628–1639. doi: https://doi.org/10.18186/thermal.1025910
- Robison, A., Vacca, A. (2018). Multi-objective optimization of circular-toothed gerotors for kinematics and wear by genetic algorithm. Mechanism and Machine Theory, 128, 150–168. doi: https://doi.org/10.1016/j.mechmachtheory.2018.05.011
- De Martin, A., Jacazio, G., Sorli, M. (2019). Optimization of Gerotor Pumps with Asymmetric Profiles through an Evolutionary Strategy Algorithm. Machines, 7 (1), 17. doi: https://doi.org/10.3390/machines7010017
- Baquedano, C., García-Gil, A., Marazuela, M. Á., Carnicer, A. M., Aguilera, H., Santamarta, J. C., Mejías Fernández, A. (2022). The efficiency loss in groundwater heat pump systems triggered by thermal recycling. Renewable Energy, 200, 1458–1468. doi: https://doi.org/10.1016/j.renene.2022.10.096
- Inkeri, E., Tynjälä, T., Nikku, M. (2022). Numerical modeling of latent heat thermal energy storage integrated with heat pump for domestic hot water production. Applied Thermal Engineering, 214, 118819. doi: https://doi.org/10.1016/j.applthermaleng.2022.118819
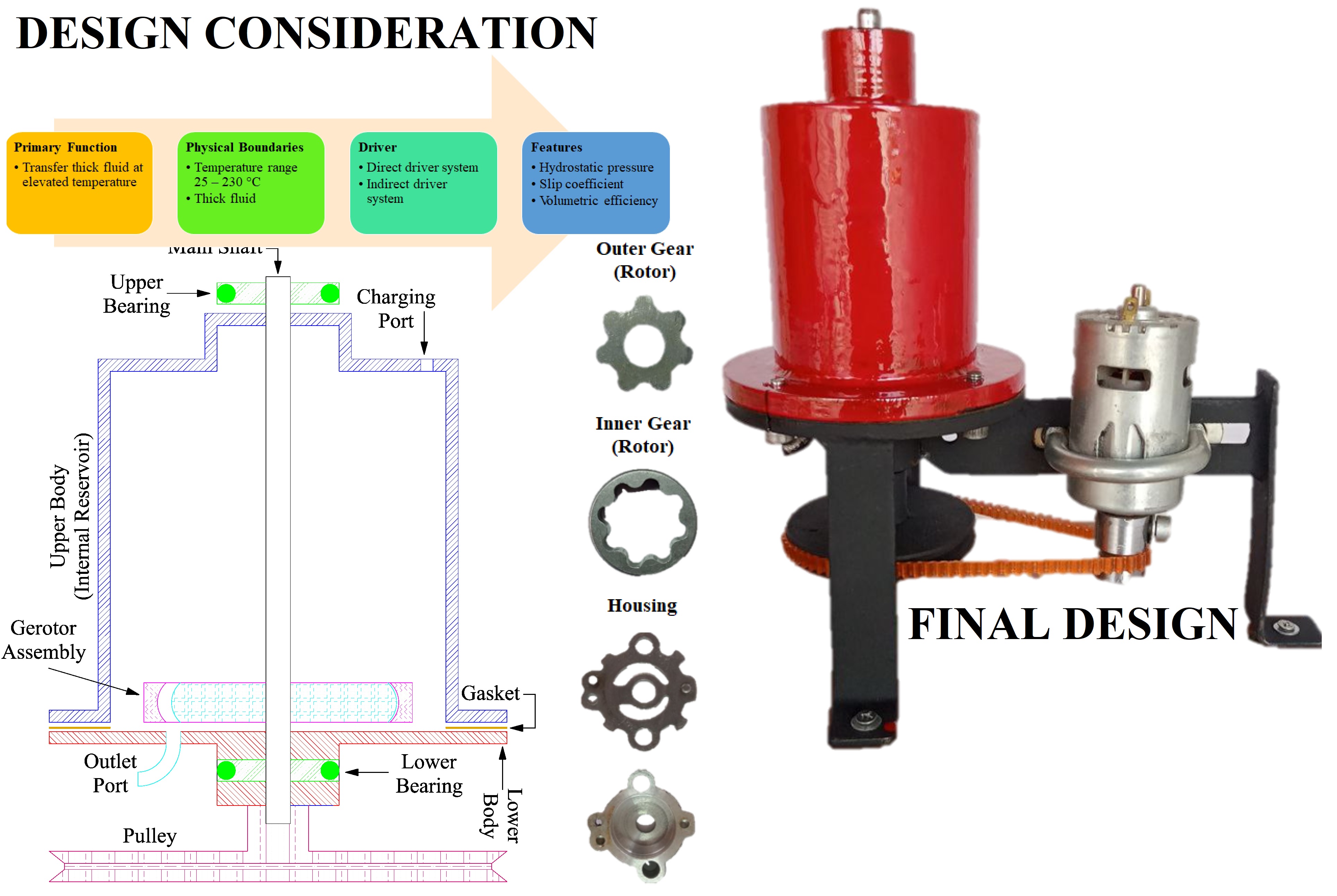
Downloads
Published
How to Cite
Issue
Section
License
Copyright (c) 2023 Dede Lia Zariatin, Agri Suwandi

This work is licensed under a Creative Commons Attribution 4.0 International License.
The consolidation and conditions for the transfer of copyright (identification of authorship) is carried out in the License Agreement. In particular, the authors reserve the right to the authorship of their manuscript and transfer the first publication of this work to the journal under the terms of the Creative Commons CC BY license. At the same time, they have the right to conclude on their own additional agreements concerning the non-exclusive distribution of the work in the form in which it was published by this journal, but provided that the link to the first publication of the article in this journal is preserved.
A license agreement is a document in which the author warrants that he/she owns all copyright for the work (manuscript, article, etc.).
The authors, signing the License Agreement with TECHNOLOGY CENTER PC, have all rights to the further use of their work, provided that they link to our edition in which the work was published.
According to the terms of the License Agreement, the Publisher TECHNOLOGY CENTER PC does not take away your copyrights and receives permission from the authors to use and dissemination of the publication through the world's scientific resources (own electronic resources, scientometric databases, repositories, libraries, etc.).
In the absence of a signed License Agreement or in the absence of this agreement of identifiers allowing to identify the identity of the author, the editors have no right to work with the manuscript.
It is important to remember that there is another type of agreement between authors and publishers – when copyright is transferred from the authors to the publisher. In this case, the authors lose ownership of their work and may not use it in any way.