Formation of the quality of holes obtained by drilling in aviation structures made from polymer composite materials
DOI:
https://doi.org/10.15587/1729-4061.2023.279618Keywords:
polymeric composite materials, hole drilling, hole roughness, geometric precisionAbstract
The subject of this study is the quality indicators (geometric accuracy, roughness, cylindricity and taperness) of holes obtained by drilling in aircraft structures (AS) made of polymeric composite materials (PCM). The quality indicators of holes in AS made from PCM were studied by using kinematic schemes across and along the direction of drilling. A kinematic scheme of formation of the predicted surface roughness of the hole in AS made from PCM has been built. The calculation of the predicted roughness of PCM holes taking into account the geometry of the drill and drilling modes has been proposed. Experimental studies have been implemented to establish the parameters of predicted roughness, geometric accuracy, taperness, as well as deviations from cylindricity. The methods used were the method of expert assessments and experimental studies of quality indicators of PCM openings. The following results were obtained: the roughness in full-scale experiments turned out to be lower than the theoretical calculated values with a difference of not more than 10...15 %. It was found that roughness, taperness, deviations from geometric precision and cylindricity differ in characteristic rotation zones of the drill from 0° to 360° and depend on the drilling parameters and PCM properties. It was found that the deviation from the hole cylindricity is affected by the shrinkage of the material. The appearance of ovality in the holes of prototypes was established. The results of experimental studies of measurements of hole diameters to establish deviations from cylindricity, geometric accuracy, and taperness met the production requirements for the accuracy of their manufacture. For geometric precision and deviation from cylindricity, the results ranged from 7 to 12 IT grades, and for taperness, from 0.083 to 0.28 % per a hole in AS made from PCM and 9–10 IT grades
References
- Shyha, I., Huo, D. (Eds.) (2021). Advances in Machining of Composite Materials. Engineering Materials. Springer. doi: https://doi.org/10.1007/978-3-030-71438-3
- Andrieiev, O. V. (2020). Naukovi osnovy pidvyshchennia efektyvnosti stvorennia konstruktsiy transportnykh litakiv iz polimernykh kompozytsiynykh materialiv na etapakh zhyttievoho tsyklu vyrobu. Kyiv, 333. Available at: https://er.nau.edu.ua/handle/NAU/44706
- Oliveux, G., Dandy, L. O., Leeke, G. A. (2015). Current status of recycling of fibre reinforced polymers: Review of technologies, reuse and resulting properties. Progress in Materials Science, 72, 61–99. doi: https://doi.org/10.1016/j.pmatsci.2015.01.004
- Kondratiev, A., Kovalenko, V., Nabokina, T., Taranenko, I. (2022). Influence of physico-mechanical factors on residual technological stresses and strains of composite panels. Integrated Computer Technologies in Mechanical Engineering - 2022. Kharkiv. Available at: https://www.researchgate.net/publication/365501536_Influence_of_Physico-Mechanical_Factors_on_Residual_Technological_Stresses_and_Strains_of_Composite_Panels
- Khavin, G. L. (2015). Obrazovanie defektov pri sverlenii sloistykh kompozitov i mekhanizm poyavleniya rasslaivaniya. Visnyk NTU «KhPI». Seriya: Pryladobuduvannia, 4 (1113), 96–100. Available at: http://repository.kpi.kharkov.ua/bitstream/KhPI-Press/15182/1/vestnik_HPI_2015_4_Khavin_Obrazovanie.pdf
- Vorobiov, I., Nechyporuk, N., Maiorova, K. (2018). Experimental and numerical investigations on impulse self-pierce riveting of lightweight aircraft aluminium and mixed structures. Proceedings of 22nd International Scientific Conference Transport Means, 121–128. Available at: https://transportmeans.ktu.edu/wp-content/uploads/sites/307/2018/02/Transport-means-I-dalis-2018-09-25.pdf
- Vorobiov, I., Maiorova, K., Voronko, I., Boiko, M., Komisarov, O. (2022). Creation and Improvement Principles of the Pneumatic Manual Impulse Devices. Lecture Notes in Networks and Systems, 178–191. doi: https://doi.org/10.1007/978-3-030-94259-5_17
- Kolesnyk, V., Lysenko, B., Neshta, A., Zabara, M. (2022). Investigation of cutting parameters influence the roughness when drilling CFRP/ Ti alloy stacks. Advances in mechanical engineering and transport, 1 (18), 110–122. doi: https://doi.org/10.36910/automash.v1i18.767
- Chen, W.-C. (1997). Some experimental investigations in the drilling of carbon fiber-reinforced plastic (CFRP) composite laminates. International Journal of Machine Tools and Manufacture, 37 (8), 1097–1108. doi: https://doi.org/10.1016/s0890-6955(96)00095-8
- Shyha, I., Soo, S. L., Aspinwall, D. K., Bradley, S., Dawson, S., Pretorius, C. J. (2010). Drilling of Titanium/CFRP/Aluminium Stacks. Key Engineering Materials, 447–448, 624–633. doi: https://doi.org/10.4028/www.scientific.net/kem.447-448.624
- Xu, J., El Mansori, M. (2016). Experimental study on drilling mechanisms and strategies of hybrid CFRP/Ti stacks. Composite Structures, 157, 461–482. doi: https://doi.org/10.1016/j.compstruct.2016.07.025
- Benezech, L., Landon, Y., Rubio, W. (2011). Study of Manufacturing Defects and Tool Geometry Optimisation for Multi-Material Stack Drilling. Advanced Materials Research, 423, 1–11. doi: https://doi.org/10.4028/www.scientific.net/amr.423.1
- Caggiano, A., Angelone, R., Teti, R. (2017). Image Analysis for CFRP Drilled Hole Quality Assessment. Procedia CIRP, 62, 440–445. doi: https://doi.org/10.1016/j.procir.2017.03.045
- Zitoune, R., Krishnaraj, V., Collombet, F., Le Roux, S. (2016). Experimental and numerical analysis on drilling of carbon fibre reinforced plastic and aluminium stacks. Composite Structures, 146, 148–158. doi: https://doi.org/10.1016/j.compstruct.2016.02.084
- Lupkin, B., Maiorova, K., Vorobiov, I., Nikichanov, V., Sikulskyi, V. (2022). Study of Drilling Cutting Modes Impact on Shrinkage and Surface Roughness of Holes in Composite Materials. Integrated Computer Technologies in Mechanical Engineering - 2022. Kharkiv.
- Isbilir, O., Ghassemieh, E. (2013). Comparative study of tool life and hole quality in drilling of cfrp/titanium stack using coated carbide drill. Machining Science and Technology, 17 (3), 380–409. doi: https://doi.org/10.1080/10910344.2013.806098
- Davim, J., Rubio, J., Abrao, A. (2007). A novel approach based on digital image analysis to evaluate the delamination factor after drilling composite laminates. Composites Science and Technology, 67 (9), 1939–1945. doi: https://doi.org/10.1016/j.compscitech.2006.10.009
- Rahmé, P., Landon, Y., Lachaud, F., Piquet, R., Lagarrigue, P. (2010). Analytical models of composite material drilling. The International Journal of Advanced Manufacturing Technology, 52 (5-8), 609–617. doi: https://doi.org/10.1007/s00170-010-2773-5
- Lupkin, B. V., Andrieiev, O. V., Antoniuk, V. S., Vysloukh, S. P., Korolkov, Yu. A., Voloshko, O. V. (2023). Prohnozuvannia parametriv shorstkosti poverkhni otvoru pry sverdlinni kompozytsiynykh materialiv. Zbirnyk naukovykh prats XI-oi Mizhnarodnoi naukovo-tekhnichnoi konferentsii «Prohresyvni tekhnolohii v mashynobuduvanni». Lviv-Zveniv, 62–66.
- Tesfaye Jule, L., Ramaswamy, K., Nagaprasad, N., Shanmugam, V., Vignesh, V. (2021). Design and analysis of serial drilled hole in composite material. Materials Today: Proceedings, 45, 5759–5763. doi: https://doi.org/10.1016/j.matpr.2021.02.587
- Hocheng, H. (2012). Machining technology for composite materials. Woodhead Publishing. doi: https://doi.org/10.1533/9780857095145
- Maiorova, K., Vorobiov, I., Andrieiev, O., Lupkin, B., Sikulskiy, V. (2022). Forming the geometric accuracy and roughness of holes when drilling aircraft structures made from polymeric composite materials. Eastern-European Journal of Enterprise Technologies, 2 (1 (116)), 71–80. doi: https://doi.org/10.15587/1729-4061.2022.254555
- Vambol, O., Shevtsova, M., Tsaritsynskyi, A., Nabokina, T., Kondratiev, A. (2022). Temperature Effect on Elastic, Thermomechanical and Thermal Properties of Polymer Composite Materials. Lecture Notes in Networks and Systems, 466–476. doi: https://doi.org/10.1007/978-3-031-20141-7_43
- Stepanov, A. A. (1987). Obrabotka rezaniem vysokoprochnykh kompozitsionnykh materialov. Leningrad: Mashinostroenie, 176.
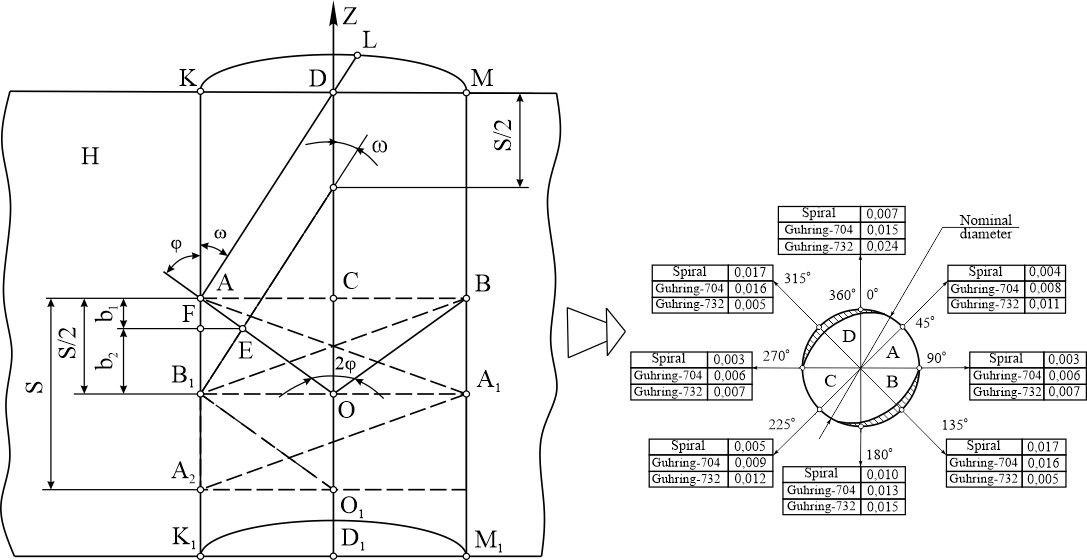
Downloads
Published
How to Cite
Issue
Section
License
Copyright (c) 2023 Kateryna Maiorova, Oleksii Andrieiev, Borys Lupkin, Victor Antonyuyk, Sergii Vysloukh

This work is licensed under a Creative Commons Attribution 4.0 International License.
The consolidation and conditions for the transfer of copyright (identification of authorship) is carried out in the License Agreement. In particular, the authors reserve the right to the authorship of their manuscript and transfer the first publication of this work to the journal under the terms of the Creative Commons CC BY license. At the same time, they have the right to conclude on their own additional agreements concerning the non-exclusive distribution of the work in the form in which it was published by this journal, but provided that the link to the first publication of the article in this journal is preserved.
A license agreement is a document in which the author warrants that he/she owns all copyright for the work (manuscript, article, etc.).
The authors, signing the License Agreement with TECHNOLOGY CENTER PC, have all rights to the further use of their work, provided that they link to our edition in which the work was published.
According to the terms of the License Agreement, the Publisher TECHNOLOGY CENTER PC does not take away your copyrights and receives permission from the authors to use and dissemination of the publication through the world's scientific resources (own electronic resources, scientometric databases, repositories, libraries, etc.).
In the absence of a signed License Agreement or in the absence of this agreement of identifiers allowing to identify the identity of the author, the editors have no right to work with the manuscript.
It is important to remember that there is another type of agreement between authors and publishers – when copyright is transferred from the authors to the publisher. In this case, the authors lose ownership of their work and may not use it in any way.