Proving the possibility to rationalize the process of seed materials separation with a vibro-pneumatic centrifugal separator using a theoretical model
DOI:
https://doi.org/10.15587/1729-4061.2023.291114Keywords:
vibro-pneumatic centrifugal separator, density of seed material, multiphase medium, fluid, separation parametersAbstract
The object of research is the seed material and working bodies of a vibro-pneumatic centrifugal separator; the subject is their interaction. The established surfaces, which are the results of the simulation of the process of separation of seed materials in the vibro-pneumatic centrifugal separator, have a curve to the plane whose parameters are the speed of the air flow and the frequency of oscillations of the working surface. It is noted that this nature of the dependence of the purity of the «heavy» fraction of seeds on parameters of the separation process makes it possible to determine the rational ranges of these parameters, at which the maximum value of this characteristic is reached. Experimental simulation of the separation process in the vibro-pneumatic centrifugal separator of wheat, sunflower, and soybean seed materials under production conditions showed a high convergence of the results with the results of the simulation of the process under the same initial conditions. It was established that the correlation coefficients between the points obtained experimentally and obtained by simulation for the given results are in the range from 0.89 to 0.95. At the same time, the differences are the purity values of the «heavy» seed fraction, and not in the nature of its change due to changes in the parameters of the separation process. The expediency of using modeling when determining the rational values of the parameters of the separation process in the vibro-pneumatic centrifugal separator is noted. This will help increase the energy and resource efficiency of the equipment due to the absence of the need for experimental setup. The rational ranges of air flow speed and vibration frequency of the rotor of the vibro-pneumatic centrifugal separator for the separation of seed materials have been determined: wheat – 1.2...1.5 m/s; 4500...5100 cycles per minute; sunflower – 1.3...1.5 m/s; 4500...5000 cycles per minute; soybeans – 1.3...1.6 m/s; 5000...5500 cycles per minute
References
- Stepanenko, S., Aneliak, M., Kuzmych, A., Kustov, S., Lysaniuk, V. (2022). Improving the efficiency of harvesting sunflower seed crops. INMATEH Agricultural Engineering, 67 (2), 331–340. doi: https://doi.org/10.35633/inmateh-67-34
- Stepanenko, S. P. (2017). Research pneumatic gravity separation grain materials. International Scientific Journal "Mechanization in Agriculture", 2, 54–56. Available at: https://stumejournals.com/journals/am/2017/2/54.full.pdf
- Chaplygin, M., Bespalova, O., Podzorova, M. (2019). Results of tests of devices for sunflower harvesting in economic conditions. E3S Web of Conferences, 126, 00063. doi: https://doi.org/10.1051/e3sconf/201912600063
- Jin, W., Ding, Y., Bai, S., Zhang, X., Yan, J., Zhou, X. (2021). Design and experiments of the reel board header device for an oil sunflower harvester. Transactions of the Chinese Society of Agricultural Engineering, 37 (3), 27–36. Available at: http://www.tcsae.org/nygcxben/article/abstract/20210304
- Rogovskii, I. L., Martiniuk, D. I., Voinash, S. A., Luchinovich, A. A., Sokolova, V. A., Ivanov, A. M., Churakov, A. V. (2021). Modeling the throughput capacity of threshing-separating apparatus of grain harvester’s combines. IOP Conference Series: Earth and Environmental Science, 677 (4), 042098. doi: https://doi.org/10.1088/1755-1315/677/4/042098
- Shaforostov, V. D., Makarov, S. S., Elizarov, P. A. (2018). A harvester to a breeding and seeds growing combine for sunflower harvesting. Oil Crops. Scientific and Technical Bulletin of All-Russian Research Institute of Oil Crops by the Name of Pustovoit V.S., 3 (175), 76–80. doi: https://doi.org/10.25230/2412-608x-2018-3-175-76-80
- Bredykhin, V., Gurskyi, P., Alfyorov, O., Bredykhina, K., Pak, A. (2021). Improving the mechanical-mathematical model of grain mass separation in a fluidized bed. Eastern-European Journal of Enterprise Technologies, 3 (1 (111)), 79–86. doi: https://doi.org/10.15587/1729-4061.2021.232017
- Kumar, D., Kalita, P. (2017). Reducing Postharvest Losses during Storage of Grain Crops to Strengthen Food Security in Developing Countries. Foods, 6 (1), 8. doi: https://doi.org/10.3390/foods6010008
- Kharchenko, S., Borshch, Y., Kovalyshyn, S., Piven, M., Abduev, M., Miernik, A. et al. (2021). Modeling of Aerodynamic Separation of Preliminarily Stratified Grain Mixture in Vertical Pneumatic Separation Duct. Applied Sciences, 11 (10), 4383. doi: https://doi.org/10.3390/app11104383
- Bulgakov, V., Nikolaenko, S., Holovach, I., Adamchuk, V., Kiurchev, S., Ivanovs, S., Olt, J. (2020). Theory of grain mixture particle motion during aspiration separation. Agronomy Research, 18 (1), 18–37. Available at: https://dspace.emu.ee/xmlui/handle/10492/5667
- Tishchenko, L., Kharchenko, S., Kharchenko, F., Bredykhin, V., Tsurkan, O. (2016). Identification of a mixture of grain particle velocity through the holes of the vibrating sieves grain separators. Eastern-European Journal of Enterprise Technologies, 2 (7 (80)), 63–69. doi: https://doi.org/10.15587/1729-4061.2016.65920
- Bakum, M. V., Kharchenko, S. O., кovalyshyn, S. Y., Krekot, M. M., Kharchenko, F. M., Shvets, O. P. et al. (2022). Identification of parameters of the separation process of safflower seed material on sieves. Journal of Physics: Conference Series, 2408 (1), 012013. doi: https://doi.org/10.1088/1742-6596/2408/1/012013
- Salemi, E., Tessari, U., Mastrocicco, N. C., Micol. (2010). Improved gravitational grain size separation method. Applied Clay Science, 48 (4), 612–614. doi: https://doi.org/10.1016/j.clay.2010.03.014
- Bredykhin, V., Pak, A., Gurskyi, P., Denisenko, S., Bredykhina, K. (2021). Improving the mechanical-mathematical model of pneumatic vibration centrifugal fractionation of grain materials based on their density. Eastern-European Journal of Enterprise Technologies, 4 (1 (112)), 54–60. doi: https://doi.org/10.15587/1729-4061.2021.236938
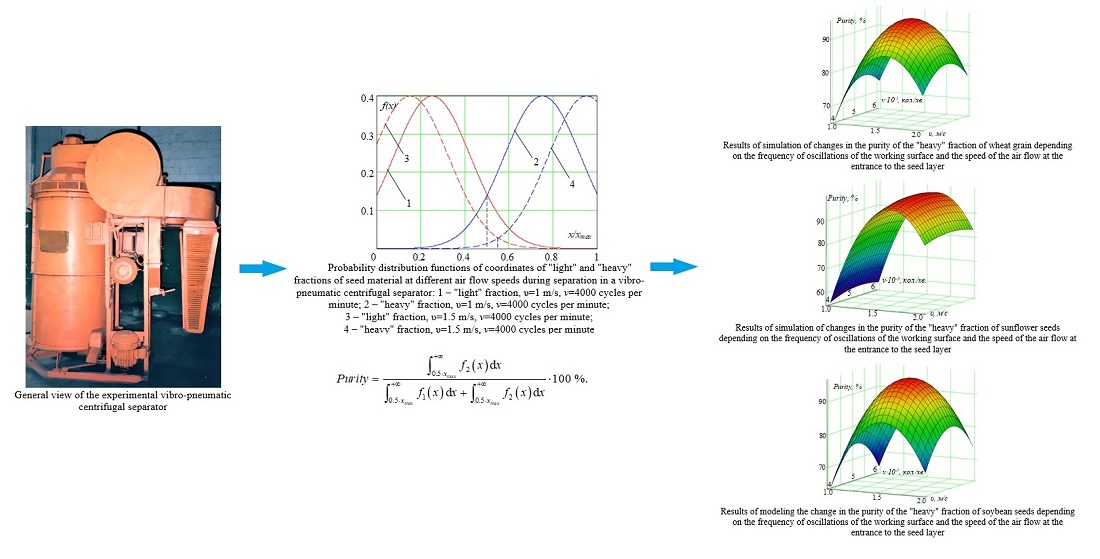
Downloads
Published
How to Cite
Issue
Section
License
Copyright (c) 2023 Vadym Bredykhin, Alexey Bogomolov, Liliia Kis-Korkishchenko, Andrey Pak, Alina Pak

This work is licensed under a Creative Commons Attribution 4.0 International License.
The consolidation and conditions for the transfer of copyright (identification of authorship) is carried out in the License Agreement. In particular, the authors reserve the right to the authorship of their manuscript and transfer the first publication of this work to the journal under the terms of the Creative Commons CC BY license. At the same time, they have the right to conclude on their own additional agreements concerning the non-exclusive distribution of the work in the form in which it was published by this journal, but provided that the link to the first publication of the article in this journal is preserved.
A license agreement is a document in which the author warrants that he/she owns all copyright for the work (manuscript, article, etc.).
The authors, signing the License Agreement with TECHNOLOGY CENTER PC, have all rights to the further use of their work, provided that they link to our edition in which the work was published.
According to the terms of the License Agreement, the Publisher TECHNOLOGY CENTER PC does not take away your copyrights and receives permission from the authors to use and dissemination of the publication through the world's scientific resources (own electronic resources, scientometric databases, repositories, libraries, etc.).
In the absence of a signed License Agreement or in the absence of this agreement of identifiers allowing to identify the identity of the author, the editors have no right to work with the manuscript.
It is important to remember that there is another type of agreement between authors and publishers – when copyright is transferred from the authors to the publisher. In this case, the authors lose ownership of their work and may not use it in any way.