Optimization of welding direction model parameters to enhance the tensile strength of ST 42 steel joints through variation of current strength simulation
DOI:
https://doi.org/10.15587/1729-4061.2024.295536Keywords:
current strength simulation, welding direction joint model, tensile strengthAbstract
The welding process plays a central role in the welding industry, where the joint zone undergoing the welding process experiences structural and mechanical property changes. This research evaluates the comparison of current strength and parameters in the directional welding joint model, a critical aspect of addressing common weaknesses in welded joints. The research objects include four current levels (100, 120, 140, 160 A) and three types of welding directions (longitudinal, transversal, and combination). The aim of this study is to detect the optimal combination in welded joints that can produce a maximum tensile strength ratio. The research method involves tensile testing on various specimen models of joint types at specific current strength levels.
The research results indicate that at the current strength level of 120 A, the combined directional welding joint model (longitudinal+transverse) provides a maximum tensile strength reaching 335.370 MPa. This finding stands out significantly, surpassing the tensile strength values at other current levels and welding model types, such as at 100 A (331.574 MPa), 140 A (332.315 MPa), and 160 A (332.685 MPa). This discovery highlights that the combined joint model yields a substantial improvement in joint strength, making it an optimal solution for various current strength levels and joint models.
The key feature of this research involves specific recommendations for the welding industry, including guidelines on selecting optimal parameters to enhance the tensile strength of joints. The directional welding joint models can be a reference in designing welding procedure specifications to incorporate construction elements using ST 42 material. This research contributes both theoretically and practically, offering opportunities for improving efficiency and structural safety in the welding process, thus positively impacting the quality of joints in construction and manufacturing applications
References
- Salehpour, F., Nematifard, V., Maram, G., Afkar, A. (2021). Experimental Investigation of TIG Welding Input Parameters Effects on Mechanical Characteristics. International Journal of Engineering, 34 (2). https://doi.org/10.5829/ije.2021.34.02b.30
- You, Y.-T., Kim, J.-W. (2017). Fiber Laser Welding Properties of Copper Materials for Secondary Batteries. Materials Science, 23 (4). https://doi.org/10.5755/j01.ms.23.4.16316
- Ozsarac, U. (2012). Investigation of Mechanical Properties of Galvanized Automotive Sheets Joined by Resistance Spot Welding. Journal of Materials Engineering and Performance, 21 (5), 748–755. https://doi.org/10.1007/s11665-012-0189-0
- Inoué, S. (1960). On the physical properties of the mitotic spindle. Annals of the New York Academy of Sciences, 90 (2), 529–530. https://doi.org/10.1111/j.1749-6632.1960.tb23269.x
- Ariyanto, Arsyad, H., Syahid, M., Renreng, I. (2022). Optimization of Welding Parameters for Resistance Spot Welding with Variations in the Roughness of the Surface of the AISI 304 Stainless Steel Joint to Increase Joint Quality. International Journal of Mechanical Engineering and Robotics Research, 11 (11), 877–883. https://doi.org/10.18178/ijmerr.11.11.877-883
- Jin, B., Tian, L., Hao, J., Wang, H., Wang, Y. (2022). Axial compressive behavior of twining-bamboo-confined thin-walled steel tubular columns. Journal of Constructional Steel Research, 192, 107246. https://doi.org/10.1016/j.jcsr.2022.107246
- Jaypuria, S., Doshi, N., Pratihar, D. K. (2018). Effects of Welding Parameters on Mechanical Properties in Electron Beam Welded CuCrZr Alloy Plates. IOP Conference Series: Materials Science and Engineering, 338, 012013. https://doi.org/10.1088/1757-899x/338/1/012013
- Ma, H., Zheng, H., Zhang, W., Tang, Z., Lui, E. M. (2020). Experimental and Numerical Study of Mechanical Behavior of Welded Steel Plate Joints. Metals, 10 (10), 1293. https://doi.org/10.3390/met10101293
- Prasad, S., Pal, S., Robi, P. S. (2020). Analysis of weld characteristics of micro plasma arc welded thin stainless steel 306 L sheet. Journal of Manufacturing Processes, 57, 957–977. https://doi.org/10.1016/j.jmapro.2020.07.062
- Gunawan, E., Choifin, M., Khoirul Rosidin, M., Nur Afifah, Y., Lestariningsih, W., Sungging Pradana, M. et al. (2019). Analysis of the Effect of Current Flow Variations in GTAW on SS 400 Plate Material Connected with SUS 304 Stainless Steel Plate Against Tensile Strength and Hardness with ER308L Electrodes. Journal of Physics: Conference Series, 1175, 012277. https://doi.org/10.1088/1742-6596/1175/1/012277
- Wang, X. (2003). Fatigue and microstructure of welded joints of metal sheets for automotive exhaust system. JSAE Review, 24 (3), 295–301. https://doi.org/10.1016/s0389-4304(03)00041-9
- Chen, Z., Wang, J., Liu, J., Cong, Z. (2020). Tensile and shear performance of rotary inter-module connection for modular steel buildings. Journal of Constructional Steel Research, 175, 106367. https://doi.org/10.1016/j.jcsr.2020.106367
- Ghorbel, R., Ktari, A., Haddar, N. (2021). Experimental analysis of temperature field and distortions in multi-pass welding of stainless cladded steel. The International Journal of Advanced Manufacturing Technology, 113 (11-12), 3525–3542. https://doi.org/10.1007/s00170-021-06788-y
- Kumar, P., Sinha, A. N., Hirwani, C. K., Murugan, M., Saravanan, A., Singh, A. K. (2021). Effect of welding current in TIG welding 304L steel on temperature distribution, microstructure and mechanical properties. Journal of the Brazilian Society of Mechanical Sciences and Engineering, 43 (7). https://doi.org/10.1007/s40430-021-03082-6
- Bozkurt, F., Çakir, F. H., Schmidova, E., Sunil Kumar, M. R. (2020). The Effect of Welding Parameters on Static and Dynamic Behaviors of Spot Welded Ti6Al4V Sheets. Journal of Materials Engineering and Performance, 29 (11), 7468–7479. https://doi.org/10.1007/s11665-020-05202-0
- Dittrich, F., Kaars, J., Masek, B., Jenicek, S., Wagner, M. F.-X., Mayr, P. (2019). HAZ characterization of welded 42SiCr steel treated by quenching and partitioning. Journal of Materials Processing Technology, 268, 37–46. https://doi.org/10.1016/j.jmatprotec.2018.12.035
- Singh, J., Arora, K. S., Shajan, N., Shome, M., Shukla, D. K. (2020). Influence of wire feed rate to speed ratio on arc stability and characteristics of cold metal transfer weld–brazed dissimilar joints. The International Journal of Advanced Manufacturing Technology, 108 (11-12), 3491–3505. https://doi.org/10.1007/s00170-020-05637-8
- Kumar-Krishnasamy, R., Siegele, D. (2010). 3D modelling of a multi pass dissimilar tube welding and post weld heat treatment of nickel based alloy and chromium steel. International Journal of Pressure Vessels and Piping, 87 (11), 643–649. https://doi.org/10.1016/j.ijpvp.2010.08.010
- Yuce, C., Karpat, F., Yavuz, N. (2018). Effects of Heat Input in Laser Welding of Dissimilar Galvanized Steel to Aluminium Alloy. Proceedings of the 4th World Congress on Mechanical, Chemical, and Material Engineering. https://doi.org/10.11159/icmie18.125
- Kocabekir, B., Kaçar, R., Gündüz, S., Hayat, F. (2008). An effect of heat input, weld atmosphere and weld cooling conditions on the resistance spot weldability of 316L austenitic stainless steel. Journal of Materials Processing Technology, 195 (1-3), 327–335. https://doi.org/10.1016/j.jmatprotec.2007.05.026
- Kishore, K., Kumar, P., Mukhopadhyay, G. (2021). Microstructure, Tensile and Fatigue Behaviour of Resistance Spot Welded Zinc Coated Dual Phase and Interstitial Free Steel. Metals and Materials International, 28 (4), 945–965. https://doi.org/10.1007/s12540-020-00939-8
- Ghosh, P. S., Sen, A., Chattopadhyaya, S., Sharma, S., Singh, J., Dwivedi, S. P. et al. (2021). Prediction of Transient Temperature Distributions for Laser Welding of Dissimilar Metals. Applied Sciences, 11 (13), 5829. https://doi.org/10.3390/app11135829
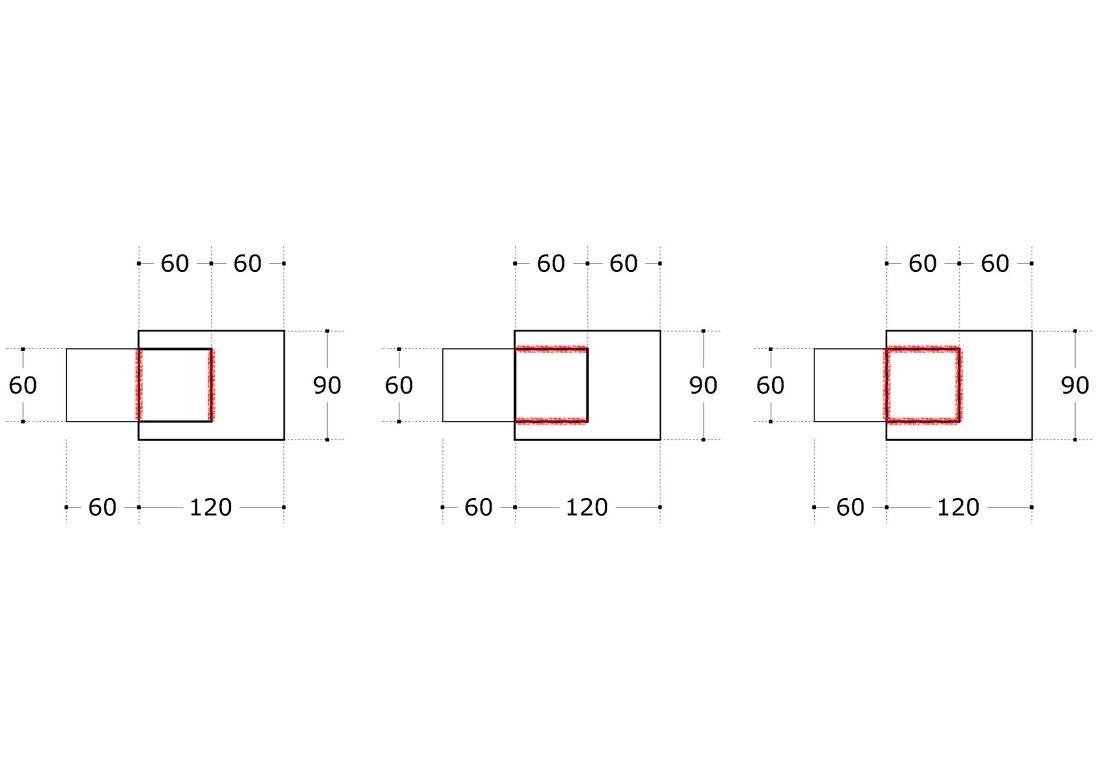
Downloads
Published
How to Cite
Issue
Section
License
Copyright (c) 2024 Saripuddin M, Ariyanto, Sriwati, Muhammad Fathur Rahman

This work is licensed under a Creative Commons Attribution 4.0 International License.
The consolidation and conditions for the transfer of copyright (identification of authorship) is carried out in the License Agreement. In particular, the authors reserve the right to the authorship of their manuscript and transfer the first publication of this work to the journal under the terms of the Creative Commons CC BY license. At the same time, they have the right to conclude on their own additional agreements concerning the non-exclusive distribution of the work in the form in which it was published by this journal, but provided that the link to the first publication of the article in this journal is preserved.
A license agreement is a document in which the author warrants that he/she owns all copyright for the work (manuscript, article, etc.).
The authors, signing the License Agreement with TECHNOLOGY CENTER PC, have all rights to the further use of their work, provided that they link to our edition in which the work was published.
According to the terms of the License Agreement, the Publisher TECHNOLOGY CENTER PC does not take away your copyrights and receives permission from the authors to use and dissemination of the publication through the world's scientific resources (own electronic resources, scientometric databases, repositories, libraries, etc.).
In the absence of a signed License Agreement or in the absence of this agreement of identifiers allowing to identify the identity of the author, the editors have no right to work with the manuscript.
It is important to remember that there is another type of agreement between authors and publishers – when copyright is transferred from the authors to the publisher. In this case, the authors lose ownership of their work and may not use it in any way.