Improving the thermostatic steam trap characteristics using spring elements with the shape memory effect
DOI:
https://doi.org/10.15587/1729-4061.2024.300489Keywords:
steam trap, spring element, shape memory effect, inertia, thermal force cyclingAbstract
The object of research is the deformation-force characteristics of spring elements of thermostatic steam traps with the shape memory effect.
The research solves the problem related to the imperfection of the design of steam traps controlling elements and their high inertia.
Experimental studies on the impact of the spring force elements cooling rate on the deformation-force characteristics were conducted. Experimental studies showed that the significant impact of the spring force elements cooling rate on the deformation-force characteristics is observed exceptionally under the deformation mode at a temperature t ≤ Мf. Based on the results of the experiments, it was found that decreasing the cooling rate from 66.7 to 0.013 °C/s has a positive effect on the spring element deformation-force characteristics.
Distinctive feature of the work is the study of winding pitch and thermal force cycling impact on the deformation-force characteristics of spring elements. It was found that using thermal force cycling makes it possible to reduce the force required for complete compression of the spring element by 60 %. Intensive decrease in the force required for the complete compression of the spring elements occurs during the first 100 thermal force cycles.
The rational method for spring elements heat treatment has been given. It is based on the next steps: heating to a temperature of 400–500 °C for 1 hour; exposure at this temperature for an hour; cooling with rate 0.013 °C/s, the number of thermal force cycles is at least 100 with a winding pitch of 8·10–3 m. Based on research results, an improved design of thermostatic steam trap with controlling element in the form of cylindrical compression spring made of the VSP-1 alloy based on nitinol has been presented
References
- Steam Trap and Boiler Efficiency Research. Final Report (2020). DNV GL. Available at: https://ma-eeac.org/wp-content/uploads/MA-CIEC-Stage-5-Final-Report-MA20C05-G-STBE-FINAL-20201020.pdf
- Sahoo, T. (2021). Steam Traps Failure. Root Cause Failure Analysis, 295–308. https://doi.org/10.1002/9781119615606.ch16
- Mobley, R. K. (2004). Steam Traps. Maintenance Fundamentals, 365–373. https://doi.org/10.1016/b978-075067798-1/50039-x
- Kavak, H., Döner, N. (2022). Impact of Steam Traps On Energy Efficiency and Energy Cost Analysis: The Case of a Textile Factory. Mühendis ve Makina, 63 (709), 651–671. https://doi.org/10.46399/muhendismakina.1128047
- Gonzalez, C. H., Oliveira, C. A. do N., Pina, E. A. C. de, Urtiga Filho, S. L., Araújo Filho, O. O. de, Araújo, C. J. de. (2010). Heat treatments and thermomechanical cycling influences on the R-phase in Ti-Ni shape memory alloys. Materials Research, 13 (3), 325–331. https://doi.org/10.1590/s1516-14392010000300008
- Oliveira, C. A. do N., Gonzalez, C. H., Olimpio Filho, O., Silva, N. J. da, Guimarães, P. B., Nuñez-Mendoza, E., Cuéllar, E. M. L. (2015). Thermomechanical Analysis on Ti-Ni Shape Memory Helical Springs Under Cyclic Tensile Loads. Materials Research, 18 (suppl 2), 17–24. https://doi.org/10.1590/1516-1439.334514
- Hadi, A., Yousefi-Koma, A., Elahinia, M., Moghaddam, M. M., Ghazavi, A. (2011). A shape memory alloy spring-based actuator with stiffness and position controllability. Proceedings of the Institution of Mechanical Engineers, Part I: Journal of Systems and Control Engineering, 225 (7), 902–917. https://doi.org/10.1177/2041304110394570
- Lemanski, J. L. (2006). A Low Hysteresis NiTiFe Shape Memory Alloy Based Thermal Conduction Switch. AIP Conference Proceedings. https://doi.org/10.1063/1.2192327
- Krishnan, V. B., Bewerse, C., Notardonato, W. U., Vaidyanathan, R., Balachandran, U. (Balu), Amm, K. et al. (2008). A thermal conduction switch based on low hysteresis nitife shape memory alloy helical springs. AIP Conference Proceedings. https://doi.org/10.1063/1.2900374
- Stachowiak, D. (2019). A computational and experimental study of shape memory alloy spring actuator. Przegląd Elektrotechniczny, 1 (7), 31–34. https://doi.org/10.15199/48.2019.07.07
- Da Silva, K. C. A., Gonzalez, C. H., Oliveira, C. A. do N., Cândido Junior, M., Rocha, J. O. S. (2024). Study of superelastic fatigue in Ni-Ti alloy sensors/actuators with shape memory. Observatório De La Economía Latinoamericana, 22 (1), 3943–3962. https://doi.org/10.55905/oelv22n1-205
- Polishchuk, V. A., Nikolaiev, O. L., Zadorozhnaya, T. P. (2016). Determination of spring elements characteristics using shape memory effect during thermomechanical impact. Collection of Scientific Publications NUS, 463 (1), 26–29. https://doi.org/10.15589/jnn20160104
- Benafan, O., Brown, J., Calkins, F. T., Kumar, P., Stebner, A. P., Turner, T. L. et al. (2013). Shape memory alloy actuator design: CASMART collaborative best practices and case studies. International Journal of Mechanics and Materials in Design, 10 (1), 1–42. https://doi.org/10.1007/s10999-013-9227-9
- Pylypchak, V., Zhukov, O. (2017). Pat. No. 116687 UA. Termostatychnyi kondensatovidvidnyk. No. u201700033; declareted: 03.01.2017; published: 25.05.2017, Bul. No. 10. Available at: https://base.uipv.org/searchINV/search.php?action=viewdetails&IdClaim=235931
- Huang, T.-S., Ou, S.-F., Kuo, C.-H., Yang, C.-H. (2020). Effects of Thermomechanical Treatment on Phase Transformation of the Ti50Ni49W1 Shape Memory Alloy. Metals, 10 (4), 527. https://doi.org/10.3390/met10040527
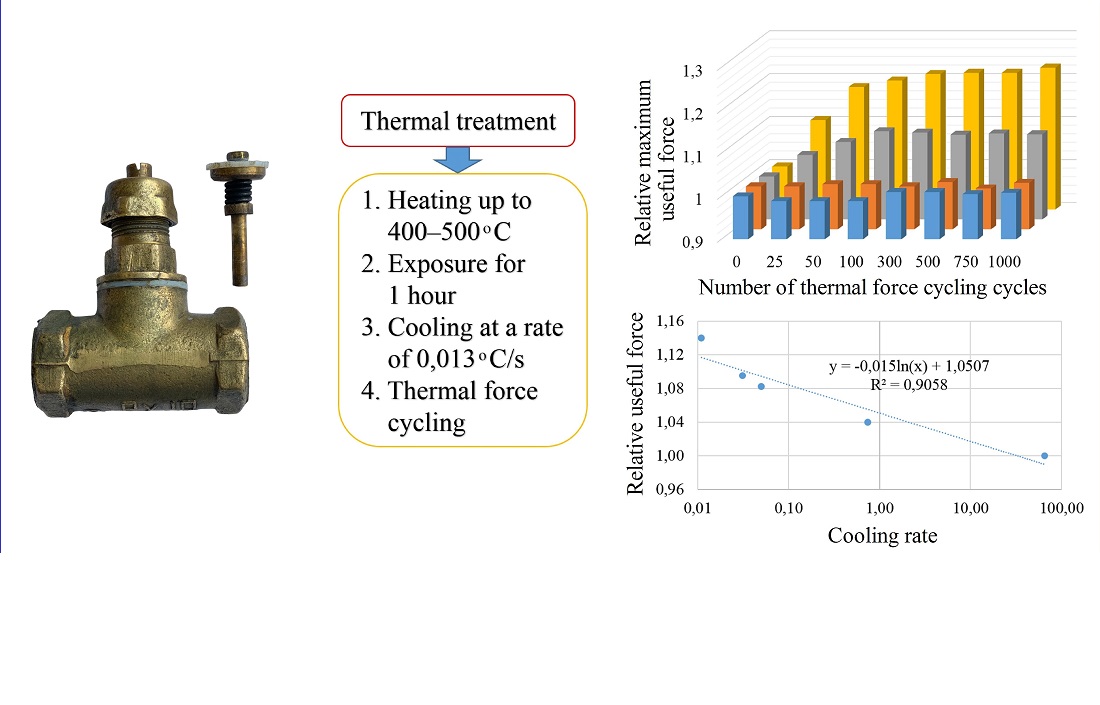
Downloads
Published
How to Cite
Issue
Section
License
Copyright (c) 2024 Vitaliy Pylypchak, Oleksandr Epifanov, Pavlo Patsurkovskyi, Yuriy Shapovalov

This work is licensed under a Creative Commons Attribution 4.0 International License.
The consolidation and conditions for the transfer of copyright (identification of authorship) is carried out in the License Agreement. In particular, the authors reserve the right to the authorship of their manuscript and transfer the first publication of this work to the journal under the terms of the Creative Commons CC BY license. At the same time, they have the right to conclude on their own additional agreements concerning the non-exclusive distribution of the work in the form in which it was published by this journal, but provided that the link to the first publication of the article in this journal is preserved.
A license agreement is a document in which the author warrants that he/she owns all copyright for the work (manuscript, article, etc.).
The authors, signing the License Agreement with TECHNOLOGY CENTER PC, have all rights to the further use of their work, provided that they link to our edition in which the work was published.
According to the terms of the License Agreement, the Publisher TECHNOLOGY CENTER PC does not take away your copyrights and receives permission from the authors to use and dissemination of the publication through the world's scientific resources (own electronic resources, scientometric databases, repositories, libraries, etc.).
In the absence of a signed License Agreement or in the absence of this agreement of identifiers allowing to identify the identity of the author, the editors have no right to work with the manuscript.
It is important to remember that there is another type of agreement between authors and publishers – when copyright is transferred from the authors to the publisher. In this case, the authors lose ownership of their work and may not use it in any way.